·
Engenharia de Produção ·
Gestão de Produção
Envie sua pergunta para a IA e receba a resposta na hora
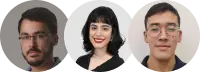
Prefere sua atividade resolvida por um tutor especialista?
- Receba resolvida até o seu prazo
- Converse com o tutor pelo chat
- Garantia de 7 dias contra erros
Recomendado para você
17
Disponibilidade de Equipamentos na Manutenção Industrial
Gestão de Produção
UNIJUI
1
Planejamento Operacional e Processos de Distribuição
Gestão de Produção
UNIJUI
12
Cronoanálise: Métodos e Tempo Padrão na Produção
Gestão de Produção
UNIJUI
19
Estudo de Tempo e Métodos: Análise e Melhorias de Processos
Gestão de Produção
UNIJUI
20
Estudo de Tempos e Métodos na Organização da Produção
Gestão de Produção
UNIJUI
32
Mapeamento do Fluxo de Valor do Projeto Executivo de Arquitetura em um Órgão Público
Gestão de Produção
UNIJUI
Texto de pré-visualização
JOURNAL OF LEAN SYSTEMS 2016 Vol 2 Nº 3 pp 87106 httpleansystemufscbr 87 Lean office mapeamento do fluxo de valor administrativo em rotina de trabalho de órgão público Lean office administrative value stream mapping in a routine of work in a public organ Carla Beatriz da Luz Peralta carlablpgmailcom Fernando Henrique Lermen fernandolermenhotmailcom Eduardo de Leon Martins dududeleonhotmailcom Vander Luiz da Silva vanderluizhotmailcom Márcia Elisa Soares Echeveste echevestemargmailcom Universidade Federal do Rio Grande do Sul UFRGS Porto Alegre Rio Grande do Sul Article History Submitted 2016 11 17 Revised 2016 12 14 Accepted 2016 12 15 Resumo No decorrer dos anos a manufatura Lean se encontrou em crescente desenvolvimento e vem conquistando cada vez mais espaços em seus universos de atuação contudo as organizações que decidem aplicar a filosofia Lean em seus processos focam apenas em processos de manufatura em detrimento das áreas administrativas Com base nisso o presente estudo visou propor melhorias para uma família de processos administrativos correntes em um Órgão Publico Federal aplicando princípios e conceitos do Lean Office Este trabalho foi desenvolvido por meio de análise dos registros históricos em sistema de informação e Mapeamento do Fluxo de Valor Foi possível selecionar uma famíliaalvo para o estudo mapear o estado atual dos processos identificando seus lead times e perdasdesperdícios criar um plano de ação e posteriormente propor melhorias exequíveis com o objetivo de reduzilas ou eliminálas Contudo notase que há uma redução de em torno 82 no tempo entre as etapas iniciais e finais do processo em evidência conferindo que os princípios enxutos demonstramse capazes de ofertar bons resultados também para os setores administrativos Palavras Chaves Lean Office Mapeamento do Fluxo de Valor Gestão de Processos Desperdícios Administração Pública Abstract Over the years Lean manufacturing was found in increasing development and has been gaining more space in their respective universes however organizations that decide to apply the philosophy Lean in its processes focus only on manufacturing processes at the expense of areas administrative Based on this the present study aimed to propose improvements to a family of current administrative processes in a Federal Public Agency applying principles and concepts of Lean Office This work was developed through analysis of historical records information system and Value Stream Mapping it was possible to select a target family to study map the current state of processes identifying their lead times and losses waste create a plan of action and then propose feasible improvements in order to reduce them or eliminate them However it notes that there is a reduction of around 82 in time enters the early stages and process end in evidence checking that lean principles show themselves capable of offering good results also for the administrative sectors Key Words Lean Office Value Stream Mapping Process Management Wastes Public Administration Journal of Lean Systems Peralta et al 2017 httpleansystemufscbr 88 1 Introdução Estudos relatam que as empresas que buscam aplicar princípios enxutos em seus processos acabam por preferir seus processos de manufatura a seus processos administrativos Porém com a alta competitividade e qualificação das empresas atuantes no mercado muitas já encaram como uma vantagem possuir um escritório atuando de maneira enxuta O conceito de produção enxuta Lean foi introduzido pela primeira vez na década de 1980 Pruijt 2003 Vale destacar que antes disso ocorreu a crise do petróleo que afetou governos empresas e sociedades no mundo inteiro Em 1974 a economia japonesa havia caído para um nível de crescimento zero e muitas empresas estavam com problemas Porém na Toyota Motor Company embora os lucros tenham diminuído obtiveram ganhos se comparado às outras companhias A diferença entre ela e as outras empresas fez com que as pessoas se questionassem sobre o que estaria acontecendo na Toyota naquele período Ohno 1997 A partir desse momento se inicia a implementação do Sistema Toyota de Produção pelo mundo e o sistema just in time passou a ser adotado por empresas dos mais variados setores tanto no Ocidente quanto no Oriente Graeml Peinado 2007 Porém para que seja possível o entendimento do Sistema Toyota de Produção é necessário compreender o sistema produtivo como um todo que consiste em uma rede de processos e operações Denominase processo o fluxo de materiais ou informações no tempo e no espaço ou seja é a transformação da matériaprima em componente semiacabado e por consequência em produto acabado Já as operações podem ser visualizadas como o trabalho realizado para efetivar essa transformação Shingo 1996 Toda produção executada tanto na fábrica como no escritório deve ser entendida como uma rede funcional de processos e operações e necessitam ser compreendidos para que seja possível alcançar melhorias efetivas na produção Shingo 1996 Segundo Werkema 2011 o Lean Manufacturing é uma iniciativa que busca eliminar desperdícios isto é excluir o que não tem valor para o cliente e imprimir velocidade à empresa O Sistema Toyota de Produção por representar uma forma de produzir cada vez mais com menos foi denominado um sistema Lean Manufacturing Journal of Lean Systems Peralta et al 2017 httpleansystemufscbr 89 O Lean Office é uma evolução adaptativa do Lean Manufacturing diferenciandose em alguns aspectos enquanto no Lean Manufacturing têmse bem visíveis os cenários de trabalho pois se tratam de processos com fluxos físicos no Lean Office os cenários de trabalho são muitas vezes de difícil visualização pois se tratam de processos envolvendo fluxos não físicos Pagnossin Ross 2016 Em outras palavras o Lean Office é um sistema de gestão voltado para processos em que o fluxo de valor não está vinculado a materiais e sim a informações e conhecimentos McManus 2005 Diante do exposto o objetivo desse trabalho é propor um plano de melhorias para uma família de processos administrativos correntes em um órgão da Administração Pública Federal fazendo uso de princípios e conceitos do Lean Office Este trabalho se justifica pela oportunidade de melhoria identificada em um processo administrativo pertencente a um órgão da esfera pública Foi possível por meio de pesquisa no sistema utilizado pelo estabelecimento Sistema Integrado de Administração Financeira SIAFI extrair dados referentes aos Restos a Pagar não processados Restos a Pagar processados e seus respectivos cancelamentos durante os cinco últimos exercícios financeiros e posteriormente realizar análises Porém os dados relativos a Restos a Pagar processados foram descartados pelo fato de seu montante somar valor ínfimo em comparação aos Restos a Pagar não processados Para facilitar o entendimento do artigo o mesmo será dividido em cinco seções A primeira seção apresentou uma breve introdução ao assunto do artigo juntamente com seu objetivo e justificativa O referencial teórico na segunda seção abrange uma explicação sobre Administração pública e federal Produção enxuta Mapeamento do fluxo de valor Lean Office e Mapeamento do fluxo de valor administrativo Na terceira seção apresentase a metodologia do trabalho Os resultados e discussões serão apresentados na quarta seção e por fim na quinta seção são apresentadas as considerações finais referentes ao artigo 2 Referencial teórico 21 Administração Pública e Federal Todo processo de compras em instituições públicas deve se ater à Lei nº 8666 de 21 de junho de 1993 Lei de Licitações e Contratos a qual propicia uma visão geral sobre todas as licitações e contratos que envolvem compras obras e serviços de órgão públicos Journal of Lean Systems Peralta et al 2017 httpleansystemufscbr 90 Uma das funções de todos os órgãos da administração pública é a realização de compras e contratação de serviços necessários para a execução de seus objetivos organizacionais Ao comprar os itens necessários para o particular basta verificar o que está faltando e posteriormente verificar onde os produtos desejados estão disponíveis pelos preços mais baixos A compra mais vantajosa é aquela que obteve a maior redução de custo que adequamse as necessidades do comprador Já as compras para o setor público são mais complexas e exigem maior responsabilidade com o uso dos recursos públicos Após a realização dos procedimentos licitatórios adequados a execução da despesa orçamentária pública conforme a Lei nº 4320 de 17 de março de 1964 que estatui normas gerais de direito financeiro para elaboração e controle dos orçamentos e balanços da União dos Estados dos Municípios e do Distrito Federal dáse em três estágios empenho liquidação e pagamento Brasil 1964 O pagamento se refere ao terceiro e último estágio da despesa pública sendo processados no momento da emissão da Ordem Bancária e de seus respectivos documentos relativos aos tributos e retenções previstas O mesmo somente pode ser emitido após regular liquidação da despesa Entendese como Restos a Pagar processados aqueles que antes do prazo para sua inscrição foram recebidas as mercadorias ou a prestação de serviço já foram realizadas ou seja já tiveram a liquidação da despesa concretizada porém encontrase ainda pendente de pagamento E os Restos a Pagar não processados são aqueles que até o momento de sua inscrição não tiveram a liquidação da despesa realizada 22 Produção Enxuta O termo Produção Enxuta também conhecida como Lean Production foi criado no final da década de 80 em um projeto de pesquisa do Massachusetts Institute of Technology MIT sobre a indústria automobilística mundial A pesquisa revelou que a Toyota havia desenvolvido um novo e superior modelo de gestão nas principais áreas dos negócios como manufatura desenvolvimento de produtos e relacionamento com os clientes e fornecedores Lean Institute Brasil 2015 A Produção Enxuta é uma filosofia e estratégia de negócios para aumentar a satisfação dos clientes através da melhor utilização dos recursos em um menor tempo com qualidade e zelando pela qualidade e motivação de seus colaboradores Para isso ela envolve e integra Journal of Lean Systems Peralta et al 2017 httpleansystemufscbr 91 não só a manufatura mas todas as partes de uma organização com o objetivo de agregar valor aos processos Ghinato 2000 Baseados na demanda real dos clientes a criação de fluxos contínuos e sistemas puxados são desenvolvidos juntamente com análise e melhoria do fluxo de valor das cadeias de valor desde a matériaprima até os produtos acabados Lean Institute Brasil 2015 Segundo Ohno 1997 o Sistema Toyota de Produção é a absoluta eliminação do desperdício e possui como seus pilares de sustentação