·
Cursos Gerais ·
Gestão da Qualidade
Envie sua pergunta para a IA e receba a resposta na hora
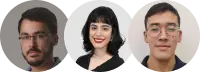
Prefere sua atividade resolvida por um tutor especialista?
- Receba resolvida até o seu prazo
- Converse com o tutor pelo chat
- Garantia de 7 dias contra erros
Recomendado para você
4
Qualidade de Produtos e Serviços
Gestão da Qualidade
UMG
6
Prova 2 Gestao da Qualidade de Produtos e Processos
Gestão da Qualidade
UMG
2
Discursiva Gestão da Qualidade
Gestão da Qualidade
UMG
5
Prova - Gestão de Qualidade - Anhanguera
Gestão da Qualidade
UMG
27
Sst - Semana 8
Gestão da Qualidade
UMG
6
Qualidades em Produtos e Serviços 1
Gestão da Qualidade
UMG
4
Qualidade de Produtos e Serviços
Gestão da Qualidade
UMG
5
Sst - Semana 4
Gestão da Qualidade
UMG
13
Ap1 Exercicio Gestão de Produção e Qualidade
Gestão da Qualidade
UMG
11
Gestao de Qualidade e Competitividade
Gestão da Qualidade
UMG
Texto de pré-visualização
4 Reliability-centred Maintenance As the wise use of our development and production assets provides us with the means to acquire more assets, they must be kept working effec- tively at all times. When premature failures do occur, they must be well understood and prevented whenever possible. Recent articles and infor- mation from forward thinking sources state that, ‘industry spends approx- imately one-third of its annual maintenance budget on unnecessary or improperly scheduled maintenance’ and they cite examples where . . . 68% of the advanced maintenance techniques which were recom- mended were not performed properly . . . and now everyone is at the top of the J-curve.1* 2 My greatest fear (and greatest opportunities) as we research and examine many of our industries is based on my experiences in developing maintenance pro- grams that address the ‘Great Divide’.2 Because the operating age of many assets has led to the unfortunate development of the proprietary or protective maintenance ‘shell’, it has caused most maintenance depart- ments to develop ‘blind spots’ to reliability, safety, and productivity to a point where they are not consciously aware they even exist. As taught in the reliability-centered maintenance class, assets do fail in stages, and failures can often be anticipated and identified. This is the first step of getting priority work accomplished. Thirdly, ‘the degree of job skill, training, and aptitude an operator or tradesman possesses’ is directly related to the amount of knowledge he or she possesses. This corresponds to effectivel ess and utilization effectiveness knowledge needed to accomplish First Generator - Second Generation Equipment maintenance tasks safely, profitably, and reliably. Effective leadership development is held in the ‘virtuous’ curve. Creating the 1: Introduction to Reliability-centred Maintenance The ever-developing task of maintaining our assets before they breakdown efficiently, and cost effective- ly, is represented by generational application of maintenance methods used by maintenance departments in a number of dif- ferent fields. Figure 1.3 shows how the six main concepts of maintenance evolve.3 The developments follow the need to increase equipment performance and optimize the plant’s pro- ductive capabilities during each generation. The concepts are broken down into a series of time periods - illustrated by Ever-improving generations on equipment failure .. First Generation Maintenance 1940 .. 1960 .. 1985 .. First Generation Solidiaed Progress 1930 .. 1975 .. 1980 .. Improved Reliability and Availability 1990 .. 2000 Second Generation 1960 Maintenance techniques 1920 Third Generation 1950 .. 1985 Major New Developments 1960 • Afwayr and Dnvineigatory ties • Technology PdwefMjant • Safety standards And safety Hasardous Successes Thier Generation Improvements • Emergence of Further Global Progressive Standards Continuity of risk control Technology such as condition monitoring As described earlier: A maintenance department does no longer serve a function in isol- ated difficulty. • Therefore, the overall responsibility for the maintenance of the facility, equipment and the process lies with a number of people, that is, with many departments including research and development at all levels. • The task of offering real challenges a nd rewards in the world of engineering, a new breed of contract gives a new outlook. From both the engineers and maintenance managers’ points of view, the challenges facing the maintenance team offer an excellent oppor- tunity to get the whole organization involved. The live project development approach has some added difficulties but beneficial elements: It gives all others power to ‘ comment on the - The general consensus is that the importance