·
Engenharia Civil ·
Materiais de Construção Civil 1
Envie sua pergunta para a IA e receba a resposta na hora
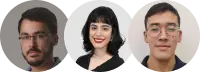
Prefere sua atividade resolvida por um tutor especialista?
- Receba resolvida até o seu prazo
- Converse com o tutor pelo chat
- Garantia de 7 dias contra erros
Recomendado para você
14
Aula sobre Cisalhamento Transversal
Materiais de Construção Civil 1
UNIFACEAR
46
Serviços Preliminares e Locação de Obra
Materiais de Construção Civil 1
UNIFACEAR
45
Conceitos e Tipos de Alvenaria para Vedações Verticais
Materiais de Construção Civil 1
UNIFACEAR
21
Introdução e Propriedades dos Materiais de Construção
Materiais de Construção Civil 1
UNIFACEAR
32
Fundamentos de Fundações: Análise e Investigação do Subsolo
Materiais de Construção Civil 1
UNIFACEAR
13
Comportamento dos Materiais: Propriedades e Testes
Materiais de Construção Civil 1
UNIFACEAR
38
Introdução aos Materiais Cerâmicos e Porcelanato
Materiais de Construção Civil 1
UNIFACEAR
18
Flambagem de Colunas: Conceitos e Exemplos
Materiais de Construção Civil 1
UNIFACEAR
43
Superestrutura: Fôrmas, Armaduras e Concreto
Materiais de Construção Civil 1
UNIFACEAR
30
Fibrocimento: Introdução, Produtos e Mercado no Brasil
Materiais de Construção Civil 1
UNIFACEAR
Texto de pré-visualização
AGLOMERANTES Lauri Anderson Lenz Aglomerantes 2 1 DEFINIÇÃO Aglomerante é o material ativo ligante em geral pulverulento cuja principal função é formar uma pasta que promove a união entre os grãos do agregado São utilizados na obtenção das argamassas e concretos na forma da própria pasta e também na confecção de natas As pastas são portanto misturas de aglomerante com água São pouco usadas devido aos efeitos secundários causados pela retração Podem ser utilizadas nos rejuntamentos de azulejos e ladrilhos As natas são pastas preparadas com excesso de água As natas de cal são utilizadas em pintura e as de cimento são usadas sobre argamassas para obtenção de superfícies lisas 2 CLASSIFICAÇÃO DOS AGLOMERANTES De acordo com o mecanismo de endurecimento os aglomerantes podem ser classificados em Aglomerantes quimicamente inertes seu endurecimento ocorre devido à secagem do material A argila é um exemplo de aglomerante inerte Aglomerantes quimicamente ativos seu endurecimento se dá por meio de reações químicas É o caso da cal e do cimento Os aglomerantes quimicamente ativos são subdivididos em dois grupos aéreos são os aglomerantes que endurecem pela ação química do CO2 no ar como por exemplo o gesso e a cal aérea hidráulicos são os aglomerantes que endurecem pela ação exclusiva da água como por exemplo a cal hidráulica o cimento Portland etc Este fenômeno recebe o nome de hidratação poliméricos são os aglomerantes que tem reação devido a polimerização de uma matriz Quanto à composição os aglomerantes são classificados em Aglomerantes 3 Aglomerantes simples são formados por apenas um produto com pequenas adições de outros componentes com o objetivo de melhorar algumas características do produto final Normalmente as adições não ultrapassam 5 em peso do material O cimento Portland comum é um exemplo deste tipo de material Aglomerantes com adição são compostos por um aglomerante simples com adições em quantidades superiores com o objetivo de conferir propriedades especiais ao aglomerante como menor permeabilidade menor calor de hidratação menor retração entre outras Aglomerantes compostos formados pela mistura de subprodutos industriais ou produtos de baixo custo com aglomerante simples O resultado é um aglomerante com custo de produção relativamente mais baixo e com pro priedades específicas Como exemplo temos o cimento pozolânico que é uma mistura do cimento Portland com uma adição chamada pozolana 3 CONCEITO DE PEGA Os aglomerantes também podem ser caracterizados segundo o tempo que levam para começar a processar o endurecimento da pasta onde são empregados O período inicial de solidificação da pasta é chamado de pega Ao se adicionar por exemplo água a um aglomerante hidráulico depois de certo tempo começam a ocorrer reações químicas de hidratação que dão origem à formação de compostos que aos poucos vão fazendo com que a pasta perca sua fluidez até que deixe de ser deformável para pequenas cargas e se torne rígida Início de pega de um aglomerante hidráulico é o período inicial de solidificação da pasta É contado a partir do lançamento da água no aglomerante até ao início das reações químicas com os compostos do aglomerante Esse fenômeno é caracterizado pelo aumento brusco da viscosidade e pela elevação da temperatura da pasta Fim de pega de um aglomerante hidráulico é quando a pasta se solidifica completamente não significando entretanto que ela tenha adquirido toda sua resistência o que só será conseguido após anos A determinação dos tempos de início de e de fim de pega do aglomerante são importantes pois através deles podese ter ideia do tempo disponível para trabalhar Aglomerantes 4 transportar lançar e adensar argamassas e concertos regálos para execução da cura bem como transitar sobre a peça Não se deve confundir pega com endurecimento O fim da pega significa que a pasta não pode mais ser manuseada e terminada essa fase inicia o endurecimento Apesar de no fim da pega a pasta já ter alguma resistência é durante o endurecimento que os ganhos de resistência são significativos De acordo com o tempo que o aglomerante desenvolve a pega na pasta podemos classificálo em Aglomerantes de pega rápida quando a pasta inicia sua solidificação num intervalo de tempo inferior a 30 minutos Aglomerantes de pega semirrápida quando a pasta inicia sua solidificação num intervalo de tempo entre 30 a 60 minutos Aglomerantes de pega normal quando a solidificação da pasta ocorre num intervalo de tempo entre 60 minutos e 6 horas No caso dos cimentos de pega normal o fim da pega se dá de cinco a dez horas depois do lançamento da água ao aglomerante Nos cimentos de pega rápida o fim da pega se verifica poucos minutos após o seu início 4 CAL A cal é obtida a partir da calcinação da rocha calcária a temperaturas elevadas composta principalmente por óxidos de cálcio e pequenas quantidades de impurezas como óxidos de magnésio sílica óxidos de ferro e óxidos de alumínio Existem três tipos de cales cal aérea cal virgem e cal hidratada e a cal hidráulica 41 CAL VIRGEM É o aglomerante resultante da calcinação de rochas calcárias CaCO3 numa temperatura inferior a de fusão do material 850 a 900C O processo de fabricação consiste resumidamente na extração da rocha e queima calcinação O produto da Aglomerantes 5 queima é chamado de cal viva ou virgem A obtenção da cal virgem pode ser expressa pela seguinte equação química O produto que se obtém com a calcinação do carbonato de cálcio recebe o nome de cal virgem ou cal viva CaO que ainda não é o aglomerante usado em construção 42 CAL EXTINTA OU HIDRATADA Para ser utilizada como aglomerante a cal precisa ser transformada em hidróxido o que se consegue com a adição de água O processo de hidratação da cal virgem adição de água é executado no canteiro de obras As pedras são colocadas em tanques onde ocorre a sua extinção ao se misturarem com a água O fenômeno de transformação de cal virgem em cal extinta ou hidratada é exotérmico isto é se dá com grande desprendimento de calor 250 calg podendo em alguns casos a temperatura atingir 400 C o que torna o processo altamente perigoso A equação química que ilustra o processo de extinção é apresentada abaixo A cal viva ou virgem normalmente apresentase em forma de grãos de grande tamanho e estrutura porosa ou em pó Já a cal hidratada é encontrada em forma de flocos ou em pó Ambas apresentam a coloração branca As características da rocha de origem influenciam diretamente a composição química da cal Segundo Oliveira 2008 quanto à composição a cal pode ser classificada em Aglomerantes 6 Cal cálcica composta por no mínimo 75 de óxidos de cálcio CaO Esse tipo de cal possui como característica a maior capacidade de sustentação da areia Cal magnesiana possui no mínimo 20 de óxidos de magnésio MgO em sua composição Quando utilizada em argamassas esse tipo de cal dá origem a misturas mais trabalháveis Como vimos anteriormente a adição de água à cal feita em obra é chamada de extinção Esse processo é feito em tanques próprios e quando a água é adicionada inicia se uma reação onde há liberação de calor Na variedade cálcica a reação é violenta com grande liberação de calor podendo atingir temperaturas da ordem de 400 em tanques fechados Na variedade magnesiana a reação é mais lenta com menor geração de calor Nesse sentido é interessante conhecer o comportamento da cal durante o processo de extinção para avaliar a maneira mais segura de manusear o material Oliveira 2008 recomenda um teste simples que pode ser feito em obra e consiste em colocar num balde 2 a 3 pedaços de cal aproximadamente 12 kg cada e encobrilos com água Se a extinção ocorrer em menos de 5 minutos a cal é classificada como extinção rápida Se a extinção ocorrer num intervalo de tempo de 5 a 30 minutos o material é classificado como de extinção média e caso demore mais de 30 minutos é