o Justintime JIT O mesmo autor ainda relata que o JIT é uma abordagem disciplinada que visa aprimorar a produtividade global e eliminar os desperdícios Ele possibilita a produção eficaz em termos de custo assim como o fornecimento apenas da quantidade adequada no momento e locais certos utilizando o mínimo de instalações equipamento materiais e recursos humanos Com o surgimento da Produção Enxuta no ramo automobilístico inicialmente indústrias de ramos diversos e distintos esboçaram uma espécie de rejeição relacionada à aplicação de técnicas originadas pelo Sistema Toyota de Produção em suas áreas Assim Womack e Jones 2004 identificaram cinco princípios fundamentais para que esta aplicação fosse possível conforme apresentados na Tabela 1 Tabela 1 Princípios enxutos VALOR Diferente do que muitos pensam não é a empresa e sim o cliente quem define o que é valor Para ele a necessidade gera o valor e cabe às empresas determinarem qual é essa necessidade procurar satisfazêla e cobrar por isso um preço específico a fim de manter a empresa no negócio e aumentar seus lucros por meio da melhoria contínua dos processos e da redução de custos FLUXO DE VALOR Denominase em analisar a cadeia produtiva e separar os processos em três tipos aqueles que efetivamente geram valor aqueles que não geram valor mas são importantes para a manutenção dos processos e da qualidade e por fim aqueles que não agregam valor devendo ser eliminados imediatamente As empresas devem olhar para todo o processo da criação do produto à pósvenda FLUXO CONTÍNUO Com base na análise do fluxo contínuo que se deve dar fluidez para os processos e atividades Isso exige uma mudança na mentalidade das pessoas devendo deixar de lado a ideia de segregação entre os setores Elaborar um Fluxo Contínuo com as etapas restantes é uma tarefa difícil do processo e também a mais estimulante O efeito imediato da criação de fluxos contínuos pode ser sentido na redução dos tempos de concepção de produtos e de processamento de pedidos e em estoques PRODUÇÃO PUXADA Através da produção puxada a empresa se permite inverter o fluxo produtivo isto é as empresas não mais empurram os produtos para o consumidor por intermédio de descontos e promoções e sim o consumidor passa a puxar o Fluxo de Valor reduzindo a necessidade de estoques e valorizando o produto Journal of Lean Systems Peralta et al 2017 httpleansystemufscbr 92 PERFEIÇÃO A busca incessante pelo aperfeiçoamento contínuo em direção a um estado ideal deve direcionar todos os esforços da empresa em processos transparentes em que todos os membros da cadeia tenham conhecimento profundo do processo como um todo podendo dialogar e buscar continuamente melhores formas de se criar valor Fonte Adaptado de Lean Institute Brasil 2015 Ao pensar sobre eliminação total do desperdício de acordo com Ohno 1997 se deve ter em mente os seguintes pontos aumento da eficiência só faz sentido quando está associado à redução de custos para isso deve ser feito o possível para que se necessite do mínimo de mãodeobra e que seja produzido somente o necessário e cada operador e cada linha deve ter sua eficiência observada onde primeiramente devemse observar os operadores como um grupo e logo a eficiência da fábrica como um todo devendo ser melhorada a cada estágio Desta forma conforme Shingo 1996 o Sistema Toyota de Produção identifica sete tipos de perda Ao mesmo tempo Rother e Shook 2003 afirmam que estes tipos de perdas se estendem também aos ambientes administrativos em muitas vezes admitindo proporções maiores do que em ambientes de manufatura Um ambiente administrativo desorganizado cheio de desperdícios exige um preço muito alto das pessoas envolvidas fazendo com que não consigam se sentir bemsucedidas Sendo assim a Tabela 2 apresenta a definição dos sete desperdícios sendo eles superprodução espera transporte processamento estoque movimento e produtos defeituosos Tabela 2 Definição dos sete desperdícios SUPERPRODUÇÃO O desperdício da superprodução é definido no momento em que se produz antes da hora desejada quando se produz demais alguma coisa ou a mais que o necessário Produzir cedo demais ou a mais que o necessário não melhora a eficiência e ainda consome recursos tais como materiais pessoas e armazenamento disponível Estabelecer uma sequência de fluxo de trabalho para satisfazer o próximo cliente padronização para cada processo e dispositivos de sinalização para evitar adiantamento no processamento são ações possíveis para eliminação deste tipo de desperdício ESPERA A espera significa tempo ocioso isto é seja esperar por papéis pessoas máquinas ou informações significa desperdício Os exemplos são claros dentro dos escritórios esperar por assinaturas telefonemas e máquinas por exemplo sendo o desperdício mais fácil de ser detectado Atitudes como multiqualificar os empregados para que o fluxo de trabalho continue durante a ausência de algum deles bem como equilibrar a carga de trabalho para o dia a fim de que todas as pessoas sejam utilizadas da melhor maneira possível TRANSPORTE Transportar algo para algum lugar além do local o qual deveria ser colocado arquivado empilhado ou movido desperdiça tempo e energia Além de toda esta movimentação desnecessária fatores de perdas estão suscetíveis de acontecer Portanto tornar a distância de transporte a menor possível pode ser encarada como uma atitude que busca acabar com o desperdício de transporte Journal of Lean Systems Peralta et al 2017 httpleansystemufscbr 93 PROCESSAMENTO O desperdício do processamento normalmente se dá em relação ao processamento de atividades redundantes isto é atividades em que o cliente não está interessado Verificar as assinaturas e o trabalho de outra pessoa são espécies de desperdícios de processamento podendo ser eliminados através de revisões das etapas que agregam valor em cada processo e dinamizálas ou eliminálas ESTOQUE O desperdício de estoque pode ser um hábito difícil de ser extinto O estoque representa uma margem de segurança da qual pode ser que não seja cômodo a abandonar Porém o estoque em excesso ocupa espaço e pode impactar na segurança e tornarse obsoleto caso as solicitações de trabalho forem alteradas Temse como exemplo arquivos não necessários suprimentos extras e copias desnecessárias de alguns documentos sendo que além de se ter coisas a mais para lidar as coisas ainda podem tornarse obsoletas antes que você tenha a chance de utilizálas A partir do momento em que se certifica de que o trabalho chega ao processo e não fica parado e produzse somente o necessário para satisfazer o seu cliente seguinte no fluxo os desperdícios de estoque estarão sendo eliminados MOVIMENTO Atividades de trabalho ineficazes normalmente são as responsáveis por movimentos desnecessários como andar abaixar e alcançar Assim qualquer movimento desnecessário para a condução de uma operação é considerado desperdício Para eliminar este tipo de desperdício padronize folhas gavetas e armários por toda a área de atuação e utilize códigos de cores ao máximo PRODUTOS DEFEITUOSOS Também conhecido como desperdício de defeitos ou correção este desperdício é facilmente definido e compreendido Consiste em fazer algo novamente devido aos defeitos erros encontrados em operação realizada A diminuição de produtividade deixar de realizar atividades em seu processamento normal para lidar com defeitos e retrabalho é a principal consequência deste desperdício podendo ser diminuído e até eliminado Fonte Adaptado de Shingo 1996 23 Mapeamento do Fluxo de Valor O mapeamento é apenas uma técnica e portanto o que se torna de suma importância é implementar um fluxo que agregue valor ao fluxo de produção tendo esta atividade facilitada após mapear e focar o fluxo com a visão de estado ideal ou pelo menos melhorado o mesmo Para isso é necessário que seja seguida as seguintes etapas Rother Shook 2003 Definir o gerente do fluxo de valor nesta etapa deve ser definida uma pessoa para que assuma a responsabilidade de identificar todas as formas de desperdícios e compreender o fluxo de valor Selecionar uma família de processos mapear todo o fluxo de um produto é muito complicado sendo necessário que os produtos sejam agrupados por famílias compostas por produtos que passem por processos semelhantes Mapeamento da situação atual Partindo do pressuposto de que a família já foi selecionada desenhase a representação do fluxo de processo e informações da Journal of Lean Systems Peralta et al 2017 httpleansystemufscbr 94 empresa através de um conjunto de ícones para representar os processos e fluxos nos quais se procura enxergar os gargalos e problemas existentes Mapeamento da situação futura Através do Mapa de Estado Atual e adotando regras alinhadas aos princípios enxutos se elimina todos os desperdícios identificados originandose o Mapa de Estado Futuro e Plano de melhorias é elaborado a partir do Mapa de Estado Futuro descrevendo ações e atividades a serem adotadas para que a empresa consiga atingir o estado futuro ideal 24 Lean Office O Lean Office garante que durante seu trabalho os processos possuem apenas as unidades de trabalho necessárias e nas quantidades necessárias isto é consiste em um ambiente o qual as pessoas visam eliminar atividades que não adicionam valor implicando em desperdícios Tapping Shuker 2010 No âmbito administrativo há grande preocupação com as unidades de trabalho juntamente com as de informações Neste contexto a aplicação dos princípios Lean no escritório remete o aprendizado com relação a unidades de trabalho e de informações Na área administrativa conceitos Lean são recomendados por Tapping e Shuker 2010 e apresentam as seguintes fases Fase de demanda do cliente de imediato o cliente deve ser determinado juntamente com sua demanda para que a partir disso o processo esteja em condições de atender a demanda Nesta fase podem ser utilizadas as ferramentas eou conceitos do cálculo do tempo Takt Cálculo do Pitch 5S para o escritório e Métodos de solução de problemas Fase de fluxo contínuo um fluxo contínuo deve ser estabelecido de forma que haja uma garantia de que as corretas unidades de trabalho cheguem aos clientes no momento e nas quantidades certas podendo neste caso ser utilizadas as ferramentas de sistema Kanban FIFO Balanceamento de linha Trabalho padronizado e Layout da área de trabalho e Fase de nivelamento após a determinação da demanda do cliente e estabelecido o fluxo contínuo o trabalho deve ser distribuído homogeneamente de modo que se Journal of Lean Systems Peralta et al 2017 httpleansystemufscbr 95 encontre um nivelamento ao longo do sistema de produção Para isto a caixa de nivelamento de carga é uma ferramenta que pode ser feito uso Atendidas as fases citadas o gerenciamento do fluxo de valor sustenta a mudança para uma empresa Lean O estudo desenvolvido por Gomes Souza Ferreira e Gontijo 2016 teve como objetivo apresentar a solução de Lean Office para um problema no processo de solicitação de passagens de um Programa de Pósgraduação onde com a implementação foram possíveis reduzir o lead time que foi de 25 e o process time em 1483 Pagnossin e Roos 2016 tiveram como problema de pesquisa os atrasos no encaminhamento de informações técnicas a clientes de uma organização prestadora de serviços no caso uma distribuidora de combustíveis Os mesmos autores tiveram como objetivo reduzir e eliminar desperdícios no fluxo de valor de informações e conhecimentos com isso os dados mostraram que o problema prático foi solucionado no caso os clientes não tiveram mais problemas de atrasos na entrega das informações técnicas relacionadas