of maintenance is increasing - mainly because the costs associated with the absence of maintenance have increased over the last decade or so. The time being spent on development is special today. • Furthermore, the rational way of thinking about maintenance is being replaced by a great degree of personal commitment to reliability and mainte- nance. • Depending on whether it is an autonomous problem or a continuously monitored activity, Serious people find it useful to address the causes and frequency of problems. We may work with the same contract and basic priorities, as improvements offer a managed approach to qualified specialists within the facilities. The general difficulties, by all accounts, finance is one of major problems that this field faces, as it affects the success of keeping essential assets functioning smoothly. The training and experience of maintenance managers and engineers among the experts of the developing nations ensures that a variety of challenges are facilitated. The sharing of equipment is now a serious expression of the mutual cooperation worldwide. In the face of such conditions Therefore, all new processes and techniques within the area of maintenance require active support and cooperation, of all the people involved. viii Reliability-centered Maintenance 5.4 Operational consequences 103 5.5 CM consequences 106 5.6 Economic consequences 107 6 Protective Maintenance 1: Preventive Tasks 109 6.1 Condition-based maintenance 110 6.2 Age-related and random failure patterns 117 6.3 Age-related preventive maintenance 118 6.4 Scheduled discard and scheduled restoration tasks 124 6.5 Scheduled field task 126 6.6 Statistical law and age-related failures 129 7 Protective Maintenance 2: Predictive Tasks 144 7.1 Conditions-based maintenance 145 7.2 The 'P-to-F' interval 149 7.3 Identifying the condition of components 150 7.4 Other condition-based preventive tasks 151 7.5 An overall view 155 7.6 When preventive tasks are worth doing 156 7.7 Conducting other tasks 159 8 Scheduled Actions: Failure-finding Tasks 167 8.1 Reliability as a science 168 8.2 Failure-finding tasks 170 8.3.1 Practical details 171 8.3.2 Mathematical basis 173 8.3.3 When schedules make sense. Other related maintenance tasks 183 9.1 Redesign 184 9.2 No scheduled maintenance 185 10 The RCM (Reliability-centered Maintenance) Decision Diagram 10.1 The RCM decision process and tasks 193 10.2 Other considerations 196 10.3 Components and RCM worksheet x Contents ix 11 Implementing RCM Recommendations 212 11.1 The rules of the RCM task selection process 212 11.2 Updating data 214 11.3 The RCM analysis audit trails 215 11.4 Tasks into schedules 217 11.5 RCM computer and control systems 218 11.6 Manpower 222 12 Achieving Consistency and Failure Data Analysis 12.1 RCM management and control 235 12.2 Using earlier history data 236 12.3 Common failure data 237 Appendices Appendix 1A Summary of Contents Appendix 2 Component Failure Rates and Unconditioning Tasks 305 Bibliography 333 Glossary 335 436 256 308 323 434 413 Preface Humanity continues to depend on more intensive effort to meet the world's pressing needs. Whereas, for decades, efforts to obtain greater output from vocational, industrial, agricultural, and real estate assets at acceptable cost have relied initially almost exclusively on the use of technology, we find today advanced methods of professional observation and management of physical Mass Production and Manufacturing Amalgamated Relationship-centered Maintenance has been the most intense development of emerging disciplines over the post world war period. In 1978, the first technically credible analysis of the RCM methodology was published in industry. MSG-3, a latest structured system, has been in development over subsequent years led by Stanley Nowlan, a NOAA statistician until 1989, and independently by the FAA. The resulting innovation of application boundary RCM has led us to considerably reduce uncertainties in industries where technology reliability must be November 1990, see the development of RCM2 for industries other than Preface xii Reliability-centered Maintenance The first editions of this book, published in the UK in 1991 and the USA in 1992, helped thousands of people around the world to become acquainted with Reliability-centred Maintenance (RCM). We are delighted to note that, as a result, it has rapidly established itself as the most cost effective way for any industry to achieve the maximum maintenance effectiveness. I hope this book will enable readers to use the methodology to achieve the same results in the following years. It will remain essentially unaltered in its overall framework, but several new developments bring it up to