classificado como extinção lenta Além do desprendimento de calor a extinção da cal tem como consequência o aumento de volume da pasta também chamado de rendimento Petrucci 1975 apresenta a classificação da cal em dois tipos de acordo com o rendimento Cal gorda possui rendimento superior a 182 ou seja uma unidade de volume de cal dá origem a mais de 182 unidades de volume de pasta A variedade cálcica é um exemplo de cal gorda Cal magra possui rendimento inferior a 182 ou seja uma unidade de volume de cal dá origem a menos de 182 unidades de volume de pasta A cal magnesiana é um exemplo de cal magra Aglomerantes 7 Após a adição de água a mistura é deixada em repouso num processo conhecido como envelhecimento da pasta O período de envelhecimento varia de acordo com o formato do material Cal em pedra o período de envelhecimento varia de 7 a 10 dias quando a variedade é cálcica e 2 semanas para a cal magnesiana Cal em pó o período de envelhecimento mínimo é de 24 horas Após o processo de extinção a cal é utilizada na composição de argamassas sendo misturada em proporções adequadas com cimento e areia Segundo Oliveira 2008 as argamassas de cal têm consistência mais ou menos plástica e endurecem por recombinação do hidróxido com o gás carbônico CO2 do ar reconstituindo o carbonato original cujos cristais formados ligam de maneira permanente os grãos do agregado utilizado Essa fase é chamada de recarbonatação Dessa forma o endurecimento das argamassas de cal se processa de fora para dentro exigindo certa porosidade que permita a evaporação da água e a penetração do gás carbônico A cal hidratada difere de a virgem por seu processo de hidratação ser feito em usina A cal virgem é moída e pulverizada e o material moído é misturado com uma quantidade exata de água Após a cal hidratada é separada da não hidratada e de impurezas por processos diversos A Figura 01 ilustra o ciclo completo da cal Figura 01 O ciclo de transformações da matéria prima e da cal Fonte O autor 2022 Aglomerantes 8 A cal hidratada possui como vantagens a maior facilidade de manuseio transporte a armazenamento além de maior segurança principalmente quanto a queimaduras pois o produto encontrase pronto para ser usado eliminando as operações de extinção e envelhecimento Oliveira 2008 aponta como desvantagens da cal hidratada o menor rendimento a menor capacidade de sustentação da areia e o fato de as misturas onde é empregada resultarem em argamassas menos trabalháveis A cal hidratada pode ser encontrada em diversas embalagens 8kg 20kg 25kg ou 40kg Normalmente estão disponíveis no mercado três tipos de material CH I Cal hidratada especial tipo I CH II Cal hidratada comum tipo II CH III Cal hidratada com carbonatos tipo III A nomenclatura diferenciada é consequência das diferentes propriedades químicas e físicas de cada produto As cales do tipo CHI e CHII são as mais empregadas na construção civil por possuírem maior capacidade de retenção de água e de areia tornandoas mais econômicas Na Construção Civil a cal é utilizada principalmente em argamassas de assentamento e revestimento pinturas misturas asfálticas estabilização de solos fabricação de blocos sílicocalcários indústria metalúrgica etc A adição de cal às argamassas proporciona melhorias em muitas características da mistura O uso da cal propicia o aumento de trabalhabilidade da mistura o que também contribui para tornar as argamassas mais econômicas pela possibilidade de aumento na quantidade de agregados O custo reduzido da cal também contribui para tornar seu uso atrativo O uso de cal nas argamassas também aumenta a retenção de água o que melhora a aderência entre os elementos da construção pois a argamassa cede água gradativamente para os elementos onde é empregada Outra contribuição da cal nas argamassas é a redução do fenômeno de retração que é a diminuição de volume capaz de gerar o aparecimento de fissuras Os revestimentos feitos de argamassa de cal e areia devem ser executados em camadas finas com intervalo de aproximadamente 10 dias entre uma camada e outra para possibilitar o endurecimento completo do material Aglomerantes 9 As pinturas à base de cal possuem propriedades fungicidas e bactericidas Além disso a cal pode ser utilizada para a separação da escória que é um resíduo da fabricação de aço para a construção civil Em obra devese evitar o recebimento da cal quando a embalagem estiver danificada e quando o material não deve ficar estocado por longos períodos O produto deve ser armazenado em pilhas de no máximo 20 sacos em local fechado e sobre estrados ou chapas de madeira 5 GESSO O gesso é um aglomerante obtido a partir da eliminação parcial ou total da água de cristalização contida em uma rocha natural chamada gipsita que ocorre na natureza em camadas estratificadas A obtenção ocorre por meio de 3 etapas a extração da rocha a diminuição de tamanho da mesma por processos de trituração e a queima do material A última etapa também é conhecida como calcinação e consiste em expor a rocha a temperaturas que podem variar de 100 a 300ºC obtendo como resultado o gesso com desprendimento de vapor dágua De acordo com a temperatura de queima podem resultar diferentes tipos de produtos O processo de queima da gipsita normalmente é feito em fornos rotativos e pode ser resumido na equação química a seguir De acordo com Oliveira 2008 o gesso ao ser misturado com água tornase plástico e enrijece rapidamente retornando a sua composição original Essa combinação fazse com a produção de uma fina malha de cristais de sulfato hidratado interpenetrada responsável pela coesão do conjunto Esse fenômeno conhecido como pega é acompanhado de elevação de temperatura tratandose de uma reação exotérmica Normalmente o gesso possui tempo de pega entre 15 e 20 minutos A temperatura da água funciona como acelerador de pega e a quantidade como retardador Aglomerantes 10 ou seja quanto maior a temperatura da água mais rápido o material reage e quanto maior a quantidade de água mais lentamente ocorrem as reações Quanto maior a quantidade de água adicionada maior a porosidade e menor a resistência Oliveira 2008 afirma que quando o processo de calcinação do gesso é feito em temperaturas mais elevadas tem como resultado um material de pega mais lenta porém de maior resistência Segundo o mesmo autor as pastas de gesso depois de endurecidas atingem resistência à compressão entre 5 e 15 MPa De acordo com Petrucci 1975 a quantidade de água necessária para o amassamento do gesso é de 50 a 70 O amassamento é feito com excesso de água para evitar uma pega muito rápida tornando a pasta manuseável por tempo suficiente à aplicação A perda de água excedente conduz ao endurecimento e aumento da resistência A Figura 02 ilustra o ciclo de transformação do gesso Figura 02 O ciclo de transformações da matéria prima e do gesso Fonte O autor O gesso como material de construção é um pó branco de elevada finura comercializado principalmente em sacos de 50 kg com o nome de gesso estuque ou gessomolde Algumas empresas fornecem embalagens de 1kg 20 kg e 40 kg No Brasil o gesso é um material relativamente escasso sendo pouco empregado como aglomerante e mais utilizado em fins ornamentais Aglomerantes 11 Possui ainda boa aderência a tijolos pedra e ferro mas é desaconselhável seu uso em superfícies metálicas pelo risco de corrosão Por outro lado não possui boa aderência a superfícies de madeira Apresenta excelentes propriedades de isolamento térmico acústico e impermeabilidade do ar É utilizado principalmente como material de acabamento em interiores para obtenção de superfícies lisas podendo substituir a massa corrida e a massa fina Nesse caso pode ser utilizado puro apenas misturado com água ou em misturas com areias sob forma de argamassas Atualmente o gesso é empregado em larga escala no formato de placas as chamadas paredes leves ou drywall Essas placas são utilizadas em forros divisórias para dar acabamento em uma parede de alvenaria bruta ou em mal estado ou para melhorar os índices de vedações térmicos ou acústicos do ambiente em que for empregado Por ser um aglomerante aéreo não se presta para a aplicação em ambientes externos devido à baixa resistência em presença da água 6 CIMENTO O cimento é um aglomerante hidráulico produzido a partir de uma mistura de rocha calcária e argila A calcinação dessa mistura dá origem ao clinquer um produto de natureza granulosa cuja composição química é constituída essencialmente de silicatos hidráulicos de cálcio com certa proporção de outras substâncias que modificam suas propriedades ou facilitam seu emprego De acordo com Oliveira 2008 entre os constituintes fundamentais do cimento 95 a 96 podemos citar Cal CaO Sílica SiO2 Alumina Al2O3 Óxido de Ferro Fe2O3 Magnésia MgO em proporção máxima de 5 Impurezas Aglomerantes 12 Processo de fabricação do cimento De acordo com a ABCP 2011 o processo de fabricação do cimento passa pelas seguintes etapas extração britagem e depósito das rochas mistura das matériasprimas homogeneização queima resfriamento adições e moagem O cimento tem como principais matériasprimas a rocha calcária e a argila Ambos os materiais são extraídos