aos combustíveis 25 Mapeamento do Fluxo de Valor Administrativo Tapping e Shuker 2010 proporcionam conteúdos relacionados ao mapeamento do fluxo de valor adaptado aos ambientes de escritório e ambientes administrativos de modo que os tornem escritórios de atuação enxuta Porém algumas dificuldades foram encontradas no momento desta adaptação aos ambientes administrativos devido a algumas características da atividade como os estoques invisíveis e tempos de realização dos processos altamente voláteis na maioria dos casos prevalece somente o processamento de informações e os processos dependem diretamente dos colaboradores De maneira geral o Mapeamento do Fluxo de Valor Administrativo segue a mesma metodologia do Mapeamento do Fluxo de Valor apresentado na subseção 23 deste trabalho porém diverge nos aspectos na etapa de selecionar uma família de processos são tratados dos fluxos de trabalho ao invés de produtos e na etapa de mapeamento da situação atual da empresa são descritas todas as atividades atuais envolvidas no fluxo de trabalho explicitando dados como número de pessoas envolvidas nas atividades e tempo de atividades 3 Procedimentos Metodológicos Para a análise de processos pertencentes à rotina administrativa de um órgão da Administração Pública Federal utilizouse a ferramenta de Mapeamento do Fluxo de Valor Journal of Lean Systems Peralta et al 2017 httpleansystemufscbr 96 Administrativo composto pelas etapas de Seleção dos Processos Desenho do Estado Atual Desenho do Estado Futuro e Plano de Ação 31 Seleção dos Processos A escolha dos processos se deu pela razão de buscar atender orientações emanadas por autoridades competentes pelas quais o órgão exerce papel de subordinação relativas à inscrição de empenhos em situação de Restos a Pagar e seus cancelamentos Desta forma através de acesso e inúmeras consultas ao Sistema Integrado de Administração Financeira SIAFI foi possível a coleta de dados necessários para análise almejada relacionadas aos anos de 2010 à 2014 Primeiramente foi realizado o levantamento de empenhos inscritos em situação de Restos a Pagar não processados para verificação se há relação entre o montante em Reais e o número de empenhos inscritos De posse destes dados foi possível realizar a segregação destes empenhos de acordo com suas respectivas naturezas de despesas isto é classificálos nas seguintes naturezas aquisição de material de consumo material permanente prestação de serviços por terceiros entre outros Por fim estudos similares foram realizados para os empenhos em Restos a Pagar não processados cancelados durante os respectivos anos em estudo 32 Desenho do Estado Atual No desenho de estado atual foram descritas as atividades atuais envolvidas no fluxo de trabalho realizado Neste desenho representaramse as atividades e suas respectivas entradas e saídas além do responsável ou área responsável pela execução da atividade e como esta é realizada 33 Desenho do Estado Futuro Os processos avaliados possuem atividades similares durante o seu transcurso contudo o fator que deve ser observado com atenção é a seleção das métricas apropriadas visando à eliminação de desperdícios no fluxo do processo Neste caso algumas métricas primárias a serem aplicadas são Lead time processing time e tempo de ciclo As métricas primárias utilizadas ao serem estratificadas resultam em métricas mais específicas como no caso do tempo de ciclo que é possível ser desmembrado em tempo gasto em esperas e em caminhadas entre os setores envolvidos Desta forma após a identificação das atividades passíveis de melhorias é possível à construção de um plano de ação Journal of Lean Systems Peralta et al 2017 httpleansystemufscbr 97 34 Plano de Ação Todas as ações propostas no Plano de Ação têm o intuito de eliminar os desperdícios identificados durante a análise de seu mapa melhorando o fluxo de informações e visando diminuir o seu Lead time Anterior à aplicação do Plano de Ação deve ser utilizada uma ferramenta de auxílio na priorização de resolução de dificuldades encontradas chamada Matriz GUT Esta matriz serve para classificar a ordem de atuação perante os problemas levando em consideração fatores como gravidade do problema urgência de sua solução e tendência de piorar 4 Resultados e Discussão 41 Seleção dos Processos Na seleção de processos administrativos foram utilizados o quantitativo de empenhos inscritos e o quantitativo de seus cancelamentos conforme apresentado na Figura 1 Figura 1 Quantitativo de empenhos inscritos em Restos a Pagar e seus respectivos cancelamentos Para que seja possível a verificação da natureza da despesa iniciada de cada empenho ou seja qual a finalidade que a despesa se destina como por exemplo aquisição de materiais de consumo para manutenção da vida vegetativa da organização aquisição de materiais permanentes ou de uso duradouro prestação de serviço por terceiros pagamento de indenizações ou ajuda de custo diárias entre outras foi necessário realizar uma pesquisa detalhada através do uso do Sistema Integrado de Administração Financeira Em seguida de posse do quantitativo de empenhos inscritos em Restos a Pagar coube realizar a segregação dos mesmos de acordo com as naturezas de despesas mais correntes Journal of Lean Systems Peralta et al 2017 httpleansystemufscbr 98 durante os últimos cinco anos e plotar um gráfico ilustrado por meio de Figura 2 no qual são exibidas as proporções de cada natureza de despesa no respectivo ano Figura 2 Demonstrativo de empenhos inscritos em Restos a Pagar por natureza de despesa ao ano Analisando a Figura 2 é possível afirmar que os maiores índices de empenhos inscritos em Restos a Pagar são voltados para a aquisição de materiais de consumo para a administração da organização Portanto o simples fato de inscrever empenhos em Restos a Pagar não se considera algo preocupante quando comparado ao cancelamento dos mesmos pelos motivos deste último ocasionar a perda do recurso provisionado e ainda a Figura 3 apresenta que a quantidade de empenhos inscritos na situação em pesquisa não está diretamente relacionada aos seus índices de cancelamento e sim à natureza da despesa Sendo assim de posse das informações supracitadas se conclui que os empenhos que possuem como finalidade a prestação de serviços por terceiros mesmo sendo inscritos em Restos a Pagar em menor quantidade que os demais empenhos das diversas naturezas de despesas existentes possuem maiores índices de cancelamentos Portanto se tornam de suma importância que sejam realizados estudos em relação a esta situação Desta forma foram selecionados aleatoriamente três processos relacionados à prestação de serviço por terceiros inscritos em Restos a Pagar durante o exercício financeiro Journal of Lean Systems Peralta et al 2017 httpleansystemufscbr 99 de 2014 para que possam ser acompanhadas todas as atividades atuais vinculadas a estes processos Figura 3 Demonstrativo de porcentagens de empenhos inscritos em Restos a Pagar cancelados por natureza de despesa ao ano 42 Desenho do Estado Atual O próximo passo realizado foi à confecção do desenho do estado atual da rotina de trabalho em estudo Para isso foi necessário mapear todas as atividades desde o início do processo que consiste na descentralização do crédito via sistema gerencial do Governo Federal até seu final no caso a inscrição em situação de Restos a Pagar podendo ocasionar em duas situações distintas a entrega do material ou prestação do serviço ou a não realização e consequentemente o cancelamento da despesa Avaliando todas as atividades realizadas no processo administrativo em estudo que se inicia com a provisão da nota de crédito fato que dá início ao processo de aquisição de qualquer bem ou prestação de serviço para a Administração Pública Federal e finaliza com a execução do serviço ou cancelamento da despesa que ocorre pelo fato de fornecedores não mostrarem interesse no serviço gerando desperdícios Após as observações e acompanhamento in loco dos processos estudados verificouse os tempos de cada operação em dias úteis foram identificados os desperdícios ao longo dos processos e também os procedimentos de trabalho adotados pela organização Assim foi possível traçar o Mapa do Estado Atual conforme apresentado no Apêndice A Considerando os caminhos similares que os processos tomaram nas bifurcações encontradas os tempos de processamentos os quais estão explícitos no desenho do mapa do Journal of Lean Systems Peralta et al 2017 httpleansystemufscbr 100 estado atual e seus respectivos lead times foram levantados sendo estes últimos consolidados e apresentados na Tabela 1 Tabela 1 Consolidação de lead time PROCESSOS LEAD TIME dias úteis 1 232 2 298 3 217 Portanto foi possível constatar o tempo que a organização necessitou para que conseguisse executar os respectivos serviços Diante disso é possível determinar que o lead time dos processos em estudo foi bastante elevado mesmo levando em consideração que os envolvidos no processo não ocuparam de forma exclusiva os seus tempos de trabalho direcionados somente para os processos avaliados havendo outros processos transcorrendo ao mesmo tempo No Desenho do Estado Atual foram identificados os desperdícios ao longo do processo sendo enumerados de 1 a 7 conforme apresenta a Tabela 2 Tabela 2 Identificação dos desperdícios DESPERDÍCIO 1 Tipo Desperdício de espera Consolidado a partir do momento em que o crédito é descentralizado para a organização pelo órgão gerencial do Governo Federal porém o Ordenador de Despesas não é informado para que seja distribuído ficando o mesmo disponível em tela causando dias de espera para dar sequência ao processo DESPERDÍCIO 2 Tipo Desperdício de espera Consiste na demora que ocorre quando o Ordenador de Despesas não determina de maneira célere quem serão os responsáveis pela confecção das requisições DESPERDÍCIO 3 Tipo Desperdício de espera Ocasionado por não haver um planejamento de necessidades por parte das respectivas seções ou repartições da organização alinhado com os objetivos do Ordenador de Despesas para a organização sendo que as mesmas iniciam estes levantamentos a partir do momento do recebimento da informação de que foi distribuído recurso DESPERDÍCIO 4 Tipo Desperdício de superprodução Resultante da superprodução de documentos diversos que necessitam da assinatura e aprovação das mesmas pessoas na organização Dificilmente o Ordenador de Despesas Fiscal Administrativo e Encarregado do Setor Financeiro são encontrados em suas respectivas salas para assinatura de imediato das documentações envolvidas no processo ou até mesmo pelo fato dos referidos se ausentarem da organização não havendo um substituto atuante ocasionando em um acúmulo de documentações em suas caixas de entrada DESPERDÍCIOS 5 Tipo Desperdício de transporte e espera O Desperdício de transporte foi identificado quando após confeccionada a nota de empenho algum integrante da SALC deve percorrer em média 1000 mil metros a pé para que seja protocolada e entregue junto ao Almoxarifado para posterior envio ao fornecedor Por conta disto e do trabalho diário da seção muitas vezes as notas de empenhos são acumuladas durante dias ocasionando em desperdício de espera para que seja transportada até ao Almoxarifado Journal of Lean Systems Peralta et al 2017 httpleansystemufscbr 101 DESPERDÍCIO 6 Tipo Desperdício de processamento Pelo fato que a verificação do contato do fornecedor na grande maioria das vezes já foi feito pelos integrantes da SALC por motivos específicos ocasionando em uma operação redundante no processo DESPERDÍCIO 7 Tipo Desperdício