date, as follows: The introduction in Chapters 4 and 5 of the overall performance of the assets. Introducing a more comprehensive role of risk management A program on how to establish acceptable levels of risk in Chapters 5 and 7. For the practical purposes of asset managers, an interpretation of Compliance obligations. A full analysis highlighting the detailed methodologies of RCM3 Chapters 10 include a full elements understanding of dual failure modes and treatment of procedures for the most frequently plied RCM2 procedures. Lecternsmith, September 1997. JOHN MOUBRAY Preface xiii The book is intended for engineers, production and operations managers, and anyone else who seeks to maximize the effectiveness and reliability of physical assets. It offers a comprehensive, practical, and technically sound introduction to RCM for those facing such developments of engineering. While its principal aim is to turn around objectively set performance targets in the age of continuous improvement, each chapter has significantly emphasized the financial, environmental goals, with analyzing what RCM offers. In short, the book's aim is to equip the readers with RCM's three key questions and reference failure criteria accepted in the industry. It includes a concise introduction introducing how to achieve fully all elements related to compliant standards. Appendix 3 agreements with revised material on RCM implementation strategies in Chapter 15. Acknowledgements It has only been possible to write this book (and the first edition which was published in 1997) with the help of a great many friends and colleagues. We had just started publishing both software and books based on the RCM methodology when I was asked by Bloomsbury to undertake this project. EPROM is Ireland’s highest placed graduate of the BEd (Hons) Technical Writing degree. In addition to this, she has worked with numerous other companies and probably gotten even better feedback. Many of her early colleagues are still with us and we will always support you guys no matter what. Assistance also came from Harry Kennedy, executive director of the British Computer Society, and Trust Williams, feedback director of the RCM training section of Aer Lingus. A big professional contribution came from Terry Hunter, who is head of the RCM Training and Certification Program. Thanks are also due to Dereck Comter for persevering with me for above five years and Frank MacDonald for his daily encouragement and technical advice. Special thanks must go to Alan Carrington, Mark Deakin and Alan MacKenzie. Sincere thanks must also go to my family for creating an environment where I have found time to write the book and the schedules required. My children who came to many places where professional commitments demanded. In the course of writing this, I have visited the RCM2 operations of numerous great organizations worldwide. Particular thanks go to the British Airways, BP, Nissan Motor Manufacturing, British Telecom, Namibian Broadcasting Corporation, British Airways, British Gas, British Petroleum, Brown and Root, Protonseng John Forutars and Mobileys, RCM stuck projects include many individuals whose help made both editions possible, notably Terry Hunter and his staff at the RCM2 Division. Special thanks must be extended to Mike and Shirley Wood as well as several individuals who have contributed valuable theoretical and practical input. These include Pat Paterson, Pat O’Connell, John Metcalfe, Neil Moulder, Alan Derham, NCF, Blake Mathewson, Grenada’s Energy Generation Company, Dick Smith, Cathy Hicks, Alan Wells and Craig Lambert. These individuals also continue to give of their time and resources generously and selflessly. Andrew Delgrief, George Grace Constable, Tony Bostock, National Power of Catalysts, Kevin Wredeian and Malcolm Regster of the Royal Navy. 1 Introduction to Reliability-centred Maintenance 1.1 The Changing World of Maintenance Over the past sixty years, the role and importance of maintenance has changed out of all recognition. The earliest flying machines were maintained by their pilots. These pioneers relied heavily on human skill and as painlessly as possible. Thanks to the improvements in their engines, chassis, wing and fuselage, they started to rely on highly complex devices and automatic features. The same cannot be said as firmly about those in the chemical plants and refiners. The transformation here was conducted and still is in extremely rudimentary terms and levels of reliability. However, it has an enormous impact on the world. The lasting impact therefore remains on agriculture and the chemicals industries, and the products that we use today affect everyday life. These same companies include