·
Cursos Gerais ·
Modelagem de Sistemas Mecânicos
Envie sua pergunta para a IA e receba a resposta na hora
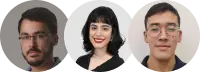
Prefere sua atividade resolvida por um tutor especialista?
- Receba resolvida até o seu prazo
- Converse com o tutor pelo chat
- Garantia de 7 dias contra erros
Recomendado para você
20
Introdução aos Sistemas Mecânicos e Projetos de Transmissão
Modelagem de Sistemas Mecânicos
UNISA
18
Dimensionamento de Eixos: Análise de Materiais e Esforços Mecânicos
Modelagem de Sistemas Mecânicos
UNISA
45
Conceitos em Engrenagens Cilíndricas de Dentes Retos
Modelagem de Sistemas Mecânicos
UNISA
15
Conceitos no Dimensionamento de Sistemas Mecânicos
Modelagem de Sistemas Mecânicos
UNISA
2
Avaliação Contínua - Folha de Resposta
Modelagem de Sistemas Mecânicos
UNISA
1
Estudo do Controle de Velocidade em Motores de Corrente Continua
Modelagem de Sistemas Mecânicos
UNISA
3
Avaliação Integrada AVI - Detalhes e Questões
Modelagem de Sistemas Mecânicos
UNISA
7
Modelagem e Simulação Dinâmica de Manipulador Robótico Planar
Modelagem de Sistemas Mecânicos
UFRB
1
Modificações no Script para Trajetória Curva no Mecanismo Robótico
Modelagem de Sistemas Mecânicos
UCS
17
Modelagem Matemática de Motor CC em Mesa de Coordenadas
Modelagem de Sistemas Mecânicos
ENIAC
Texto de pré-visualização
SISTEMAS MECÂNICOS José Francisco de Barros Júnior 2 SUMÁRIO 1 INTRODUÇÃO AOS SISTEMAS MECÂNICOS 3 2 CONCEITOS NO DIMENSIONAMENTO DE SISTEMAS MECÂNICOS 22 3 CONCEITOS NO DIMENSIONAMENTO DE EIXOS ÁRVORES 36 4 CONCEITOS EM ENGRENAGENS CILÍNDRICAS DE DENTES RETOS ECDR 53 5 CONCEITOS EM ENGRENAGENS CILÍNDRICAS DE DENTES HELICOIDAIS ECDH 97 6 CONCEITOS NOS ELEMENTOS DE ACOPLAMENTO 147 3 1 INTRODUÇÃO AOS SISTEMAS MECÂNICOS Neste Bloco serão apresentadas as grandezas fundamentais da física e da mecânica e sua aplicação prática Esses conhecimentos são necessários para realizar um Projeto Mecânico ou seja a aplicação do elemento ou peça e sua geometria para assim poder dimensionar A disciplina de Sistemas Mecânicos utilizará conceitos apresentados em Resistência dos Materiais e Elementos de Máquinas além de apresentar conceitos novos como a correlação das grandezas fundamentais da Mecânica o Torque o Momento Torçor e a mudança em velocidade e também as transmissões de movimento linear para a circunferencial Com isto serão apresentadas equações para determinar o valor obtido nas velocidades angulares 𝜔 e nas velocidades periféricas 𝜗𝑝 bem como a determinação da unidade da Potência para mensurar o Trabalho mecânico realizado em um sistema 11 Introdução a projetos mecânicos Na disciplina de Sistemas Mecânicos estudaremos a transmissão mecânica por meios rígidos e flexíveis redutores e elementos de união Também conheceremos e aprenderemos a dimensionar a transmissão por engrenagens e correias com a utilização de redutores e elementos de união entre motor e máquina O objetivo principal deste estudo é apresentar a teoria já em suas aplicações reais como por exemplo Transmissão de potência entre motor e máquina Caixas de engrenagens de máquinas operatrizes Veículos aviões embarcações Transporte de materiais correia transportadora 4 Equipamentos de elevação e transporte Entre outros Buscamos também facilitar o entendimento e a elaboração de projetos mecânicos por meio do estudo de Especificações e definições dos meios de transmissão de força Classificação dos elementos de máquinas Transmissão de força por