·
Cursos Gerais ·
Modelagem de Sistemas Mecânicos
Envie sua pergunta para a IA e receba a resposta na hora
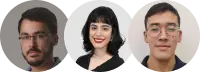
Prefere sua atividade resolvida por um tutor especialista?
- Receba resolvida até o seu prazo
- Converse com o tutor pelo chat
- Garantia de 7 dias contra erros
Recomendado para você
20
Introdução aos Sistemas Mecânicos e Projetos de Transmissão
Modelagem de Sistemas Mecânicos
UNISA
18
Dimensionamento de Eixos: Análise de Materiais e Esforços Mecânicos
Modelagem de Sistemas Mecânicos
UNISA
158
Introdução aos Sistemas Mecânicos e Dimensionamento
Modelagem de Sistemas Mecânicos
UNISA
15
Conceitos no Dimensionamento de Sistemas Mecânicos
Modelagem de Sistemas Mecânicos
UNISA
2
Avaliação Contínua - Folha de Resposta
Modelagem de Sistemas Mecânicos
UNISA
1
Estudo do Controle de Velocidade em Motores de Corrente Continua
Modelagem de Sistemas Mecânicos
UNISA
3
Avaliação Integrada AVI - Detalhes e Questões
Modelagem de Sistemas Mecânicos
UNISA
7
Modelagem e Simulação Dinâmica de Manipulador Robótico Planar
Modelagem de Sistemas Mecânicos
UFRB
246
Modelagem e Simulação de Sistemas
Modelagem de Sistemas Mecânicos
UNISALESIANO
6
Aproximação Linear de Modelos Não Lineares
Modelagem de Sistemas Mecânicos
FEI
Texto de pré-visualização
SISTEMAS MECÂNICOS José Francisco de Barros Júnior 2 4 CONCEITOS EM ENGRENAGENS CILÍNDRICAS DE DENTES RETOS ECDR Neste Bloco serão apresentados os principais conceitos de uma engrenagem item selecionado dentre uma extensa gama de elementos de máquinas que é utilizada no conjunto de um sistema mecânico Ao considerar o objetivo de aprendizagem foi selecionado o elemento de uma Engrenagem Cilíndrica de Dentes Retos ECDR assim serão apresentados os conceitos de suas aplicações a seleção de materiais que irá compor a engrenagem o processo de fabricação selecionado e suas especificações desde a geometria até todas as dimensões que por meio do memorial de cálculo que será definido comporá o projeto mecânico que ao final terá a resistência da engrenagem com os diversos esforços das cargas mecânicas e suportará sem fadigar e sofrer redução de vida útil 41 CARACTERÍSTICAS FUNDAMENTAIS DAS ENGRENAGENS DO MODELO ECDR As engrenagens são elementos de transmissão largamente utilizados em projeto de máquinas pois tem vantagens em sua utilização em sistemas mecânicos razão de transmissão constante relação potênciapeso elevados custo baixo em grandes produções rendimento elevado e sua variedade de formas de transmissão Veja a seguir os critérios fundamentais das Engrenagens Fabricação de engrenagens Qualidade das engrenagens Características gerais Tipos de engrenagens Engrenagens cilíndricas de dentes retos Características geométricas Dimensionamento 3 411 Processos de Fabricação de Engrenagens Os processos de fabricação de engrenagens podem ser realizados por a Usinagem b Fundição c Sem retirada de cavaco Veja a seguir como funciona cada processo A usinagem de engrenagens pode ser A usinagem por geração que utiliza fresas caracol conforme a Figura 41 Engrenagem de corte conforme a Figura 42 ou de Cremalheira de corte conforme a Figura 43 Sendo que entre os 3 processos pelo método de usinagem o mais utilizado na indústria é o de Engrenagem de corte Figura 42 a Usinagem de engrenagens Figura 41 Usinagem por fresa caracol Fonte ANDRADE SD 4 Figura 42 Usinagem por engrenagem de corte Fonte ANDRADE SD Figura 43 Usinagem por cremalheira de corte Fonte SHIGLEY 2011 Figura 44 Usinagem por fresa módulo Fonte ANDRADE SD 5 b Fundição de engrenagens A fabricação de engrenagens por fundição utiliza processos por gravidade demonstrado na Figura 5a sob pressão na Figura 5b ou em casca na Figura 5c que são apresentados a seguir A Figura 45 a a seguir nos apresenta de forma detalhada as etapas do processo de fabricação de engrenagens pelo método de Fundição por gravidade em que se inicia a etapa de fabricação nos seus moldes fixomóvel Começando pelos moldes fixo e móvel passando pelo cadinho com metal fundente que por gravidade energia potencial preenche os moldes para que ao final tenhamos nossa engrenagem Após este processo há apenas uma etapa de lixamento para que atenda aos dimensionais geométricos Figura 45 a Processo de fabricação das engrenagens pelo método de Fundição Ciclo do Processo de Fundição por gravidade Fonte Adaptado de KIMINAME CASTRO OLIVEIRA SD 6 A Figura 45 b a seguir nos apresenta o processo de fabricação de engrenagens pelo método sob pressão em que se inicia a etapa de fabricação nos seus moldes fixomóvel Começando pelos moldes fixo e móvel passando pelo sistema de pistão para a injeção de material fundente que por pressão finaliza o preenchimento dos moldes e ao final teremos a nossa engrenagem Após este processo há uma etapa de lixamento para que atenda aos dimensionais geométricos Figura 45 b Processo de fabricação das engrenagens pelo método de Fundição Ciclo do Processo sob pressão Fonte Adaptado de KIMINAME CASTRO OLIVEIRA SD A Figura 45 c a seguir nos apresenta o processo de fabricação de engrenagens pelo método em casca em que se inicia a etapa de fabricação nos seus moldes fixomóvel Começando pelo molde fixo e molde móvel em casca passando metal fundente na caixa basculada antes de ser inserida no forno térmico para que ao final tenhamos nossa engrenagem 7 Figura 45 c Processo de fabricação das engrenagens pelo método de Fundição Ciclo do Processo de Fundição em casca Fonte Adaptado de KIMINAME CASTRO OLIVEIRA SD c Sem retirada de cavaco Esse processo é dividido em dois subgrupos estampagem e forjamento O processo de estampagem ocorre por meio da pressão aplicada entre a matéria prima e o seu molde matriz para assim ser obtida a engrenagem Já o forjamento é classificado entre os processos de extrusão e trefilação laminação forjamento em matriz conforme Figura 46 8 Figura 46 Processo de fabricação de engrenagens pelo método sem retirada de cavaco Processo Forjamento Fonte Adaptado de KIMINAME CASTRO OLIVEIRA SD 412 Qualidade das Engrenagens O conceito de qualidade das engrenagens ocorre por meio das Normas DIN 862 e 867 que especifica as 12 principais características de qualidade Qualidade 1 Atualmente não utilizada pode ser usada quando não há uma referência da aplicação desta Engrenagem Qualidade 2 São utilizadas em indústria de precisão Relojoaria e aparelhos de precisão Qualidade 3 São utilizadas como padrão em laboratórios de controle Assim são consideradas engrenagens de precisão Qualidade 4 Utilizase na fabricação de engrenagens padrão engrenagens para aviação e engrenagens de alta precisão para torres de radar Qualidade 5 São utilizadas em aviões máquina operatrizes instrumentos de medida turbinas etc Qualidade 6 Utilizase em automóveis ônibus caminhões navios e mecanismo de alta rotação Qualidade 7 Engrenagens Sheivadas são empregadas em veículos máquinas operatrizes máquinas de levantamento e transporte etc Qualidade 8 e 9 São as mais empregadas pois não precisam ser retificadas Utilizamse em máquinas gerais 9 Qualidade 10 a 12 São engrenagens mais rústicas normalmente utilizadas em máquinas agrícolas Desta forma podese concluir que das 12 principais características de qualidade a Qualidade 1 é utilizada para aplicações com elevada precisão e segue até a Qualidade 12 cuja aplicação será mais rústica por exemplo em máquinas agrícolas moinhos de moagem de cana de açúcar etc 413 Aplicação Tipos e a Geometria de Engrenagens Cilíndricas de Dentes Retos ECDR Algo fundamental a saber é que os principais critérios e condições de aplicação de engrenagens estão descritas na norma DIN 862 e 867 que referencia os critérios de Geometria Conforme a engrenagem Figura 47 e também especificam o grau de qualidade materiais de fabricação quais processos de fabricação podem ser utilizados e por fim as dimensões que terá a engrenagem que será projetada para atender aos requisitos de resistência em condições de diversos esforços mecânicos e assim aumentar a sua vida útil Figura 47 Características geométricas conforme DIN 862 e 867 Neste acoplamento entre as engrenagens vemos a engrenagem de diâmetro maior Coroa e a de diâmetro menor Pinhão Fonte SHIGLEY 2011 10 Para facilitar a sequência de projeto iremos apresentar três tipos de nomenclaturas para as formas de acoplamento durante a transmissão de energia de uma ECDR 1 Engrenagens externas Em que a energia mecânica de transmissão gerada e seu acoplamento ocorrem de forma Externa conforme Figura 48 a Figura 48 a Exemplo do tipo de Engrenagem Cilíndrica de Dente Reto ECDR com engrenamento externo Fonte MELCONIAN 2011 2 Engrenagens internas em que a energia mecânica de transmissão gerada e seu acoplamento ocorrem de forma Interna conforme Figura 48 b Figura 48 b Exemplo do tipo de Engrenagem Cilíndrica de Dente Reto ECDR com engrenamento interno Fonte MELCONIAN 2011 3 Pinhão e cremalheira que geram a energia mecânica de transmissão e seu acoplamento também ocorre de forma Externa conforme Figura 48 c 11 Figura 48 c Exemplo do tipo de Engrenagem Cilíndrica de Dente Reto ECDR Pinhão e cremalheira Fonte MELCONIAN 2011 Os elementos mecânicos em análise neste Bloco são as Engrenagens Cilíndricas de Dentes Retos ECDR que serão dimensionadas conforme DIN 862 e 867 normas que ditam a geometria de cada elemento mecânico como as engrenagens Estas podem ter a geometria variada e por consequência diferentes referencias de nomenclatura e pontos de