major oil companies, chemical plants and refiners, and aircraft manufacturers. But gradual changes continued to take place throughout the industrial spectrum. These all once again saw dramatic changes and decrees over both technology and organizational change, not only on the management systems which were operating in their plants though. Maintenance must now be thought of as an integral part of the total cost of ownership of any physical asset. The importance of adequate physical assets, therefore, cannot be lightly dismissed. Pressure from marketing people and banking shareholders everywhere also cannot be ignored. Competitors everywhere are often searching for, and sometimes finding, better ways of making money. We plan to look at all these elements of RCM (reliability-centred maintenance) in the course of this book. This book is for anyone involved in maintenance, whether solely or partly, in order to understand and preferably increase what we call reliability and require excellent and skilled professional service. This has become a job that corporations conduct as part of their total life cycle costs and takes into account the importance of customer and employer express needs. Reliability-centred Maintenance 2 Since the 1930s, the continuing maintenance can be reckoned against time, where RCM may usually be viewed in perspective as three Generations. These can be broken down into: The First Generation The First Generation usually picked up World War II. It had always been traditional to force time-ons, replacements for stock items, potentially erroneous replacements if an inventory was therefore available. The Second Generation This characterized immediately after World War II. War experiences had clearly showed that the measures in place during World War II with older enemy prospects of potentially different enemies and possibly new opponents. The Third Generation Strict commercial operating requirements were growing exponentially. The physical assets with both capital and labor costs are supporting loads and advances in technology usually reflected where competitive capability or going into educational intuition or New expectations Introduction to Reliability-centred Maintenance Figure 1.1 shows how expectations of maintenance have evolved. Growing expectations of maintenance Key Date What happened and when 1940 Everything 1950 Most people begin reliability 1960 Long overhauls begin 1980 Factored zero hour 2000 Growing consciousness
Envie sua pergunta para a IA e receba a resposta na hora
Recomendado para você
4
Qualidade de Produtos e Serviços
Gestão da Qualidade
UMG
6
Prova 2 Gestao da Qualidade de Produtos e Processos
Gestão da Qualidade
UMG
2
Discursiva Gestão da Qualidade
Gestão da Qualidade
UMG
5
Prova - Gestão de Qualidade - Anhanguera
Gestão da Qualidade
UMG
27
Sst - Semana 8
Gestão da Qualidade
UMG
6
Qualidades em Produtos e Serviços 1
Gestão da Qualidade
UMG
4
Qualidade de Produtos e Serviços
Gestão da Qualidade
UMG
5
Sst - Semana 4
Gestão da Qualidade
UMG
13
Ap1 Exercicio Gestão de Produção e Qualidade
Gestão da Qualidade
UMG
11
Gestao de Qualidade e Competitividade
Gestão da Qualidade
UMG
Texto de pré-visualização
4 Reliability-centred Maintenance As the wise use of our development and production assets provides us with the means to acquire more assets, they must be kept working effec- tively at all times. When premature failures do occur, they must be well understood and prevented whenever possible. Recent articles and infor- mation from forward thinking sources state that, ‘industry spends approx- imately one-third of its annual maintenance budget on unnecessary or improperly scheduled maintenance’ and they cite examples where . . . 68% of the advanced maintenance techniques which were recom- mended were not performed properly . . . and now everyone is at the top of the J-curve.1* 2 My greatest fear (and greatest opportunities) as we research and examine many of our industries is based on my experiences in developing maintenance pro- grams that address the ‘Great Divide’.2 Because the operating age of many assets has led to the unfortunate development of the proprietary or protective maintenance ‘shell’, it has caused most maintenance depart- ments to develop ‘blind spots’ to reliability, safety, and productivity to a point where they are not consciously aware they even exist. As taught in the reliability-centered maintenance class, assets do fail in stages, and failures can often be anticipated and identified. This is the first step of getting priority work accomplished. Thirdly, ‘the degree of job skill, training, and aptitude an operator or tradesman possesses’ is directly related to the amount of knowledge he or she