de depósitos naturais chamados jazidas e no caso da rocha calcária é necessário realizar um processo de britagem após a extração para reduzir as dimensões do material ao tamanho adequado Em seguida as matériasprimas são armazenadas em local específico de onde são encaminhadas para a dosagem que consiste em realizar a mistura da rocha calcária e da argila em proporções adequadas Essa primeira mistura é chamada de farinha crua e é encaminhada a moinhos específicos para a redução do tamanho dos grãos e homogeneização do material Para aperfeiçoar a mistura de seus componentes a farinha pode ainda passar por estruturas verticais chamadas silos de homogeneização que realizam a mistura dos materiais por processos pneumáticos e de gravidade A seguir a mistura é encaminhada a fornos rotativos onde ocorre a queima do material processo conhecido como clinquerização e realizado a temperaturas da ordem de 1400C O resultado desta queima é o clinquer que ao sair do forno é encaminhado ao processo de resfriamento O cimento pode ser composto por outros materiais além do clinquer Esses materiais chamados de adições são produtos geralmente de baixo custo que melhoram algumas propriedades do cimento além de baratear o custo de produção Após o resfriamento são feitas as adições necessárias ao clinquer e essa nova mistura de materiais é encaminhada ao processo de moagem onde o material é transformado em pó O cimento resultante da moagem é avaliado segundo alguns critérios de qualidade e após essa avaliação está pronto para a comercialização Uma ilustração resumida do processo é apresentada na Figura 03 Aglomerantes 13 Figura 03 Processo de fabricação do Cimento Portland Fonte Cimento Mauá 2021 As principais matériasprimas adicionadas ao clínquer são o gesso as escórias de altoforno os materiais pozolânicos e os materiais carbonáticos A contribuição de cada uma destas adições às propriedades finais do cimento podem ser resumidas da seguinte forma gesso tem como função básica regular o tempo de pega do cimento No cimento Portland é feita a adição de 15 a 3 ao clínquer para retardar os efeitos da hidratação do C3A escória de altoforno é o subproduto obtido durante a produção de ferro gusa nas indústrias siderúrgicas resultante do processo de fusão do minério de ferro com cal e carvão A escória se separa do ferro gusa por diferença de densidade Quimicamente é composta de uma série de silicatos que ao serem adicionados ao clínquer do cimento são capazes de sofrer reações de hidratação e posterior endurecimento A adição de escória contribui para a melhoria de algumas propriedades do cimento como por exemplo a durabilidade e a resistência à agentes químicos materiais pozolânicos são rochas vulcânicas ou matérias orgânicas fossilizadas encontradas na natureza certos tipos de argilas queimadas em elevadas temperaturas e derivados da queima de carvão mineral nas usinas Aglomerantes 14 termelétricas entre outros Esses materiais também apresentam propriedades ligantes se bem que de forma potencial para que passem a desenvolver a propriedade de ligante não basta a água é necessária a presença de mais um outro material por exemplo o clínquer O cimento com adição desse material apresenta a vantagem de conferir maior impermeabilidade as misturas com ele produzidas materiais carbonáticos são minerais moídos e calcinados Contribui para tornar a mistura mais trabalhável servindo como um lubrificante entre as partículas dos demais componentes do cimento A Figura 04 ilustra um esquema das matérias primas que compõe o cimento Figura 04 Matérias primas que formam o cimento Fonte O autor 2022 Compostos do clinquer A mistura dessas matériasprimas e a exposição à temperatura de fusão dão origem ao clinquer Como consequência desse processo ocorrem combinações químicas que resultam na formação dos seguintes compostos cujas proporções influenciam diretamente nas propriedades do cimento Aglomerantes 15 Silicato Tricálcico C3S esse componente contribui para a resistência da pasta em todas as idades O cimento ao ser misturado com a água começa a sofrer reações químicas fenômeno que chamamos de hidratação Durante a hidratação do cimento há liberação de certa quantidade de calor chamado calor de hidratação O silicato tricálcico é um dos componentes que mais libera calor durante as reações de hidratação do cimento Silicato Bicálcico C2S contribui para o endurecimento da pasta em idades avançadas e contribui pouco para a liberação de calor na hidratação do cimento Aluminato Tricálcico C3A contribui para a resistência no primeiro dia para a rapidez de pega e é o componente que mais libera calor na reação de hidratação Ferroaluminato Tetracálcio C4AF apresenta pouca influência nas características da pasta A Figura 05 a seguir mostra o comportamento mecânico dos componentes hidratáveis do cimento Figura 05 Comportamento mecânico dos compostos de cimento Fonte Petrucci 1979 Aglomerantes 16 Analisando a figura anterior verificase que a o silicato tricálcico C3S é o maior responsável pela resistência em todas as idades especialmente no primeiro mês de vida b o silicato dicálcico C2S é o maior responsável pelo ganho de resistência em idades mais avançadas principalmente após um ano de idade c o aluminato tricálcico C3A contribui para ganhos de resistência especialmente no primeiro dia d o ferroaluminato tetracálcico C4AF pouco contribui para a resistência do cimento e e o silicato tricálcico C3S e o aluminato tricálcico C3A muito contribuem para a liberação do calor de hidratação do cimento devido ao grande ganho de resistência que apresentam no 10 dia Formação dos cristais do cimento Na presença de água os silicatos C3S e C2S e os aluminatos C3A e C4AF formam produtos de hidratação que com o transcorrer do tempo dão origem a uma massa firme e resistente A hidratação dos aluminatos C3A e C4AF na presença do gesso adicionado na fabricação do cimento resulta na formação de etringitas que assumem formas de agulhas e começam minutos após o início da hidratação sendo estas responsáveis pelo fenômeno da pega A hidratação dos silicatos se dá algumas horas após o início da hidratação do cimento A hidratação do C3S e C2S origina silicatos de cálcio hidratados que possuem composição química muito variada e são representados genericamente por CSH e CH CaOH2 hidróxido de cálcio compostos que preenchem o espaço ocupado previamente pela água e pelas partículas de cimento em dissolução Os cristais de CSH formados são pequenos e fibrilares e o CH forma grandes cristais prismáticos A Tabela 01 ilustra os cristais do cimento visto por miscroscopia eletrônica e descreve as suas características Aglomerantes 17 Tabela 01 Cristais do cimento Cristal Imagem do cristal Características CSH Estruturas fibrilares Hidratação dos silicatos Altíssima resistência mecânica Quimicamente bastante estáveis Baixa porosidade 50 a 60 do volume da pasta CH Em formato hexagonal CaOH2 Agente de pH da pasta 13 Porosos Baixa resistência mecânica Solúvel em água Reativos quimicamente Etringita Estruturas tubulares e porosos Hidratação dos aluminatos e gesso Baixa resistência mecânica Primeiros cristais formados Pode causar falsa pega 15 a 20 do volume da pasta Monossulfato Hidratação dos aluminatos e gesso Porosos formato de pétala de rosa Quimicamente instáveis Baixa resistência mecânica Solúvel em água Decomposição da etringita Fonte O Autor Aglomerantes 18 Tipos de Cimento Na maioria dos casos o cimento é comercializado em sacos de papel contendo 50 kg de material ou a granel De acordo com as adições e com a resistência à compressão mínima que atinge em 28 dias o cimento recebe uma nomenclatura composta das seguintes partes O tipo de cimento é representado por números romanos seguidos ou não de letras de acordo com a composição Um mesmo tipo de cimento pode ter diferentes classes de resistência representada por um número correspondente à resistência em megapascais Mpa obtida em ensaio específico Segundo Oliveira 2008 o ensaio para determinar a classe de resistência do cimento é descrito em detalhes na NBR 7215 e de forma resumida consiste em moldar amostras também chamadas de corposdeprova de uma argamassa composta por 1 medida do cimento a ser analisado e 3 medidas de areia As amostras são mantidas em condições adequadas e ensaiadas em idades de 1 3 7 e 28 dias Os resultados mínimos de resistência devem ser de 8 Mpa na idade de 3 dias 15 MPa na idade de 7 dias e 25 MPa na idade de 28 dias A resistência mínima aos 28 dias é a classe de resistência do cimento Quanto à composição e classe de resistência o cimento pode ser dividido em diferentes tipos conforme é apresentado a seguir Cimento Tipo I CP I Também chamado de Cimento Portland comum É composto em sua maior parte por clínquer contendo uma pequena adição de gesso aproximadamente 5 que age como retardador da pega A NBR 5732 é a norma que trata deste tipo de cimento e Aglomerantes 19 estabelece 3 classes de resistência para o mesmo 25 MPa 32 MPa e 40 MPa Este tipo de cimento também pode receber adição de pequena quantidade de material pozolânico 1 5 recebendo a denominação de CP IS É indicado para construções que