meios rígidos e flexíveis Classificação e aplicação de redutores e elementos de união Dimensionamento e aplicações 12 Torque nas transmissões 121 Torque ou Momento Torçor definido pela Física Por meio de conceitos fundamentais da física definese o Torque ou Momento Torçor como a tendência que uma força tem de rotacionar um corpo sobre o qual ela é aplicada O torque é um vetor perpendicular ao plano formado pelos vetores força e raio de rotação conforme representada na Figura 11 5 Figura 11 Direção dos vetores de Força e distância para realizar um Torque ou Momento Fletor Fonte HELERBROCK SDb Sempre que uma força for aplicada a alguma distância do eixo de rotação de um corpo esse corpo estará sujeito à rotação assim o torque pode ser entendido como o agente dinâmico das rotações Dessa forma ele está para os movimentos de rotação como a força está para os movimentos de translação Se quisermos fazer que um corpo gire em torno de algum ponto devemos exercer um torque sobre ele Veja a seguir alguns exemplos de Torque aplicado em nossa rotina Quando abrimos uma porta aplicamos força em um ponto distante do seu eixo de rotação Desta forma imprimimos sobre ela um torque maior conforme Figura 12 6 Figura 12 A maçaneta de uma porta é aberta pela aplicação de um torque Fonte HELERBROCK SDb Ao usarmos uma chave de boca como na Figura 13 podemos ver o aperto dos parafusos de uma roda de um veículo e utilizando um Torquimetro maior precisão do Torque aplicado é possível perceber que quanto maior for o tamanho da alavanca menor será o esforço necessário para parafusar a roda 7 Figura 13 Aplicação do Torque com um Torquimetro produto da Força aplicada e a dimensão da Ferramenta O torque conforme apresentado nas figuras 11 e 12 e quando há transmissões mecânicas forma de energia é produto de duas grandezas entre a força tangencial FT aplicada com ângulo de atuação de 𝑠𝑒𝑛 𝜃 definido e o raio r da peça O vetor torque pode ser calculado por meio do produto vetorial entre força e distância conforme a figura 14 e a equação a seguir 𝑀𝑇 𝐹𝑇 𝑑 𝑠𝑒𝑛 𝜃 8 Figura 14 Torque aplicado os esforços e a transmissão de movimento Fonte MELCONIAN 2011 Segundo Helerbroock na fórmula apresentada anteriormente θ é o ângulo formado entre o raio de rotação r e a força F No caso em que a força é aplicada com um ângulo de 90º em relação ao raio r o seno do ângulo é igual a 1 O raio r é determinado pela distância do ponto de aplicação até o eixo de rotação do corpo e também é conhecido como braço de alavanca Quanto maior for o braço de alavanca de um corpo mais fácil será rotacionálo E para determinar o módulo do torque pode ser calculado pelo produto da força vezes distância vezes 𝑠𝑒𝑛 do ângulo de 𝜃 Na nossa aplicação em Sistemas Mecânicos θ 90 e a inclinação da Força aplicada em sen θ 1 Considerando uma distância d r raio usualmente para os cálculos de Torque utilizase a equação abaixo 𝑀𝑇 𝐹𝑇 𝑟 Sendo A unidade do torque de acordo com o Sistema Internacional é Newton vezes metro Nm 9 MT Momento Torçor ou Torque Nm FT Força Tangencial N r raio m θ ângulo entre r e F graus Vamos aplicar Exercício 1 O velejador ao identificar a direção do vento gira uma manivela no sentido antihorário Com essa direção o vento tem uma maior eficiência no contato com a superfície da vela e isso gera uma Força F 50 N que é aplicada com ângulo θ de 45º em relação a um braço de alavanca de 025 m Desta forma o velejador poderá aproveitar a maior força aplicada e