dimensões obtidos através do cálculo de projeto Esse cálculo tem como objetivo definir a propriedade mecânica de sua ruptura e tempo de duração da vida útil que dependem do tipo e horas diárias de funcionamento como você poderá ver mais à frente na Tabela AGMA 𝝋 Abaixo na Figura 49 serão apresentadas as cotas dos diâmetros principais de acordo com as normas DIN 862 e 867 12 Figura 4 9 Diâmetros principais de uma ECDR Fonte SHIGLEY 2011 Diâmetros principais Diâmetro primitivo 𝑑0 𝑚 𝑍 Diâmetro de base 𝑑𝑔 𝑑0 𝑐𝑜𝑠 𝛼 Diâmetro interno pé dente 𝑑𝑓 𝑑0 2 ℎ𝑓 Diâmetro externo cabeça do dente 𝑑𝑘 𝑑0 2 ℎ𝑘 Para determinar os diâmetros principais suas características geométricas e seus valores dimensionais de acordo com a Norma DIN 862 e 867 você verá na Tabela 41 as principais equações que deverão ser consideradas pelo projetista no Memorial de Cálculo do Projeto de um Sistema Mecânico que neste caso será a Engrenagem Cilíndricas de Dentes Retos ECDR 13 Tabela 41 Equações que determinam os valores que compõe a geometria de uma Engrenagem Cilíndrica de Dentes Retos ECRD Fonte MELCONIAN 2011 De acordo com as Normas DIN 862 e 867 a Figura 410 apresenta as terminologias utilizadas nas características geométricas de uma ECDR Número de dentes Z 𝑍 𝑑0 𝑚 Módulo m m t0 𝜋 Diâmetro primitivo 𝑑0 𝑑0 𝑚 𝑍 Diâmetro de base 𝑑𝑔 𝑑𝑔 𝑑0 𝑐𝑜𝑠𝛼0 Passo 𝑡0 𝑡0 𝑚 𝜋 Espessura do dente no primitivo 𝑆0 𝑡0 2 folga nula no flanco Altura comum do dente ℎ 2 𝑚 Altura da cabeça do dente ℎ𝑘 𝑚 Altura total do dente ℎ𝑧 22 𝑚 Altura do pé do dente ℎ𝑓 12 m Vão entre os dentes no primitivo 𝑙0 𝑡0 2 folga nula no flanco Ângulo de pressão 𝛼0 20 145 𝑜𝑢 25 Folga da cabeça 𝑆𝐾 02 𝑚 Relação da transmissão 𝑖 𝑍2 𝑍1 𝑑02 𝑑01 𝑛1 𝑛2 Largura do dente b 9m 𝑏 14m Distância entre centros 𝐶𝑐 𝑑01 𝑑02 2 14 Figura 410 Terminologias utilizadas nas Engrenagens Cilíndricas de Dentes Retos ECDR Fonte SHIGLEY 2011 42 DIMENSIONAMENTO DE ENGRENAGENS CILÍNDRICAS DE DENTES RETOS ECDR Neste item serão apresentadas as principais equações que serão utilizadas no dimensionamento de uma ECDR para atender ao limite e à aplicação deste elemento mecânico ao ser solicitada em um projeto Etapa 1 Dimensionamento com o Critério de desgaste As etapas de um projeto de um elemento mecânico engrenagens de dentes retos seguem dessa maneira Veja a seguinte expressão que deve ser utilizada no dimensionamento de pinhões com ângulo de pressão 20 e número de dentes de 18 a 40 Material utilizado na fabricação Material aço 𝑏1𝑑01 2 572 105 𝑀𝑡 𝑝2 𝑎𝑑𝑚 𝑖 1 𝑖 014 𝜑 Sendo que há 2 condições nesta expressão de Volume da base do dente 15 í𝑛𝑑𝑖𝑐𝑒 𝑒𝑛𝑔𝑟𝑒𝑛𝑎𝑔𝑒𝑛𝑠 𝑒𝑥𝑡𝑒𝑟𝑛𝑎𝑠 í𝑛𝑑𝑖𝑐𝑒 𝑒𝑛𝑔𝑟𝑒𝑛𝑎𝑔𝑒𝑛𝑠 𝑖𝑛𝑡𝑒𝑟𝑛𝑎𝑠 𝑜𝑢 𝑝𝑙𝑎𝑛𝑒𝑡á𝑟𝑖𝑎𝑠 Ambos os exemplos de Engrenamento Externo ou Interno foram apresentados na Figura 47 Seguem outras variáveis consideradas no cálculo acima b1 Largura do dente do pinhão mm d01 Diâmetro primitivo do pinhão mm MT Momento torçor do pinhão Nmm Padm Pressão admissível de contato Nmm2 𝑖 Relação de transmissão Z2Z1 adimensional 𝜑 Fator de serviço consultar tabela adimensional Etapa 2 Para o Dimensionamento de ECDR Pressão admissível 𝑝𝑎𝑑𝑚𝑖𝑠𝑠í𝑣𝑒𝑙 𝑝𝑎𝑑𝑚 0487 𝐻𝐵 𝑊1 6 𝑁 𝑚𝑚2 No exemplo que vamos aplicar mais à frente no enunciado do Estudo de Caso para Dimensionar uma ECDR serão fornecidos os valores de Dureza Horas de atividade do elemento mecânico e seu Valor de utilização Agma 𝜑 Assim falta o valor do Fator de Durabilidade W Seu cálculo é feito por meio da equação a seguir Fator de durabilidade W 𝑊 60 𝑛𝑝 ℎ 106 16 Em que Np Rotação do pinhão rpm h Duração do par horas HB Dureza Brinell Nmm2 A tabela 42 a seguir apresenta a correlação entre os tipos de material que podem ser utilizados na confecção de uma ECDR e os valores determinados por meio do método de ensaio de dureza Brinell Vale lembrar que não há uma equação de conversão entre os métodos dos Ensaios de Dureza mas existe uma tabela que correlaciona o valor obtido em diferentes métodos utilizados no ensaio A tabela 42 apresenta apenas como referência os Valores de HBrinell Mas para os tipos de aços descritos abaixo deverá ser utilizada a tabela Rockwell C HRc mesmo sendo só como referência Os aços são SAE 4320 SAE 4340 SAE 8620 SAE 8640 e temperados Tabela 42 Tabela de Dureza pelo Método Brinell Material HBRINELL 𝑵 𝒎𝒎𝟐 Aço fundido tipo 2 1700 2500 Aço fundido tipo 𝐵2 1250 1500 Aço SAE 1020 1400 1750 Aço SAE 1040 1800 2300 Aço SAE 1050 2200 2600 Aço SAE 31453150 1900 2300 Aço SAE 4320 2000 4200 Aço SAE 4340 2600 6000 Aço SAE 8620 1700 2700 Aço SAE 8640 2000 6000 Aço fundido cinzento 1200 2400 Aço fundido nodular 1100 1400 Fonte MELCONIAN 2011 17 Já a Tabela 43 apresenta o conceito de determinação dos valores de dureza obtidos nos Ensaios de Dureza Uma importante informação não há uma equação ou uma tabela que ajude a realizar a conversão nos valores do Ensaio de Dureza pois cada valor é associado ao seu ensaio e tem particularidades de carga aplicada O elemento penetrador da superfície e a forma da impressão que será analisada de acordo com o método de ensaio e também com o valor de Dureza Brinnell HB solicitada na equação pode ser encontrada em catálogos ou em certificados de fabricação do lote produzido de Aço ou Ferro Fundido Estes terão as informações de Composição Química e as Propriedades Mecânicas com Tenacidade e sua Dureza conforme exemplo da Tabela 43 Tabela 43 Valores de correlação entre os valores obtidos nos Ensaios de dureza Brinell Resistência 𝑁 𝑚𝑚2 Rockwell Impr mm Carga 30 kN Esfera Dureza HB 𝑁 𝑚𝑚2 Aço carbono HB x 036 C Rc B Rb A Ra Shore Vickers 365 2270 997 29 104 646 39 279 370 2690 969 28 104 641 38 270 375 2620 943 26 103 636 37 263 380 2550 918 25 102 630 37 256 400 2290 824 21 98 608 33 229 Fonte adaptado de MELCONIAN 2011 No cálculo da expressão a seguir temos a relação entre a Largura da engrenagem b e o Diâmetro primitivo d0 e é determinado o valor de b d0 Então para ECDR e para o bom dimensionamento da engrenagem haverá duas condições 1 Engrenagem Biapoiada o valor é b d0 12 Característica as duas extremidades do eixo são apoiadas 2 Engrenagem em Balanço o valor é b d0 075 Característica uma das extremidades do eixo é apoiada 18 Confira como é a representação dessas expressões na figura 411 Figura 411 Representação das duas formas de uma ECDR se apoiar em um eixo Fonte MELCONIAN 2011 Na tabela 44 apresentada a seguir é definido o incremento no módulo após sua obtenção no cálculo do módulo de engrenamento de uma ECDR Este cálculo é usado para a fabricação de engrenagens no processo de fresamento e o módulo da ferramenta será o Módulo da engrenagem somado ao incremento Tabela 44 Correlação entre os valores dos Módulos normalizados DIN 780 e o incremento para a ferramenta de fabricação da engrenagem Módulo mm Incremento mm 03 a 10 010 10 a 40 025 40 a 70 050 70 a 160 100 160 a 240 200 240 a 450 300 450 a 750 500 Fonte adaptado de MELCONIAN 2011 Etapa 3 Esforços de flexão no pé do dente e os Tipos de Esforços gerados Normalmente para projetar escolhemos um critério para o dimensionamento e outro para a verificação No caso de engrenagens dimensionamos pelo desgaste e verificamos pelo critério de tensão no pé do dente Essa deve ser menor que a tensão admissível do material indicado 19 Durante a atividade desta engrenagem em um sistema mecânico de Transmissão de Movimentos Rotativos acontecerão Esforços de Flexão nos Pés dos Dentes da engrenagem ECDR Nas engrenagens cilíndricas de dentes retos ECDR são gerados dois esforços que geram uma Força de Flexão nos Pés dos Dentes da ECDR conforme apresentado na Figura 412 Os esforços são 1 Força tangencial 2 Força radial Figura 412 Representação da interação das forças Tangenciais e Radiais que gera Flexão no Pé dos Dentes de uma ECDR Fonte SHIGLEY 2011 Então as seguintes equações são aplicadas para obter o valor dos Esforços Para o caso de uma Força Tangencial 𝐹𝑡 veja a Figura 413 1 Força tangencial 𝑭𝒕 A carga tangencial Ft é responsável pelo movimento das engrenagens sendo também a carga que origina o momento fletor tendendo por flexão o pé do dente 20 A fórmula tangencial é determinada da seguinte maneira 𝐹𝑡 𝑀𝑡 𝑟0 2𝑀𝑡 𝑑0 raio primitivo 𝑟0 𝑑0 2 Em que Ft força tangencial N MT torque Nmm ro raio primitivo da engrenagem mm do diâmetro da engrenagem mm Figura 413 Força Tangencial aplicada e que gera esforço de Flexão no pé do dente Fonte SHIGLEY 2011 Então para obter o valor da Força Radial 𝐹𝑟 aplicada temos 2 Força radial 𝑭𝒓 A Força Radial atua na direção radial no Pé do Dente de uma engrenagem ECDR É determinada por meio da tangente do ângulo α ângulo de pressão tag 𝛼 𝐹𝑟 𝐹𝑡 Temos Fr Ft tag α 21 Em que Fr carga radial N Ft carga tangencial N α ângulo de pressão graus 3 Força resultante 𝐹r É a resultante Ft e Fr sendo determinada por meio de Pitágoras como segue Em que Fn carga resultante N Fr carga radial N Ft carga tangencial N Ou ainda pelas reações 𝑐𝑜𝑠 𝛼 𝐹𝑡 𝐹𝑛 𝐹𝑛 𝐹𝑡 𝑐𝑜𝑠 𝛼 As cargas radial e resultante serão importantes no dimensionamento de eixos e mancais sendo necessário o seu dimensionamento das engrenagens Etapa 4 Tensão máxima aplicada e a correlação entre a Tensão Material usada na fabricação da ECDR e o valor do esforço de Tensão de flexão no pé do dente A tensão atuante no pé do dente deve ser menor ou igual à tensão admissível do material indicado Veja a seguir fórmula que determina a intensidade da tensão máxima que a engrenagem sofrerá e que seu material de fabricação deverá resistir além de indicar os limites da Propriedades Mecânicas