não necessitem de condições especiais e não apresentem exposição a agentes agressivos como águas subterrâneas esgotos água do mar e presença de sulfatos Por utilizar muito clinker seu custo de produção é elevado e por isso é pouco fabricado Cimento Tipo II CP II Recebe a adição de materiais de baixo custo o que confere propriedades especiais ao cimento A norma que trata deste tipo de cimento é NBR 11578 e as classes de resistência em que o mesmo pode ser fabricado são 25 MPa 32 MPa e 40 MPa As adições e aplicações recomendadas para cada tipo desse cimento são apresentadas na Tabela 02 Tabela 02 Adições e aplicação do cimento Tipo do Cimento Adição Usos Recomendados CP IIE Adição de escória granulada de altoforno em proporções que variam de 6 a 34 e que confere baixo calor de hidratação ao cimento Estruturas que exijam um desprendimento de calor moderadamente lento e que possam ser atacadas por sulfatos CP IIZ Adição de material pozolânico em proporções que variam de 6 a 14 o que confere menor permeabilidade à pasta onde são aplicados Obras subterrâneas marítimas e com presença de água prémoldados concreto protendido CP IIF Adição de material carbonático também chamado de fíler em proporções que variam de 6 a 10 Obras de concreto armado argamassa de assentamento e revestimento pisos e pavimentos todos em meio nãoagressivo Fonte NBR 11578 Cimento Tipo III CP III Também chamado de Cimento Portland de altoforno caracterizase por conter adição de escória em teores que variam de 35 a 70 Este tipo de cimento confere baixo calor de hidratação maior impermeabilidade e durabilidade e maior resistência a sulfatos às misturas onde é empregado Recomendado para obras de grande porte e sujeitas a condições de alta agressividade barragens fundações tubos para condução de líquidos agressivos esgotos e efluentes industriais concretos com agregados Aglomerantes 20 reativos obras submersas pavimentação de estradas pistas de aeroportos Por ser recomendado para obras de grande porte e onde haverá grande consumo é frequentemente comercializado à granel não em sacos e sob encomenda A norma que trata deste cimento é a NBR 5735 a qual estabelece 3 classes de resistência para este tipo de cimento 25 MPa 32 MPa e 40 MPa Cimento Tipo IV CP IV Também chamado de Cimento Portland pozolânico possui adição de pozolana em teores que variam de 15 a 50 que conferem alta impermeabilidade e durabilidade às misturas em que são empregados É recomendado para obras expostas à ação de águas correntes e ambientes agressivos Em longo prazo eleva a resistência mecânica de concretos quando os mesmo são comparados a concretos similares feitos com cimento comum É fabricado nas classes de resistência de 25 Mpa e 32 Mpa de acordo com a NBR 5736 Cimento Tipo V CP V ARI Este tipo de cimento confere alta resistência inicial nas primeiras idades dos concretos onde é aplicado O cimento tipo ARI ou alta resistência inicial não possui nenhuma adição especial A capacidade de desenvolver a resistência mais rápido que os demais cimentos é resultado do processo de fabricação diferenciado principalmente quanto à composição do clínquer que possui um percentual diferenciado de argila e à moagem do material que é mais fina quando comparada aos demais cimentos Como consequência a hidratação ocorre de maneira mais rápida É indicado para obras em que seja necessária a desforma rápida do concreto na confecção de elementos pré moldados blocos postes tubos entre outros A norma que trata deste tipo de cimento é a NBR 5733 que estabelece a resistência mínima para ensaios específicos com este tipo de cimento conforme Tabela 03 Aglomerantes 21 Tabela 03 Resistência mínima para ensaios específicos Idade Resistência Mínima 1 dia 14 MPa 3 dias 24 MPa 7 dias 34 MPa Fonte NBR 5733 Cimento Resistente a Sulfatos RS De acordo com a ABCP qualquer dos cimentos já estudados pode ser resistente a sulfatos desde que se enquadre em alguns requisitos como teor do componente químico C3A do clínquer inferior a 8 e teor de adições carbonáticas de no máximo 5 Os cimentos do tipo altoforno também podem ser resistentes a sulfatos quando contiverem entre 60 e 70 de escória granulada de altoforno em massa Os cimentos do tipo pozolânico que contiverem entre 25 e 40 de material pozolânico em massa também apresentam comportamento satisfatório quando expostos à ação de águas sulfatadas O cimento resistente a sulfatos é recomendado para uso em redes de esgotos de águas servidas ou industriais água do mar e em alguns tipos de solos ambientes onde este agente agressivo pode estar presente Cimento Aluminoso Resulta do cozimento de uma mistura de bauxita e calcário De acordo com Oliveira 2008 este tipo de cimento possui pega lenta porém alcança altas resistências em pouco tempo 315 MPa em 2 dias 40 MPa em 28 dias A reação de hidratação é intensa e desenvolve grandes quantidades de calor Sua principal utilização é como cimento refratário resistindo a temperaturas superiores a 1200ºC podendo chegar a 1400C em misturas com agregados convenientemente escolhidos Não é fabricado no Brasil Cimento Branco CPB Possui coloração branca em função das matériasprimas utilizadas na sua fabricação caulim no lugar da argila que possuem baixos teores de óxido de ferro e Aglomerantes 22 manganês Além disso são observadas condições especiais durante o processo de fabricação O cimento branco pode ser do tipo estrutural ou nãoestrutural O CPB estrutural é utilizado em concretos brancos para fins arquitetônicos e é fabricado nas classes de resistência 25 MPa 32 MPa e 40 MPa O CPB não estrutural é utilizado para rejuntamento de azulejos e aplicações não estruturais Em ambos os casos o cimento pode ser associado a pigmentos o que resulta nos concretos coloridos 7 OUTROS AGLOMERANTES Alguns autores classificam os asfaltos como aglomerantes Vamos falar desses materiais de maneira resumida pois a grande maioria das aplicações que necessitam de aglomerantes faz uso dos tipos minerais como o gesso a cal e o cimento Oliveira 2008 define os asfaltos como produtos resultantes de matéria hidrocarbonada de cor preta presente em petróleos crus nos quais se encontra dissolvido por óleos solventes Quando esses óleos são removidos do petróleo cru obtémse o asfalto Segundo o mesmo autor os asfaltos caracterizamse por serem aglomerantes de forte ligação rapidamente adesivos altamente impermeáveis e de longa durabilidade São utilizados principalmente em obras de pavimentação e de impermeabilização entre outras aplicações Segundo Oliveira 2008 os asfaltos podem ser classificados em 3 tipos sendo cada tipo caracterizado da seguinte maneira Cimentos Asfálticos são obtidos a partir dos materiais residuais da destilação do petróleo compostos por asfalto e óleo Sua consistência varia de firme a dura em temperaturas normais devendo ser aquecidos para se tornarem aplicáveis na forma de fluido São classificados segundo a resistência que oferecem à penetração determinada em ensaio específico Asfaltos líquidos são obtidos pela mistura de cimentos asfálticos com óleos asfaltos de cura lenta SC e solventes cura média MC ou rápida RC e são aquecidos em temperaturas inferiores às do cimento asfáltico para o uso São produzidos em diversas variedades e recebem a nomenclatura em função da cura SC MC ou RC e da consistência 0 mais mole a 5 mais firmes Aglomerantes 23 Emulsões asfálticas são misturas líquidas e homogêneas de cimento asfáltico emulsionantes e água com a proporção de água variando de 30 a 45 apresentandose em colorações que variam do marromclaro ao marrom escuro De acordo com Silva 1985 as emulsões são classificadas de acordo com a rapidez em que ocorre a perda de água também chamada de quebra ou ruptura Aglomerantes 24 REFERÊNCIAS BIBLIOGRÁFICAS CALLISTER W D Ciência e Engenharia de Materiais Uma Introdução John Wiley Sons Inc 2002 Associação Brasileira de Cimento Portland Fabricação do cimento Disponível em httpwwwabcporgbrconteudo basicosobrecimentofabricacaofabricacao Acesso em 26 jul 2011 Associação Brasileira de Cimento Portland Tipos de cimento Disponível em httpwwwabcporgbrconteudo basicosobrecimentotiposaversatilidadedo cimentobrasileiro Acesso em 28 jul 2011 Associação Brasileira de Normas Técnicas NBR 5732 Cimento Portland comum Rio de Janeiro 1991 Associação Brasileira de Normas Técnicas NBR 5733 Cimento Portland de alta resistência inicial Rio de Janeiro 1991 Associação Brasileira de Normas Técnicas NBR 5735 Cimento Portland de altoforno Rio de Janeiro 1991 Associação Brasileira de Normas Técnicas NBR 5736 Cimento Portland pozolânico Rio de Janeiro 1991 Associação Brasileira de Normas Técnicas NBR 7215 Cimento Portland determinação da resistência à compressão Rio de Janeiro 1996 Associação Brasileira de Normas Técnicas NBR 11578 Cimento Portland composto especificação Rio de Janeiro 1991 Associação Brasileira de Normas Técnicas NBR 12989 Cimento Portland branco especificação Rio de Janeiro 1993 OLIVEIRA HM Aglomerantes In BAUER LFA Org Materiais de Construção I 5 ed Rio de Janeiro LTC 2008 p 11 34 OLIVEIRA HM Cimento Portland In BAUER LFA Org Materiais de Construção I 5 ed Rio de Janeiro LTC 2008 p 35 62 PETRUCCI E G R Materiais de Construção Porto Alegre Globo 1975 SILVA Moema Ribas Materiais de Construção São Paulo PINI 1985
