·
Engenharia Mecânica ·
Transferência de Calor
Envie sua pergunta para a IA e receba a resposta na hora
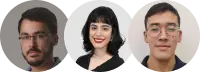
Prefere sua atividade resolvida por um tutor especialista?
- Receba resolvida até o seu prazo
- Converse com o tutor pelo chat
- Garantia de 7 dias contra erros
Recomendado para você
57
Escoamento em Dutos: Capítulo 8 - Condições de Entrada e Escoamento Desenvolvido
Transferência de Calor
PUC
37
Estudo sobre Convecção Natural e Mista em Placas Verticais e Horizontais
Transferência de Calor
PUC
1
Propriedades Termofísicas de Materiais Metálicos em Diversas Temperaturas
Transferência de Calor
PUC
82
Transferência de Calor por Convecção em Engenharia Mecânica
Transferência de Calor
PUC
1
Lista de Questões de Física Térmica
Transferência de Calor
PUC
32
Condução Bidimensional em Regime Permanente: Métodos de Solução da Equação da Difusão de Calor
Transferência de Calor
PUC
4
Problemas de Transferência de Calor em Parabrisas e Paredes de Fornos
Transferência de Calor
PUC
2
Prova de Transferência de Calor - Engenharia Química
Transferência de Calor
PUC
46
Análise do Método Capacitivo em Condução Transiente
Transferência de Calor
PUC
4
Análise de Condução Térmica em Materiais Compostos e Elementos de Reatores Nucleares
Transferência de Calor
PUC
Texto de pré-visualização
Escoamento Externo Escoamento Externo Sc f Sh Sc f x Sh TM f Nu f x Nu TC x x x x x x x x Re Re Pr Re Re Pr TABLE 51 Function Fη for Boundary Layer Along a Flat Plate at Zero Incidence 3 Wilhelm Nusselt 1882 1957 Wilhelm Nusselt a German engineer was born November 25 1882 at Nurnberg Germany He studied machinery at the Technical Universities of BerlinCharlottenburg and Munchen and graduated in 1904 He conducted advanced studies in mathematics and physics and became an assistant to O Knoblauch at the Laboratory for Technical Physics in Munchen He completed his doctoral thesis on the Conductivity of Insulating Materials in 1907 using the Nusselt Sphere for his experiments From 1907 to 1909 he worked as an assistant to Millier in Dresden and qualified for a Professorship with his work on Heat and Momentum Transfer in Tubes In 1915 Nusselt published his pioneering paper The Basic Laws of Heat Transfer in which he first proposed the dimensionless groups now known as the principal parameters in the similarity theory of heat transfer Other famous works were concerned with the film condensation of steam on vertical surfaces the combustion of pulverized coal and the analogy between heat and mass transfer in evaporation Found among the primarily mathematical works of Nusselt are the well known solutions for laminar heat transfer in the entrance region of tubes for heat exchange in crossflow and the basic theory of regenerators Nusselt was a professor at the Technical Universities of Karlsruhe from 19201925 and at Munchen from 1925 until his retirement in 1952 He was awarded the GaussMedal and the Grashof Commemorative Medal Nusselt died in Munchen on September 1 1957 Número de Nusselt local para fluxo de ar normal a um cilindro circular Adaptado com permissão de W H Giedt Trans ASME 71 375 1949 Ecoamento Externo Obtenção das Relações Métodos Experimentais Empíricos Métodos Teóricos ou Numéricos Escoamento Externo Método Empírico uT L T h A T q iV S L S Pr1 Pr2 Pr3 NuL log ReL log n m L L C Nu Re Pr Pr1 Pr2 Pr3 n NuL Pr log ReL log m L n L C Nu Re Pr Para TM n m L L Sc C Sh Re Escoamento externo Reynolds crítico ReL u L u L Re x c laminar flow t Re Re hroughout L x c transition to turbulent flow Re Re at Re R e L x c c x c L x L 5 5 10 Re x c Solução por Similaridade Escoamento laminar Incompressível Regime Estacionário Propriedades constantes Dissipação viscosa desprezível Gradiente de pressão desprezível 2 2 2 2 2 2 0 y D y v x u y T y v T x T u y u y v u x u u y v x u A AB A A u e v não dependem de T e Similarity Solution 2 2 0 y u y v u x u u y v x u Solução por Similaridade Solução de Blasius Blasius H 1908 Grenzschichten in Flussigkeiten mit kleiner Reibung Z Math Phys vol 56 pp 137 x u y x y u x y u u Substituindo em linhas de corrente x v y u u x u f d df u u portanto d u df x u d df u x u y y u 3 2 3 2 2 0 d f f d f d d Substituindo na eq Da QM Condições de contorno u u x e v x u x 0 0 0 1 0 0 0 d df f d df A solução pode ser feita em série ou integração numérica 1 2 1 2 with 099 at 5 50 5 R 0 e x x u u vx u 2 2 0 0 with s y u d f u u vx y d 2 2 0 and 0332 d f d 1 2 2 0664Re 2 x s x Cf x u Da mesma forma