possesses. This corresponds to effectivel ess and utilization effectiveness knowledge needed to accomplish First Generator - Second Generation Equipment maintenance tasks safely, profitably, and reliably. Effective leadership development is held in the ‘virtuous’ curve. Creating the 1: Introduction to Reliability-centred Maintenance The ever-developing task of maintaining our assets before they breakdown efficiently, and cost effective- ly, is represented by generational application of maintenance methods used by maintenance departments in a number of dif- ferent fields. Figure 1.3 shows how the six main concepts of maintenance evolve.3 The developments follow the need to increase equipment performance and optimize the plant’s pro- ductive capabilities during each generation. The concepts are broken down into a series of time periods - illustrated by Ever-improving generations on equipment failure .. First Generation Maintenance 1940 .. 1960 .. 1985 .. First Generation Solidiaed Progress 1930 .. 1975 .. 1980 .. Improved Reliability and Availability 1990 .. 2000 Second Generation 1960 Maintenance techniques 1920 Third Generation 1950 .. 1985 Major New Developments 1960 • Afwayr and Dnvineigatory ties • Technology PdwefMjant • Safety standards And safety Hasardous Successes Thier Generation Improvements • Emergence of Further Global Progressive Standards Continuity of risk control Technology such as condition monitoring As described earlier: A maintenance department does no longer serve a function in isol- ated difficulty. • Therefore, the overall responsibility for the maintenance of the facility, equipment and the process lies with a number of people, that is, with many departments including research and development at all levels. • The task of offering real challenges a nd rewards in the world of engineering, a new breed of contract gives a new outlook. From both the engineers and maintenance managers’ points of view, the challenges facing the maintenance team offer an excellent oppor- tunity to get the whole organization involved. The live project development approach has some added difficulties but beneficial elements: It gives all others power to ‘ comment on the - The general consensus is that the importance of maintenance is increasing - mainly because the costs associated with the absence of maintenance have increased over the last decade or so. The time being spent on development is special today. • Furthermore, the rational way of thinking about maintenance is being replaced by a great degree of personal commitment to reliability and mainte- nance. • Depending on whether it is an autonomous problem or a continuously monitored activity, Serious people find it useful to address the causes and frequency of problems. We may work with the same contract and basic priorities, as improvements offer a managed approach to qualified specialists within the facilities. The general difficulties, by all accounts, finance is one of major problems that this field faces, as it affects the success of keeping essential assets functioning smoothly. The training and experience of maintenance managers and engineers among the experts of the developing nations ensures that a variety of challenges are facilitated. The sharing of equipment is now a serious expression of the mutual cooperation worldwide. In the face of such conditions Therefore, all new processes and techniques within the area of maintenance require active support and cooperation, of all the people involved. viii Reliability-centered Maintenance 5.4 Operational consequences 103 5.5 CM consequences 106 5.6 Economic consequences 107 6 Protective Maintenance 1: Preventive Tasks 109 6.1 Condition-based maintenance 110 6.2 Age-related and random failure patterns 117 6.3 Age-related preventive maintenance 118 6.4 Scheduled discard and scheduled restoration tasks 124 6.5 Scheduled field task 126 6.6 Statistical law and age-related failures 129 7 Protective Maintenance 2: Predictive Tasks 144 7.1 Conditions-based maintenance 145 7.2 The 'P-to-F' interval 149 7.3 Identifying the condition of components 150 7.4 Other condition-based preventive tasks 151 7.5 An overall view 155 7.6 When preventive tasks are worth doing 156 7.7 Conducting other tasks 159 8 Scheduled Actions: Failure-finding Tasks 167 8.1 Reliability as a science 168 8.2 Failure-finding tasks 170 8.3.1 Practical details 171 8.3.2 Mathematical basis 173 8.3.3 When schedules make sense. Other related maintenance tasks 183 9.1 Redesign 184 9.2 No scheduled maintenance 185 10 The RCM (Reliability-centered Maintenance) Decision Diagram 10.1 The RCM decision process and tasks 193 10.2 Other considerations 196 10.3 Components and RCM worksheet x Contents