Envie sua pergunta para a IA e receba a resposta na hora
Recomendado para você
14
Aula sobre Cisalhamento Transversal
Materiais de Construção Civil 1
UNIFACEAR
46
Serviços Preliminares e Locação de Obra
Materiais de Construção Civil 1
UNIFACEAR
45
Conceitos e Tipos de Alvenaria para Vedações Verticais
Materiais de Construção Civil 1
UNIFACEAR
21
Introdução e Propriedades dos Materiais de Construção
Materiais de Construção Civil 1
UNIFACEAR
32
Fundamentos de Fundações: Análise e Investigação do Subsolo
Materiais de Construção Civil 1
UNIFACEAR
13
Comportamento dos Materiais: Propriedades e Testes
Materiais de Construção Civil 1
UNIFACEAR
38
Introdução aos Materiais Cerâmicos e Porcelanato
Materiais de Construção Civil 1
UNIFACEAR
18
Flambagem de Colunas: Conceitos e Exemplos
Materiais de Construção Civil 1
UNIFACEAR
43
Superestrutura: Fôrmas, Armaduras e Concreto
Materiais de Construção Civil 1
UNIFACEAR
30
Fibrocimento: Introdução, Produtos e Mercado no Brasil
Materiais de Construção Civil 1
UNIFACEAR
Texto de pré-visualização
AGLOMERANTES Lauri Anderson Lenz Aglomerantes 2 1 DEFINIÇÃO Aglomerante é o material ativo ligante em geral pulverulento cuja principal função é formar uma pasta que promove a união entre os grãos do agregado São utilizados na obtenção das argamassas e concretos na forma da própria pasta e também na confecção de natas As pastas são portanto misturas de aglomerante com água São pouco usadas devido aos efeitos secundários causados pela retração Podem ser utilizadas nos rejuntamentos de azulejos e ladrilhos As natas são pastas preparadas com excesso de água As natas de cal são utilizadas em pintura e as de cimento são usadas sobre argamassas para obtenção de superfícies lisas 2 CLASSIFICAÇÃO DOS AGLOMERANTES De acordo com o mecanismo de endurecimento os aglomerantes podem ser classificados em Aglomerantes quimicamente inertes seu endurecimento ocorre devido à secagem do material A argila é um exemplo de aglomerante inerte Aglomerantes quimicamente ativos seu endurecimento se dá por meio de reações químicas É o caso da cal e do cimento Os aglomerantes quimicamente ativos são subdivididos em dois grupos aéreos são os aglomerantes que endurecem pela ação química do CO2 no ar como por exemplo o gesso e a cal aérea hidráulicos são os aglomerantes que endurecem pela ação exclusiva da água como por exemplo a cal hidráulica o cimento Portland etc Este fenômeno recebe o nome de hidratação poliméricos são os aglomerantes que tem reação devido a polimerização de uma matriz Quanto à composição os aglomerantes são classificados em Aglomerantes 3 Aglomerantes simples são formados por apenas um produto com pequenas adições de outros componentes com o objetivo de melhorar algumas características do produto final Normalmente as adições não ultrapassam 5 em peso do material O cimento Portland comum é um exemplo deste tipo de material Aglomerantes com adição são compostos por um aglomerante simples com adições em quantidades superiores com o objetivo de conferir propriedades especiais ao aglomerante como menor permeabilidade menor calor de hidratação menor retração entre outras Aglomerantes compostos formados pela mistura de subprodutos industriais ou produtos de baixo custo com aglomerante simples O resultado é um aglomerante com custo de produção relativamente mais baixo e com pro priedades específicas Como exemplo temos o cimento pozolânico que é uma mistura do cimento Portland com uma adição chamada pozolana 3 CONCEITO DE PEGA Os aglomerantes também podem ser caracterizados segundo o tempo que levam para começar a processar o endurecimento da pasta onde são empregados O período inicial de solidificação da pasta é chamado de pega Ao se adicionar por exemplo água a um aglomerante hidráulico depois de certo tempo começam a ocorrer reações químicas de hidratação que dão origem à formação de compostos que aos poucos vão fazendo com que a pasta perca sua fluidez até que deixe de ser deformável para pequenas cargas e se torne rígida Início de pega de um aglomerante hidráulico é o período inicial de solidificação da pasta É contado a partir do lançamento da água no aglomerante até ao início das reações químicas com os compostos do aglomerante Esse fenômeno é caracterizado pelo aumento brusco da viscosidade e pela elevação da temperatura da pasta Fim de pega de um aglomerante hidráulico é quando a pasta se solidifica completamente não significando entretanto que ela tenha adquirido toda sua resistência o que só será conseguido após anos A determinação dos tempos de início de e de fim de pega do aglomerante são importantes pois através deles podese ter ideia do tempo disponível para trabalhar Aglomerantes 4 transportar lançar e adensar argamassas e concertos regálos para execução da cura bem como transitar sobre a peça Não se deve confundir pega com endurecimento O fim da pega significa que a pasta não pode mais ser manuseada e terminada essa fase inicia o endurecimento Apesar de no fim da pega a pasta já ter alguma resistência é durante o endurecimento que os ganhos de resistência são significativos De acordo com o tempo que o aglomerante desenvolve a pega na pasta podemos classificálo em Aglomerantes de pega rápida quando a pasta inicia sua solidificação num intervalo de tempo inferior a 30 minutos Aglomerantes de pega semirrápida quando a pasta inicia sua solidificação num intervalo de tempo entre 30 a 60 minutos Aglomerantes de pega normal quando a solidificação da pasta ocorre num intervalo de tempo entre 60 minutos e 6 horas No caso dos cimentos de pega normal o fim da pega se dá de cinco a dez horas depois do lançamento da água ao aglomerante Nos cimentos de pega rápida o fim da pega se verifica poucos minutos após o seu início 4 CAL A cal é obtida a partir da calcinação da rocha calcária a temperaturas elevadas composta principalmente por óxidos de cálcio e pequenas quantidades de impurezas como óxidos de magnésio sílica óxidos de ferro e óxidos de alumínio Existem três tipos de cales cal aérea cal virgem e cal hidratada e a cal hidráulica 41 CAL VIRGEM É o aglomerante resultante da calcinação de rochas calcárias CaCO3 numa temperatura inferior a de fusão do material 850 a 900C O processo de fabricação consiste resumidamente na extração da rocha e queima calcinação O produto da Aglomerantes 5 queima é chamado de cal viva ou virgem A obtenção da cal virgem pode ser expressa pela seguinte equação química O produto que se obtém com a calcinação do carbonato de cálcio recebe o nome de cal virgem ou cal viva CaO que ainda não é o aglomerante usado em construção 42 CAL EXTINTA OU HIDRATADA Para ser utilizada como aglomerante a cal precisa ser transformada em hidróxido o que se consegue com a adição de água O processo de hidratação da cal virgem adição de água é executado no canteiro de obras As pedras são colocadas em tanques onde ocorre a sua extinção ao se misturarem com a água O fenômeno de transformação de cal virgem em cal extinta ou hidratada é exotérmico isto é se dá com grande desprendimento de calor 250 calg podendo em alguns casos a temperatura atingir 400 C o que torna o processo altamente perigoso A equação química que ilustra o processo de extinção é apresentada abaixo A cal viva ou virgem normalmente apresentase em forma de grãos de grande tamanho e estrutura porosa ou em pó Já a cal hidratada é encontrada em forma de flocos ou em pó Ambas apresentam a coloração branca As características da rocha de origem influenciam diretamente a composição química da cal Segundo Oliveira 2008 quanto à composição a cal pode ser classificada em Aglomerantes 6 Cal cálcica composta por no mínimo 75 de óxidos de cálcio CaO Esse tipo de cal possui como característica a maior capacidade de sustentação da areia Cal magnesiana possui no mínimo 20 de óxidos de magnésio MgO em sua composição Quando utilizada em argamassas esse tipo de cal dá origem a misturas mais trabalháveis Como vimos anteriormente a adição de água à cal feita em obra é chamada de extinção Esse processo é feito em tanques próprios e quando a água é adicionada inicia se uma reação onde há liberação de calor Na variedade cálcica a reação é violenta com grande liberação de calor podendo atingir temperaturas da ordem de 400 em tanques fechados Na variedade magnesiana a reação é mais lenta com menor geração de calor Nesse sentido é interessante conhecer o comportamento da cal durante o processo de extinção para avaliar a maneira mais segura de manusear o material Oliveira 2008 recomenda um teste simples que pode ser feito em obra e consiste em colocar num balde 2 a 3 pedaços de cal aproximadamente 12 kg cada e encobrilos com água Se a extinção ocorrer em menos de 5 minutos a cal é classificada como extinção rápida Se a extinção ocorrer num intervalo de tempo de 5 a 30 minutos o material é classificado como de extinção média e caso demore mais de 30 minutos é classificado como extinção lenta Além do desprendimento de calor a extinção da cal tem como consequência o aumento de volume da