para a equação da energia 1 2 0 0 with x s s y h q T T k T y k u vx dT d 1 3 0 and 0332 Pr for Pr 06 dT d 1 2 1 3 0332 Re Pr x x x h x Nu k 1 3 r and P t s s T T T T T 2 2 Pr 0 2 d T f dT d d Pr06 laminar Da mesma forma para a equação de TM A s A A s A A 0 2 2 2 2 d f d Sc d d A A 60 0 332 3 1 0 Sc para Sc d d com A 3 1 1 3 1 2 0 0 60 332Re 0 Sc Sc Sc D x h Sh x u D y D n h sendo c x AB x m x A AB y A AB A S A A x m laminar Cálculo dos valores médios 0 1 x s x sdx x 1 2 1328 Re x Cf x Temperatura de filme 2 s f T T T 60 Pr Pr 664Re 0 2 60 Pr Pr Re 664 0 1 Pr 0 332 1 13 2 1 2 1 13 2 1 0 2 1 2 1 3 1 0 x f x x x x x f x x f x x x k h x Nu ou h h u x k h dx x u x k h dx x h 60 0 664Re 13 1 2 Sc Sc D x h Sh maneira similar De x AB x m x Outras correlações Para Pr1 metais líquidos t podese considerar velocidade uniforme uu solução de Kays e Crawford 1980 Pr Re 100 0 05 Pr 0 565 2 1 Peclet de número Pe onde e Pe Pe Nu x x x Uma correlação geral para placa isotérmica Churchill e Ozoe 1973 100 0 0468 Pr 1 Pr 3387Re 0 3 14 2 13 2 1 x x x Pe Nu x x Nu Nu sendo Turbulent Flow Escoamento Turbulento Parametros locais a partir de dados experimentais Schlichting 1968 Prof Dr phil Hermann Schlichting 10 Re 10 15 10 Re 0 0592Re 8 7 7 5 1 x x x f x de erro para C c t turb x turb ou Sc f x Pr 0 37 Re 5 1 Utilizando a analogia de Reynolds modificada Cap 6 3000 60 0 0296Re Re 60 Pr 60 Pr 0 0296Re Pr Re 6 Pr 2 13 5 4 13 5 4 3 2 Sc Sc Sc St Sh St Nu cap St C x x m x x x x f Camada limite mista 1 0 1 c c x L L am turb x h h dx h dx L Substituindo e assumindo 5 Rexc 5 10 4 5 1 3 0037 Re 871 Pr L L Nu 5 8 5 5 10 Re 10 Re 10 5 60 Pr 60 cx L Se xcL 4 5 1 3 0037 Re 871 Pr L L Nu Da mesma forma para TM 4 5 1 3 0037 Re 871 Pr L L Nu 5 8 5 5 10 Re 10 Re 10 5 3000 60 cx L Sc Se xcL 4 5 1 3 0037 Re 871 Pr L L Nu L Sh L Sh 13 Sc Sc13 Special Cases Special Cases Unheated Starting Length USL andor Uniform Heat Flux For both uniform surface temperature UST and uniform surface heat flux USF the effect of the USL on the local Nusselt number may be represented as follows 0 1 3 0 1 Re Pr x x b a m x x Nu Nu x Nu C Laminar Turbulent UST USF UST USF a 34 34 910 910 b 13 13 19 19 C 0332 0453 00296 00308 m 12 12 45 45 Special Cases cont Valores médios para UST s x s q h T T 1 1 2 0 laminar 1 2 for throughout flo 8 for througho w turbulent flo ut w p p p p L L L Nu Nu L L p p 1 laminarturbulent flow numerical integration f 1 or c c L x L L am turb x h h h dx h dx L USF s s x q T T h s s q q A Treatment of NonConstant Property Effects Evaluate properties at the film temperature 2 s f T T T L s s q h A T T Problem Conveyor Belt Problem 724 Convection cooling of steel plates on a conveyor by air in parallel flow KNOWN Plate dimensions and initial temperature Velocity and temperature of air in parallel flow over plates FIND Initial rate of heat transfer from plate Rate of change of plate temperature Problem Conveyor Belt cont PROPERTIES Table A1 AISI 1010 steel 573K kp 492 WmK c 549 JkgK 7832 kgm3 Table A4 Air p 1 atm Tf 433K 304 106 m2s k 00361 WmK Pr 0688 ANALYSIS The initial rate of heat transfer from a plate is 2 s i i q 2h A T T 2h L T T With 6 2 5 ReL u L 10 m s 1m 304 10 m s 329 10 flow is laminar over the entire surface Hence L 1 2 1 3 1 2 1 3 5 L Nu 0664Re Pr 0664 329 10 0688 336 L 2 h k L Nu 00361W m K 1m 336 121W m K 2 2 q 2 121W m K 1m 300 20 C 6780W SCHEMATIC Air T 20 C o oo u 10 ms oo T C i o 300 q 6 mm L 1 m q L 1 m ASSUMPTIONS 1 Negligible radiation 2 Negligible effect of conveyor velocity on boundary layer development 3 Plates are isothermal 4 Negligible heat transfer from edges of plate 5 5 Rexc 5 10 6 Constant properties Problem Conveyor Belt cont COMMENTS 1 With 4 p Bi h 2 k 74 10 use of the lumped capacitance method is appropriate 2 Despite the large plate temperature and the small convection coefficient if adjoining plates are in close proximity radiation exchange with the surroundings will be small and the assumption of negligible radiation is justifiable Performing an energy balance at an instant of time for a control surface about the plate out st E E 2 2 i i L c dT h 2L T T dt 2 3 i 2 121W m K 300 20 C dT 026 Cs dt 7832 kg m 0006m 549J kg K Cylinder in Cross Flow Cilindro com escoamento transversal Stagnation point Location of zero velocity and maximum pressure 0 u Followed by boundary layer development under a favorable pressure gradient and hence acceleration of the free stream flow dp dx 0 0 du dx As the rear of the cylinder