e a sua Vida Útil 𝜎𝑚á𝑥 𝐹𝑡 𝑞 𝜑 𝑏 𝑚𝑛 𝜎𝑚𝑎𝑡𝑒𝑟𝑖𝑎𝑙 22 Em que σ máx Tensão máxima atuante na base do dente Nmm2 𝝈 material Tensão admissível do material Nmm2 Ft Força tangencial N mn Módulo normalizado mm b Largura do dente do pinhão mm ϕ Fator de serviço tabela AGMA adimensional q Fator de forma adimensional Etapa 5 Cálculo do Fator de forma 𝑞 que deverá ser de acordo com o número de dentes entre as engrenagens como por exemplo Coroa e Pinhão com geometria de uma ECDR O fator de forma de engrenagem é obtido em função do número de dentes da engrenagem conforme apresentado na Tabela 45 Tabela 45 Correlação entre os valores do número de dentes e o fator de forma Fonte SHIGLEY 2011 Obs Se o número e dentes for intermediário aos apresentados na Tabela 45 será necessário realizar a operação matemática de interpolação tanto no número de dentes Z quanto no Fator de Forma q 23 Etapa 6 Obtémse nas tabelas a seguir o Valor dos Fatores de Serviço AGMA 𝝋 Este valor será considerado entre 2 condições ou seja 10 ou 24 horas de serviço para então obter o valor dos fatores de serviço AGMA conforme os exemplos apresentados a seguir nas Tabelas 46 e 47 Vale lembra que os valores do Fator de Serviço AGMA ϕ de uma engrenagem ECDR como exemplificados nas Tabelas 46 e 47 ficam sempre à disposição em catálogos de fabricantes de engrenagens ou elementos de máquinas aplicado a um sistema mecânico Tabela 46 Tabelas de fatores de serviço AGMA ϕ Fonte adaptado de MELCONIAN 2011 A Tabela 47 apresenta características fundamentais para o dimensionamento e a correta seleção do valor de acordo com as horas de serviço Esta condição altera a vida útil do projeto de um sistema mecânico Tabela 47 Continuação do exemplo de Tabelas de fatores de serviço AGMA ϕ para o acionamento de motores a explosão e serviços intermitentes Motor Elétrico Motor Elétrico Motores a Explosão Multicilíndricos 10 h 3 h 3 h 10 h 24 h 100 050 100 125 150 125 100 125 150 175 175 150 175 200 225 Fonte adaptado de MELCONIAN 2011 Aplicações Serviço Horas de Atividade 10 h 24 h AGITADORES Líquidos 100 125 Misturadores de polpa 125 150 Semilíquidos de densidade variável 125 150 ALIMENTADORES Alimentadores helicoidais 125 150 Alimentadores recíprocos 175 200 Transportadores esteira e correia 125 150 24 43 TENSÕES ADMISSÍVEIS Neste subtema serão avaliados e determinados os valores máximos de tensão do material para assim poder determinar qual material poderá ser utilizado na fabricação de uma ECDR Veja a seguir a tabela 48 com especificações das tensões admissíveis para os materiais Tabela 48 Tensões ideais para os materiais no dimensionamento de engrenagens MATERIAL Mpa 𝑵 𝒎𝒎𝟐 FoFo cinzento 40 FoFo nodular 80 Aço fundido 90 SAE 10101020 90 SAE 10401050 120 SAE 43204340 170 SAE 86208640 200 Mat Sintético Resinas 35 Fonte adaptado de MELCONIAN 2011 Algumas recomendações são indicadas Recomendação 1 O projeto ideal é aquele em que a tensão atuante no pé do dente está bem próxima da tensão admissível no seu limite inferior Se a tensão atuante estiver acima da tensão admissível 𝝈 a engrenagem pode não suportar a transmissão vindo a romper na base do dente prematuramente Se por outro lado a tensão atuante estiver bem aquém da tensão admissível a engrenagem estará superdimensionada tornandose antieconômica Recomendação 2 Ângulo de pressão 𝛼 Observe o par de dentes apresentado na Figura 414 a seguir 25 Iniciam o contato no ponto A A cinemática do mecanismo faz com que o ponto A descreva a trajetória AB No ponto B termina o contato entre os dentes O segmento de reta AB descrito pela trajetória do ponto de contato e a tangente comum aos diâmetros primitivos das engrenagens define o ângulo da pressão Pela norma DIN 867 recomendase a utilização do ângulo de pressão α 20 Figura 414 Trajetória demonstrada desde seu o início até o fim do contato entre dentes Fonte SHIGLEY 2011 Recomendação 3 A seguir serão apresentadas as Engrenagens com perfil cicloidal e as teorias relacionadas a elas Suas representações podem ser vistas nas figuras 415 416 417 e 418 Aplicações Esse tipo de engrenagem é limitada às construções mecânicas podendo ser encontrada em bombas ventiladores volumétricos relógios e aparelhos de precisão 26 Processos de Fabricação A engrenagem cicloidal é obtida por meio de estampagem trefilação brochamento ou injeção mecânica fina por fresamento ou aplainamento As ferramentas são mais caras pois possuem flancos retos O processo de fabricação por ser mais preciso tornase mais caro Curva Cicloidal Posição inicial Figura 415 Ambas as Figuras representam um contato entre engrenagens com curva cicloidal A curva cicloidal é obtida fazendo rolar o círculo 1 sobre o círculo 2 sem que ocorra escorregamento A trajetória do ponto A no movimento descreve a curva cicloidal Círculo 1 em movimento e Círculo 2 fixo Observe que à medida que o círculo 1 rola sem escorregamento sobre a periferia do círculo 2 o ponto A se desloca para a posição A1 formando o arco A A1 que representa parte da curva cicloidal A parte pontilhada da trajetória do ponto A é a trajetória a ser descrita pelo ponto na sequência do movimento Fonte SHIGLEY 2011 27 Engrenagem curva de envolvente A maioria absoluta das engrenagens utilizadas nas construções mecânicas é constituída de dentadura com perfil envolvente Isso ocorre em virtude de o processo de fabricação ser mais simples resultando em um menor custo Figura 416 Representação de um dente da engrenagem curva de envolvente Fonte SHIGLEY 2011 Para entender a representação da Figura 416 apresentada acima os seguintes pontos têm sua nomenclatura e sua teoria das características geométricas Ponto 1 Corda def é enrolada ao redor do cilindro e mantida esticada Ponto 2 Ponto b na corda é o ponto traçador ou seja a medida que a corda é enrolada e desenrolada ao redor do cilindro esse ponto irá traçar a curva evolvente ac Ponto 3 No ponto b o raio é exatamente a distância be 28 Ponto 4 Raio de curvatura da evolvente é zero em a e um máximo em c Ponto 5 de é normal em relação à evolvente em todos os pontos da intersecção e ao mesmo tempo sempre tangente ao cilindro A Seguindo a sequência de detalhamento das características geométricas para aplicação seguimos com o exemplo da Curva Envolvente e o quanto o início desta curva será considerado sendo apresentado a seguir na Figura 417 Figura 417 Engrenamento com dentadura de perfil evolvente Fonte SHIGLEY 2011 A seguir na Figura 418 temos o exemplo da utilização de uma engrenagem cicloidal com o perfil envolvente comumente utilizado em relógios 29 Figura 418 Perfil do engrenamento cicloidal normalmente utilizado em relógios Fonte SHIGLEY 2011 Vamos Aplicar Exercício Estudo de Caso Dimensionamento de engrenagens ECDR Roteiro para o dimensionamento de um par de engrenagens O pinhão engrenagem menor Item 1 da Figura 419 é o dimensionado pois se ele resistir ao esforço aplicado a coroa engrenagem maior Item 2 da Figura 419 suportará com folga a mesma carga por ser uma engrenagem maior Figura 419 Sistema Mecânico de transmissão de movimento entre pinhão e coroa Ambas são ECDR Fonte MELCONIAN 2011 30 Dimensionamento do pinhão Procedimento 1 Critério de pressão desgaste Para que não haja a ocorrência de uma Fadiga Superficial Crateração conforme Figura 420 deverão ser consideradas no cálculo durante o dimensionamento da engrenagem as seguintes etapas para realizar um bom e seguro projeto de engrenagens É importante lembrar que estamos aprendendo sobre engrenagens cilíndricas de Dentes Retos Figura 420 Ocorrência da Fadiga Superficial denominada de Crateração nos dentes de uma ECDR Fonte ANDRADE SD 11 Torque no pinhão 𝑀𝑇 30 𝜋 𝑃 𝑛 𝑁 𝑚 12 Relação de transmissão i 𝑖 𝑍2 𝑍1 13 Pressão admissível Padm deverá ser calculada conforme apresentado na equação a seguir e como foi visto na Etapa 2 Para o Dimensionamento de ECDR Pressão admissível 𝒑𝒂𝒅𝒎𝒊𝒔𝒔í𝒗𝒆𝒍 Para determinar seu valor deverão ser determinadas as seguintes variáveis Dureza pelo método Brinell e o fator de durabilidade 31 padm 0487 HB W1 6 N mm2 131 Determinar a dureza Para a equação da tensão admissível será utilizado o valor de dureza pelo método Brinell que é obtido conforme exemplificado nas Tabelas 42 e 43 132 Fator de durabilidade W 𝑊 60 𝑛𝑝ℎ 106 Isolando o Fator de Durabilidade W 𝑊 1 6 𝑊 6 𝑊0168 133 Cálculo da pressão admissível Como foi calculado no item 13 deste exercício 𝑝𝑎𝑑𝑚 0487 𝐻𝐵 𝑊 1 6 Poderá ser calculado o valor da Máxima Tensão admissível para o projeto da engrenagem ECDR 134 Fator de serviço ϕ Obtémse na tabela AGMA Representados nas Tabelas 46 e 47 Ex O fator de serviço ϕ para eixo de transmissão e carga uniforme para funcionamento de 10 h diárias é Ao consultar o valor de AGMA à disposição em catálogos de fabricantes de engrenagens ou elementos aplicado a um sistema mecânico ϕ 1 eixo de transmissão carga uniforme 10hdia ϕ 1 tabela AGMA 32 14 Volume mínimo do pinhão Para determina o volume do Pé dos Dentes em engrenagens s ECDR utilizase a seguinte equação b1 d0 2 572 105 MT padm2 i 1 i 014 φ Unidades no Sistema Internacional SI Índice Denominase x o 2 membro da equação Temse então Volume mínimo do pinhão 𝑏1 𝑑0 2 𝑥 15 Módulo do engrenamento O módulo do engrenamento é determinado por meio de 𝑏1 𝑑0 2 𝑥 Eq I Volume mínimo do pinhão 𝑏1 𝑑01 𝑦 𝑏1 𝑦 𝑑01 Eq II Substituindo II em I tem se 𝑦 𝑑0 𝑑01 2 𝑥 𝑑01 3 𝑥 𝑦 𝑑01 𝑥 𝑦 3 O módulo do engrenamento é determinado pela expressão do diâmetro primitivo 𝑑01 𝑚 𝑍1 Assim 33 𝑚 