·
Engenharia Naval e Oceânica ·
Máquinas Elétricas
Envie sua pergunta para a IA e receba a resposta na hora
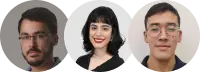
Prefere sua atividade resolvida por um tutor especialista?
- Receba resolvida até o seu prazo
- Converse com o tutor pelo chat
- Garantia de 7 dias contra erros
Recomendado para você
1
Links compartilhados - Análise de conteúdos
Máquinas Elétricas
UMG
6
A123 Systems: Advanced Battery Energy Storage for Renewable Integration
Máquinas Elétricas
UMG
1
Webinar Series on Battery Testing and Advanced Battery Materials
Máquinas Elétricas
UMG
20
Research on Recycle and Closed-Cycle Diesel Engines for Underwater Applications
Máquinas Elétricas
UMG
3
Closed Cycle Diesel Power Psychrocyle by Charles B. Totten
Máquinas Elétricas
UMG
244
A Design Tool for the Evaluation of Atmosphere Independent Propulsion in Submarines
Máquinas Elétricas
UMG
6
Status of Advanced Battery Technologies for the EV Market
Máquinas Elétricas
UMG
6
Vanadium Redox Flow Batteries: The Future of Grid Energy Storage
Máquinas Elétricas
UMG
190
Entwicklung und Merkmale von Unterseebooten
Máquinas Elétricas
UMG
9
Advanced Underwater Power Systems for Autonomous Underwater Vehicles
Máquinas Elétricas
UMG
Texto de pré-visualização
his abstract introduces results from OnTo Technologys innovative recycling process to produce new materials for new batteries from materials from spent batteries Recycling spent batteries is a growing problem for the consumer electronics electric vehicle industries The electronics industry is facing pressure to see that material is recycled efficiently and responsibly as agreed in the Basal convention 1 The automotive industry already recycles at highrates and plans to maintain this activity into the next generation of vehicles 2 The growth in commodities prices and legislative mandates play an important role in building demand for efficient and environmentally friendly recycling Pyrometallugical and hydrometallurgical technologies are the basis of todays battery recycling options these processes burn dissolve or melt spent battery material and produce hazardous waste byproducts such as slag 35 Cobalt and nickel metal recovery is the general goal for these processes As battery chemistry dilutes expensive cobalt and nickel metal recovery becomes less valuable Furthermore the electrolyte is incinerated and lost in todays recycling technology OnTos Advanced Battery recycling process uses greenchemical techniques with minimal environmental impact to reclaim advanced solidstate materials and electrolyte at a fraction of the cost of current methods This effort processed recycled LiCoO2 from computers with an average of 116 cycles and 50 capacity fade The regeneration of recycled material is shown in Figure 1 in which the 003 Xray diffraction peak increases in intensity crystallinity and 2Θ position lithium content with regeneration The position and intensity of the peak are consistent with material capable of cycling lithiumions at theoretical capacity 140 mAg 6 Electrolyte was collected from the same 100 lb batch of batteries the electrolyte material collected has moisture levels below 20ppm Fig 2 shows a gas chromatogram of recovered electrolyte which displays clearly the two solventfractions present These materials can be reused in battery manufacturing Preliminary economic evaluation for the process estimates that that cathode may be recycled and treated for 110th the energy cost of creating cathode material using current recycling technology OnTos method requires several hours of low temperature processing to produce a highly crystalline fully lithiated LiCoO2 compared with smeltprocessing which requires extensive purification and multiple days of high temperature solid state synthesis to return LiCoO2 This work was supported in part by the Vehicle Recycling Partnership and the National Science Foundation Small Business Innovation Research Program Award 0750552 Steven E Sloop is with OnTo Technology LLC 63221 Service RD STE F Bend Oregon 97701 phone 5413897897 fax 4259559617 email ssloopontotechnologycom 0 500 1000 1500 2000 2500 3000 3500 18 185 19 195 20 Counts 2 Theta Fig 1 XRay diffraction peak intensity against 2Θ for the 003 reflection from recycled and regenerated LiCoO2 The treated sample with additive is highly crystalline with 003 matching fully lithiated material REFERENCES 1 C Carroll HighTech Trash National Geographic January 2008 2 C Wheeler An OEM Look at Hybrid Vehicle and Battery Recycling Proceedings from the 12th International Battery Materials Recycling Seminar Exhibit 3 JW Lyman GR Palmer Recycling of NickelMetal Hydride Battery Scrap Hydrogen and Metal Hydride Batteries PD Bennett T Sakai Eds The Electrochemical Society Inc Battery Division Proceedings V 9427 415 4 WJ McLaughlin US Patent 5345033 5 C Siret Closing the Battery Loop Umicore Recycling Solutions Proceedings from the 12th International Battery Materials Recycling Seminar Exhibit 6 R J Gummo M M Thackeray W I F David S Hull Mat Res Bull 27 327 1992 Recycling Advanced Batteries Steven E Sloop T 1000 1500 2000 2500 3000 3500 4000 4500 0 100000 200000 300000 400000 500000 600000 700000 800000 900000 Time Abundance TIC 004D 793 1327 1649 Fig 2 Gas chromatographic trace intensity vs retention time of bulk recovered electrolyte solvents The sample contains 31 alkyl carbonateethylene carbonate water content is 19 ppm Treatment with additive Treatment without additive Raw recovered material Ethyl Methyl Carbonate 19 ppm Water Ethylene Carbonate