ix 11 Implementing RCM Recommendations 212 11.1 The rules of the RCM task selection process 212 11.2 Updating data 214 11.3 The RCM analysis audit trails 215 11.4 Tasks into schedules 217 11.5 RCM computer and control systems 218 11.6 Manpower 222 12 Achieving Consistency and Failure Data Analysis 12.1 RCM management and control 235 12.2 Using earlier history data 236 12.3 Common failure data 237 Appendices Appendix 1A Summary of Contents Appendix 2 Component Failure Rates and Unconditioning Tasks 305 Bibliography 333 Glossary 335 436 256 308 323 434 413 Preface Humanity continues to depend on more intensive effort to meet the world's pressing needs. Whereas, for decades, efforts to obtain greater output from vocational, industrial, agricultural, and real estate assets at acceptable cost have relied initially almost exclusively on the use of technology, we find today advanced methods of professional observation and management of physical Mass Production and Manufacturing Amalgamated Relationship-centered Maintenance has been the most intense development of emerging disciplines over the post world war period. In 1978, the first technically credible analysis of the RCM methodology was published in industry. MSG-3, a latest structured system, has been in development over subsequent years led by Stanley Nowlan, a NOAA statistician until 1989, and independently by the FAA. The resulting innovation of application boundary RCM has led us to considerably reduce uncertainties in industries where technology reliability must be November 1990, see the development of RCM2 for industries other than Preface xii Reliability-centered Maintenance The first editions of this book, published in the UK in 1991 and the USA in 1992, helped thousands of people around the world to become acquainted with Reliability-centred Maintenance (RCM). We are delighted to note that, as a result, it has rapidly established itself as the most cost effective way for any industry to achieve the maximum maintenance effectiveness. I hope this book will enable readers to use the methodology to achieve the same results in the following years. It will remain essentially unaltered in its overall framework, but several new developments bring it up to date, as follows: The introduction in Chapters 4 and 5 of the overall performance of the assets. Introducing a more comprehensive role of risk management A program on how to establish acceptable levels of risk in Chapters 5 and 7. For the practical purposes of asset managers, an interpretation of Compliance obligations. A full analysis highlighting the detailed methodologies of RCM3 Chapters 10 include a full elements understanding of dual failure modes and treatment of procedures for the most frequently plied RCM2 procedures. Lecternsmith, September 1997. JOHN MOUBRAY Preface xiii The book is intended for engineers, production and operations managers, and anyone else who seeks to maximize the effectiveness and reliability of physical assets. It offers a comprehensive, practical, and technically sound introduction to RCM for those facing such developments of engineering. While its principal aim is to turn around objectively set performance targets in the age of continuous improvement, each chapter has significantly emphasized the financial, environmental goals, with analyzing what RCM offers. In short, the book's aim is to equip the readers with RCM's three key questions and reference failure criteria accepted in the industry. It includes a concise introduction introducing how to achieve fully all elements related to compliant standards. Appendix 3 agreements with revised material on RCM implementation strategies in Chapter 15. Acknowledgements It has only been possible to write this book (and the first edition which was published in 1997) with the help of a great many friends and colleagues. We had just started publishing both software and books based on the RCM methodology when I was asked by Bloomsbury to undertake this project. EPROM is Ireland’s highest placed graduate of the BEd (Hons) Technical Writing degree. In addition to this, she has worked with numerous other companies and probably gotten even better feedback. Many of her early colleagues are still with us and we will always support you guys no matter what. Assistance also came from Harry Kennedy, executive director of the British Computer Society, and Trust Williams, feedback director of the RCM training section of Aer Lingus. A big professional contribution came from Terry Hunter, who is head of the RCM Training and Certification Program. Thanks are also due to Dereck Comter for persevering with me for above five years and Frank MacDonald for his daily encouragement and technical