𝑑01 𝑍1 O módulo a ser utilizado será o normalizado mais próximo ao módulo calculado que será obtido por meio da tabela de módulos normalizados DIN780 𝑚𝑛 Módulo normalizado módulo da ferramenta que vai usinar a engrenagem 16 Diâmetro primitivo recalculado Definido o módulo da ferramenta é recalculado o diâmetro primitivo por intermédio de 𝑑01 𝑅 𝑚𝑛 𝑍1 17 Largura do pinhão 𝑏1 𝑥 𝑑01 𝑅 2 2 Critério de resistência à flexão no pé do dente A tensão máxima no pé do dente é expressa por meio de Figura 421 Apresenta a força tangencial aplicada e o esforço gerado no pé do dente Fonte SHIGLEY 2011 Considerando a equação que define a máxima tensão no pé do dente da engrenagem onde também é possível selecionar a melhor matéria prima para produção de uma engrenagem 34 𝜎𝑚á𝑥 𝐹𝑡 𝑞 𝜑 𝑏 𝑚𝑛 𝜎𝑚𝑎𝑡𝑒𝑟𝑖𝑎𝑙 21 Força tangencial FT 𝐹𝑇 2 𝑀𝑇1 𝑑01 2 𝑀𝑇2 𝑑02 𝑁 22 Fator de forma q Obtémse por meio da tabela 45 apresentada anteriormente neste Bloco 23 Módulo normalizado mn Obtémse por meio da tabela 44 24 Largura do pinhão b Mesmo do 18 Largura do pinhão b1 X d01 R 2 25 Por meio da equação da Tensão máxima atuante no pé do dente 𝝈𝒎á𝒙 e o valor da Tensão do Material 𝝈𝒎𝒂𝒕𝒆𝒓𝒊𝒂𝒍 é obtido o valor da largura do Pinhão b Ft q φ σmáx mn σmaterial Vamos Aplicar Para condição de aprendizagem no exercício proposto a seguir estará as informações dos valores das variáveis que serão aplicadas no dimensionamento que nesse bloco será realizado para uma Engrenagem de Dentes Retos ECDR Exercício 1 Dimensionar o par de engrenagens cilíndricas de dentes retos ECDR para que possa atuar com segurança na transmissão especificada em seguida 35 A transmissão será acionada por um motor de P 15 CV 11 kW que atua com uma rotação de 1140 rpm ω 38 πrads O material a ser utilizado é o SAE 4340 A dureza específica é 58 HRC e a duração prevista para 10000h As engrenagens atuarão em eixos de transmissão com carga uniforme com o tempo de serviço máximo de 10h diárias Figura 422 Sistema Mecânico de transmissão de movimento entre pinhão e coroa ambas são ECDR Fonte MELCONIAN 2011 Considere 𝑏1 𝑑01 025 Relação entre a largura e o diâmetro primitivo da engrenagem 𝛼 20 Ângulo de pressão 𝑍1 29 dentes pinhão 𝑍2 110 dentes coroa 11 Torque no pinhão 𝑀𝑇 30 𝜋 𝑃 𝑛 𝑁 𝑚 𝑀𝑇 30 𝜋 11000 1140 𝑁 𝑚 𝑀𝑇 9214 𝑁 𝑚 𝑀𝑇 92141 𝑁 𝑚𝑚 36 12 Relação de transmissão i 𝑖 𝑍2 𝑍1 𝑖 110 29 3793 𝑖 379 13 Pressão admissível 131 Fator de durabilidade W 𝑊 60 𝑛𝑝 ℎ 106 𝑊 60 1140 1 104 106 𝑊 60 1140 1 102 𝑊 684 como 𝑊 1 6 297 132 Cálculo da pressão padm 0487 HB W 1 6 𝑝𝑎𝑑𝑚 0487 6000 297 𝑝𝑎𝑑𝑚 0487 6000 297 𝑝𝑎𝑑𝑚 983838 984 102 𝑁 𝑚𝑚2 A dureza de 58 HRC corresponde a 6000 HB ou seja 6000 Nmm2 14 Fator de serviço ϕ Obtémse na tabela AGMA 37 O fator de serviço ϕ para eixo de transmissão carga uniforme para funcionamento de 10 h diárias é ϕ 1 tabela AGMA 15 Volume mínimo do pinhão 𝑏1 𝑑0 2 572 105 𝑀𝑇 𝑝𝑎𝑑𝑚2 𝑖 1 𝑖 014 𝜑 𝑏1 𝑑0 2 572 105 92140 984 1022 379 1 379 014 1 𝑏1 𝑑0 2 572 105 92140 9842 1022 479 393 1 𝐿𝑒𝑚𝑏𝑟𝑎𝑛𝑑𝑜 𝑎 𝑐𝑜𝑛𝑑𝑖çã𝑜 𝑒𝑥𝑝𝑜𝑛𝑒𝑛𝑐𝑖𝑎𝑙 1022 104 𝑏1 𝑑0 2 66343 𝑚𝑚3 𝑏1 𝑑0 2 66343 104 𝑚𝑚3 16 Módulo de engrenamento 𝑏1 𝑑0 2 66343 𝑚𝑚3 I 𝑏1 𝑑01 025 𝑏1 025 𝑑01 II Substituindo II em I 025 d01 d0 2 66343 mm3 d01 3 66343 025 d01 66343 025 265372 mm3 d01 265372 mm3 3 d01 6426 mm Portanto 38 𝑚 𝑑01 𝑍1 643 29 𝑚 221 𝑚𝑚 Por meio da DIN 780 conforme tabela 47 incremento de 025 fixase o módulo da ferramenta em 𝑚𝑛 225 𝑚𝑚 Módulo normalizado DIN 780 17 Recálculo do diâmetro primitivo do pinhão 𝑑01𝑅 𝑚𝑛 𝑍1 𝑑01𝑅 225 29 𝑑01𝑅 6525 𝑚𝑚 18 Largura do pinhão 𝑏1 𝑑01𝑅 2 66343 𝑏1 66343 𝑑01𝑅 2 66343 65252 𝑏1 16 mm 2 Resistência à flexão no pé do dente 21 Força tangencial FT 𝐹𝑇 2 𝑀𝑇1 𝑑01𝑅 𝑁 𝐹𝑇 2 92140 𝑁𝑚𝑚 6525 𝑚𝑚 𝐹𝑇 285 𝑁 22 Fator de forma q Como Z1 29 dentes encontramos na tabela fator q 30835 39 23 Fator de serviço ϕ Obtémse na tabela AGMA O fator de serviço ϕ para eixo de transmissão carga uniforme para funcionamento de 10 h diárias é Ao consultar o valor de AGMA à disposição em catálogos de fabricantes de engrenagens ou elementos aplicado a um sistema mecânico ϕ 1 eixo de transmissão carga uniforme 10hdia ϕ 1 tabela AGMA 24 Módulo normalizado O mesmo do item 16 de acordo com tabela 46 𝒎𝒏 225 mm DIN 780 25 Largura do pinhão b O mesmo do item 18 𝑏1 16 𝑚𝑚 26 Tensão máxima atuante no pé do dente 𝜎𝑚á𝑥 𝐹𝑡 𝑞 𝜑 𝑏 𝑚𝑛 𝜎𝑚𝑎𝑡𝑒𝑟𝑖𝑎𝑙 𝜎𝑚á𝑥 2825 30835 1 16 225 𝜎𝑚𝑎𝑡𝑒𝑟𝑖𝑎𝑙 𝜎𝑚á𝑥 242 𝑁 𝑚𝑚2 27 Análise do dimensionamento Como a tensão máxima atuante é superior à tensão admissível do material concluise que o pinhão será redimensionado 𝜎4340 170 𝑁 𝑚𝑚2 de acordo com a tabela 48 𝜎𝑚á𝑥 242 𝑁 𝑚𝑚2 𝜎4340 170 𝑁 𝑚𝑚2 40 Com a condição não atendida da Tensão máxima aplicada no pé do dente da engrenagem ECDR o valor da tensão do material inicialmente selecionado não atenderá aos esforços deste elemento mecânico a ECDR Assim o recálculo terá de ser feito com os seguintes itens a serem alterados como sugestão Selecionar outro material exemplo Aço 1020 𝜎1020 300 𝑁 𝑚𝑚2 𝜎4340 170 𝑁 𝑚𝑚2 assim atenderá a solicitação de flexão no pé do dente Alterar Largura do pé do dente b Número de dentes Z ou Diâmetro primitivo da engrenagem 𝑑0 Assim deverá realizar todo o roteiro de cálculo sugerido 28 Redimensionamento do pinhão 281 1ª Hipótese mantémse o módulo e fazse o redimensionamento da largura b utilizando a tensão admissível do material SAE 4340 Como 𝜎4340 170 𝑁 𝑚𝑚2 vem que 𝑏 𝐹𝑡 𝑞 𝜑 𝜎4340 𝑚𝑛 𝑏 2285 30835 1 170 225 𝑏 23 𝑚𝑚 Para esse dimensionamento temos um pinhão com as seguintes características Número de dentes Z1 29 dentes Módulo mn 225 mm Diâmetro primitivo 𝑑01𝑅 6525 𝑚𝑚 Largura 𝑏 23 𝑚𝑚 282 Relação largura b diâmetro primitivo do b1 d01 23 6525 035 41 Portanto b1 d01 035 12 a engrenagem está dentro das especificações 283 2ª hipótese mantémse a largura alterando o módulo da 𝒃𝟏 16 mm engrenagem e consequentemente o diâmetro primitivo e a força tangencial 284 Alterase também o valor do módulo normalizado 𝒎𝒏 275 mm pois a tensão admissível está bem aquém da tensão máxima obtida 285 Diâmetro primitivo d01R Z1 mn d01R 29 275 d01R 7975 mm 286 Força tangencial FT FT 2 MT1 d01R N FT 2 92140 7975 N FT 2310 N 287 Tensão máxima atuante σmáx Ft q φ b1 mn σmáx 2310 30835 1 16 275 σmáx 162 N mm2 288 Análise do dimensionamento Como a 𝜎𝑚á𝑥 162 𝑁 𝑚𝑚2 𝜎4340 170 𝑁 𝑚𝑚2 concluise que a engrenagem está em perfeitas condições de utilização 42 289 Relação entre largura e diâmetro primitivo 𝑏1 𝑑01 16 7975 02 Portanto 𝑏1 𝑑01 02 12 a relação encontrase dentro da especificação indicada Para esse dimensionamento temos um pinhão com as seguintes características Número de dentes 𝑍1 29 dentes Módulo 𝑚𝑛 275 mm Diâmetro primitivo 𝑑01𝑅 7975 𝑚𝑚 Largura 𝑏 16 𝑚𝑚 Conforme apresentado na Tabela 41 temos as equações para determinar os valores das dimensões requerida nas Normas DIN 862 e 867 Já a Tabela 49 a seguir se refere as características geométricas de uma ECDR de acordo com as Normas DIN 862 e 867 43 Tabela 49 Formulário das variáveis fundamentais do projeto de uma ECDR Fonte adaptado de MELCONIAN 2011 A Tabela 410 a seguir é uma continuação da Tabela 49 Tabela 410 continuação Formulário das variáveis fundamentais do projeto de uma ECDR Formulário Pinhão mm Coroa mm Espessura do dente no primitivo folga nula no flanco 𝑆0 𝑡0 2 𝑆0 𝑡0 2 864 2 432 𝑆0 𝑡0 2 864 2 432 Formulário Pinhão mm Coroa mm Módulo normalizado DIN 780 𝑚𝑛 275 𝑚𝑛 275 Passo 𝑡0 𝑡0 𝑚𝑛 𝜋 𝑡0 275 𝜋 864 𝑡0 275 𝜋 864 Vão entre os dentes no primitivo folga nula no flanco 𝑙0 𝑡0 2 𝑙0 864 2 432 𝑙0 864 2 432 Altura da cabeça do dente ℎ𝑘 𝑚𝑛 ℎ𝑘 275 ℎ𝑘 275 Altura comum do dente ℎ𝑓 12 𝑚𝑛 ℎ𝑓 12 275 33 ℎ𝑓 12 275 33 Altura comum do dente ℎ 2 𝑚𝑛 ℎ 2 275 55 ℎ 2 275 55 Altura total do dente ℎ𝑧 22 𝑚𝑛 ℎ𝑧 22 275 605 ℎ𝑧 22 275 605 44 Folga da cabeça 𝑆𝐾 02 𝑚𝑛 𝑆𝐾 02 275 055 𝑆𝐾 02 275 055 Diâmetro primitivo 𝑑0 𝑑0 𝑚𝑛 𝑍 𝑑0 𝑚𝑛 𝑍1 𝑑0 275 29 𝑑0 7975 𝑑0 𝑚𝑛 𝑍2 𝑑0 275 110 𝑑0 3025 Fonte adaptado de MELCONIAN 2011 A Tabela 411 a seguir é uma continuação da Tabela 410 e se refere as características geométricas de uma ECDR de acordo com as Normas DIN 862 e 867 Tabela 411 continuação Formulário das variáveis fundamentais do projeto de uma ECDR Fonte adaptado de MELCONIAN 2011 Formulário Pinhão mm Coroa mm Diâmetro de base 𝑑𝑔 𝑑𝑔 𝑑0 𝑐𝑜𝑠𝛼0 𝑑𝑔1 𝑑01 𝑐𝑜𝑠𝛼0 𝑑𝑔1 7975 𝑐𝑜𝑠 20 𝑑𝑔1 7494 𝑑𝑔2 𝑑02 𝑐𝑜𝑠𝛼0 𝑑𝑔2 3025 𝑐𝑜𝑠 20 𝑑𝑔2 28425 Diâmetro interno 𝑑𝑓 𝑑0 24𝑚𝑛 𝑑𝑓1 𝑑01 24𝑚𝑛 𝑑𝑓1 7975 24 275 𝑑𝑓1 7315 𝑑𝑓2 𝑑02 24𝑚𝑛 𝑑𝑓2 3025 24 275 𝑑𝑓1 2959 Diâmetro externo 𝑑𝑘 𝑑0 2𝑚𝑛 𝑑𝑘1 𝑑01 2𝑚𝑛 𝑑𝑘1 7975 2 275 𝑑𝑘1 8525 𝑑𝑘2 𝑑02 2𝑚𝑛 𝑑𝑘2 3025 2 275 𝑑𝑘2 308 Distância entre centros 𝐶𝑐 𝑑01 𝑑02 2 7975 3025 2 𝐶𝑐 19112 Largura das engrenagens 𝑏1 𝑏2 16 45 Conclusão Neste bloco nós estudamos o vasto universo dos elementos de máquinas Além disso revisamos a disciplina de resistência dos materiais Foi apresentado o elemento engrenagens como referência na aplicação de um Projeto Mecânico frente as etapas que devem ser seguidas abordando a seleção do material o tipo de processo de fabricação utilizado as geometrias e como dimensionar para obter uma Engrenagem Cilíndrica de Dentes Retos ECDR para assim termos o completo Memorial de Cálculo do elemento mecânico em questão e que neste exemplo compõe um Sistema Mecânico Referências Bibliográficas ANDRADE A S Elementos Orgânicos de Máquinas II UFP SD KIMINAMI C S CASTRO W B OLIVEIRA M F Introdução aos processos de fabricação de produtos metálicos São Paulo Blucher 2013 MELCONIAN S Elementos de Máquinas 9ª ed São Paulo Erica 2011 MOTT R L Elementos de máquinas em projetos mecânicos São Paulo 2015 NORTON R L Projetos de Máquinas Uma Abordagem Integrada 4º ed Porto Alegre Bookman 2013 SHIGLEY J E BUDYNAS R G NISBETT J K Elementos de máquinas de Shigley 8ª ed São Paulo AMGH Editora Ltda 2011