is approached the pressure must begin to increase Hence there is a minimum in the pressure distribution px after which boundary layer development occurs under the influence of an adverse pressure gradient 0 0 dp dx du dx Cylinder in Cross Flow cont Separation occurs when the velocity gradient reduces to zero 0 du dy y and is accompanied by flow reversal and a downstream wake Location of separation depends on boundary layer transition ReD VD VD 80º 140º Cylinder in Cross Flow cont The dimensionless form of the drag force is 2 Figure 78 2 D D f F C A V CD 2105 Re Cylinder in Cross Flow cont The Average Nusselt Number NuD hD k Churchill and Bernstein Correlation 4 5 58 1 2 1 3 1 4 2 3 062Re Pr Re 03 1 282000 1 04 Pr D D D Nu Cylinders of Noncircular Cross Section Re Pr1 3 m D D Nu C Table 73 C m ReDPr02 Re Pr1 3 m D D Nu C Correlação de Zhukauskas 0 36 10 Pr 0 37 10 Pr 10 Re 1 500 Pr 70 Pr Pr Pr Re 6 4 1 n n C Nu D S n m D Todas as propriedades avaliadas em T exceto Prs avaliada em Ts Tube Banks Feixe de tubos com escoamento transversal max ST V V S D T Alinhado e Quincôncio Alinhado Quincôncio if 2 max ST V V S D S D D T S D T if 2 max 2 ST V V S D S D D T S D D or Tube Banks cont Flow Conditions Average Nusselt Number for an Isothermal Array 1 4 036 2 Re max Pr Pr Pr m D D s Nu C C 2 Table 77 Table 78 C m C All properties are evaluated at except for Prs 2 i o T T Tube Banks cont Fluid Outlet Temperature To s o s i T T p T T DNh exp T T VN S c T L N N N x What may be said about To as N Total Heat Rate s m q hA T sA N DL s i s o m s i s o T T T T T T T n T T Pressure Drop 2 max 2 L V p N f Figures 713 and 714 f Spheres and Packed Beds The Sphere and Packed Beds Flow over a sphere Boundary layer development is similar to that for flow over a cylinder involving transition and separation Gas Flow through a Packed Bed Flow is characterized by tortuous paths through a bed of fixed particles Large surface area per unit volume renders configuration desirable for the transfer and storage of thermal energy 1 4 1 2 2 3 04 2 04Re 006Re Pr D D D s Nu Figure 78 D C What are the limiting values of the Nusselt number and the convection coefficient for slow flows over small spheres Spheres and Packed Beds cont For a packed bed of spheres 0575 206 Re void fraction 03 05 H D j p t m q hA T total surface area of particles Ap t exp p t s o s i c b p hA T T T T VA c crosssectional area of bed Ac b Jets Gas Jet Impingement Characterized by large convection coefficients and used for cooling and heating in numerous manufacturing electronic and aeronautic applications Flow and Heat Transfer for a Circular or Rectangular Jet Significant Features Mixing and velocity profile development in the free jet Stagnation point and zone Velocity profile development in the wall jet Jets Local Nusselt number distribution Average Nusselt number from Fig 717 h r h e h r hD Nu f Re Pr A H D k V D Re A Correlations Section 772 Jet Arrays Slot Jets What is the nature and effect of jet interactions and discharge conditions Nusselt number correlations for arrays of circular and slot jets Section 772 Problem Extrusion Process Problem 763 Cooling of extruded copper wire by convection and radiation KNOWN Velocity diameter initial temperature and properties of extruded wire Temperature and velocity of air Temperature of surroundings FIND a Differential equation for temperature distribution Tx along the wire b Exact solution for negligible radiation and corresponding value of temperature at prescribed length x L 5m of wire c Effect of radiation on temperature of wire at prescribed length Effect of wire velocity and emissivity on temperature distribution Problem Extrusion Process cont SCHEMATIC T 25 C o oo V 5 ms dx Air dqrad dqconv D 5 mm V 02 ms e Tsur o 25 C ASSUMPTIONS 1 Negligible variation of wire temperature in radial direction 2 Negligible effect of axial conduction along the wire 3 Constant properties 4 Radiation exchange between small surface and large enclosure 5 Motion of wire has a negligible effect on the convection coefficient Ve V PROPERTIES Copper 3 8900kg m cp 400J kg K 055 Air k 0037 W m K 5 2 3 10 m s Pr 069 ANALYSIS a Applying conservation of energy to a stationary control surface through which the wire moves steadystate conditions exist and in out E E 0 Hence with inflow due to advection and outflow due to advection convection and radiation e c p e c p conv rad V A c T V A c T dT dq dq 0 Problem Extrusion Process cont 2 4 4 e p sur V D 