advice. Special thanks must go to Alan Carrington, Mark Deakin and Alan MacKenzie. Sincere thanks must also go to my family for creating an environment where I have found time to write the book and the schedules required. My children who came to many places where professional commitments demanded. In the course of writing this, I have visited the RCM2 operations of numerous great organizations worldwide. Particular thanks go to the British Airways, BP, Nissan Motor Manufacturing, British Telecom, Namibian Broadcasting Corporation, British Airways, British Gas, British Petroleum, Brown and Root, Protonseng John Forutars and Mobileys, RCM stuck projects include many individuals whose help made both editions possible, notably Terry Hunter and his staff at the RCM2 Division. Special thanks must be extended to Mike and Shirley Wood as well as several individuals who have contributed valuable theoretical and practical input. These include Pat Paterson, Pat O’Connell, John Metcalfe, Neil Moulder, Alan Derham, NCF, Blake Mathewson, Grenada’s Energy Generation Company, Dick Smith, Cathy Hicks, Alan Wells and Craig Lambert. These individuals also continue to give of their time and resources generously and selflessly. Andrew Delgrief, George Grace Constable, Tony Bostock, National Power of Catalysts, Kevin Wredeian and Malcolm Regster of the Royal Navy. 1 Introduction to Reliability-centred Maintenance 1.1 The Changing World of Maintenance Over the past sixty years, the role and importance of maintenance has changed out of all recognition. The earliest flying machines were maintained by their pilots. These pioneers relied heavily on human skill and as painlessly as possible. Thanks to the improvements in their engines, chassis, wing and fuselage, they started to rely on highly complex devices and automatic features. The same cannot be said as firmly about those in the chemical plants and refiners. The transformation here was conducted and still is in extremely rudimentary terms and levels of reliability. However, it has an enormous impact on the world. The lasting impact therefore remains on agriculture and the chemicals industries, and the products that we use today affect everyday life. These same companies include major oil companies, chemical plants and refiners, and aircraft manufacturers. But gradual changes continued to take place throughout the industrial spectrum. These all once again saw dramatic changes and decrees over both technology and organizational change, not only on the management systems which were operating in their plants though. Maintenance must now be thought of as an integral part of the total cost of ownership of any physical asset. The importance of adequate physical assets, therefore, cannot be lightly dismissed. Pressure from marketing people and banking shareholders everywhere also cannot be ignored. Competitors everywhere are often searching for, and sometimes finding, better ways of making money. We plan to look at all these elements of RCM (reliability-centred maintenance) in the course of this book. This book is for anyone involved in maintenance, whether solely or partly, in order to understand and preferably increase what we call reliability and require excellent and skilled professional service. This has become a job that corporations conduct as part of their total life cycle costs and takes into account the importance of customer and employer express needs. Reliability-centred Maintenance 2 Since the 1930s, the continuing maintenance can be reckoned against time, where RCM may usually be viewed in perspective as three Generations. These can be broken down into: The First Generation The First Generation usually picked up World War II. It had always been traditional to force time-ons, replacements for stock items, potentially erroneous replacements if an inventory was therefore available. The Second Generation This characterized immediately after World War II. War experiences had clearly showed that the measures in place during World War II with older enemy prospects of potentially different enemies and possibly new opponents. The Third Generation Strict commercial operating requirements were growing exponentially. The physical assets with both capital and labor costs are supporting loads and advances in technology usually reflected where competitive capability or going into educational intuition or New expectations Introduction to Reliability-centred Maintenance Figure 1.1 shows how expectations of maintenance have evolved. Growing expectations of maintenance Key Date What happened and when 1940 Everything 1950 Most people begin reliability 1960 Long overhauls begin 1980 Factored zero hour 2000 Growing consciousness