Envie sua pergunta para a IA e receba a resposta na hora
Recomendado para você
20
Introdução aos Sistemas Mecânicos e Projetos de Transmissão
Modelagem de Sistemas Mecânicos
UNISA
18
Dimensionamento de Eixos: Análise de Materiais e Esforços Mecânicos
Modelagem de Sistemas Mecânicos
UNISA
158
Introdução aos Sistemas Mecânicos e Dimensionamento
Modelagem de Sistemas Mecânicos
UNISA
15
Conceitos no Dimensionamento de Sistemas Mecânicos
Modelagem de Sistemas Mecânicos
UNISA
2
Avaliação Contínua - Folha de Resposta
Modelagem de Sistemas Mecânicos
UNISA
1
Estudo do Controle de Velocidade em Motores de Corrente Continua
Modelagem de Sistemas Mecânicos
UNISA
3
Avaliação Integrada AVI - Detalhes e Questões
Modelagem de Sistemas Mecânicos
UNISA
7
Modelagem e Simulação Dinâmica de Manipulador Robótico Planar
Modelagem de Sistemas Mecânicos
UFRB
246
Modelagem e Simulação de Sistemas
Modelagem de Sistemas Mecânicos
UNISALESIANO
6
Aproximação Linear de Modelos Não Lineares
Modelagem de Sistemas Mecânicos
FEI
Texto de pré-visualização
SISTEMAS MECÂNICOS José Francisco de Barros Júnior 2 4 CONCEITOS EM ENGRENAGENS CILÍNDRICAS DE DENTES RETOS ECDR Neste Bloco serão apresentados os principais conceitos de uma engrenagem item selecionado dentre uma extensa gama de elementos de máquinas que é utilizada no conjunto de um sistema mecânico Ao considerar o objetivo de aprendizagem foi selecionado o elemento de uma Engrenagem Cilíndrica de Dentes Retos ECDR assim serão apresentados os conceitos de suas aplicações a seleção de materiais que irá compor a engrenagem o processo de fabricação selecionado e suas especificações desde a geometria até todas as dimensões que por meio do memorial de cálculo que será definido comporá o projeto mecânico que ao final terá a resistência da engrenagem com os diversos esforços das cargas mecânicas e suportará sem fadigar e sofrer redução de vida útil 41 CARACTERÍSTICAS FUNDAMENTAIS DAS ENGRENAGENS DO MODELO ECDR As engrenagens são elementos de transmissão largamente utilizados em projeto de máquinas pois tem vantagens em sua utilização em sistemas mecânicos razão de transmissão constante relação potênciapeso elevados custo baixo em grandes produções rendimento elevado e sua variedade de formas de transmissão Veja a seguir os critérios fundamentais das Engrenagens Fabricação de engrenagens Qualidade das engrenagens Características gerais Tipos de engrenagens Engrenagens cilíndricas de dentes retos Características geométricas Dimensionamento 3 411 Processos de Fabricação de Engrenagens Os processos de fabricação de engrenagens podem ser realizados por a Usinagem b Fundição c Sem retirada de cavaco Veja a seguir como funciona cada processo A usinagem de engrenagens pode ser A usinagem por geração que utiliza fresas caracol conforme a Figura 41 Engrenagem de corte conforme a Figura 42 ou de Cremalheira de corte conforme a Figura 43 Sendo que entre os 3 processos pelo método de usinagem o mais utilizado na indústria é o de Engrenagem de corte Figura 42 a Usinagem de engrenagens Figura 41 Usinagem por fresa caracol Fonte ANDRADE SD 4 Figura 42 Usinagem por engrenagem de corte Fonte ANDRADE SD Figura 43 Usinagem por cremalheira de corte Fonte SHIGLEY 2011 Figura 44 Usinagem por fresa módulo Fonte ANDRADE SD 5 b Fundição de engrenagens A fabricação de engrenagens por fundição utiliza processos por gravidade demonstrado na Figura 5a sob pressão na Figura 5b ou em casca na Figura 5c que são apresentados a seguir A Figura 45 a a seguir nos apresenta de forma detalhada as etapas do processo de fabricação de engrenagens pelo método de Fundição por gravidade em que se inicia a etapa de fabricação nos seus moldes fixomóvel Começando pelos moldes fixo e móvel passando pelo cadinho com metal fundente que por gravidade energia potencial preenche os moldes para que ao final tenhamos nossa engrenagem Após este processo há apenas uma etapa de lixamento para que atenda aos dimensionais geométricos Figura 45 a Processo de fabricação das engrenagens pelo método de Fundição Ciclo do Processo de Fundição por gravidade Fonte Adaptado de KIMINAME CASTRO OLIVEIRA SD 6 A Figura 45 b a seguir nos apresenta o processo de fabricação de engrenagens pelo método sob pressão em que se inicia a etapa de fabricação nos seus moldes fixomóvel Começando pelos moldes fixo e móvel passando pelo sistema de pistão para a injeção de material fundente que por pressão finaliza o preenchimento dos moldes e ao final teremos a nossa engrenagem Após este processo há uma etapa de lixamento para que atenda aos dimensionais geométricos Figura 45 b Processo de fabricação das engrenagens pelo método de Fundição Ciclo do Processo sob pressão Fonte Adaptado de KIMINAME CASTRO OLIVEIRA SD A Figura 45 c a seguir nos apresenta o processo de fabricação de engrenagens pelo método em casca em que se inicia a etapa de fabricação nos seus moldes fixomóvel Começando pelo molde fixo e molde móvel em casca passando metal fundente na caixa basculada antes de ser inserida no forno térmico para que ao final tenhamos nossa engrenagem 7 Figura 45 c Processo de fabricação das engrenagens pelo método de Fundição Ciclo do Processo de Fundição em casca Fonte Adaptado de KIMINAME CASTRO OLIVEIRA SD c Sem retirada de cavaco Esse processo é dividido em dois subgrupos estampagem e forjamento O processo de estampagem ocorre por meio da pressão aplicada entre a matéria prima e o seu molde matriz para assim ser obtida a engrenagem Já o forjamento é classificado entre os processos de extrusão e trefilação laminação forjamento em matriz conforme Figura 46 8 Figura 46 Processo de fabricação de engrenagens pelo método sem retirada de cavaco Processo Forjamento Fonte Adaptado de KIMINAME CASTRO OLIVEIRA SD 412 Qualidade das Engrenagens O conceito de qualidade das engrenagens ocorre por meio das Normas DIN 862 e 867 que especifica as 12 principais características de qualidade Qualidade 1 Atualmente não utilizada pode ser usada quando não há uma referência da aplicação desta Engrenagem Qualidade 2 São utilizadas em indústria de precisão Relojoaria e aparelhos de precisão Qualidade 3 São utilizadas como padrão em laboratórios de controle Assim são consideradas engrenagens de precisão Qualidade 4 Utilizase na fabricação de engrenagens padrão engrenagens para aviação e engrenagens de alta precisão para torres de radar Qualidade 5 São utilizadas em aviões máquina operatrizes instrumentos de medida turbinas etc Qualidade 6 Utilizase em automóveis ônibus caminhões navios e mecanismo de alta rotação Qualidade 7 Engrenagens Sheivadas são empregadas em veículos máquinas operatrizes máquinas de levantamento e transporte etc Qualidade 8 e 9 São as mais empregadas pois não precisam ser retificadas Utilizamse em máquinas gerais 9 Qualidade 10 a 12 São engrenagens mais rústicas normalmente utilizadas em máquinas agrícolas Desta forma podese concluir que das 12 principais características de qualidade a Qualidade 1 é utilizada para aplicações com elevada precisão e segue até a Qualidade 12 cuja aplicação será mais rústica por exemplo em máquinas agrícolas moinhos de moagem de cana de açúcar etc 413 Aplicação Tipos e a Geometria de Engrenagens Cilíndricas de Dentes Retos ECDR Algo fundamental a saber é que os principais critérios e condições de aplicação de engrenagens estão descritas na norma DIN 862 e 867 que referencia os critérios de Geometria Conforme a engrenagem Figura 47 e também especificam o grau de qualidade materiais de fabricação quais processos de fabricação podem ser utilizados e por fim as dimensões que terá a engrenagem que será projetada para atender aos requisitos de resistência em condições de diversos esforços mecânicos e assim aumentar a sua vida útil Figura 47 Características geométricas conforme DIN 862 e 867 Neste acoplamento entre as engrenagens vemos a engrenagem de diâmetro maior Coroa e a de diâmetro menor Pinhão Fonte SHIGLEY 2011 10 Para facilitar a sequência de projeto iremos apresentar três tipos de nomenclaturas para as formas de acoplamento durante a transmissão de energia de uma ECDR 1 Engrenagens externas Em que a energia mecânica de transmissão gerada e seu acoplamento ocorrem de forma Externa conforme Figura 48 a Figura 48 a Exemplo do tipo de Engrenagem Cilíndrica de Dente Reto ECDR com engrenamento externo Fonte MELCONIAN 2011 2 Engrenagens internas em que a energia mecânica de transmissão gerada e seu acoplamento ocorrem de forma Interna conforme Figura 48 b Figura 48 b Exemplo do tipo de Engrenagem Cilíndrica de Dente Reto ECDR com engrenamento interno Fonte MELCONIAN 2011 3 Pinhão e cremalheira que geram a energia mecânica de transmissão e seu acoplamento também ocorre de forma Externa conforme Figura 48 c 11 Figura 48 c Exemplo do tipo de Engrenagem Cilíndrica de Dente Reto ECDR Pinhão e cremalheira Fonte MELCONIAN 2011 Os elementos mecânicos em análise neste Bloco são as Engrenagens Cilíndricas de Dentes Retos ECDR que serão dimensionadas conforme DIN 862 e 867 normas que ditam a geometria de cada elemento mecânico como as engrenagens Estas podem ter a geometria variada e por consequência diferentes referencias de nomenclatura e pontos de dimensões obtidos através do cálculo de projeto Esse cálculo tem como objetivo definir a propriedade mecânica de sua ruptura e