4 c dT Ddx h T T T T 0 4 4sur e p dT 4 h T T T T dx V Dc 1 Alternatively if the control surface is fixed to the wire conditions are transient and the energy balance is of the form out st E E or 2 4 4sur p D dT Ddx h T T T T dx c 4 dt 4 4sur p dT 4 h T T T T dt Dc Dividing the left and righthand sides of the equation by dxdt and Ve dx dt respectively Eq 1 is obtained b Neglecting radiation separating variables and integrating Eq 1 becomes i T x T 0 e p dT 4h dx T T V Dc i e p T T 4h x ln T T V Dc i e p 4hx T T T T exp V Dc 2 Problem Extrusion Process cont With 5 2 ReD VD 5m s 0005m 3 10 m s 833 the ChurchillBernstein correlation yields D 4 5 1 2 1 3 58 1 4 2 3 062 833 069 833 Nu 03 1 144 282000 1 04 069 D 2 0037W m K k h Nu 144 107W m K D 0005m Hence applying Eq 2 at x L 2 o 3 4 107W m K 5m T 25 C 575 C exp 8900kg m 02ms 0005m 400J kg K To 340 C Hence radiation makes a discernable contribution to cooling of the wire c Numerically integrating from x 0 to x L 50m we obtain To 309 C Problem Extrusion Process cont The speed with which the wire is drawn from the extruder has a significant influence on the temperature distribution The temperature decay decreases with increasing Ve due to the increasing effect of advection on energy transfer in the x direction The effect of the surface emissivity is less pronounced although as expected the temperature decay becomes more pronounced with increasing COMMENTS 1 A critical parameter in wire extrusion processes is the coiling temperature that is the temperature at which the wire may be safely coiled for subsequent storage or shipment The larger the production rate Ve the longer the cooling distance needed to achieve a desired coiling temperature 2 Cooling may be enhanced by increasing the crossflow velocity and the specific effect of V may also be explored 0 1 2 3 4 5 Distance from extruder exit xm 100 200 300 400 500 600 Wire temperature TC Ve05 ms Ve02 ms Ve01 ms 0 1 2 3 4 5 Distance from extruder exit xm 300 350 400 450 500 550 600 Wire temperature TC eps08 eps055 eps0 Parametric conditions reveal the following distributions Problem Thermocouple Junction Problem 778 Measurement of combustion gas temperature with a spherical thermocouple junction KNOWN Velocity and temperature of combustion gases Diameter and emissivity of thermocouple junction Combustor temperature FIND a Time to achieve 98 of maximum thermocouple temperature rise for negligible radiation b Steadystate thermocouple temperature c Effect of gas velocity and thermocouple emissivity on measurement error SCHEMATIC ASSUMPTIONS 1 Validity of lumped capacitance analysis 2 Constant properties 3 Negligible conduction through lead wires 4 Radiation exchange between small surface and a large enclosure parts b and c Problem Thermocouple Junction cont PROPERTIES Thermocouple 01 10 k 100 WmK c 385 JkgK 8920 kgm3 Gases k 005 WmK 50 106 m2s Pr 069 ANALYSIS a If the lumped capacitance analysis may be used it follows from Equation 55 that i s T T Vc D c t ln ln 50 T T hA 6h Neglecting the viscosity ratio correlation for variable property effects use of V 5 ms with the Whitaker correlation yields 1 2 2 3 04 D D D Nu hD k 2 04Re 006Re Pr D 6 2 5m s 0001m VD Re 100 50 10 m s 1 2 2 3 04 2 005W m K h 2 04 100 006 100 069 328W m K 0001m Since Bi h ro 3 k 55 104 the lumped capacitance method may be used 3 2 0001m 8920kg m 385J kg K t ln 50 683s 6 328W m K Problem Thermocouple Junction cont b Performing an energy balance on the junction qconv qrad Hence evaluating radiation exchange from Equation 17 and with 05 4 4 s s c hA T T A T T 8 2 4 4 4 4 2 05 567 10 W m K 1000 T K T 400 K 328W m K T 936 K Parametric calculations to determine the effects of V and yield the following results 0 5 10 15 20 25 Velocity Vms 900 950 1000 Temperature TK Emissivity epsilon 05 01 02 03 04 05 06 07 08 09 1 Emissivity 890 910 930 950 970 990 Temperature TK Velocity V 5 ms Problem Thermocouple Junction cont Since the temperature recorded by the thermocouple junction increases with increasing V and decreasing the measurement error T T decreases with increasing V and decreasing The error is due to net radiative transfer from the junction which depresses T and hence should decrease with decreasing For a prescribed heat loss the temperature difference T T decreases with decreasing convection resistance and hence with increasing hV COMMENTS To infer the actual gas temperature 1000 K from the measured result 936 K correction would have to be made for radiation exchange with the cold surroundings What measures may be taken to reduce the error associated with radiation effects