pasta também chamado de rendimento Petrucci 1975 apresenta a classificação da cal em dois tipos de acordo com o rendimento Cal gorda possui rendimento superior a 182 ou seja uma unidade de volume de cal dá origem a mais de 182 unidades de volume de pasta A variedade cálcica é um exemplo de cal gorda Cal magra possui rendimento inferior a 182 ou seja uma unidade de volume de cal dá origem a menos de 182 unidades de volume de pasta A cal magnesiana é um exemplo de cal magra Aglomerantes 7 Após a adição de água a mistura é deixada em repouso num processo conhecido como envelhecimento da pasta O período de envelhecimento varia de acordo com o formato do material Cal em pedra o período de envelhecimento varia de 7 a 10 dias quando a variedade é cálcica e 2 semanas para a cal magnesiana Cal em pó o período de envelhecimento mínimo é de 24 horas Após o processo de extinção a cal é utilizada na composição de argamassas sendo misturada em proporções adequadas com cimento e areia Segundo Oliveira 2008 as argamassas de cal têm consistência mais ou menos plástica e endurecem por recombinação do hidróxido com o gás carbônico CO2 do ar reconstituindo o carbonato original cujos cristais formados ligam de maneira permanente os grãos do agregado utilizado Essa fase é chamada de recarbonatação Dessa forma o endurecimento das argamassas de cal se processa de fora para dentro exigindo certa porosidade que permita a evaporação da água e a penetração do gás carbônico A cal hidratada difere de a virgem por seu processo de hidratação ser feito em usina A cal virgem é moída e pulverizada e o material moído é misturado com uma quantidade exata de água Após a cal hidratada é separada da não hidratada e de impurezas por processos diversos A Figura 01 ilustra o ciclo completo da cal Figura 01 O ciclo de transformações da matéria prima e da cal Fonte O autor 2022 Aglomerantes 8 A cal hidratada possui como vantagens a maior facilidade de manuseio transporte a armazenamento além de maior segurança principalmente quanto a queimaduras pois o produto encontrase pronto para ser usado eliminando as operações de extinção e envelhecimento Oliveira 2008 aponta como desvantagens da cal hidratada o menor rendimento a menor capacidade de sustentação da areia e o fato de as misturas onde é empregada resultarem em argamassas menos trabalháveis A cal hidratada pode ser encontrada em diversas embalagens 8kg 20kg 25kg ou 40kg Normalmente estão disponíveis no mercado três tipos de material CH I Cal hidratada especial tipo I CH II Cal hidratada comum tipo II CH III Cal hidratada com carbonatos tipo III A nomenclatura diferenciada é consequência das diferentes propriedades químicas e físicas de cada produto As cales do tipo CHI e CHII são as mais empregadas na construção civil por possuírem maior capacidade de retenção de água e de areia tornandoas mais econômicas Na Construção Civil a cal é utilizada principalmente em argamassas de assentamento e revestimento pinturas misturas asfálticas estabilização de solos fabricação de blocos sílicocalcários indústria metalúrgica etc A adição de cal às argamassas proporciona melhorias em muitas características da mistura O uso da cal propicia o aumento de trabalhabilidade da mistura o que também contribui para tornar as argamassas mais econômicas pela possibilidade de aumento na quantidade de agregados O custo reduzido da cal também contribui para tornar seu uso atrativo O uso de cal nas argamassas também aumenta a retenção de água o que melhora a aderência entre os elementos da construção pois a argamassa cede água gradativamente para os elementos onde é empregada Outra contribuição da cal nas argamassas é a redução do fenômeno de retração que é a diminuição de volume capaz de gerar o aparecimento de fissuras Os revestimentos feitos de argamassa de cal e areia devem ser executados em camadas finas com intervalo de aproximadamente 10 dias entre uma camada e outra para possibilitar o endurecimento completo do material Aglomerantes 9 As pinturas à base de cal possuem propriedades fungicidas e bactericidas Além disso a cal pode ser utilizada para a separação da escória que é um resíduo da fabricação de aço para a construção civil Em obra devese evitar o recebimento da cal quando a embalagem estiver danificada e quando o material não deve ficar estocado por longos períodos O produto deve ser armazenado em pilhas de no máximo 20 sacos em local fechado e sobre estrados ou chapas de madeira 5 GESSO O gesso é um aglomerante obtido a partir da eliminação parcial ou total da água de cristalização contida em uma rocha natural chamada gipsita que ocorre na natureza em camadas estratificadas A obtenção ocorre por meio de 3 etapas a extração da rocha a diminuição de tamanho da mesma por processos de trituração e a queima do material A última etapa também é conhecida como calcinação e consiste em expor a rocha a temperaturas que podem variar de 100 a 300ºC obtendo como resultado o gesso com desprendimento de vapor dágua De acordo com a temperatura de queima podem resultar diferentes tipos de produtos O processo de queima da gipsita normalmente é feito em fornos rotativos e pode ser resumido na equação química a seguir De acordo com Oliveira 2008 o gesso ao ser misturado com água tornase plástico e enrijece rapidamente retornando a sua composição original Essa combinação fazse com a produção de uma fina malha de cristais de sulfato hidratado interpenetrada responsável pela coesão do conjunto Esse fenômeno conhecido como pega é acompanhado de elevação de temperatura tratandose de uma reação exotérmica Normalmente o gesso possui tempo de pega entre 15 e 20 minutos A temperatura da água funciona como acelerador de pega e a quantidade como retardador Aglomerantes 10 ou seja quanto maior a temperatura da água mais rápido o material reage e quanto maior a quantidade de água mais lentamente ocorrem as reações Quanto maior a quantidade de água adicionada maior a porosidade e menor a resistência Oliveira 2008 afirma que quando o processo de calcinação do gesso é feito em temperaturas mais elevadas tem como resultado um material de pega mais lenta porém de maior resistência Segundo o mesmo autor as pastas de gesso depois de endurecidas atingem resistência à compressão entre 5 e 15 MPa De acordo com Petrucci 1975 a quantidade de água necessária para o amassamento do gesso é de 50 a 70 O amassamento é feito com excesso de água para evitar uma pega muito rápida tornando a pasta manuseável por tempo suficiente à aplicação A perda de água excedente conduz ao endurecimento e aumento da resistência A Figura 02 ilustra o ciclo de transformação do gesso Figura 02 O ciclo de transformações da matéria prima e do gesso Fonte O autor O gesso como material de construção é um pó branco de elevada finura comercializado principalmente em sacos de 50 kg com o nome de gesso estuque ou gessomolde Algumas empresas fornecem embalagens de 1kg 20 kg e 40 kg No Brasil o gesso é um material relativamente escasso sendo pouco empregado como aglomerante e mais utilizado em fins ornamentais Aglomerantes 11 Possui ainda boa aderência a tijolos pedra e ferro mas é desaconselhável seu uso em superfícies metálicas pelo risco de corrosão Por outro lado não possui boa aderência a superfícies de madeira Apresenta excelentes propriedades de isolamento térmico acústico e impermeabilidade do ar É utilizado principalmente como material de acabamento em interiores para obtenção de superfícies lisas podendo substituir a massa corrida e a massa fina Nesse caso pode ser utilizado puro apenas misturado com água ou em misturas com areias sob forma de argamassas Atualmente o gesso é empregado em larga escala no formato de placas as chamadas paredes leves ou drywall Essas placas são utilizadas em forros divisórias para dar acabamento em uma parede de alvenaria bruta ou em mal estado ou para melhorar os índices de vedações térmicos ou acústicos do ambiente em que for empregado Por ser um aglomerante aéreo não se presta para a aplicação em ambientes externos devido à baixa resistência em presença da água 6 CIMENTO O cimento é um aglomerante hidráulico produzido a partir de uma mistura de rocha calcária e argila A calcinação dessa mistura dá origem ao clinquer um produto de natureza granulosa cuja composição química é constituída essencialmente de silicatos hidráulicos de cálcio com certa proporção de outras substâncias que modificam suas propriedades ou facilitam seu emprego De acordo com Oliveira 2008 entre os constituintes fundamentais do cimento 95 a 96 podemos citar Cal CaO Sílica SiO2 Alumina Al2O3 Óxido de Ferro Fe2O3 Magnésia MgO em proporção máxima de 5 Impurezas Aglomerantes 12 Processo de fabricação do cimento De acordo com a ABCP 2011 o processo de fabricação do cimento passa pelas seguintes etapas extração britagem e depósito das rochas mistura das matériasprimas homogeneização queima resfriamento adições e moagem O cimento tem como principais matériasprimas a rocha calcária e a argila Ambos os materiais são extraídos de depósitos naturais chamados jazidas e no caso da rocha calcária é necessário realizar um processo de britagem após a