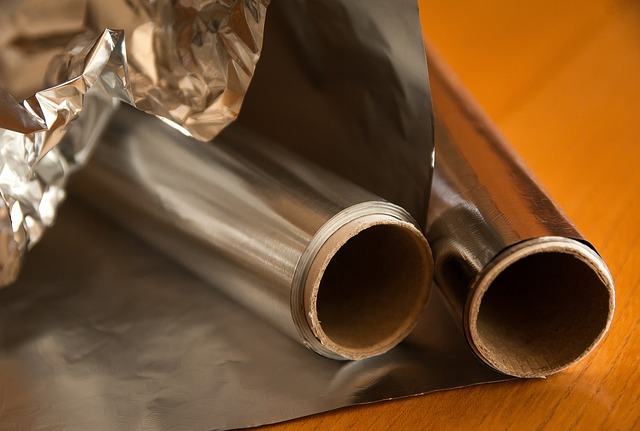
A laminação a frio recebe este nome por se dar a temperaturas abaixo da temperatura de recristalização do material. Nete processo há uma taxa de encruamento crescente e, consequentemente, aumento na dureza e na resistência mecânica.
Apesar de ser preferível no acabamento após laminação a quente, há espaço para a laminação a frio na conformação de materiais não-ferrosos, tais como alumínio, cobre e suas ligas. Caso as chapas de alumínio sejam oriundas do método roll casting a laminação pode ocorrer somente a frio, podendo se empregar tratamentos térmicos intermediários caso necessário.
Os produtos da laminação a frio são chapas finas, fitas, tiras ou folhas de excelente acabamento e ótimo controle dimensional.
Este processo de laminação permite menores reduções de espessura do que a laminação a quente. A sua microestrutura é composta por grãos alongados, devido ao encruamento. Por conta deste formato dos grãos, as peças que passam por laminação a frio possuem anisotropia, apresentando propriedades diferentes dependendo da direção.
Laminadores quádruos são os favoritos para o emprego de laminação a frio, se atingindo velocidades de até 30 m/s na laminação e se obtendo reduções de 50% a 90%. Pode haver lubrificação do processo por meio de hidrocarbonetos de base parafínica, o que melhora o desempenho da laminação.
Vantagens
Este é um processo que produz peças de ótimo acabamento e controle das suas dimensões. Não há formação de carepa e não é necessário realizar aquecimento do metal em fornos antes da passagem pelos laminadores. São obtidas chapas e folhas de pequena espessura e maior velocidade nos passes, o que torna este processo muito produtivo.
Desvantagens
O que limita o emprego desta operação é a ductilidade da matéria-prima, pois muitos metais permitem uma redução muito baixa, com tendência a encruar e se tornar ainda menos dúcteis. Alguns tratamentos térmicos podem ocorrer entre passes, o que aumenta o custo do processo.