Envie sua pergunta para a IA e receba a resposta na hora
Recomendado para você
57
Escoamento em Dutos: Capítulo 8 - Condições de Entrada e Escoamento Desenvolvido
Transferência de Calor
PUC
37
Estudo sobre Convecção Natural e Mista em Placas Verticais e Horizontais
Transferência de Calor
PUC
1
Propriedades Termofísicas de Materiais Metálicos em Diversas Temperaturas
Transferência de Calor
PUC
82
Transferência de Calor por Convecção em Engenharia Mecânica
Transferência de Calor
PUC
1
Lista de Questões de Física Térmica
Transferência de Calor
PUC
32
Condução Bidimensional em Regime Permanente: Métodos de Solução da Equação da Difusão de Calor
Transferência de Calor
PUC
4
Problemas de Transferência de Calor em Parabrisas e Paredes de Fornos
Transferência de Calor
PUC
2
Prova de Transferência de Calor - Engenharia Química
Transferência de Calor
PUC
46
Análise do Método Capacitivo em Condução Transiente
Transferência de Calor
PUC
4
Análise de Condução Térmica em Materiais Compostos e Elementos de Reatores Nucleares
Transferência de Calor
PUC
Texto de pré-visualização
Escoamento Externo Escoamento Externo Sc f Sh Sc f x Sh TM f Nu f x Nu TC x x x x x x x x Re Re Pr Re Re Pr TABLE 51 Function Fη for Boundary Layer Along a Flat Plate at Zero Incidence 3 Wilhelm Nusselt 1882 1957 Wilhelm Nusselt a German engineer was born November 25 1882 at Nurnberg Germany He studied machinery at the Technical Universities of BerlinCharlottenburg and Munchen and graduated in 1904 He conducted advanced studies in mathematics and physics and became an assistant to O Knoblauch at the Laboratory for Technical Physics in Munchen He completed his doctoral thesis on the Conductivity of Insulating Materials in 1907 using the Nusselt Sphere for his experiments From 1907 to 1909 he worked as an assistant to Millier in Dresden and qualified for a Professorship with his work on Heat and Momentum Transfer in Tubes In 1915 Nusselt published his pioneering paper The Basic Laws of Heat Transfer in which he first proposed the dimensionless groups now known as the principal parameters in the similarity theory of heat transfer Other famous works were concerned with the film condensation of steam on vertical surfaces the combustion of pulverized coal and the analogy between heat and mass transfer in evaporation Found among the primarily mathematical works of Nusselt are the well known solutions for laminar heat transfer in the entrance region of tubes for heat exchange in crossflow and the basic theory of regenerators Nusselt was a professor at the Technical Universities of Karlsruhe from 19201925 and at Munchen from 1925 until his retirement in 1952 He was awarded the GaussMedal and the Grashof Commemorative Medal Nusselt died in Munchen on September 1 1957 Número de Nusselt local para fluxo de ar normal a um cilindro circular Adaptado com permissão de W H Giedt Trans ASME 71 375 1949 Ecoamento Externo Obtenção das Relações Métodos Experimentais Empíricos Métodos Teóricos ou Numéricos Escoamento Externo Método Empírico uT L T h A T q iV S L S Pr1 Pr2 Pr3 NuL log ReL log n m L L C Nu Re Pr Pr1 Pr2 Pr3 n NuL Pr log ReL log m L n L C Nu Re Pr Para TM n m L L Sc C Sh Re Escoamento externo Reynolds crítico ReL u L u L Re x c laminar flow t Re Re hroughout L x c transition to turbulent flow Re Re at Re R e L x c c x c L x L 5 5 10 Re x c Solução por Similaridade Escoamento laminar Incompressível Regime Estacionário Propriedades constantes Dissipação viscosa desprezível Gradiente de pressão desprezível 2 2 2 2 2 2 0 y D y v x u y T y v T x T u y u y v u x u u y v x u A AB A A u e v não dependem de T e Similarity Solution 2 2 0 y u y v u x u u y v x u Solução por Similaridade Solução de Blasius Blasius H 1908 Grenzschichten in Flussigkeiten mit kleiner Reibung Z Math Phys vol 56 pp 137 x u y x y u x y u u Substituindo em linhas de corrente x v y u u x u f d df u u portanto d u df x u d df u x u y y u 3 2 3 2 2 0 d f f d f d d Substituindo na eq Da QM Condições de contorno u u x e v x u x 0 0 0 1 0 0 0 d df f d df A solução pode ser feita em série ou integração numérica 1 2 1 2 with 099 at 5 50 5 R 0 e x x u u vx u 2 2 0 0 with s y u d f u u vx y d 2 2 0 and 0332 d f d 1 2 2 0664Re 2 x s x Cf x u Da mesma forma para a equação da energia 1 2 0 0 with x s s y h q T T k T y k u vx dT d 1 3 0 and 0332 Pr for Pr 06 dT d 1 2 1 3 0332 Re