Envie sua pergunta para a IA e receba a resposta na hora
Recomendado para você
1
Links compartilhados - Análise de conteúdos
Máquinas Elétricas
UMG
6
A123 Systems: Advanced Battery Energy Storage for Renewable Integration
Máquinas Elétricas
UMG
1
Webinar Series on Battery Testing and Advanced Battery Materials
Máquinas Elétricas
UMG
20
Research on Recycle and Closed-Cycle Diesel Engines for Underwater Applications
Máquinas Elétricas
UMG
3
Closed Cycle Diesel Power Psychrocyle by Charles B. Totten
Máquinas Elétricas
UMG
244
A Design Tool for the Evaluation of Atmosphere Independent Propulsion in Submarines
Máquinas Elétricas
UMG
6
Status of Advanced Battery Technologies for the EV Market
Máquinas Elétricas
UMG
6
Vanadium Redox Flow Batteries: The Future of Grid Energy Storage
Máquinas Elétricas
UMG
190
Entwicklung und Merkmale von Unterseebooten
Máquinas Elétricas
UMG
9
Advanced Underwater Power Systems for Autonomous Underwater Vehicles
Máquinas Elétricas
UMG
Texto de pré-visualização
his abstract introduces results from OnTo Technologys innovative recycling process to produce new materials for new batteries from materials from spent batteries Recycling spent batteries is a growing problem for the consumer electronics electric vehicle industries The electronics industry is facing pressure to see that material is recycled efficiently and responsibly as agreed in the Basal convention 1 The automotive industry already recycles at highrates and plans to maintain this activity into the next generation of vehicles 2 The growth in commodities prices and legislative mandates play an important role in building demand for efficient and environmentally friendly recycling Pyrometallugical and hydrometallurgical technologies are the basis of todays battery recycling options these processes burn dissolve or melt spent battery material and produce hazardous waste byproducts such as slag 35 Cobalt and nickel metal recovery is the general goal for these processes As battery chemistry dilutes expensive cobalt and nickel metal recovery becomes less valuable Furthermore the electrolyte is incinerated and lost in todays recycling technology OnTos Advanced Battery recycling process uses greenchemical techniques with minimal environmental impact to reclaim advanced solidstate materials and electrolyte at a fraction of the cost of current methods This effort processed recycled LiCoO2 from computers with an average of 116 cycles and 50 capacity fade The regeneration of recycled material is shown in Figure 1 in which the 003 Xray diffraction peak increases in intensity crystallinity and 2Θ position lithium content with regeneration The position and intensity of the peak are consistent with material capable of cycling lithiumions at theoretical capacity 140 mAg 6 Electrolyte was collected from the same 100 lb batch of batteries the electrolyte material collected has moisture levels below 20ppm Fig 2 shows a gas chromatogram of recovered electrolyte which displays clearly the two solventfractions present These materials can be reused in battery manufacturing Preliminary economic evaluation for the process estimates that that cathode may be recycled and treated for 110th the energy cost of creating cathode material using current recycling technology OnTos method requires several hours of low temperature processing to produce a highly crystalline fully lithiated LiCoO2 compared with smeltprocessing which requires extensive purification and multiple days of high temperature solid state synthesis to return LiCoO2 This work was supported in part by the Vehicle Recycling Partnership and the National Science Foundation Small Business Innovation Research Program Award 0750552 Steven E Sloop is with OnTo Technology LLC 63221 Service RD STE F Bend Oregon 97701 phone 5413897897 fax 4259559617 email ssloopontotechnologycom 0 500 1000 1500 2000 2500 3000 3500 18 185 19 195 20 Counts 2 Theta Fig 1 XRay diffraction peak intensity against 2Θ for the 003 reflection from recycled and regenerated LiCoO2 The treated sample with additive is highly crystalline with 003 matching fully lithiated material REFERENCES 1 C Carroll HighTech Trash National Geographic January 2008 2 C Wheeler An OEM Look at Hybrid Vehicle and Battery Recycling Proceedings from the 12th International Battery Materials Recycling Seminar Exhibit 3 JW Lyman GR Palmer Recycling of NickelMetal Hydride Battery Scrap Hydrogen and Metal Hydride Batteries PD Bennett T Sakai Eds The Electrochemical Society Inc Battery Division Proceedings V 9427 415 4 WJ McLaughlin US Patent 5345033 5 C Siret Closing the Battery Loop Umicore Recycling Solutions Proceedings from the 12th International Battery Materials Recycling Seminar Exhibit 6 R J Gummo M M Thackeray W I F David S Hull Mat Res Bull 27 327 1992 Recycling Advanced Batteries Steven E Sloop T 1000 1500 2000 2500 3000 3500 4000 4500 0 100000 200000 300000 400000 500000 600000 700000 800000 900000 Time Abundance TIC 004D 793 1327 1649 Fig 2 Gas chromatographic trace intensity vs retention time of bulk recovered electrolyte solvents The sample contains 31 alkyl carbonateethylene carbonate water content is 19 ppm Treatment with additive Treatment without additive Raw recovered material Ethyl Methyl Carbonate 19 ppm Water Ethylene Carbonate