tempo de duração da vida útil que dependem do tipo e horas diárias de funcionamento como você poderá ver mais à frente na Tabela AGMA 𝝋 Abaixo na Figura 49 serão apresentadas as cotas dos diâmetros principais de acordo com as normas DIN 862 e 867 12 Figura 4 9 Diâmetros principais de uma ECDR Fonte SHIGLEY 2011 Diâmetros principais Diâmetro primitivo 𝑑0 𝑚 𝑍 Diâmetro de base 𝑑𝑔 𝑑0 𝑐𝑜𝑠 𝛼 Diâmetro interno pé dente 𝑑𝑓 𝑑0 2 ℎ𝑓 Diâmetro externo cabeça do dente 𝑑𝑘 𝑑0 2 ℎ𝑘 Para determinar os diâmetros principais suas características geométricas e seus valores dimensionais de acordo com a Norma DIN 862 e 867 você verá na Tabela 41 as principais equações que deverão ser consideradas pelo projetista no Memorial de Cálculo do Projeto de um Sistema Mecânico que neste caso será a Engrenagem Cilíndricas de Dentes Retos ECDR 13 Tabela 41 Equações que determinam os valores que compõe a geometria de uma Engrenagem Cilíndrica de Dentes Retos ECRD Fonte MELCONIAN 2011 De acordo com as Normas DIN 862 e 867 a Figura 410 apresenta as terminologias utilizadas nas características geométricas de uma ECDR Número de dentes Z 𝑍 𝑑0 𝑚 Módulo m m t0 𝜋 Diâmetro primitivo 𝑑0 𝑑0 𝑚 𝑍 Diâmetro de base 𝑑𝑔 𝑑𝑔 𝑑0 𝑐𝑜𝑠𝛼0 Passo 𝑡0 𝑡0 𝑚 𝜋 Espessura do dente no primitivo 𝑆0 𝑡0 2 folga nula no flanco Altura comum do dente ℎ 2 𝑚 Altura da cabeça do dente ℎ𝑘 𝑚 Altura total do dente ℎ𝑧 22 𝑚 Altura do pé do dente ℎ𝑓 12 m Vão entre os dentes no primitivo 𝑙0 𝑡0 2 folga nula no flanco Ângulo de pressão 𝛼0 20 145 𝑜𝑢 25 Folga da cabeça 𝑆𝐾 02 𝑚 Relação da transmissão 𝑖 𝑍2 𝑍1 𝑑02 𝑑01 𝑛1 𝑛2 Largura do dente b 9m 𝑏 14m Distância entre centros 𝐶𝑐 𝑑01 𝑑02 2 14 Figura 410 Terminologias utilizadas nas Engrenagens Cilíndricas de Dentes Retos ECDR Fonte SHIGLEY 2011 42 DIMENSIONAMENTO DE ENGRENAGENS CILÍNDRICAS DE DENTES RETOS ECDR Neste item serão apresentadas as principais equações que serão utilizadas no dimensionamento de uma ECDR para atender ao limite e à aplicação deste elemento mecânico ao ser solicitada em um projeto Etapa 1 Dimensionamento com o Critério de desgaste As etapas de um projeto de um elemento mecânico engrenagens de dentes retos seguem dessa maneira Veja a seguinte expressão que deve ser utilizada no dimensionamento de pinhões com ângulo de pressão 20 e número de dentes de 18 a 40 Material utilizado na fabricação Material aço 𝑏1𝑑01 2 572 105 𝑀𝑡 𝑝2 𝑎𝑑𝑚 𝑖 1 𝑖 014 𝜑 Sendo que há 2 condições nesta expressão de Volume da base do dente 15 í𝑛𝑑𝑖𝑐𝑒 𝑒𝑛𝑔𝑟𝑒𝑛𝑎𝑔𝑒𝑛𝑠 𝑒𝑥𝑡𝑒𝑟𝑛𝑎𝑠 í𝑛𝑑𝑖𝑐𝑒 𝑒𝑛𝑔𝑟𝑒𝑛𝑎𝑔𝑒𝑛𝑠 𝑖𝑛𝑡𝑒𝑟𝑛𝑎𝑠 𝑜𝑢 𝑝𝑙𝑎𝑛𝑒𝑡á𝑟𝑖𝑎𝑠 Ambos os exemplos de Engrenamento Externo ou Interno foram apresentados na Figura 47 Seguem outras variáveis consideradas no cálculo acima b1 Largura do dente do pinhão mm d01 Diâmetro primitivo do pinhão mm MT Momento torçor do pinhão Nmm Padm Pressão admissível de contato Nmm2 𝑖 Relação de transmissão Z2Z1 adimensional 𝜑 Fator de serviço consultar tabela adimensional Etapa 2 Para o Dimensionamento de ECDR Pressão admissível 𝑝𝑎𝑑𝑚𝑖𝑠𝑠í𝑣𝑒𝑙 𝑝𝑎𝑑𝑚 0487 𝐻𝐵 𝑊1 6 𝑁 𝑚𝑚2 No exemplo que vamos aplicar mais à frente no enunciado do Estudo de Caso para Dimensionar uma ECDR serão fornecidos os valores de Dureza Horas de atividade do elemento mecânico e seu Valor de utilização Agma 𝜑 Assim falta o valor do Fator de Durabilidade W Seu cálculo é feito por meio da equação a seguir Fator de durabilidade W 𝑊 60 𝑛𝑝 ℎ 106 16 Em que Np Rotação do pinhão rpm h Duração do par horas HB Dureza Brinell Nmm2 A tabela 42 a seguir apresenta a correlação entre os tipos de material que podem ser utilizados na confecção de uma ECDR e os valores determinados por meio do método de ensaio de dureza Brinell Vale lembrar que não há uma equação de conversão entre os métodos dos Ensaios de Dureza mas existe uma tabela que correlaciona o valor obtido em diferentes métodos utilizados no ensaio A tabela 42 apresenta apenas como referência os Valores de HBrinell Mas para os tipos de aços descritos abaixo deverá ser utilizada a tabela Rockwell C HRc mesmo sendo só como referência Os aços são SAE 4320 SAE 4340 SAE 8620 SAE 8640 e temperados Tabela 42 Tabela de Dureza pelo Método Brinell Material HBRINELL 𝑵 𝒎𝒎𝟐 Aço fundido tipo 2 1700 2500 Aço fundido tipo 𝐵2 1250 1500 Aço SAE 1020 1400 1750 Aço SAE 1040 1800 2300 Aço SAE 1050 2200 2600 Aço SAE 31453150 1900 2300 Aço SAE 4320 2000 4200 Aço SAE 4340 2600 6000 Aço SAE 8620 1700 2700 Aço SAE 8640 2000 6000 Aço fundido cinzento 1200 2400 Aço fundido nodular 1100 1400 Fonte MELCONIAN 2011 17 Já a Tabela 43 apresenta o conceito de determinação dos valores de dureza obtidos nos Ensaios de Dureza Uma importante informação não há uma equação ou uma tabela que ajude a realizar a conversão nos valores do Ensaio de Dureza pois cada valor é associado ao seu ensaio e tem particularidades de carga aplicada O elemento penetrador da superfície e a forma da impressão que será analisada de acordo com o método de ensaio e também com o valor de Dureza Brinnell HB solicitada na equação pode ser encontrada em catálogos ou em certificados de fabricação do lote produzido de Aço ou Ferro Fundido Estes terão as informações de Composição Química e as Propriedades Mecânicas com Tenacidade e sua Dureza conforme exemplo da Tabela 43 Tabela 43 Valores de correlação entre os valores obtidos nos Ensaios de dureza Brinell Resistência 𝑁 𝑚𝑚2 Rockwell Impr mm Carga 30 kN Esfera Dureza HB 𝑁 𝑚𝑚2 Aço carbono HB x 036 C Rc B Rb A Ra Shore Vickers 365 2270 997 29 104 646 39 279 370 2690 969 28 104 641 38 270 375 2620 943 26 103 636 37 263 380 2550 918 25 102 630 37 256 400 2290 824 21 98 608 33 229 Fonte adaptado de MELCONIAN 2011 No cálculo da expressão a seguir temos a relação entre a Largura da engrenagem b e o Diâmetro primitivo d0 e é determinado o valor de b d0 Então para ECDR e para o bom dimensionamento da engrenagem haverá duas condições 1 Engrenagem Biapoiada o valor é b d0 12 Característica as duas extremidades do eixo são apoiadas 2 Engrenagem em Balanço o valor é b d0 075 Característica uma das extremidades do eixo é apoiada 18 Confira como é a representação dessas expressões na figura 411 Figura 411 Representação das duas formas de uma ECDR se apoiar em um eixo Fonte MELCONIAN 2011 Na tabela 44 apresentada a seguir é definido o incremento no módulo após sua obtenção no cálculo do módulo de engrenamento de uma ECDR Este cálculo é usado para a fabricação de engrenagens no processo de fresamento e o módulo da ferramenta será o Módulo da engrenagem somado ao incremento Tabela 44 Correlação entre os valores dos Módulos normalizados DIN 780 e o incremento para a ferramenta de fabricação da engrenagem Módulo mm Incremento mm 03 a 10 010 10 a 40 025 40 a 70 050 70 a 160 100 160 a 240 200 240 a 450 300 450 a 750 500 Fonte adaptado de MELCONIAN 2011 Etapa 3 Esforços de flexão no pé do dente e os Tipos de Esforços gerados Normalmente para projetar escolhemos um critério para o dimensionamento e outro para a verificação No caso de engrenagens dimensionamos pelo desgaste e verificamos pelo critério de tensão no pé do dente Essa deve ser menor que a tensão admissível do material indicado 19 Durante a atividade desta engrenagem em um sistema mecânico de Transmissão de Movimentos Rotativos acontecerão Esforços de Flexão nos Pés dos Dentes da engrenagem ECDR Nas engrenagens cilíndricas de dentes retos ECDR são gerados dois esforços que geram uma Força de Flexão nos Pés dos Dentes da ECDR conforme apresentado na Figura 412 Os esforços são 1 Força tangencial 2 Força radial Figura 412 Representação da interação das forças Tangenciais e Radiais que gera Flexão no Pé dos Dentes de uma ECDR Fonte SHIGLEY 2011 Então as seguintes equações são aplicadas para obter o valor dos Esforços Para o caso de uma Força Tangencial 𝐹𝑡 veja a Figura 413 1 Força tangencial 𝑭𝒕 A carga tangencial Ft é responsável pelo movimento das engrenagens sendo também a carga que origina o momento fletor tendendo por flexão o pé do dente 20 A fórmula tangencial é determinada da seguinte maneira 𝐹𝑡 𝑀𝑡 𝑟0 2𝑀𝑡 𝑑0 raio primitivo 𝑟0 𝑑0 2 Em que Ft força tangencial N MT torque Nmm ro raio primitivo da engrenagem mm do diâmetro da engrenagem mm Figura 413 Força Tangencial aplicada e que gera esforço de Flexão no pé do dente Fonte SHIGLEY 2011 Então para obter o valor da Força Radial 𝐹𝑟 aplicada temos 2 Força radial 𝑭𝒓 A Força Radial atua na direção radial no Pé do Dente de uma engrenagem ECDR É determinada por meio da tangente do ângulo α ângulo de pressão tag 𝛼 𝐹𝑟 𝐹𝑡 Temos Fr Ft tag α 21 Em que Fr carga radial N Ft carga tangencial N α ângulo de pressão graus 3 Força resultante 𝐹r É a resultante Ft e Fr sendo determinada por meio de Pitágoras como segue Em que Fn carga resultante N Fr carga radial N Ft carga tangencial N Ou ainda pelas reações 𝑐𝑜𝑠 𝛼 𝐹𝑡 𝐹𝑛 𝐹𝑛 𝐹𝑡 𝑐𝑜𝑠 𝛼 As cargas radial e resultante serão importantes no dimensionamento de eixos e mancais sendo necessário o seu dimensionamento das engrenagens Etapa 4 Tensão máxima aplicada e a correlação entre a Tensão Material usada na fabricação da ECDR e o valor do esforço de Tensão de flexão no pé do dente A tensão atuante no pé do dente deve ser menor ou igual à tensão admissível do material indicado Veja a seguir fórmula que determina a intensidade da tensão máxima que a engrenagem sofrerá e que seu material de fabricação deverá resistir além de indicar os limites da Propriedades Mecânicas e a sua Vida Útil 𝜎𝑚á𝑥 𝐹𝑡 𝑞 𝜑 𝑏 𝑚𝑛 𝜎𝑚𝑎𝑡𝑒𝑟𝑖𝑎𝑙 22 Em que σ máx Tensão máxima atuante na base do dente Nmm2 𝝈 material Tensão