Pr x x x h x Nu k 1 3 r and P t s s T T T T T 2 2 Pr 0 2 d T f dT d d Pr06 laminar Da mesma forma para a equação de TM A s A A s A A 0 2 2 2 2 d f d Sc d d A A 60 0 332 3 1 0 Sc para Sc d d com A 3 1 1 3 1 2 0 0 60 332Re 0 Sc Sc Sc D x h Sh x u D y D n h sendo c x AB x m x A AB y A AB A S A A x m laminar Cálculo dos valores médios 0 1 x s x sdx x 1 2 1328 Re x Cf x Temperatura de filme 2 s f T T T 60 Pr Pr 664Re 0 2 60 Pr Pr Re 664 0 1 Pr 0 332 1 13 2 1 2 1 13 2 1 0 2 1 2 1 3 1 0 x f x x x x x f x x f x x x k h x Nu ou h h u x k h dx x u x k h dx x h 60 0 664Re 13 1 2 Sc Sc D x h Sh maneira similar De x AB x m x Outras correlações Para Pr1 metais líquidos t podese considerar velocidade uniforme uu solução de Kays e Crawford 1980 Pr Re 100 0 05 Pr 0 565 2 1 Peclet de número Pe onde e Pe Pe Nu x x x Uma correlação geral para placa isotérmica Churchill e Ozoe 1973 100 0 0468 Pr 1 Pr 3387Re 0 3 14 2 13 2 1 x x x Pe Nu x x Nu Nu sendo Turbulent Flow Escoamento Turbulento Parametros locais a partir de dados experimentais Schlichting 1968 Prof Dr phil Hermann Schlichting 10 Re 10 15 10 Re 0 0592Re 8 7 7 5 1 x x x f x de erro para C c t turb x turb ou Sc f x Pr 0 37 Re 5 1 Utilizando a analogia de Reynolds modificada Cap 6 3000 60 0 0296Re Re 60 Pr 60 Pr 0 0296Re Pr Re 6 Pr 2 13 5 4 13 5 4 3 2 Sc Sc Sc St Sh St Nu cap St C x x m x x x x f Camada limite mista 1 0 1 c c x L L am turb x h h dx h dx L Substituindo e assumindo 5 Rexc 5 10 4 5 1 3 0037 Re 871 Pr L L Nu 5 8 5 5 10 Re 10 Re 10 5 60 Pr 60 cx L Se xcL 4 5 1 3 0037 Re 871 Pr L L Nu Da mesma forma para TM 4 5 1 3 0037 Re 871 Pr L L Nu 5 8 5 5 10 Re 10 Re 10 5 3000 60 cx L Sc Se xcL 4 5 1 3 0037 Re 871 Pr L L Nu L Sh L Sh 13 Sc Sc13 Special Cases Special Cases Unheated Starting Length USL andor Uniform Heat Flux For both uniform surface temperature UST and uniform surface heat flux USF the effect of the USL on the local Nusselt number may be represented as follows 0 1 3 0 1 Re Pr x x b a m x x Nu Nu x Nu C Laminar Turbulent UST USF UST USF a 34 34 910 910 b 13 13 19 19 C 0332 0453 00296 00308 m 12 12 45 45 Special Cases cont Valores médios para UST s x s q h T T 1 1 2 0 laminar 1 2 for throughout flo 8 for througho w turbulent flo ut w p p p p L L L Nu Nu L L p p 1 laminarturbulent flow numerical integration f 1 or c c L x L L am turb x h h h dx h dx L USF s s x q T T h s s q q A Treatment of NonConstant Property Effects Evaluate properties at the film temperature 2 s f T T T L s s q h A T T Problem Conveyor Belt Problem 724 Convection cooling of steel plates on a conveyor by air in parallel flow KNOWN Plate dimensions and initial temperature Velocity and temperature of air in parallel flow over plates FIND Initial rate of heat transfer from plate Rate of change of plate temperature Problem Conveyor Belt cont PROPERTIES Table A1 AISI 1010 steel 573K kp 492 WmK c 549 JkgK 7832 kgm3 Table A4 Air p 1 atm Tf 433K 304 106 m2s k 00361 WmK Pr 0688 ANALYSIS The initial rate of heat transfer from a plate is 2 s i i q 2h A T T 2h L T T With 6 2 5 ReL u L 10 m s 1m 304 10 m s 329 10 flow is laminar over the entire surface Hence L 1 2 1 3 1 2 1 3 5 L Nu 0664Re Pr 0664 329 10 0688 336 L 2 h k L Nu 00361W m K 1m 336 121W m K 2 2 q 2 121W m K 1m 300 20 C 6780W SCHEMATIC Air T 20 C o oo u 10 ms oo T C i o 300 q 6 mm L 1 m q L 1 m ASSUMPTIONS 1 Negligible radiation 2 Negligible effect of conveyor velocity on boundary layer development 3 Plates are isothermal 4 Negligible heat transfer from edges of plate 5 5 Rexc 5 10 6 Constant properties Problem Conveyor Belt cont COMMENTS 1 With 4 p Bi h 2 k 74 10 use of the lumped capacitance method is appropriate 2 Despite the large plate temperature and the small convection coefficient if adjoining plates are in close proximity radiation exchange with the surroundings will be small and the assumption of negligible radiation is justifiable Performing an energy balance at an instant of time for a control surface about the plate out st E E 2 2 i i L c dT h 2L T T dt 2 3 i 2 121W m K 300 20 C dT 026 Cs dt 7832 kg m 0006m 549J kg K Cylinder in Cross Flow Cilindro com escoamento transversal Stagnation point Location of zero velocity and maximum pressure 0 u Followed by boundary layer development under a favorable pressure gradient and hence acceleration of the free stream flow dp dx 0 0 du dx As the rear of the cylinder is approached the pressure must begin to increase Hence there is a minimum in the pressure distribution px after which boundary