extração para reduzir as dimensões do material ao tamanho adequado Em seguida as matériasprimas são armazenadas em local específico de onde são encaminhadas para a dosagem que consiste em realizar a mistura da rocha calcária e da argila em proporções adequadas Essa primeira mistura é chamada de farinha crua e é encaminhada a moinhos específicos para a redução do tamanho dos grãos e homogeneização do material Para aperfeiçoar a mistura de seus componentes a farinha pode ainda passar por estruturas verticais chamadas silos de homogeneização que realizam a mistura dos materiais por processos pneumáticos e de gravidade A seguir a mistura é encaminhada a fornos rotativos onde ocorre a queima do material processo conhecido como clinquerização e realizado a temperaturas da ordem de 1400C O resultado desta queima é o clinquer que ao sair do forno é encaminhado ao processo de resfriamento O cimento pode ser composto por outros materiais além do clinquer Esses materiais chamados de adições são produtos geralmente de baixo custo que melhoram algumas propriedades do cimento além de baratear o custo de produção Após o resfriamento são feitas as adições necessárias ao clinquer e essa nova mistura de materiais é encaminhada ao processo de moagem onde o material é transformado em pó O cimento resultante da moagem é avaliado segundo alguns critérios de qualidade e após essa avaliação está pronto para a comercialização Uma ilustração resumida do processo é apresentada na Figura 03 Aglomerantes 13 Figura 03 Processo de fabricação do Cimento Portland Fonte Cimento Mauá 2021 As principais matériasprimas adicionadas ao clínquer são o gesso as escórias de altoforno os materiais pozolânicos e os materiais carbonáticos A contribuição de cada uma destas adições às propriedades finais do cimento podem ser resumidas da seguinte forma gesso tem como função básica regular o tempo de pega do cimento No cimento Portland é feita a adição de 15 a 3 ao clínquer para retardar os efeitos da hidratação do C3A escória de altoforno é o subproduto obtido durante a produção de ferro gusa nas indústrias siderúrgicas resultante do processo de fusão do minério de ferro com cal e carvão A escória se separa do ferro gusa por diferença de densidade Quimicamente é composta de uma série de silicatos que ao serem adicionados ao clínquer do cimento são capazes de sofrer reações de hidratação e posterior endurecimento A adição de escória contribui para a melhoria de algumas propriedades do cimento como por exemplo a durabilidade e a resistência à agentes químicos materiais pozolânicos são rochas vulcânicas ou matérias orgânicas fossilizadas encontradas na natureza certos tipos de argilas queimadas em elevadas temperaturas e derivados da queima de carvão mineral nas usinas Aglomerantes 14 termelétricas entre outros Esses materiais também apresentam propriedades ligantes se bem que de forma potencial para que passem a desenvolver a propriedade de ligante não basta a água é necessária a presença de mais um outro material por exemplo o clínquer O cimento com adição desse material apresenta a vantagem de conferir maior impermeabilidade as misturas com ele produzidas materiais carbonáticos são minerais moídos e calcinados Contribui para tornar a mistura mais trabalhável servindo como um lubrificante entre as partículas dos demais componentes do cimento A Figura 04 ilustra um esquema das matérias primas que compõe o cimento Figura 04 Matérias primas que formam o cimento Fonte O autor 2022 Compostos do clinquer A mistura dessas matériasprimas e a exposição à temperatura de fusão dão origem ao clinquer Como consequência desse processo ocorrem combinações químicas que resultam na formação dos seguintes compostos cujas proporções influenciam diretamente nas propriedades do cimento Aglomerantes 15 Silicato Tricálcico C3S esse componente contribui para a resistência da pasta em todas as idades O cimento ao ser misturado com a água começa a sofrer reações químicas fenômeno que chamamos de hidratação Durante a hidratação do cimento há liberação de certa quantidade de calor chamado calor de hidratação O silicato tricálcico é um dos componentes que mais libera calor durante as reações de hidratação do cimento Silicato Bicálcico C2S contribui para o endurecimento da pasta em idades avançadas e contribui pouco para a liberação de calor na hidratação do cimento Aluminato Tricálcico C3A contribui para a resistência no primeiro dia para a rapidez de pega e é o componente que mais libera calor na reação de hidratação Ferroaluminato Tetracálcio C4AF apresenta pouca influência nas características da pasta A Figura 05 a seguir mostra o comportamento mecânico dos componentes hidratáveis do cimento Figura 05 Comportamento mecânico dos compostos de cimento Fonte Petrucci 1979 Aglomerantes 16 Analisando a figura anterior verificase que a o silicato tricálcico C3S é o maior responsável pela resistência em todas as idades especialmente no primeiro mês de vida b o silicato dicálcico C2S é o maior responsável pelo ganho de resistência em idades mais avançadas principalmente após um ano de idade c o aluminato tricálcico C3A contribui para ganhos de resistência especialmente no primeiro dia d o ferroaluminato tetracálcico C4AF pouco contribui para a resistência do cimento e e o silicato tricálcico C3S e o aluminato tricálcico C3A muito contribuem para a liberação do calor de hidratação do cimento devido ao grande ganho de resistência que apresentam no 10 dia Formação dos cristais do cimento Na presença de água os silicatos C3S e C2S e os aluminatos C3A e C4AF formam produtos de hidratação que com o transcorrer do tempo dão origem a uma massa firme e resistente A hidratação dos aluminatos C3A e C4AF na presença do gesso adicionado na fabricação do cimento resulta na formação de etringitas que assumem formas de agulhas e começam minutos após o início da hidratação sendo estas responsáveis pelo fenômeno da pega A hidratação dos silicatos se dá algumas horas após o início da hidratação do cimento A hidratação do C3S e C2S origina silicatos de cálcio hidratados que possuem composição química muito variada e são representados genericamente por CSH e CH CaOH2 hidróxido de cálcio compostos que preenchem o espaço ocupado previamente pela água e pelas partículas de cimento em dissolução Os cristais de CSH formados são pequenos e fibrilares e o CH forma grandes cristais prismáticos A Tabela 01 ilustra os cristais do cimento visto por miscroscopia eletrônica e descreve as suas características Aglomerantes 17 Tabela 01 Cristais do cimento Cristal Imagem do cristal Características CSH Estruturas fibrilares Hidratação dos silicatos Altíssima resistência mecânica Quimicamente bastante estáveis Baixa porosidade 50 a 60 do volume da pasta CH Em formato hexagonal CaOH2 Agente de pH da pasta 13 Porosos Baixa resistência mecânica Solúvel em água Reativos quimicamente Etringita Estruturas tubulares e porosos Hidratação dos aluminatos e gesso Baixa resistência mecânica Primeiros cristais formados Pode causar falsa pega 15 a 20 do volume da pasta Monossulfato Hidratação dos aluminatos e gesso Porosos formato de pétala de rosa Quimicamente instáveis Baixa resistência mecânica Solúvel em água Decomposição da etringita Fonte O Autor Aglomerantes 18 Tipos de Cimento Na maioria dos casos o cimento é comercializado em sacos de papel contendo 50 kg de material ou a granel De acordo com as adições e com a resistência à compressão mínima que atinge em 28 dias o cimento recebe uma nomenclatura composta das seguintes partes O tipo de cimento é representado por números romanos seguidos ou não de letras de acordo com a composição Um mesmo tipo de cimento pode ter diferentes classes de resistência representada por um número correspondente à resistência em megapascais Mpa obtida em ensaio específico Segundo Oliveira 2008 o ensaio para determinar a classe de resistência do cimento é descrito em detalhes na NBR 7215 e de forma resumida consiste em moldar amostras também chamadas de corposdeprova de uma argamassa composta por 1 medida do cimento a ser analisado e 3 medidas de areia As amostras são mantidas em condições adequadas e ensaiadas em idades de 1 3 7 e 28 dias Os resultados mínimos de resistência devem ser de 8 Mpa na idade de 3 dias 15 MPa na idade de 7 dias e 25 MPa na idade de 28 dias A resistência mínima aos 28 dias é a classe de resistência do cimento Quanto à composição e classe de resistência o cimento pode ser dividido em diferentes tipos conforme é apresentado a seguir Cimento Tipo I CP I Também chamado de Cimento Portland comum É composto em sua maior parte por clínquer contendo uma pequena adição de gesso aproximadamente 5 que age como retardador da pega A NBR 5732 é a norma que trata deste tipo de cimento e Aglomerantes 19 estabelece 3 classes de resistência para o mesmo 25 MPa 32 MPa e 40 MPa Este tipo de cimento também pode receber adição de pequena quantidade de material pozolânico 1 5 recebendo a denominação de CP IS É indicado para construções que não necessitem de condições especiais e não apresentem exposição a agentes agressivos como águas subterrâneas esgotos água do