admissível do material Nmm2 Ft Força tangencial N mn Módulo normalizado mm b Largura do dente do pinhão mm ϕ Fator de serviço tabela AGMA adimensional q Fator de forma adimensional Etapa 5 Cálculo do Fator de forma 𝑞 que deverá ser de acordo com o número de dentes entre as engrenagens como por exemplo Coroa e Pinhão com geometria de uma ECDR O fator de forma de engrenagem é obtido em função do número de dentes da engrenagem conforme apresentado na Tabela 45 Tabela 45 Correlação entre os valores do número de dentes e o fator de forma Fonte SHIGLEY 2011 Obs Se o número e dentes for intermediário aos apresentados na Tabela 45 será necessário realizar a operação matemática de interpolação tanto no número de dentes Z quanto no Fator de Forma q 23 Etapa 6 Obtémse nas tabelas a seguir o Valor dos Fatores de Serviço AGMA 𝝋 Este valor será considerado entre 2 condições ou seja 10 ou 24 horas de serviço para então obter o valor dos fatores de serviço AGMA conforme os exemplos apresentados a seguir nas Tabelas 46 e 47 Vale lembra que os valores do Fator de Serviço AGMA ϕ de uma engrenagem ECDR como exemplificados nas Tabelas 46 e 47 ficam sempre à disposição em catálogos de fabricantes de engrenagens ou elementos de máquinas aplicado a um sistema mecânico Tabela 46 Tabelas de fatores de serviço AGMA ϕ Fonte adaptado de MELCONIAN 2011 A Tabela 47 apresenta características fundamentais para o dimensionamento e a correta seleção do valor de acordo com as horas de serviço Esta condição altera a vida útil do projeto de um sistema mecânico Tabela 47 Continuação do exemplo de Tabelas de fatores de serviço AGMA ϕ para o acionamento de motores a explosão e serviços intermitentes Motor Elétrico Motor Elétrico Motores a Explosão Multicilíndricos 10 h 3 h 3 h 10 h 24 h 100 050 100 125 150 125 100 125 150 175 175 150 175 200 225 Fonte adaptado de MELCONIAN 2011 Aplicações Serviço Horas de Atividade 10 h 24 h AGITADORES Líquidos 100 125 Misturadores de polpa 125 150 Semilíquidos de densidade variável 125 150 ALIMENTADORES Alimentadores helicoidais 125 150 Alimentadores recíprocos 175 200 Transportadores esteira e correia 125 150 24 43 TENSÕES ADMISSÍVEIS Neste subtema serão avaliados e determinados os valores máximos de tensão do material para assim poder determinar qual material poderá ser utilizado na fabricação de uma ECDR Veja a seguir a tabela 48 com especificações das tensões admissíveis para os materiais Tabela 48 Tensões ideais para os materiais no dimensionamento de engrenagens MATERIAL Mpa 𝑵 𝒎𝒎𝟐 FoFo cinzento 40 FoFo nodular 80 Aço fundido 90 SAE 10101020 90 SAE 10401050 120 SAE 43204340 170 SAE 86208640 200 Mat Sintético Resinas 35 Fonte adaptado de MELCONIAN 2011 Algumas recomendações são indicadas Recomendação 1 O projeto ideal é aquele em que a tensão atuante no pé do dente está bem próxima da tensão admissível no seu limite inferior Se a tensão atuante estiver acima da tensão admissível 𝝈 a engrenagem pode não suportar a transmissão vindo a romper na base do dente prematuramente Se por outro lado a tensão atuante estiver bem aquém da tensão admissível a engrenagem estará superdimensionada tornandose antieconômica Recomendação 2 Ângulo de pressão 𝛼 Observe o par de dentes apresentado na Figura 414 a seguir 25 Iniciam o contato no ponto A A cinemática do mecanismo faz com que o ponto A descreva a trajetória AB No ponto B termina o contato entre os dentes O segmento de reta AB descrito pela trajetória do ponto de contato e a tangente comum aos diâmetros primitivos das engrenagens define o ângulo da pressão Pela norma DIN 867 recomendase a utilização do ângulo de pressão α 20 Figura 414 Trajetória demonstrada desde seu o início até o fim do contato entre dentes Fonte SHIGLEY 2011 Recomendação 3 A seguir serão apresentadas as Engrenagens com perfil cicloidal e as teorias relacionadas a elas Suas representações podem ser vistas nas figuras 415 416 417 e 418 Aplicações Esse tipo de engrenagem é limitada às construções mecânicas podendo ser encontrada em bombas ventiladores volumétricos relógios e aparelhos de precisão 26 Processos de Fabricação A engrenagem cicloidal é obtida por meio de estampagem trefilação brochamento ou injeção mecânica fina por fresamento ou aplainamento As ferramentas são mais caras pois possuem flancos retos O processo de fabricação por ser mais preciso tornase mais caro Curva Cicloidal Posição inicial Figura 415 Ambas as Figuras representam um contato entre engrenagens com curva cicloidal A curva cicloidal é obtida fazendo rolar o círculo 1 sobre o círculo 2 sem que ocorra escorregamento A trajetória do ponto A no movimento descreve a curva cicloidal Círculo 1 em movimento e Círculo 2 fixo Observe que à medida que o círculo 1 rola sem escorregamento sobre a periferia do círculo 2 o ponto A se desloca para a posição A1 formando o arco A A1 que representa parte da curva cicloidal A parte pontilhada da trajetória do ponto A é a trajetória a ser descrita pelo ponto na sequência do movimento Fonte SHIGLEY 2011 27 Engrenagem curva de envolvente A maioria absoluta das engrenagens utilizadas nas construções mecânicas é constituída de dentadura com perfil envolvente Isso ocorre em virtude de o processo de fabricação ser mais simples resultando em um menor custo Figura 416 Representação de um dente da engrenagem curva de envolvente Fonte SHIGLEY 2011 Para entender a representação da Figura 416 apresentada acima os seguintes pontos têm sua nomenclatura e sua teoria das características geométricas Ponto 1 Corda def é enrolada ao redor do cilindro e mantida esticada Ponto 2 Ponto b na corda é o ponto traçador ou seja a medida que a corda é enrolada e desenrolada ao redor do cilindro esse ponto irá traçar a curva evolvente ac Ponto 3 No ponto b o raio é exatamente a distância be 28 Ponto 4 Raio de curvatura da evolvente é zero em a e um máximo em c Ponto 5 de é normal em relação à evolvente em todos os pontos da intersecção e ao mesmo tempo sempre tangente ao cilindro A Seguindo a sequência de detalhamento das características geométricas para aplicação seguimos com o exemplo da Curva Envolvente e o quanto o início desta curva será considerado sendo apresentado a seguir na Figura 417 Figura 417 Engrenamento com dentadura de perfil evolvente Fonte SHIGLEY 2011 A seguir na Figura 418 temos o exemplo da utilização de uma engrenagem cicloidal com o perfil envolvente comumente utilizado em relógios 29 Figura 418 Perfil do engrenamento cicloidal normalmente utilizado em relógios Fonte SHIGLEY 2011 Vamos Aplicar Exercício Estudo de Caso Dimensionamento de engrenagens ECDR Roteiro para o dimensionamento de um par de engrenagens O pinhão engrenagem menor Item 1 da Figura 419 é o dimensionado pois se ele resistir ao esforço aplicado a coroa engrenagem maior Item 2 da Figura 419 suportará com folga a mesma carga por ser uma engrenagem maior Figura 419 Sistema Mecânico de transmissão de movimento entre pinhão e coroa Ambas são ECDR Fonte MELCONIAN 2011 30 Dimensionamento do pinhão Procedimento 1 Critério de pressão desgaste Para que não haja a ocorrência de uma Fadiga Superficial Crateração conforme Figura 420 deverão ser consideradas no cálculo durante o dimensionamento da engrenagem as seguintes etapas para realizar um bom e seguro projeto de engrenagens É importante lembrar que estamos aprendendo sobre engrenagens cilíndricas de Dentes Retos Figura 420 Ocorrência da Fadiga Superficial denominada de Crateração nos dentes de uma ECDR Fonte ANDRADE SD 11 Torque no pinhão 𝑀𝑇 30 𝜋 𝑃 𝑛 𝑁 𝑚 12 Relação de transmissão i 𝑖 𝑍2 𝑍1 13 Pressão admissível Padm deverá ser calculada conforme apresentado na equação a seguir e como foi visto na Etapa 2 Para o Dimensionamento de ECDR Pressão admissível 𝒑𝒂𝒅𝒎𝒊𝒔𝒔í𝒗𝒆𝒍 Para determinar seu valor deverão ser determinadas as seguintes variáveis Dureza pelo método Brinell e o fator de durabilidade 31 padm 0487 HB W1 6 N mm2 131 Determinar a dureza Para a equação da tensão admissível será utilizado o valor de dureza pelo método Brinell que é obtido conforme exemplificado nas Tabelas 42 e 43 132 Fator de durabilidade W 𝑊 60 𝑛𝑝ℎ 106 Isolando o Fator de Durabilidade W 𝑊 1 6 𝑊 6 𝑊0168 133 Cálculo da pressão admissível Como foi calculado no item 13 deste exercício 𝑝𝑎𝑑𝑚 0487 𝐻𝐵 𝑊 1 6 Poderá ser calculado o valor da Máxima Tensão admissível para o projeto da engrenagem ECDR 134 Fator de serviço ϕ Obtémse na tabela AGMA Representados nas Tabelas 46 e 47 Ex O fator de serviço ϕ para eixo de transmissão e carga uniforme para funcionamento de 10 h diárias é Ao consultar o valor de AGMA à disposição em catálogos de fabricantes de engrenagens ou elementos aplicado a um sistema mecânico ϕ 1 eixo de transmissão carga uniforme 10hdia ϕ 1 tabela AGMA 32 14 Volume mínimo do pinhão Para determina o volume do Pé dos Dentes em engrenagens s ECDR utilizase a seguinte equação b1 d0 2 572 105 MT padm2 i 1 i 014 φ Unidades no Sistema Internacional SI Índice Denominase x o 2 membro da equação Temse então Volume mínimo do pinhão 𝑏1 𝑑0 2 𝑥 15 Módulo do engrenamento O módulo do engrenamento é determinado por meio de 𝑏1 𝑑0 2 𝑥 Eq I Volume mínimo do pinhão 𝑏1 𝑑01 𝑦 𝑏1 𝑦 𝑑01 Eq II Substituindo II em I tem se 𝑦 𝑑0 𝑑01 2 𝑥 𝑑01 3 𝑥 𝑦 𝑑01 𝑥 𝑦 3 O módulo do engrenamento é determinado pela expressão do diâmetro primitivo 𝑑01 𝑚 𝑍1 Assim 33 𝑚 𝑑01 𝑍1 O módulo a ser utilizado será o normalizado mais próximo ao módulo calculado que será obtido por meio da tabela de módulos