layer development occurs under the influence of an adverse pressure gradient 0 0 dp dx du dx Cylinder in Cross Flow cont Separation occurs when the velocity gradient reduces to zero 0 du dy y and is accompanied by flow reversal and a downstream wake Location of separation depends on boundary layer transition ReD VD VD 80º 140º Cylinder in Cross Flow cont The dimensionless form of the drag force is 2 Figure 78 2 D D f F C A V CD 2105 Re Cylinder in Cross Flow cont The Average Nusselt Number NuD hD k Churchill and Bernstein Correlation 4 5 58 1 2 1 3 1 4 2 3 062Re Pr Re 03 1 282000 1 04 Pr D D D Nu Cylinders of Noncircular Cross Section Re Pr1 3 m D D Nu C Table 73 C m ReDPr02 Re Pr1 3 m D D Nu C Correlação de Zhukauskas 0 36 10 Pr 0 37 10 Pr 10 Re 1 500 Pr 70 Pr Pr Pr Re 6 4 1 n n C Nu D S n m D Todas as propriedades avaliadas em T exceto Prs avaliada em Ts Tube Banks Feixe de tubos com escoamento transversal max ST V V S D T Alinhado e Quincôncio Alinhado Quincôncio if 2 max ST V V S D S D D T S D T if 2 max 2 ST V V S D S D D T S D D or Tube Banks cont Flow Conditions Average Nusselt Number for an Isothermal Array 1 4 036 2 Re max Pr Pr Pr m D D s Nu C C 2 Table 77 Table 78 C m C All properties are evaluated at except for Prs 2 i o T T Tube Banks cont Fluid Outlet Temperature To s o s i T T p T T DNh exp T T VN S c T L N N N x What may be said about To as N Total Heat Rate s m q hA T sA N DL s i s o m s i s o T T T T T T T n T T Pressure Drop 2 max 2 L V p N f Figures 713 and 714 f Spheres and Packed Beds The Sphere and Packed Beds Flow over a sphere Boundary layer development is similar to that for flow over a cylinder involving transition and separation Gas Flow through a Packed Bed Flow is characterized by tortuous paths through a bed of fixed particles Large surface area per unit volume renders configuration desirable for the transfer and storage of thermal energy 1 4 1 2 2 3 04 2 04Re 006Re Pr D D D s Nu Figure 78 D C What are the limiting values of the Nusselt number and the convection coefficient for slow flows over small spheres Spheres and Packed Beds cont For a packed bed of spheres 0575 206 Re void fraction 03 05 H D j p t m q hA T total surface area of particles Ap t exp p t s o s i c b p hA T T T T VA c crosssectional area of bed Ac b Jets Gas Jet Impingement Characterized by large convection coefficients and used for cooling and heating in numerous manufacturing electronic and aeronautic applications Flow and Heat Transfer for a Circular or Rectangular Jet Significant Features Mixing and velocity profile development in the free jet Stagnation point and zone Velocity profile development in the wall jet Jets Local Nusselt number distribution Average Nusselt number from Fig 717 h r h e h r hD Nu f Re Pr A H D k V D Re A Correlations Section 772 Jet Arrays Slot Jets What is the nature and effect of jet interactions and discharge conditions Nusselt number correlations for arrays of circular and slot jets Section 772 Problem Extrusion Process Problem 763 Cooling of extruded copper wire by convection and radiation KNOWN Velocity diameter initial temperature and properties of extruded wire Temperature and velocity of air Temperature of surroundings FIND a Differential equation for temperature distribution Tx along the wire b Exact solution for negligible radiation and corresponding value of temperature at prescribed length x L 5m of wire c Effect of radiation on temperature of wire at prescribed length Effect of wire velocity and emissivity on temperature distribution Problem Extrusion Process cont SCHEMATIC T 25 C o oo V 5 ms dx Air dqrad dqconv D 5 mm V 02 ms e Tsur o 25 C ASSUMPTIONS 1 Negligible variation of wire temperature in radial direction 2 Negligible effect of axial conduction along the wire 3 Constant properties 4 Radiation exchange between small surface and large enclosure 5 Motion of wire has a negligible effect on the convection coefficient Ve V PROPERTIES Copper 3 8900kg m cp 400J kg K 055 Air k 0037 W m K 5 2 3 10 m s Pr 069 ANALYSIS a Applying conservation of energy to a stationary control surface through which the wire moves steadystate conditions exist and in out E E 0 Hence with inflow due to advection and outflow due to advection convection and radiation e c p e c p conv rad V A c T V A c T dT dq dq 0 Problem Extrusion Process cont 2 4 4 e p sur V D 4 c dT Ddx h T T T T 0 4 4sur e p dT 4 h T T T T dx V Dc 1 Alternatively if the control surface is fixed to the wire conditions