mar e presença de sulfatos Por utilizar muito clinker seu custo de produção é elevado e por isso é pouco fabricado Cimento Tipo II CP II Recebe a adição de materiais de baixo custo o que confere propriedades especiais ao cimento A norma que trata deste tipo de cimento é NBR 11578 e as classes de resistência em que o mesmo pode ser fabricado são 25 MPa 32 MPa e 40 MPa As adições e aplicações recomendadas para cada tipo desse cimento são apresentadas na Tabela 02 Tabela 02 Adições e aplicação do cimento Tipo do Cimento Adição Usos Recomendados CP IIE Adição de escória granulada de altoforno em proporções que variam de 6 a 34 e que confere baixo calor de hidratação ao cimento Estruturas que exijam um desprendimento de calor moderadamente lento e que possam ser atacadas por sulfatos CP IIZ Adição de material pozolânico em proporções que variam de 6 a 14 o que confere menor permeabilidade à pasta onde são aplicados Obras subterrâneas marítimas e com presença de água prémoldados concreto protendido CP IIF Adição de material carbonático também chamado de fíler em proporções que variam de 6 a 10 Obras de concreto armado argamassa de assentamento e revestimento pisos e pavimentos todos em meio nãoagressivo Fonte NBR 11578 Cimento Tipo III CP III Também chamado de Cimento Portland de altoforno caracterizase por conter adição de escória em teores que variam de 35 a 70 Este tipo de cimento confere baixo calor de hidratação maior impermeabilidade e durabilidade e maior resistência a sulfatos às misturas onde é empregado Recomendado para obras de grande porte e sujeitas a condições de alta agressividade barragens fundações tubos para condução de líquidos agressivos esgotos e efluentes industriais concretos com agregados Aglomerantes 20 reativos obras submersas pavimentação de estradas pistas de aeroportos Por ser recomendado para obras de grande porte e onde haverá grande consumo é frequentemente comercializado à granel não em sacos e sob encomenda A norma que trata deste cimento é a NBR 5735 a qual estabelece 3 classes de resistência para este tipo de cimento 25 MPa 32 MPa e 40 MPa Cimento Tipo IV CP IV Também chamado de Cimento Portland pozolânico possui adição de pozolana em teores que variam de 15 a 50 que conferem alta impermeabilidade e durabilidade às misturas em que são empregados É recomendado para obras expostas à ação de águas correntes e ambientes agressivos Em longo prazo eleva a resistência mecânica de concretos quando os mesmo são comparados a concretos similares feitos com cimento comum É fabricado nas classes de resistência de 25 Mpa e 32 Mpa de acordo com a NBR 5736 Cimento Tipo V CP V ARI Este tipo de cimento confere alta resistência inicial nas primeiras idades dos concretos onde é aplicado O cimento tipo ARI ou alta resistência inicial não possui nenhuma adição especial A capacidade de desenvolver a resistência mais rápido que os demais cimentos é resultado do processo de fabricação diferenciado principalmente quanto à composição do clínquer que possui um percentual diferenciado de argila e à moagem do material que é mais fina quando comparada aos demais cimentos Como consequência a hidratação ocorre de maneira mais rápida É indicado para obras em que seja necessária a desforma rápida do concreto na confecção de elementos pré moldados blocos postes tubos entre outros A norma que trata deste tipo de cimento é a NBR 5733 que estabelece a resistência mínima para ensaios específicos com este tipo de cimento conforme Tabela 03 Aglomerantes 21 Tabela 03 Resistência mínima para ensaios específicos Idade Resistência Mínima 1 dia 14 MPa 3 dias 24 MPa 7 dias 34 MPa Fonte NBR 5733 Cimento Resistente a Sulfatos RS De acordo com a ABCP qualquer dos cimentos já estudados pode ser resistente a sulfatos desde que se enquadre em alguns requisitos como teor do componente químico C3A do clínquer inferior a 8 e teor de adições carbonáticas de no máximo 5 Os cimentos do tipo altoforno também podem ser resistentes a sulfatos quando contiverem entre 60 e 70 de escória granulada de altoforno em massa Os cimentos do tipo pozolânico que contiverem entre 25 e 40 de material pozolânico em massa também apresentam comportamento satisfatório quando expostos à ação de águas sulfatadas O cimento resistente a sulfatos é recomendado para uso em redes de esgotos de águas servidas ou industriais água do mar e em alguns tipos de solos ambientes onde este agente agressivo pode estar presente Cimento Aluminoso Resulta do cozimento de uma mistura de bauxita e calcário De acordo com Oliveira 2008 este tipo de cimento possui pega lenta porém alcança altas resistências em pouco tempo 315 MPa em 2 dias 40 MPa em 28 dias A reação de hidratação é intensa e desenvolve grandes quantidades de calor Sua principal utilização é como cimento refratário resistindo a temperaturas superiores a 1200ºC podendo chegar a 1400C em misturas com agregados convenientemente escolhidos Não é fabricado no Brasil Cimento Branco CPB Possui coloração branca em função das matériasprimas utilizadas na sua fabricação caulim no lugar da argila que possuem baixos teores de óxido de ferro e Aglomerantes 22 manganês Além disso são observadas condições especiais durante o processo de fabricação O cimento branco pode ser do tipo estrutural ou nãoestrutural O CPB estrutural é utilizado em concretos brancos para fins arquitetônicos e é fabricado nas classes de resistência 25 MPa 32 MPa e 40 MPa O CPB não estrutural é utilizado para rejuntamento de azulejos e aplicações não estruturais Em ambos os casos o cimento pode ser associado a pigmentos o que resulta nos concretos coloridos 7 OUTROS AGLOMERANTES Alguns autores classificam os asfaltos como aglomerantes Vamos falar desses materiais de maneira resumida pois a grande maioria das aplicações que necessitam de aglomerantes faz uso dos tipos minerais como o gesso a cal e o cimento Oliveira 2008 define os asfaltos como produtos resultantes de matéria hidrocarbonada de cor preta presente em petróleos crus nos quais se encontra dissolvido por óleos solventes Quando esses óleos são removidos do petróleo cru obtémse o asfalto Segundo o mesmo autor os asfaltos caracterizamse por serem aglomerantes de forte ligação rapidamente adesivos altamente impermeáveis e de longa durabilidade São utilizados principalmente em obras de pavimentação e de impermeabilização entre outras aplicações Segundo Oliveira 2008 os asfaltos podem ser classificados em 3 tipos sendo cada tipo caracterizado da seguinte maneira Cimentos Asfálticos são obtidos a partir dos materiais residuais da destilação do petróleo compostos por asfalto e óleo Sua consistência varia de firme a dura em temperaturas normais devendo ser aquecidos para se tornarem aplicáveis na forma de fluido São classificados segundo a resistência que oferecem à penetração determinada em ensaio específico Asfaltos líquidos são obtidos pela mistura de cimentos asfálticos com óleos asfaltos de cura lenta SC e solventes cura média MC ou rápida RC e são aquecidos em temperaturas inferiores às do cimento asfáltico para o uso São produzidos em diversas variedades e recebem a nomenclatura em função da cura SC MC ou RC e da consistência 0 mais mole a 5 mais firmes Aglomerantes 23 Emulsões asfálticas são misturas líquidas e homogêneas de cimento asfáltico emulsionantes e água com a proporção de água variando de 30 a 45 apresentandose em colorações que variam do marromclaro ao marrom escuro De acordo com Silva 1985 as emulsões são classificadas de acordo com a rapidez em que ocorre a perda de água também chamada de quebra ou ruptura Aglomerantes 24 REFERÊNCIAS BIBLIOGRÁFICAS CALLISTER W D Ciência e Engenharia de Materiais Uma Introdução John Wiley Sons Inc 2002 Associação Brasileira de Cimento Portland Fabricação do cimento Disponível em httpwwwabcporgbrconteudo basicosobrecimentofabricacaofabricacao Acesso em 26 jul 2011 Associação Brasileira de Cimento Portland Tipos de cimento Disponível em httpwwwabcporgbrconteudo basicosobrecimentotiposaversatilidadedo cimentobrasileiro Acesso em 28 jul 2011 Associação Brasileira de Normas Técnicas NBR 5732 Cimento Portland comum Rio de Janeiro 1991 Associação Brasileira de Normas Técnicas NBR 5733 Cimento Portland de alta resistência inicial Rio de Janeiro 1991 Associação Brasileira de Normas Técnicas NBR 5735 Cimento Portland de altoforno Rio de Janeiro 1991 Associação Brasileira de Normas Técnicas NBR 5736 Cimento Portland pozolânico Rio de Janeiro 1991 Associação Brasileira de Normas Técnicas NBR 7215 Cimento Portland determinação da resistência à compressão Rio de Janeiro 1996 Associação Brasileira de Normas Técnicas NBR 11578 Cimento Portland composto especificação Rio de Janeiro 1991 Associação Brasileira de Normas Técnicas NBR 12989 Cimento Portland branco especificação Rio de Janeiro 1993 OLIVEIRA HM Aglomerantes In BAUER LFA Org Materiais de Construção I 5 ed Rio de Janeiro LTC 2008 p 11 34 OLIVEIRA HM Cimento Portland In BAUER LFA Org Materiais de Construção I 5 ed Rio de Janeiro LTC 2008 p 35 62 PETRUCCI E G R Materiais de Construção Porto Alegre Globo 1975 SILVA Moema Ribas Materiais de Construção São Paulo PINI 1985