de espera Esta espera se dá após a remessa do empenho para o fornecedor no momento em que a Administração Pública aguarda retorno por parte do fornecedor com relação à prestação do serviço demandado 43 Desenho do Estado Futuro De maneira a dar continuidade ao Mapeamento do Fluxo de Valor de um processo administrativo de prestação de serviço em uma organização pública chegase no momento de traçar o Mapa do Desenho Estado Futuro Isto é Após O entendimento da rotina atual do processo é necessário buscar melhorias dos fluxos nos processos do ramo através da eliminação de desperdícios fluxo contínuo nivelamento de trabalho e melhoria dos processos Levando em consideração de que se deseja um lead time menor isto é uma diminuição do tempo desde o início do processo representada pelo momento da descentralização do crédito pelo Governo Federal via sistema gerencial até a apropriação do serviço executado junto à organização foi desenhado o Mapa de Estado Futuro do processo conforme apresentado no Apêndice B 44 Plano de melhorias Identificados os desperdícios definiuse a prioridade de atuação para que os mesmos sejam amenizados ou até mesmo extinguidos Então utilizouse a ferramenta Matriz GUT a qual nos facilita e auxilia no alcance desta meta Behr Moro Estabel 2008 Para isso foram reunidos todos os funcionários envolvidos nos processos e foram determinados os escores de acordo com cada critério gravidade urgência e tendência sendo representados pelos números de 1 a 5 nos quais o número 1 representa pouca ou quase nenhuma interferência com relação aos critérios e o 5 representando consequências mais graves O critério de gravidade é analisado pela intensidade ou impacto que o problema pode causar se não for solucionado A urgência é avaliada pela imposição do tempo existente para que determinada situação seja resolvida e por fim a tendência que é analisada pela tendência de evolução da situação enfrentada A Tabela 3 demonstra detalhadamente quais foram os critérios utilizados para a determinação da prioridade de atuação Journal of Lean Systems Peralta et al 2017 httpleansystemufscbr 102 Tabela 3 Representação Matriz GUT PROBLEMAS GRAVIDADE URGÊNCIA TENDÊNCIA GUT PRIORIDADE Desperdício 1 2 3 2 12 5 Desperdício 2 3 2 2 12 5 Desperdício 3 4 3 3 36 2 Desperdício 4 4 3 2 24 4 Desperdício 5 4 4 2 32 3 Desperdício 6 2 3 2 12 5 Desperdício 7 5 5 3 75 1 Onde Gravidade 1 Sem gravidade 2 Pouco grave 3 Muito grave 4 Muito mais grave e 5 Extremamente grave Urgência 1 Pode esperar 2 Pouco urgente 3 Urgente merece atenção em curto prazo 4 Muito urgente e 5 Necessidade de ação imediata e Tendência 1 Não irá mandar 2 Irá piorar em longo prazo 3 Irá piorar em médio prazo 4 Irá piorar em curto prazo e 5 Irá piorar rapidamente Com a determinação das prioridades através de auxílio da ferramenta Matriz GUT o próximo passo foi a determinação de quais medidas serão necessárias para que haja uma otimização do processo em estudo Sendo assim foi confeccionado o Plano de Ação ilustrado por intermédio da Tabela 4 Journal of Lean Systems Peralta et al 2017 httpleansystemufscbr 103 Tabela 4 Plano de ação proposto para gerenciamento dos desperdícios identificados Desperdício O que será feito Quem fará Quando será feito Como será feito 7 Redução do tempo de aguardo para que seja dado início na prestação do serviço adquirido Chefe do Almoxarifado 01122015 Será criada rotina de trabalho semanal onde todas as empresas que tiveram empenhos realizados a seu favor deverão ser contatadas com intuito de agilizar a prestação do serviço necessitado Chefe da SALC 01122015 Será determinado prazo máximo de 30 trinta dias para entrega de material ou prestação de serviços demandados 3 Redução do tempo de espera para finalização da requisição Encarregado do setor interessado 01012016 Será criado por cada seçãorepartição da organização um planejamento a curto médio e longo prazo incluindo materiais e serviços necessários 5 Redução do tempo de transporte gasto entre as repartições envolvidas no caso SALC e Almoxarifado Ordenador de Despesas 12012016 O escritório do Setor de Almoxarifado será realocado junto ao pavilhão administrativo diminuindo o percurso entre as seções 4 Não haverá pausa no fluxo de documentos por causa de acúmulo e superprodução Ordenador de Despesas Fiscal Administrativo e Encarregado Financeiro 19012016 Serão determinados horários obrigatórios durante o expediente para despacho 1 Reduzirá o tempo de espera até que o Ordenador de Despesas tome conhecimento do crédito recebido Chefe da SALC 01022016 Será criada uma rotina de trabalho na qual o chefe da SALC deverá informar de imediato o Ordenador de Despesas a cada crédito recebido 2 Reduzir o tempo de espera para descentralização aos interessados do crédito recebido pela organização Ordenador de Despesas 01022016 Será criado um Plano Diretor com objetivos estratégicos traçados pelo Ordenador de Despesas 6 Redução de tempo dispendido em processamento desnecessário SALC 01022016 Integrantes da SALC deverão remeter juntamente com a nota de empenho o contato do fornecedor pelo motivo de muitas vezes já terem realizado pesquisa similar para realização de suas operações Após determinação das prioridades de atuação através da Matriz GUT e das medidas a serem tomadas por intermédio da confecção de um Plano de Ação foi possível a otimização do processo avaliado ou seja a redução do lead time Além disso ao decorrer das pesquisas e acompanhamentos realizados durante o período foi possível identificar que todos os Journal of Lean Systems Peralta et al 2017 httpleansystemufscbr 104 processos de aquisição ou prestação de serviço independente de natureza de despesa passam pelas mesmas operações e atividades e portanto as medidas identificadas para que sejam eliminados os desperdícios podem ser aplicadas em todos os processos que envolvem compras no local de estudo resultando em um Mapa de Estado Futuro padrão conforme já apresentado no Apêndice B Desta forma adotadas e obedecidas as recomendações que visam a redução ou até eliminação dos desperdícios encontrados e levando em consideração que a operação mais importante sempre será a próxima a ser realizada durante o processo caracterizando um sistema puxado estimase um lead time máximo de 43 quarenta e três dias úteis para que seja consolidada a compra ou contratação realizada por parte da organização sendo possível que seja realizado em tempo menor que o supracitado considerando fatores como a diminuição de atividades paralelas e a próatividade do fornecedor na entrega do material ou prestação do serviço A Tabela 3 relaciona o lead time ou seja o total de dias dispendidos na execução dos processos estudados em suas condições atuais com a estimativa de dias caso as medidas recomendadas fossem adotadas e suas respectivas reduções em porcentagem Tabela 5 Comparativo lead time obtido e ideal PROCESSOS LEAD TIME Dias úteis LEAD TIME IDEAL Dias úteis REDUÇÃO 1 232 43 8146 2 298 43 8557 3 217 43 8018 Portanto diante do exposto com a redução do lead time em aproximadamente 82 é possível afirmar que os índices de empenhos inscritos em situação de Restos a Pagar consequentemente serão reduzidos ou seja os materiais serão entregues ou os serviços serão prestados durante o exercício financeiro corrente Desta forma os índices de cancelamentos e não aproveitamento dos recursos provisionados à organização também reduzirão 5 Considerações finais Este trabalho permitiu a realização de estudo sobre processo administrativo relacionado ao ramo de compras de órgão da Administração Pública Federal através do uso da ferramenta de Mapeamento do Fluxo de Valor administrativo no qual foi selecionada a Journal of Lean Systems Peralta et al 2017 httpleansystemufscbr 105 família de processos com natureza de despesa envolvendo a prestação de serviços por terceiros O processo de compras em qualquer órgão da Administração Pública é reconhecido na maioria das vezes por um processo lento e bastante burocratizado tendo em vista o fato de envolver o trabalho em conjunto de diferentes seçõesrepartições da organização e também a carência de planejamento por parte de seus gestores No decorrer dos estudos além da identificação das características supracitadas foi possível a identificação de espécies de desperdícios conforme Shingo 1996 que identifica 07 sete tipos de desperdícios os quais se estendem do ambiente de manufatura oriundos do Sistema Toyota de Produção para ambientes administrativos porém neste último são grandes as possibilidades de acarretarem efeitos negativos ao ambiente de trabalho tendo em vista a necessidade de maior comprometimento das pessoas envolvidas fato também identificado por meio informal durante as pesquisas A identificação dos desperdícios só foi possível após representação de todas as atividades envolvidas no fluxo de trabalho do processo considerando suas respectivas entradas saídas e execução em mapeamento e desenho do estado atual Desta forma tornou se possível a racionalização sobre o processo inteiro desde seu início dado pela descentralização do crédito por órgão gerencial até a apropriação da compra via sistema Desta forma foi possível propor melhorias de acordo com os desperdícios identificados visando à redução do lead time do processo de compras do órgão da Administração Pública Federal no qual foi realizado o estudo Através da confecção de plano de ação antecedido pela aplicação de Matriz GUT a qual determinou a priorização da aplicação das medidas e recomendações foi possível traçar a forma dada como ideal para o processo em estudo denominada como Mapa do Estado Futuro REFERÊNCIAS Behr A Moro E L S Estabel L B 2008 Gestão da biblioteca escolar metodologias enfoques e aplicação de ferramentas de gestão e serviços de biblioteca Ciência da Informação 372 3242 Brasil 1993 Lei no 8666 de 21 de junho de 1993 Lei de Licitações e Contrato Disponível em httpswwwplanaltogovbrccivil03LeisL8666conshtm Acessado em 20 Nov 2016 Brasil 1964 Lei nº 4320 de 17 de março de 1964 Estatui Normas Gerais de Direito Financeiro para elaboração e controle dos orçamentos e balanços da União dos Estados dos Municípios e do Distrito Federal Brasília Ghinato P 2000 Produção e Competitividade Aplicações e Inovações Recife Editora da UFPE Journal of Lean Systems Peralta et al 2017 httpleansystemufscbr 106 Gomes D E Souza R M Ferreira T A Gontijo L A 2016 Lean office para um problema no processo de solicitação de passagens de um Programa de PósGraduação Journal of Lean Systems 13 7990 Graeml A R Peinado J 2007 Administração da Produção Curitiba Unicenp Lean Institute Brasil 2005 Aplicações do Lean McManus H L 2005 Product development value stream mapping PDVSM manual Cambridge The Lean Aerospace Initiative Ohno T 1997 O Sistema Toyota de Produção Além da produção em larga escala Porto Alegre Bookman Pagnossin L G Ross C 2016 Abordagem do Lean Office aplicada em um caso prático Journal of Lean Systems 11 95113 Pruijt H 2003 Teams between neoTaylorism and antiTaylorism Economic and Industrial Democracy 241 77101 Rother M Shook J 2003 Aprendendo a enxergar Mapeando o fluxo de valor para agregar valor e eliminar o desperdício São Paulo Lean Institute Brasil Shingo S 1996 O Sistema Toyota de Produção Do ponto de vista da Engenharia de Produção Porto Alegre Bookman Tapping D Shuker T 2010 Lean Office Gerenciamento do fluxo de valor para as áreas administrativas São Paulo Leopardo Werkema C 2011 Lean Seis Sigma Rio de Janeiro Elsevier Womack J P Jones D T 2004 A mentalidade enxuta nas empresas Elimine desperdícios e crie riquezas Rio de Janeiro Elsevier This journal is licenced under a Creative Commons License Creative Commons AtribuiçãoCompartilhaIgual 40 Internacional