normalizados DIN780 𝑚𝑛 Módulo normalizado módulo da ferramenta que vai usinar a engrenagem 16 Diâmetro primitivo recalculado Definido o módulo da ferramenta é recalculado o diâmetro primitivo por intermédio de 𝑑01 𝑅 𝑚𝑛 𝑍1 17 Largura do pinhão 𝑏1 𝑥 𝑑01 𝑅 2 2 Critério de resistência à flexão no pé do dente A tensão máxima no pé do dente é expressa por meio de Figura 421 Apresenta a força tangencial aplicada e o esforço gerado no pé do dente Fonte SHIGLEY 2011 Considerando a equação que define a máxima tensão no pé do dente da engrenagem onde também é possível selecionar a melhor matéria prima para produção de uma engrenagem 34 𝜎𝑚á𝑥 𝐹𝑡 𝑞 𝜑 𝑏 𝑚𝑛 𝜎𝑚𝑎𝑡𝑒𝑟𝑖𝑎𝑙 21 Força tangencial FT 𝐹𝑇 2 𝑀𝑇1 𝑑01 2 𝑀𝑇2 𝑑02 𝑁 22 Fator de forma q Obtémse por meio da tabela 45 apresentada anteriormente neste Bloco 23 Módulo normalizado mn Obtémse por meio da tabela 44 24 Largura do pinhão b Mesmo do 18 Largura do pinhão b1 X d01 R 2 25 Por meio da equação da Tensão máxima atuante no pé do dente 𝝈𝒎á𝒙 e o valor da Tensão do Material 𝝈𝒎𝒂𝒕𝒆𝒓𝒊𝒂𝒍 é obtido o valor da largura do Pinhão b Ft q φ σmáx mn σmaterial Vamos Aplicar Para condição de aprendizagem no exercício proposto a seguir estará as informações dos valores das variáveis que serão aplicadas no dimensionamento que nesse bloco será realizado para uma Engrenagem de Dentes Retos ECDR Exercício 1 Dimensionar o par de engrenagens cilíndricas de dentes retos ECDR para que possa atuar com segurança na transmissão especificada em seguida 35 A transmissão será acionada por um motor de P 15 CV 11 kW que atua com uma rotação de 1140 rpm ω 38 πrads O material a ser utilizado é o SAE 4340 A dureza específica é 58 HRC e a duração prevista para 10000h As engrenagens atuarão em eixos de transmissão com carga uniforme com o tempo de serviço máximo de 10h diárias Figura 422 Sistema Mecânico de transmissão de movimento entre pinhão e coroa ambas são ECDR Fonte MELCONIAN 2011 Considere 𝑏1 𝑑01 025 Relação entre a largura e o diâmetro primitivo da engrenagem 𝛼 20 Ângulo de pressão 𝑍1 29 dentes pinhão 𝑍2 110 dentes coroa 11 Torque no pinhão 𝑀𝑇 30 𝜋 𝑃 𝑛 𝑁 𝑚 𝑀𝑇 30 𝜋 11000 1140 𝑁 𝑚 𝑀𝑇 9214 𝑁 𝑚 𝑀𝑇 92141 𝑁 𝑚𝑚 36 12 Relação de transmissão i 𝑖 𝑍2 𝑍1 𝑖 110 29 3793 𝑖 379 13 Pressão admissível 131 Fator de durabilidade W 𝑊 60 𝑛𝑝 ℎ 106 𝑊 60 1140 1 104 106 𝑊 60 1140 1 102 𝑊 684 como 𝑊 1 6 297 132 Cálculo da pressão padm 0487 HB W 1 6 𝑝𝑎𝑑𝑚 0487 6000 297 𝑝𝑎𝑑𝑚 0487 6000 297 𝑝𝑎𝑑𝑚 983838 984 102 𝑁 𝑚𝑚2 A dureza de 58 HRC corresponde a 6000 HB ou seja 6000 Nmm2 14 Fator de serviço ϕ Obtémse na tabela AGMA 37 O fator de serviço ϕ para eixo de transmissão carga uniforme para funcionamento de 10 h diárias é ϕ 1 tabela AGMA 15 Volume mínimo do pinhão 𝑏1 𝑑0 2 572 105 𝑀𝑇 𝑝𝑎𝑑𝑚2 𝑖 1 𝑖 014 𝜑 𝑏1 𝑑0 2 572 105 92140 984 1022 379 1 379 014 1 𝑏1 𝑑0 2 572 105 92140 9842 1022 479 393 1 𝐿𝑒𝑚𝑏𝑟𝑎𝑛𝑑𝑜 𝑎 𝑐𝑜𝑛𝑑𝑖çã𝑜 𝑒𝑥𝑝𝑜𝑛𝑒𝑛𝑐𝑖𝑎𝑙 1022 104 𝑏1 𝑑0 2 66343 𝑚𝑚3 𝑏1 𝑑0 2 66343 104 𝑚𝑚3 16 Módulo de engrenamento 𝑏1 𝑑0 2 66343 𝑚𝑚3 I 𝑏1 𝑑01 025 𝑏1 025 𝑑01 II Substituindo II em I 025 d01 d0 2 66343 mm3 d01 3 66343 025 d01 66343 025 265372 mm3 d01 265372 mm3 3 d01 6426 mm Portanto 38 𝑚 𝑑01 𝑍1 643 29 𝑚 221 𝑚𝑚 Por meio da DIN 780 conforme tabela 47 incremento de 025 fixase o módulo da ferramenta em 𝑚𝑛 225 𝑚𝑚 Módulo normalizado DIN 780 17 Recálculo do diâmetro primitivo do pinhão 𝑑01𝑅 𝑚𝑛 𝑍1 𝑑01𝑅 225 29 𝑑01𝑅 6525 𝑚𝑚 18 Largura do pinhão 𝑏1 𝑑01𝑅 2 66343 𝑏1 66343 𝑑01𝑅 2 66343 65252 𝑏1 16 mm 2 Resistência à flexão no pé do dente 21 Força tangencial FT 𝐹𝑇 2 𝑀𝑇1 𝑑01𝑅 𝑁 𝐹𝑇 2 92140 𝑁𝑚𝑚 6525 𝑚𝑚 𝐹𝑇 285 𝑁 22 Fator de forma q Como Z1 29 dentes encontramos na tabela fator q 30835 39 23 Fator de serviço ϕ Obtémse na tabela AGMA O fator de serviço ϕ para eixo de transmissão carga uniforme para funcionamento de 10 h diárias é Ao consultar o valor de AGMA à disposição em catálogos de fabricantes de engrenagens ou elementos aplicado a um sistema mecânico ϕ 1 eixo de transmissão carga uniforme 10hdia ϕ 1 tabela AGMA 24 Módulo normalizado O mesmo do item 16 de acordo com tabela 46 𝒎𝒏 225 mm DIN 780 25 Largura do pinhão b O mesmo do item 18 𝑏1 16 𝑚𝑚 26 Tensão máxima atuante no pé do dente 𝜎𝑚á𝑥 𝐹𝑡 𝑞 𝜑 𝑏 𝑚𝑛 𝜎𝑚𝑎𝑡𝑒𝑟𝑖𝑎𝑙 𝜎𝑚á𝑥 2825 30835 1 16 225 𝜎𝑚𝑎𝑡𝑒𝑟𝑖𝑎𝑙 𝜎𝑚á𝑥 242 𝑁 𝑚𝑚2 27 Análise do dimensionamento Como a tensão máxima atuante é superior à tensão admissível do material concluise que o pinhão será redimensionado 𝜎4340 170 𝑁 𝑚𝑚2 de acordo com a tabela 48 𝜎𝑚á𝑥 242 𝑁 𝑚𝑚2 𝜎4340 170 𝑁 𝑚𝑚2 40 Com a condição não atendida da Tensão máxima aplicada no pé do dente da engrenagem ECDR o valor da tensão do material inicialmente selecionado não atenderá aos esforços deste elemento mecânico a ECDR Assim o recálculo terá de ser feito com os seguintes itens a serem alterados como sugestão Selecionar outro material exemplo Aço 1020 𝜎1020 300 𝑁 𝑚𝑚2 𝜎4340 170 𝑁 𝑚𝑚2 assim atenderá a solicitação de flexão no pé do dente Alterar Largura do pé do dente b Número de dentes Z ou Diâmetro primitivo da engrenagem 𝑑0 Assim deverá realizar todo o roteiro de cálculo sugerido 28 Redimensionamento do pinhão 281 1ª Hipótese mantémse o módulo e fazse o redimensionamento da largura b utilizando a tensão admissível do material SAE 4340 Como 𝜎4340 170 𝑁 𝑚𝑚2 vem que 𝑏 𝐹𝑡 𝑞 𝜑 𝜎4340 𝑚𝑛 𝑏 2285 30835 1 170 225 𝑏 23 𝑚𝑚 Para esse dimensionamento temos um pinhão com as seguintes características Número de dentes Z1 29 dentes Módulo mn 225 mm Diâmetro primitivo 𝑑01𝑅 6525 𝑚𝑚 Largura 𝑏 23 𝑚𝑚 282 Relação largura b diâmetro primitivo do b1 d01 23 6525 035 41 Portanto b1 d01 035 12 a engrenagem está dentro das especificações 283 2ª hipótese mantémse a largura alterando o módulo da 𝒃𝟏 16 mm engrenagem e consequentemente o diâmetro primitivo e a força tangencial 284 Alterase também o valor do módulo normalizado 𝒎𝒏 275 mm pois a tensão admissível está bem aquém da tensão máxima obtida 285 Diâmetro primitivo d01R Z1 mn d01R 29 275 d01R 7975 mm 286 Força tangencial FT FT 2 MT1 d01R N FT 2 92140 7975 N FT 2310 N 287 Tensão máxima atuante σmáx Ft q φ b1 mn σmáx 2310 30835 1 16 275 σmáx 162 N mm2 288 Análise do dimensionamento Como a 𝜎𝑚á𝑥 162 𝑁 𝑚𝑚2 𝜎4340 170 𝑁 𝑚𝑚2 concluise que a engrenagem está em perfeitas condições de utilização 42 289 Relação entre largura e diâmetro primitivo 𝑏1 𝑑01 16 7975 02 Portanto 𝑏1 𝑑01 02 12 a relação encontrase dentro da especificação indicada Para esse dimensionamento temos um pinhão com as seguintes características Número de dentes 𝑍1 29 dentes Módulo 𝑚𝑛 275 mm Diâmetro primitivo 𝑑01𝑅 7975 𝑚𝑚 Largura 𝑏 16 𝑚𝑚 Conforme apresentado na Tabela 41 temos as equações para determinar os valores das dimensões requerida nas Normas DIN 862 e 867 Já a Tabela 49 a seguir se refere as características geométricas de uma ECDR de acordo com as Normas DIN 862 e 867 43 Tabela 49 Formulário das variáveis fundamentais do projeto de uma ECDR Fonte adaptado de MELCONIAN 2011 A Tabela 410 a seguir é uma continuação da Tabela 49 Tabela 410 continuação Formulário das variáveis fundamentais do projeto de uma ECDR Formulário Pinhão mm Coroa mm Espessura do dente no primitivo folga nula no flanco 𝑆0 𝑡0 2 𝑆0 𝑡0 2 864 2 432 𝑆0 𝑡0 2 864 2 432 Formulário Pinhão mm Coroa mm Módulo normalizado DIN 780 𝑚𝑛 275 𝑚𝑛 275 Passo 𝑡0 𝑡0 𝑚𝑛 𝜋 𝑡0 275 𝜋 864 𝑡0 275 𝜋 864 Vão entre os dentes no primitivo folga nula no flanco 𝑙0 𝑡0 2 𝑙0 864 2 432 𝑙0 864 2 432 Altura da cabeça do dente ℎ𝑘 𝑚𝑛 ℎ𝑘 275 ℎ𝑘 275 Altura comum do dente ℎ𝑓 12 𝑚𝑛 ℎ𝑓 12 275 33 ℎ𝑓 12 275 33 Altura comum do dente ℎ 2 𝑚𝑛 ℎ 2 275 55 ℎ 2 275 55 Altura total do dente ℎ𝑧 22 𝑚𝑛 ℎ𝑧 22 275 605 ℎ𝑧 22 275 605 44 Folga da cabeça 𝑆𝐾 02 𝑚𝑛 𝑆𝐾 02 275 055 𝑆𝐾 02 275 055 Diâmetro primitivo 𝑑0 𝑑0 𝑚𝑛 𝑍 𝑑0 𝑚𝑛 𝑍1 𝑑0 275 29 𝑑0 7975 𝑑0 𝑚𝑛 𝑍2 𝑑0 275 110 𝑑0 3025 Fonte adaptado de MELCONIAN 2011 A Tabela 411 a seguir é uma continuação da Tabela 410 e se refere as características geométricas de uma ECDR de acordo com as Normas DIN 862 e 867 Tabela 411 continuação Formulário das variáveis fundamentais do projeto de uma ECDR Fonte adaptado de MELCONIAN 2011 Formulário Pinhão mm Coroa mm Diâmetro de base 𝑑𝑔 𝑑𝑔 𝑑0 𝑐𝑜𝑠𝛼0 𝑑𝑔1 𝑑01 𝑐𝑜𝑠𝛼0 𝑑𝑔1 7975 𝑐𝑜𝑠 20 𝑑𝑔1 7494 𝑑𝑔2 𝑑02 𝑐𝑜𝑠𝛼0 𝑑𝑔2 3025 𝑐𝑜𝑠 20 𝑑𝑔2 28425 Diâmetro interno 𝑑𝑓 𝑑0 24𝑚𝑛 𝑑𝑓1 𝑑01 24𝑚𝑛 𝑑𝑓1 7975 24 275 𝑑𝑓1 7315 𝑑𝑓2 𝑑02 24𝑚𝑛 𝑑𝑓2 3025 24 275 𝑑𝑓1 2959 Diâmetro externo 𝑑𝑘 𝑑0 2𝑚𝑛 𝑑𝑘1 𝑑01 2𝑚𝑛 𝑑𝑘1 7975 2 275 𝑑𝑘1 8525 𝑑𝑘2 𝑑02 2𝑚𝑛 𝑑𝑘2 3025 2 275 𝑑𝑘2 308 Distância entre centros 𝐶𝑐 𝑑01 𝑑02 2 7975 3025 2 𝐶𝑐 19112 Largura das engrenagens 𝑏1 𝑏2 16 45 Conclusão Neste bloco nós estudamos o vasto universo dos elementos de máquinas Além disso revisamos a disciplina de resistência dos materiais Foi apresentado o elemento engrenagens como referência na aplicação de um Projeto Mecânico frente as etapas que devem ser seguidas abordando a seleção do material o tipo de processo de fabricação utilizado as geometrias e como dimensionar para obter uma Engrenagem Cilíndrica de Dentes Retos ECDR para assim termos o completo Memorial de Cálculo do elemento mecânico em questão e que neste exemplo compõe um Sistema Mecânico Referências Bibliográficas ANDRADE A S Elementos Orgânicos de Máquinas II UFP SD KIMINAMI C S CASTRO W B OLIVEIRA M F Introdução aos processos de fabricação de produtos metálicos São Paulo Blucher 2013 MELCONIAN S Elementos de Máquinas 9ª ed São Paulo Erica 2011 MOTT R L Elementos de máquinas em projetos mecânicos São Paulo 2015 NORTON R L Projetos de Máquinas Uma Abordagem Integrada 4º ed Porto Alegre Bookman 2013 SHIGLEY J E BUDYNAS R G NISBETT J K Elementos de máquinas de Shigley 8ª ed São Paulo AMGH Editora Ltda 2011