are transient and the energy balance is of the form out st E E or 2 4 4sur p D dT Ddx h T T T T dx c 4 dt 4 4sur p dT 4 h T T T T dt Dc Dividing the left and righthand sides of the equation by dxdt and Ve dx dt respectively Eq 1 is obtained b Neglecting radiation separating variables and integrating Eq 1 becomes i T x T 0 e p dT 4h dx T T V Dc i e p T T 4h x ln T T V Dc i e p 4hx T T T T exp V Dc 2 Problem Extrusion Process cont With 5 2 ReD VD 5m s 0005m 3 10 m s 833 the ChurchillBernstein correlation yields D 4 5 1 2 1 3 58 1 4 2 3 062 833 069 833 Nu 03 1 144 282000 1 04 069 D 2 0037W m K k h Nu 144 107W m K D 0005m Hence applying Eq 2 at x L 2 o 3 4 107W m K 5m T 25 C 575 C exp 8900kg m 02ms 0005m 400J kg K To 340 C Hence radiation makes a discernable contribution to cooling of the wire c Numerically integrating from x 0 to x L 50m we obtain To 309 C Problem Extrusion Process cont The speed with which the wire is drawn from the extruder has a significant influence on the temperature distribution The temperature decay decreases with increasing Ve due to the increasing effect of advection on energy transfer in the x direction The effect of the surface emissivity is less pronounced although as expected the temperature decay becomes more pronounced with increasing COMMENTS 1 A critical parameter in wire extrusion processes is the coiling temperature that is the temperature at which the wire may be safely coiled for subsequent storage or shipment The larger the production rate Ve the longer the cooling distance needed to achieve a desired coiling temperature 2 Cooling may be enhanced by increasing the crossflow velocity and the specific effect of V may also be explored 0 1 2 3 4 5 Distance from extruder exit xm 100 200 300 400 500 600 Wire temperature TC Ve05 ms Ve02 ms Ve01 ms 0 1 2 3 4 5 Distance from extruder exit xm 300 350 400 450 500 550 600 Wire temperature TC eps08 eps055 eps0 Parametric conditions reveal the following distributions Problem Thermocouple Junction Problem 778 Measurement of combustion gas temperature with a spherical thermocouple junction KNOWN Velocity and temperature of combustion gases Diameter and emissivity of thermocouple junction Combustor temperature FIND a Time to achieve 98 of maximum thermocouple temperature rise for negligible radiation b Steadystate thermocouple temperature c Effect of gas velocity and thermocouple emissivity on measurement error SCHEMATIC ASSUMPTIONS 1 Validity of lumped capacitance analysis 2 Constant properties 3 Negligible conduction through lead wires 4 Radiation exchange between small surface and a large enclosure parts b and c Problem Thermocouple Junction cont PROPERTIES Thermocouple 01 10 k 100 WmK c 385 JkgK 8920 kgm3 Gases k 005 WmK 50 106 m2s Pr 069 ANALYSIS a If the lumped capacitance analysis may be used it follows from Equation 55 that i s T T Vc D c t ln ln 50 T T hA 6h Neglecting the viscosity ratio correlation for variable property effects use of V 5 ms with the Whitaker correlation yields 1 2 2 3 04 D D D Nu hD k 2 04Re 006Re Pr D 6 2 5m s 0001m VD Re 100 50 10 m s 1 2 2 3 04 2 005W m K h 2 04 100 006 100 069 328W m K 0001m Since Bi h ro 3 k 55 104 the lumped capacitance method may be used 3 2 0001m 8920kg m 385J kg K t ln 50 683s 6 328W m K Problem Thermocouple Junction cont b Performing an energy balance on the junction qconv qrad Hence evaluating radiation exchange from Equation 17 and with 05 4 4 s s c hA T T A T T 8 2 4 4 4 4 2 05 567 10 W m K 1000 T K T 400 K 328W m K T 936 K Parametric calculations to determine the effects of V and yield the following results 0 5 10 15 20 25 Velocity Vms 900 950 1000 Temperature TK Emissivity epsilon 05 01 02 03 04 05 06 07 08 09 1 Emissivity 890 910 930 950 970 990 Temperature TK Velocity V 5 ms Problem Thermocouple Junction cont Since the temperature recorded by the thermocouple junction increases with increasing V and decreasing the measurement error T T decreases with increasing V and decreasing The error is due to net radiative transfer from the junction which depresses T and hence should decrease with decreasing For a prescribed heat loss the temperature difference T T decreases with decreasing convection resistance and hence with increasing hV COMMENTS To infer the actual gas temperature 1000 K from the measured result 936 K correction would have to be made for radiation exchange with the cold surroundings What measures may be taken to reduce the error associated with radiation effects