Envie sua pergunta para a IA e receba a resposta na hora
Recomendado para você
17
Disponibilidade de Equipamentos na Manutenção Industrial
Gestão de Produção
UNIJUI
1
Planejamento Operacional e Processos de Distribuição
Gestão de Produção
UNIJUI
12
Cronoanálise: Métodos e Tempo Padrão na Produção
Gestão de Produção
UNIJUI
19
Estudo de Tempo e Métodos: Análise e Melhorias de Processos
Gestão de Produção
UNIJUI
20
Estudo de Tempos e Métodos na Organização da Produção
Gestão de Produção
UNIJUI
32
Mapeamento do Fluxo de Valor do Projeto Executivo de Arquitetura em um Órgão Público
Gestão de Produção
UNIJUI
Texto de pré-visualização
JOURNAL OF LEAN SYSTEMS 2016 Vol 2 Nº 3 pp 87106 httpleansystemufscbr 87 Lean office mapeamento do fluxo de valor administrativo em rotina de trabalho de órgão público Lean office administrative value stream mapping in a routine of work in a public organ Carla Beatriz da Luz Peralta carlablpgmailcom Fernando Henrique Lermen fernandolermenhotmailcom Eduardo de Leon Martins dududeleonhotmailcom Vander Luiz da Silva vanderluizhotmailcom Márcia Elisa Soares Echeveste echevestemargmailcom Universidade Federal do Rio Grande do Sul UFRGS Porto Alegre Rio Grande do Sul Article History Submitted 2016 11 17 Revised 2016 12 14 Accepted 2016 12 15 Resumo No decorrer dos anos a manufatura Lean se encontrou em crescente desenvolvimento e vem conquistando cada vez mais espaços em seus universos de atuação contudo as organizações que decidem aplicar a filosofia Lean em seus processos focam apenas em processos de manufatura em detrimento das áreas administrativas Com base nisso o presente estudo visou propor melhorias para uma família de processos administrativos correntes em um Órgão Publico Federal aplicando princípios e conceitos do Lean Office Este trabalho foi desenvolvido por meio de análise dos registros históricos em sistema de informação e Mapeamento do Fluxo de Valor Foi possível selecionar uma famíliaalvo para o estudo mapear o estado atual dos processos identificando seus lead times e perdasdesperdícios criar um plano de ação e posteriormente propor melhorias exequíveis com o objetivo de reduzilas ou eliminálas Contudo notase que há uma redução de em torno 82 no tempo entre as etapas iniciais e finais do processo em evidência conferindo que os princípios enxutos demonstramse capazes de ofertar bons resultados também para os setores administrativos Palavras Chaves Lean Office Mapeamento do Fluxo de Valor Gestão de Processos Desperdícios Administração Pública Abstract Over the years Lean manufacturing was found in increasing development and has been gaining more space in their respective universes however organizations that decide to apply the philosophy Lean in its processes focus only on manufacturing processes at the expense of areas administrative Based on this the present study aimed to propose improvements to a family of current administrative processes in a Federal Public Agency applying principles and concepts of Lean Office This work was developed through analysis of historical records information system and Value Stream Mapping it was possible to select a target family to study map the current state of processes identifying their lead times and losses waste create a plan of action and then propose feasible improvements in order to reduce them or eliminate them However it notes that there is a reduction of around 82 in time enters the early stages and process end in evidence checking that lean principles show themselves capable of offering good results also for the administrative sectors Key Words Lean Office Value Stream Mapping Process Management Wastes Public Administration Journal of Lean Systems Peralta et al 2017 httpleansystemufscbr 88 1 Introdução Estudos relatam que as empresas que buscam aplicar princípios enxutos em seus processos acabam por preferir seus processos de manufatura a seus processos administrativos Porém com a alta competitividade e qualificação das empresas atuantes no mercado muitas já encaram como uma vantagem possuir um escritório atuando de maneira enxuta O conceito de produção enxuta Lean foi introduzido pela primeira vez na década de 1980 Pruijt 2003 Vale destacar que antes disso ocorreu a crise do petróleo que afetou governos empresas e sociedades no mundo inteiro Em 1974 a economia japonesa havia caído para um nível de crescimento zero e muitas empresas estavam com problemas Porém na Toyota Motor Company embora os lucros tenham diminuído obtiveram ganhos se comparado às outras companhias A diferença entre ela e as outras empresas fez com que as pessoas se questionassem sobre o que estaria acontecendo na Toyota naquele período Ohno 1997 A partir desse momento se inicia a implementação do Sistema Toyota de Produção pelo mundo e o sistema just in time passou a ser adotado por empresas dos mais variados setores tanto no Ocidente quanto no Oriente Graeml Peinado 2007 Porém para que seja possível o entendimento do Sistema Toyota de Produção é necessário compreender o sistema produtivo como um todo que consiste em uma rede de processos e operações Denominase processo o fluxo de materiais ou informações no tempo e no espaço ou seja é a transformação da matériaprima em componente semiacabado e por consequência em produto acabado Já as operações podem ser visualizadas como o trabalho realizado para efetivar essa transformação Shingo 1996 Toda produção executada tanto na fábrica como no escritório deve ser entendida como uma rede funcional de processos e operações e necessitam ser compreendidos para que seja possível alcançar melhorias efetivas na produção Shingo 1996 Segundo Werkema 2011 o Lean Manufacturing é uma iniciativa que busca eliminar desperdícios isto é excluir o que não tem valor para o cliente e imprimir velocidade à empresa O Sistema Toyota de Produção por representar uma forma de produzir cada vez mais com menos foi denominado um sistema Lean Manufacturing Journal of Lean Systems Peralta et al 2017 httpleansystemufscbr 89 O Lean Office é uma evolução adaptativa do Lean Manufacturing diferenciandose em alguns aspectos enquanto no Lean Manufacturing têmse bem visíveis os cenários de trabalho pois se tratam de processos com fluxos físicos no Lean Office os cenários de trabalho são muitas vezes de difícil visualização pois se tratam de processos envolvendo fluxos não físicos Pagnossin Ross 2016 Em outras palavras o Lean Office é um sistema de gestão voltado para processos em que o fluxo de valor não está vinculado a materiais e sim a informações e conhecimentos McManus 2005 Diante do exposto o objetivo desse trabalho é propor um plano de melhorias para uma família de processos administrativos correntes em um órgão da Administração Pública Federal fazendo uso de princípios e conceitos do Lean Office Este trabalho se justifica pela oportunidade de melhoria identificada em um processo administrativo pertencente a um órgão da esfera pública Foi possível por meio de pesquisa no sistema utilizado pelo estabelecimento Sistema Integrado de Administração Financeira SIAFI extrair dados referentes aos Restos a Pagar não processados Restos a Pagar processados e seus respectivos cancelamentos durante os cinco últimos exercícios financeiros e posteriormente realizar análises Porém os dados relativos a Restos a Pagar processados foram descartados pelo fato de seu montante somar valor ínfimo em comparação aos Restos a Pagar não processados Para facilitar o entendimento do artigo o mesmo será dividido em cinco seções A primeira seção apresentou uma breve introdução ao assunto do artigo juntamente com seu objetivo e justificativa O referencial teórico na segunda seção abrange uma explicação sobre Administração pública e federal Produção enxuta Mapeamento do fluxo de valor Lean Office e Mapeamento do fluxo de valor administrativo Na terceira seção apresentase a metodologia do trabalho Os resultados e discussões serão apresentados na quarta seção e por fim na quinta seção são apresentadas as considerações finais referentes ao artigo 2 Referencial teórico 21 Administração Pública e Federal Todo processo de compras em instituições públicas deve se ater à Lei nº 8666 de 21 de junho de 1993 Lei de Licitações e Contratos a qual propicia uma visão geral sobre todas as licitações e contratos que envolvem compras obras e serviços de órgão públicos Journal of Lean Systems Peralta et al 2017 httpleansystemufscbr 90 Uma das funções de todos os órgãos da administração pública é a realização de compras e contratação de serviços necessários para a execução de seus objetivos organizacionais Ao comprar os itens necessários para o particular basta verificar o que está faltando e posteriormente verificar onde os produtos desejados estão disponíveis pelos preços mais baixos A compra mais vantajosa é aquela que obteve a maior redução de custo que adequamse as necessidades do comprador Já as compras para o setor público são mais complexas e exigem maior responsabilidade com o uso dos recursos públicos Após a realização dos procedimentos licitatórios adequados a execução da despesa orçamentária pública conforme a Lei nº 4320 de 17 de março de 1964 que estatui normas gerais de direito financeiro para elaboração e controle dos orçamentos e balanços da União dos Estados dos Municípios e do Distrito Federal dáse em três estágios empenho liquidação e pagamento Brasil 1964 O pagamento se refere ao terceiro e último estágio da despesa pública sendo processados no momento da emissão da Ordem Bancária e de seus respectivos documentos relativos aos tributos e retenções previstas O mesmo somente pode ser emitido após regular liquidação da despesa Entendese como Restos a Pagar processados aqueles que antes do prazo para sua inscrição foram recebidas as mercadorias ou a prestação de serviço já foram realizadas ou seja já tiveram a liquidação da despesa concretizada porém encontrase ainda pendente de pagamento E os Restos a Pagar não processados são aqueles que até o momento de sua inscrição não tiveram a liquidação da despesa realizada 22 Produção Enxuta O termo Produção Enxuta também conhecida como Lean Production foi criado no final da década de 80 em um projeto de pesquisa do Massachusetts Institute of Technology MIT sobre a indústria automobilística mundial A pesquisa revelou que a Toyota havia desenvolvido um novo e superior modelo de gestão nas principais áreas dos negócios como manufatura desenvolvimento de produtos e relacionamento com os clientes e fornecedores Lean Institute Brasil 2015 A Produção Enxuta é uma filosofia e estratégia de negócios para aumentar a satisfação dos clientes através da melhor utilização dos recursos em um menor tempo com qualidade e zelando pela qualidade e motivação de seus colaboradores Para isso ela envolve e integra Journal of Lean Systems Peralta et al 2017 httpleansystemufscbr 91 não só a manufatura mas todas as partes de uma organização com o objetivo de agregar valor aos processos Ghinato 2000 Baseados na demanda real dos clientes a criação de fluxos contínuos e sistemas puxados são desenvolvidos juntamente com análise e melhoria do fluxo de valor das cadeias de valor desde a matériaprima até os produtos acabados Lean Institute Brasil 2015 Segundo Ohno 1997 o Sistema Toyota de Produção é a absoluta eliminação do desperdício e possui como seus pilares de sustentação o Justintime JIT O mesmo autor ainda relata que o JIT é uma abordagem disciplinada que visa aprimorar a produtividade global e eliminar os desperdícios Ele possibilita a produção eficaz em termos de custo assim como o fornecimento apenas da quantidade adequada no momento e locais certos utilizando o mínimo de instalações equipamento materiais e recursos humanos Com o surgimento da Produção Enxuta no ramo automobilístico inicialmente indústrias de ramos diversos e distintos esboçaram uma espécie de rejeição relacionada à aplicação de técnicas originadas pelo Sistema Toyota de Produção em suas áreas Assim Womack e Jones 2004 identificaram cinco princípios fundamentais para que esta aplicação fosse possível conforme apresentados na Tabela 1 Tabela 1 Princípios enxutos VALOR Diferente do que muitos pensam não é a empresa e sim o cliente quem define o que é valor Para ele a necessidade gera o valor e cabe às empresas determinarem qual é essa necessidade procurar satisfazêla e cobrar por isso um preço específico a fim de manter a empresa no negócio e aumentar seus lucros por meio da melhoria contínua dos processos e da redução de custos FLUXO DE VALOR Denominase em analisar a cadeia produtiva e separar os processos em três tipos aqueles que efetivamente geram valor aqueles que não geram valor mas são importantes para a manutenção dos processos e da qualidade e por fim aqueles que não agregam valor devendo ser eliminados imediatamente As empresas devem olhar para todo o processo da criação do produto à pósvenda FLUXO CONTÍNUO Com base na análise do fluxo contínuo que se deve dar fluidez para os processos e atividades Isso exige uma mudança na mentalidade das pessoas devendo deixar de lado a ideia de segregação entre os setores Elaborar um Fluxo Contínuo com as etapas restantes é uma tarefa difícil do processo e também a mais estimulante O efeito imediato da criação de fluxos contínuos pode ser sentido na redução dos tempos de concepção de produtos e de processamento de pedidos e em estoques PRODUÇÃO PUXADA Através da produção puxada a empresa se permite inverter o fluxo produtivo isto é as empresas não mais empurram os produtos para o consumidor por intermédio de descontos e promoções e sim o consumidor passa a puxar o Fluxo de Valor reduzindo a necessidade de estoques e valorizando o produto Journal of Lean Systems Peralta et al 2017 httpleansystemufscbr 92 PERFEIÇÃO A busca incessante pelo aperfeiçoamento contínuo em direção a um estado ideal deve direcionar todos os esforços da empresa em processos transparentes em que todos os membros da cadeia tenham conhecimento profundo do processo como um todo podendo dialogar e buscar continuamente melhores formas de se criar valor Fonte Adaptado de Lean Institute Brasil 2015 Ao pensar sobre eliminação total do desperdício de acordo com Ohno 1997 se deve ter em mente os seguintes pontos aumento da eficiência só faz sentido quando está associado à redução de custos para isso deve ser feito o possível para que se necessite do mínimo de mãodeobra e que seja produzido somente o necessário e cada operador e cada linha deve ter sua eficiência observada onde primeiramente devemse observar os operadores como um grupo e logo a eficiência da fábrica como um todo devendo ser melhorada a cada estágio Desta forma conforme Shingo 1996 o Sistema Toyota de Produção identifica sete tipos de perda Ao mesmo tempo Rother e Shook 2003 afirmam que estes tipos de perdas se estendem também aos ambientes administrativos em muitas vezes admitindo proporções maiores do que em ambientes de manufatura Um ambiente administrativo desorganizado cheio de desperdícios exige um preço muito alto das pessoas envolvidas fazendo com que não consigam se sentir bemsucedidas Sendo assim a Tabela 2 apresenta a definição dos sete desperdícios sendo eles superprodução espera transporte processamento estoque movimento e produtos defeituosos Tabela 2 Definição dos sete desperdícios SUPERPRODUÇÃO O desperdício da superprodução é definido no momento em que se produz antes da hora desejada quando se produz demais alguma coisa ou a mais que o necessário Produzir cedo demais ou a mais que o necessário não melhora a eficiência e ainda consome recursos tais como materiais pessoas e armazenamento disponível Estabelecer uma sequência de fluxo de trabalho para satisfazer o próximo cliente padronização para cada processo e dispositivos de sinalização para evitar adiantamento no processamento são ações possíveis para eliminação deste tipo de desperdício ESPERA A espera significa tempo ocioso isto é seja esperar por papéis pessoas máquinas ou informações significa desperdício Os exemplos são claros dentro dos escritórios esperar por assinaturas telefonemas e máquinas por exemplo sendo o desperdício mais fácil de ser detectado Atitudes como multiqualificar os empregados para que o fluxo de trabalho continue durante a ausência de algum deles bem como equilibrar a carga de trabalho para o dia a fim de que todas as pessoas sejam utilizadas da melhor maneira possível TRANSPORTE Transportar algo para algum lugar além do local o qual deveria ser colocado arquivado empilhado ou movido desperdiça tempo e energia Além de toda esta movimentação desnecessária fatores de perdas estão suscetíveis de acontecer Portanto tornar a distância de transporte a menor possível pode ser encarada como uma atitude que busca acabar com o desperdício de transporte Journal of Lean Systems Peralta et al 2017 httpleansystemufscbr 93 PROCESSAMENTO O desperdício do processamento normalmente se dá em relação ao processamento de atividades redundantes isto é atividades em que o cliente não está interessado Verificar as assinaturas e o trabalho de outra pessoa são espécies de desperdícios de processamento podendo ser eliminados através de revisões das etapas que agregam valor em cada processo e dinamizálas ou eliminálas ESTOQUE O desperdício de estoque pode ser um hábito difícil de ser extinto O estoque representa uma margem de segurança da qual pode ser que não seja cômodo a abandonar Porém o estoque em excesso ocupa espaço e pode impactar na segurança e tornarse obsoleto caso as solicitações de trabalho forem alteradas Temse como exemplo arquivos não necessários suprimentos extras e copias desnecessárias de alguns documentos sendo que além de se ter coisas a mais para lidar as coisas ainda podem tornarse obsoletas antes que você tenha a chance de utilizálas A partir do momento em que se certifica de que o trabalho chega ao processo e não fica parado e produzse somente o necessário para satisfazer o seu cliente seguinte no fluxo os desperdícios de estoque estarão sendo eliminados MOVIMENTO Atividades de trabalho ineficazes normalmente são as responsáveis por movimentos desnecessários como andar abaixar e alcançar Assim qualquer movimento desnecessário para a condução de uma operação é considerado desperdício Para eliminar este tipo de desperdício padronize folhas gavetas e armários por toda a área de atuação e utilize códigos de cores ao máximo PRODUTOS DEFEITUOSOS Também conhecido como desperdício de defeitos ou correção este desperdício é facilmente definido e compreendido Consiste em fazer algo novamente devido aos defeitos erros encontrados em operação realizada A diminuição de produtividade deixar de realizar atividades em seu processamento normal para lidar com defeitos e retrabalho é a principal consequência deste desperdício podendo ser diminuído e até eliminado Fonte Adaptado de Shingo 1996 23 Mapeamento do Fluxo de Valor O mapeamento é apenas uma técnica e portanto o que se torna de suma importância é implementar um fluxo que agregue valor ao fluxo de produção tendo esta atividade facilitada após mapear e focar o fluxo com a visão de estado ideal ou pelo menos melhorado o mesmo Para isso é necessário que seja seguida as seguintes etapas Rother Shook 2003 Definir o gerente do fluxo de valor nesta etapa deve ser definida uma pessoa para que assuma a responsabilidade de identificar todas as formas de desperdícios e compreender o fluxo de valor Selecionar uma família de processos mapear todo o fluxo de um produto é muito complicado sendo necessário que os produtos sejam agrupados por famílias compostas por produtos que passem por processos semelhantes Mapeamento da situação atual Partindo do pressuposto de que a família já foi selecionada desenhase a representação do fluxo de processo e informações da Journal of Lean Systems Peralta et al 2017 httpleansystemufscbr 94 empresa através de um conjunto de ícones para representar os processos e fluxos nos quais se procura enxergar os gargalos e problemas existentes Mapeamento da situação futura Através do Mapa de Estado Atual e adotando regras alinhadas aos princípios enxutos se elimina todos os desperdícios identificados originandose o Mapa de Estado Futuro e Plano de melhorias é elaborado a partir do Mapa de Estado Futuro descrevendo ações e atividades a serem adotadas para que a empresa consiga atingir o estado futuro ideal 24 Lean Office O Lean Office garante que durante seu trabalho os processos possuem apenas as unidades de trabalho necessárias e nas quantidades necessárias isto é consiste em um ambiente o qual as pessoas visam eliminar atividades que não adicionam valor implicando em desperdícios Tapping Shuker 2010 No âmbito administrativo há grande preocupação com as unidades de trabalho juntamente com as de informações Neste contexto a aplicação dos princípios Lean no escritório remete o aprendizado com relação a unidades de trabalho e de informações Na área administrativa conceitos Lean são recomendados por Tapping e Shuker 2010 e apresentam as seguintes fases Fase de demanda do cliente de imediato o cliente deve ser determinado juntamente com sua demanda para que a partir disso o processo esteja em condições de atender a demanda Nesta fase podem ser utilizadas as ferramentas eou conceitos do cálculo do tempo Takt Cálculo do Pitch 5S para o escritório e Métodos de solução de problemas Fase de fluxo contínuo um fluxo contínuo deve ser estabelecido de forma que haja uma garantia de que as corretas unidades de trabalho cheguem aos clientes no momento e nas quantidades certas podendo neste caso ser utilizadas as ferramentas de sistema Kanban FIFO Balanceamento de linha Trabalho padronizado e Layout da área de trabalho e Fase de nivelamento após a determinação da demanda do cliente e estabelecido o fluxo contínuo o trabalho deve ser distribuído homogeneamente de modo que se Journal of Lean Systems Peralta et al 2017 httpleansystemufscbr 95 encontre um nivelamento ao longo do sistema de produção Para isto a caixa de nivelamento de carga é uma ferramenta que pode ser feito uso Atendidas as fases citadas o gerenciamento do fluxo de valor sustenta a mudança para uma empresa Lean O estudo desenvolvido por Gomes Souza Ferreira e Gontijo 2016 teve como objetivo apresentar a solução de Lean Office para um problema no processo de solicitação de passagens de um Programa de Pósgraduação onde com a implementação foram possíveis reduzir o lead time que foi de 25 e o process time em 1483 Pagnossin e Roos 2016 tiveram como problema de pesquisa os atrasos no encaminhamento de informações técnicas a clientes de uma organização prestadora de serviços no caso uma distribuidora de combustíveis Os mesmos autores tiveram como objetivo reduzir e eliminar desperdícios no fluxo de valor de informações e conhecimentos com isso os dados mostraram que o problema prático foi solucionado no caso os clientes não tiveram mais problemas de atrasos na entrega das informações técnicas relacionadas aos combustíveis 25 Mapeamento do Fluxo de Valor Administrativo Tapping e Shuker 2010 proporcionam conteúdos relacionados ao mapeamento do fluxo de valor adaptado aos ambientes de escritório e ambientes administrativos de modo que os tornem escritórios de atuação enxuta Porém algumas dificuldades foram encontradas no momento desta adaptação aos ambientes administrativos devido a algumas características da atividade como os estoques invisíveis e tempos de realização dos processos altamente voláteis na maioria dos casos prevalece somente o processamento de informações e os processos dependem diretamente dos colaboradores De maneira geral o Mapeamento do Fluxo de Valor Administrativo segue a mesma metodologia do Mapeamento do Fluxo de Valor apresentado na subseção 23 deste trabalho porém diverge nos aspectos na etapa de selecionar uma família de processos são tratados dos fluxos de trabalho ao invés de produtos e na etapa de mapeamento da situação atual da empresa são descritas todas as atividades atuais envolvidas no fluxo de trabalho explicitando dados como número de pessoas envolvidas nas atividades e tempo de atividades 3 Procedimentos Metodológicos Para a análise de processos pertencentes à rotina administrativa de um órgão da Administração Pública Federal utilizouse a ferramenta de Mapeamento do Fluxo de Valor Journal of Lean Systems Peralta et al 2017 httpleansystemufscbr 96 Administrativo composto pelas etapas de Seleção dos Processos Desenho do Estado Atual Desenho do Estado Futuro e Plano de Ação 31 Seleção dos Processos A escolha dos processos se deu pela razão de buscar atender orientações emanadas por autoridades competentes pelas quais o órgão exerce papel de subordinação relativas à inscrição de empenhos em situação de Restos a Pagar e seus cancelamentos Desta forma através de acesso e inúmeras consultas ao Sistema Integrado de Administração Financeira SIAFI foi possível a coleta de dados necessários para análise almejada relacionadas aos anos de 2010 à 2014 Primeiramente foi realizado o levantamento de empenhos inscritos em situação de Restos a Pagar não processados para verificação se há relação entre o montante em Reais e o número de empenhos inscritos De posse destes dados foi possível realizar a segregação destes empenhos de acordo com suas respectivas naturezas de despesas isto é classificálos nas seguintes naturezas aquisição de material de consumo material permanente prestação de serviços por terceiros entre outros Por fim estudos similares foram realizados para os empenhos em Restos a Pagar não processados cancelados durante os respectivos anos em estudo 32 Desenho do Estado Atual No desenho de estado atual foram descritas as atividades atuais envolvidas no fluxo de trabalho realizado Neste desenho representaramse as atividades e suas respectivas entradas e saídas além do responsável ou área responsável pela execução da atividade e como esta é realizada 33 Desenho do Estado Futuro Os processos avaliados possuem atividades similares durante o seu transcurso contudo o fator que deve ser observado com atenção é a seleção das métricas apropriadas visando à eliminação de desperdícios no fluxo do processo Neste caso algumas métricas primárias a serem aplicadas são Lead time processing time e tempo de ciclo As métricas primárias utilizadas ao serem estratificadas resultam em métricas mais específicas como no caso do tempo de ciclo que é possível ser desmembrado em tempo gasto em esperas e em caminhadas entre os setores envolvidos Desta forma após a identificação das atividades passíveis de melhorias é possível à construção de um plano de ação Journal of Lean Systems Peralta et al 2017 httpleansystemufscbr 97 34 Plano de Ação Todas as ações propostas no Plano de Ação têm o intuito de eliminar os desperdícios identificados durante a análise de seu mapa melhorando o fluxo de informações e visando diminuir o seu Lead time Anterior à aplicação do Plano de Ação deve ser utilizada uma ferramenta de auxílio na priorização de resolução de dificuldades encontradas chamada Matriz GUT Esta matriz serve para classificar a ordem de atuação perante os problemas levando em consideração fatores como gravidade do problema urgência de sua solução e tendência de piorar 4 Resultados e Discussão 41 Seleção dos Processos Na seleção de processos administrativos foram utilizados o quantitativo de empenhos inscritos e o quantitativo de seus cancelamentos conforme apresentado na Figura 1 Figura 1 Quantitativo de empenhos inscritos em Restos a Pagar e seus respectivos cancelamentos Para que seja possível a verificação da natureza da despesa iniciada de cada empenho ou seja qual a finalidade que a despesa se destina como por exemplo aquisição de materiais de consumo para manutenção da vida vegetativa da organização aquisição de materiais permanentes ou de uso duradouro prestação de serviço por terceiros pagamento de indenizações ou ajuda de custo diárias entre outras foi necessário realizar uma pesquisa detalhada através do uso do Sistema Integrado de Administração Financeira Em seguida de posse do quantitativo de empenhos inscritos em Restos a Pagar coube realizar a segregação dos mesmos de acordo com as naturezas de despesas mais correntes Journal of Lean Systems Peralta et al 2017 httpleansystemufscbr 98 durante os últimos cinco anos e plotar um gráfico ilustrado por meio de Figura 2 no qual são exibidas as proporções de cada natureza de despesa no respectivo ano Figura 2 Demonstrativo de empenhos inscritos em Restos a Pagar por natureza de despesa ao ano Analisando a Figura 2 é possível afirmar que os maiores índices de empenhos inscritos em Restos a Pagar são voltados para a aquisição de materiais de consumo para a administração da organização Portanto o simples fato de inscrever empenhos em Restos a Pagar não se considera algo preocupante quando comparado ao cancelamento dos mesmos pelos motivos deste último ocasionar a perda do recurso provisionado e ainda a Figura 3 apresenta que a quantidade de empenhos inscritos na situação em pesquisa não está diretamente relacionada aos seus índices de cancelamento e sim à natureza da despesa Sendo assim de posse das informações supracitadas se conclui que os empenhos que possuem como finalidade a prestação de serviços por terceiros mesmo sendo inscritos em Restos a Pagar em menor quantidade que os demais empenhos das diversas naturezas de despesas existentes possuem maiores índices de cancelamentos Portanto se tornam de suma importância que sejam realizados estudos em relação a esta situação Desta forma foram selecionados aleatoriamente três processos relacionados à prestação de serviço por terceiros inscritos em Restos a Pagar durante o exercício financeiro Journal of Lean Systems Peralta et al 2017 httpleansystemufscbr 99 de 2014 para que possam ser acompanhadas todas as atividades atuais vinculadas a estes processos Figura 3 Demonstrativo de porcentagens de empenhos inscritos em Restos a Pagar cancelados por natureza de despesa ao ano 42 Desenho do Estado Atual O próximo passo realizado foi à confecção do desenho do estado atual da rotina de trabalho em estudo Para isso foi necessário mapear todas as atividades desde o início do processo que consiste na descentralização do crédito via sistema gerencial do Governo Federal até seu final no caso a inscrição em situação de Restos a Pagar podendo ocasionar em duas situações distintas a entrega do material ou prestação do serviço ou a não realização e consequentemente o cancelamento da despesa Avaliando todas as atividades realizadas no processo administrativo em estudo que se inicia com a provisão da nota de crédito fato que dá início ao processo de aquisição de qualquer bem ou prestação de serviço para a Administração Pública Federal e finaliza com a execução do serviço ou cancelamento da despesa que ocorre pelo fato de fornecedores não mostrarem interesse no serviço gerando desperdícios Após as observações e acompanhamento in loco dos processos estudados verificouse os tempos de cada operação em dias úteis foram identificados os desperdícios ao longo dos processos e também os procedimentos de trabalho adotados pela organização Assim foi possível traçar o Mapa do Estado Atual conforme apresentado no Apêndice A Considerando os caminhos similares que os processos tomaram nas bifurcações encontradas os tempos de processamentos os quais estão explícitos no desenho do mapa do Journal of Lean Systems Peralta et al 2017 httpleansystemufscbr 100 estado atual e seus respectivos lead times foram levantados sendo estes últimos consolidados e apresentados na Tabela 1 Tabela 1 Consolidação de lead time PROCESSOS LEAD TIME dias úteis 1 232 2 298 3 217 Portanto foi possível constatar o tempo que a organização necessitou para que conseguisse executar os respectivos serviços Diante disso é possível determinar que o lead time dos processos em estudo foi bastante elevado mesmo levando em consideração que os envolvidos no processo não ocuparam de forma exclusiva os seus tempos de trabalho direcionados somente para os processos avaliados havendo outros processos transcorrendo ao mesmo tempo No Desenho do Estado Atual foram identificados os desperdícios ao longo do processo sendo enumerados de 1 a 7 conforme apresenta a Tabela 2 Tabela 2 Identificação dos desperdícios DESPERDÍCIO 1 Tipo Desperdício de espera Consolidado a partir do momento em que o crédito é descentralizado para a organização pelo órgão gerencial do Governo Federal porém o Ordenador de Despesas não é informado para que seja distribuído ficando o mesmo disponível em tela causando dias de espera para dar sequência ao processo DESPERDÍCIO 2 Tipo Desperdício de espera Consiste na demora que ocorre quando o Ordenador de Despesas não determina de maneira célere quem serão os responsáveis pela confecção das requisições DESPERDÍCIO 3 Tipo Desperdício de espera Ocasionado por não haver um planejamento de necessidades por parte das respectivas seções ou repartições da organização alinhado com os objetivos do Ordenador de Despesas para a organização sendo que as mesmas iniciam estes levantamentos a partir do momento do recebimento da informação de que foi distribuído recurso DESPERDÍCIO 4 Tipo Desperdício de superprodução Resultante da superprodução de documentos diversos que necessitam da assinatura e aprovação das mesmas pessoas na organização Dificilmente o Ordenador de Despesas Fiscal Administrativo e Encarregado do Setor Financeiro são encontrados em suas respectivas salas para assinatura de imediato das documentações envolvidas no processo ou até mesmo pelo fato dos referidos se ausentarem da organização não havendo um substituto atuante ocasionando em um acúmulo de documentações em suas caixas de entrada DESPERDÍCIOS 5 Tipo Desperdício de transporte e espera O Desperdício de transporte foi identificado quando após confeccionada a nota de empenho algum integrante da SALC deve percorrer em média 1000 mil metros a pé para que seja protocolada e entregue junto ao Almoxarifado para posterior envio ao fornecedor Por conta disto e do trabalho diário da seção muitas vezes as notas de empenhos são acumuladas durante dias ocasionando em desperdício de espera para que seja transportada até ao Almoxarifado Journal of Lean Systems Peralta et al 2017 httpleansystemufscbr 101 DESPERDÍCIO 6 Tipo Desperdício de processamento Pelo fato que a verificação do contato do fornecedor na grande maioria das vezes já foi feito pelos integrantes da SALC por motivos específicos ocasionando em uma operação redundante no processo DESPERDÍCIO 7 Tipo Desperdício de espera Esta espera se dá após a remessa do empenho para o fornecedor no momento em que a Administração Pública aguarda retorno por parte do fornecedor com relação à prestação do serviço demandado 43 Desenho do Estado Futuro De maneira a dar continuidade ao Mapeamento do Fluxo de Valor de um processo administrativo de prestação de serviço em uma organização pública chegase no momento de traçar o Mapa do Desenho Estado Futuro Isto é Após O entendimento da rotina atual do processo é necessário buscar melhorias dos fluxos nos processos do ramo através da eliminação de desperdícios fluxo contínuo nivelamento de trabalho e melhoria dos processos Levando em consideração de que se deseja um lead time menor isto é uma diminuição do tempo desde o início do processo representada pelo momento da descentralização do crédito pelo Governo Federal via sistema gerencial até a apropriação do serviço executado junto à organização foi desenhado o Mapa de Estado Futuro do processo conforme apresentado no Apêndice B 44 Plano de melhorias Identificados os desperdícios definiuse a prioridade de atuação para que os mesmos sejam amenizados ou até mesmo extinguidos Então utilizouse a ferramenta Matriz GUT a qual nos facilita e auxilia no alcance desta meta Behr Moro Estabel 2008 Para isso foram reunidos todos os funcionários envolvidos nos processos e foram determinados os escores de acordo com cada critério gravidade urgência e tendência sendo representados pelos números de 1 a 5 nos quais o número 1 representa pouca ou quase nenhuma interferência com relação aos critérios e o 5 representando consequências mais graves O critério de gravidade é analisado pela intensidade ou impacto que o problema pode causar se não for solucionado A urgência é avaliada pela imposição do tempo existente para que determinada situação seja resolvida e por fim a tendência que é analisada pela tendência de evolução da situação enfrentada A Tabela 3 demonstra detalhadamente quais foram os critérios utilizados para a determinação da prioridade de atuação Journal of Lean Systems Peralta et al 2017 httpleansystemufscbr 102 Tabela 3 Representação Matriz GUT PROBLEMAS GRAVIDADE URGÊNCIA TENDÊNCIA GUT PRIORIDADE Desperdício 1 2 3 2 12 5 Desperdício 2 3 2 2 12 5 Desperdício 3 4 3 3 36 2 Desperdício 4 4 3 2 24 4 Desperdício 5 4 4 2 32 3 Desperdício 6 2 3 2 12 5 Desperdício 7 5 5 3 75 1 Onde Gravidade 1 Sem gravidade 2 Pouco grave 3 Muito grave 4 Muito mais grave e 5 Extremamente grave Urgência 1 Pode esperar 2 Pouco urgente 3 Urgente merece atenção em curto prazo 4 Muito urgente e 5 Necessidade de ação imediata e Tendência 1 Não irá mandar 2 Irá piorar em longo prazo 3 Irá piorar em médio prazo 4 Irá piorar em curto prazo e 5 Irá piorar rapidamente Com a determinação das prioridades através de auxílio da ferramenta Matriz GUT o próximo passo foi a determinação de quais medidas serão necessárias para que haja uma otimização do processo em estudo Sendo assim foi confeccionado o Plano de Ação ilustrado por intermédio da Tabela 4 Journal of Lean Systems Peralta et al 2017 httpleansystemufscbr 103 Tabela 4 Plano de ação proposto para gerenciamento dos desperdícios identificados Desperdício O que será feito Quem fará Quando será feito Como será feito 7 Redução do tempo de aguardo para que seja dado início na prestação do serviço adquirido Chefe do Almoxarifado 01122015 Será criada rotina de trabalho semanal onde todas as empresas que tiveram empenhos realizados a seu favor deverão ser contatadas com intuito de agilizar a prestação do serviço necessitado Chefe da SALC 01122015 Será determinado prazo máximo de 30 trinta dias para entrega de material ou prestação de serviços demandados 3 Redução do tempo de espera para finalização da requisição Encarregado do setor interessado 01012016 Será criado por cada seçãorepartição da organização um planejamento a curto médio e longo prazo incluindo materiais e serviços necessários 5 Redução do tempo de transporte gasto entre as repartições envolvidas no caso SALC e Almoxarifado Ordenador de Despesas 12012016 O escritório do Setor de Almoxarifado será realocado junto ao pavilhão administrativo diminuindo o percurso entre as seções 4 Não haverá pausa no fluxo de documentos por causa de acúmulo e superprodução Ordenador de Despesas Fiscal Administrativo e Encarregado Financeiro 19012016 Serão determinados horários obrigatórios durante o expediente para despacho 1 Reduzirá o tempo de espera até que o Ordenador de Despesas tome conhecimento do crédito recebido Chefe da SALC 01022016 Será criada uma rotina de trabalho na qual o chefe da SALC deverá informar de imediato o Ordenador de Despesas a cada crédito recebido 2 Reduzir o tempo de espera para descentralização aos interessados do crédito recebido pela organização Ordenador de Despesas 01022016 Será criado um Plano Diretor com objetivos estratégicos traçados pelo Ordenador de Despesas 6 Redução de tempo dispendido em processamento desnecessário SALC 01022016 Integrantes da SALC deverão remeter juntamente com a nota de empenho o contato do fornecedor pelo motivo de muitas vezes já terem realizado pesquisa similar para realização de suas operações Após determinação das prioridades de atuação através da Matriz GUT e das medidas a serem tomadas por intermédio da confecção de um Plano de Ação foi possível a otimização do processo avaliado ou seja a redução do lead time Além disso ao decorrer das pesquisas e acompanhamentos realizados durante o período foi possível identificar que todos os Journal of Lean Systems Peralta et al 2017 httpleansystemufscbr 104 processos de aquisição ou prestação de serviço independente de natureza de despesa passam pelas mesmas operações e atividades e portanto as medidas identificadas para que sejam eliminados os desperdícios podem ser aplicadas em todos os processos que envolvem compras no local de estudo resultando em um Mapa de Estado Futuro padrão conforme já apresentado no Apêndice B Desta forma adotadas e obedecidas as recomendações que visam a redução ou até eliminação dos desperdícios encontrados e levando em consideração que a operação mais importante sempre será a próxima a ser realizada durante o processo caracterizando um sistema puxado estimase um lead time máximo de 43 quarenta e três dias úteis para que seja consolidada a compra ou contratação realizada por parte da organização sendo possível que seja realizado em tempo menor que o supracitado considerando fatores como a diminuição de atividades paralelas e a próatividade do fornecedor na entrega do material ou prestação do serviço A Tabela 3 relaciona o lead time ou seja o total de dias dispendidos na execução dos processos estudados em suas condições atuais com a estimativa de dias caso as medidas recomendadas fossem adotadas e suas respectivas reduções em porcentagem Tabela 5 Comparativo lead time obtido e ideal PROCESSOS LEAD TIME Dias úteis LEAD TIME IDEAL Dias úteis REDUÇÃO 1 232 43 8146 2 298 43 8557 3 217 43 8018 Portanto diante do exposto com a redução do lead time em aproximadamente 82 é possível afirmar que os índices de empenhos inscritos em situação de Restos a Pagar consequentemente serão reduzidos ou seja os materiais serão entregues ou os serviços serão prestados durante o exercício financeiro corrente Desta forma os índices de cancelamentos e não aproveitamento dos recursos provisionados à organização também reduzirão 5 Considerações finais Este trabalho permitiu a realização de estudo sobre processo administrativo relacionado ao ramo de compras de órgão da Administração Pública Federal através do uso da ferramenta de Mapeamento do Fluxo de Valor administrativo no qual foi selecionada a Journal of Lean Systems Peralta et al 2017 httpleansystemufscbr 105 família de processos com natureza de despesa envolvendo a prestação de serviços por terceiros O processo de compras em qualquer órgão da Administração Pública é reconhecido na maioria das vezes por um processo lento e bastante burocratizado tendo em vista o fato de envolver o trabalho em conjunto de diferentes seçõesrepartições da organização e também a carência de planejamento por parte de seus gestores No decorrer dos estudos além da identificação das características supracitadas foi possível a identificação de espécies de desperdícios conforme Shingo 1996 que identifica 07 sete tipos de desperdícios os quais se estendem do ambiente de manufatura oriundos do Sistema Toyota de Produção para ambientes administrativos porém neste último são grandes as possibilidades de acarretarem efeitos negativos ao ambiente de trabalho tendo em vista a necessidade de maior comprometimento das pessoas envolvidas fato também identificado por meio informal durante as pesquisas A identificação dos desperdícios só foi possível após representação de todas as atividades envolvidas no fluxo de trabalho do processo considerando suas respectivas entradas saídas e execução em mapeamento e desenho do estado atual Desta forma tornou se possível a racionalização sobre o processo inteiro desde seu início dado pela descentralização do crédito por órgão gerencial até a apropriação da compra via sistema Desta forma foi possível propor melhorias de acordo com os desperdícios identificados visando à redução do lead time do processo de compras do órgão da Administração Pública Federal no qual foi realizado o estudo Através da confecção de plano de ação antecedido pela aplicação de Matriz GUT a qual determinou a priorização da aplicação das medidas e recomendações foi possível traçar a forma dada como ideal para o processo em estudo denominada como Mapa do Estado Futuro REFERÊNCIAS Behr A Moro E L S Estabel L B 2008 Gestão da biblioteca escolar metodologias enfoques e aplicação de ferramentas de gestão e serviços de biblioteca Ciência da Informação 372 3242 Brasil 1993 Lei no 8666 de 21 de junho de 1993 Lei de Licitações e Contrato Disponível em httpswwwplanaltogovbrccivil03LeisL8666conshtm Acessado em 20 Nov 2016 Brasil 1964 Lei nº 4320 de 17 de março de 1964 Estatui Normas Gerais de Direito Financeiro para elaboração e controle dos orçamentos e balanços da União dos Estados dos Municípios e do Distrito Federal Brasília Ghinato P 2000 Produção e Competitividade Aplicações e Inovações Recife Editora da UFPE Journal of Lean Systems Peralta et al 2017 httpleansystemufscbr 106 Gomes D E Souza R M Ferreira T A Gontijo L A 2016 Lean office para um problema no processo de solicitação de passagens de um Programa de PósGraduação Journal of Lean Systems 13 7990 Graeml A R Peinado J 2007 Administração da Produção Curitiba Unicenp Lean Institute Brasil 2005 Aplicações do Lean McManus H L 2005 Product development value stream mapping PDVSM manual Cambridge The Lean Aerospace Initiative Ohno T 1997 O Sistema Toyota de Produção Além da produção em larga escala Porto Alegre Bookman Pagnossin L G Ross C 2016 Abordagem do Lean Office aplicada em um caso prático Journal of Lean Systems 11 95113 Pruijt H 2003 Teams between neoTaylorism and antiTaylorism Economic and Industrial Democracy 241 77101 Rother M Shook J 2003 Aprendendo a enxergar Mapeando o fluxo de valor para agregar valor e eliminar o desperdício São Paulo Lean Institute Brasil Shingo S 1996 O Sistema Toyota de Produção Do ponto de vista da Engenharia de Produção Porto Alegre Bookman Tapping D Shuker T 2010 Lean Office Gerenciamento do fluxo de valor para as áreas administrativas São Paulo Leopardo Werkema C 2011 Lean Seis Sigma Rio de Janeiro Elsevier Womack J P Jones D T 2004 A mentalidade enxuta nas empresas Elimine desperdícios e crie riquezas Rio de Janeiro Elsevier This journal is licenced under a Creative Commons License Creative Commons AtribuiçãoCompartilhaIgual 40 Internacional