por um maior tempo Calcule o torque realizado sobre a manivela Dados sen θ ângulo 45º 22 Resolução 𝜏 𝑟 𝐹 𝑠𝑒𝑛𝜃 𝜏 025 50 𝑠𝑒𝑛 45 𝜏 025 50 2 2 𝜏 883 𝑁 𝑚 Exercício 2 A transmissão por correias representada na Figura 15 é composta pela polia motora 1 que possui diâmetro d1 100 mm e a polia movida 2 que possui diâmetro d2240 mm A transmissão é acionada por uma força tangencial Ft 600 N adaptado de MELCONIAN S Determine 1 Torque na polia 1 2 Torque na polia 2 10 Figura 15 Relação entre polias Fonte adaptado de MELCONIAN 2011 Solução Parte 1 Torque na polia 1 Figura 16 Relação da Força Tangencial aplicada em relação a polia 1 Fonte Adaptado de MELCONIAN 2011 𝑀𝑇1 𝐹𝑇 𝑟1 𝑟1 𝑑1 2 100 2 50 mm 50 103 m 𝑀𝑇1 600 𝑁 50 103 m 𝑀𝑇1 30 𝑁 𝑚 11 Parte 2 Torque na polia 2 Figura 17 Relação da Força Tangencial aplicada em relação a polia 2 Fonte Adaptado de MELCONIAN 2011 𝑀𝑇2 𝐹𝑇 𝑟2 𝑟2 𝑑2 2 240 2 120 mm 120 103 m 𝑀𝑇2 600 𝑁 012 𝑚 m 𝑀𝑇2 72 𝑁 𝑚 13 potência 131 A Potência definida pela Física Potência é uma grandeza física usada para calcular a quantidade de energia concedida ou consumida por unidade de tempo Em outras palavras é a taxa de variação da energia em função do tempo Assim a potência é útil para medir a rapidez com a qual uma forma de energia é transformada em outra Em nosso estudo será avaliado o quanto que uma energia mecânica é utilizada para a realização de um trabalho Dizemos que uma máquina é mais potente que as outras quando ela é capaz de realizar a mesma tarefa em um tempo menor ou ainda realizar uma quantidade maior de tarefas no mesmo intervalo de tempo 12 A definição de potência média é dada pelo trabalho realizado em função da variação de tempo P τ t Sendo P Potência média W τ Trabalho J Δt Intervalo de tempo s A unidade de medida da potência adotada pelo SI é o watt W unidade equivalente a joule por segundo Js A unidade watt foi adotada a partir de 1882 como forma de homenagear os trabalhos desenvolvidos por James Watt que foram de extrema relevância para o desenvolvimento das máquinas a vapor Segundo Helerbrock trabalho é a medida da transformação de uma forma de energia em outras formas de energia mediante a aplicação de uma força Sendo assim a definição de potência pode estar relacionada com qualquer forma de energia tais como energia mecânica energia potencial elétrica e energia térmica 132 Cálculo da potência Podemos determinar a potência realizada pela aplicação de uma força F que desloca um corpo de massa m em uma distância d Observe Figura 18 Representação de uma força F que desloca um corpo m em uma distância d Fonte HELERBROCK SDa 13 Na situação descrita acima podemos calcular a potência do movimento por meio da definição de potência média 𝑃 𝜏 𝑡 Para tanto é necessário recordar os Conceitos Fundamentais da Física e que trabalho realizado por um vetor força F conforme Figura 18 pode ser calculado por meio da seguinte fórmula 𝜏 𝐹 𝑑 𝑐𝑜𝑠 𝜃 Legenda F Força aplicada N d Distância percorrida m θ Ângulo formado entre F e d º 𝑡 Variação do Tempo s Reunindo as duas equações anteriores em uma só teremos a seguinte equação para o cálculo da potência relacionada a uma forma de energia qualquer 𝑃 𝐹 𝑑 𝑐𝑜𝑠 𝜃 𝑡 Legenda F Força aplicada N d Distância percorrida m θ Ângulo formado entre F e d º 𝑡 Variação do Tempo s Para os casos em que a força aplicada é paralela à distância percorrida pelo corpo o cosseno do ângulo θ terá seu valor máximo cos 0º 1 Portanto a potência média poderá ser calculada a partir da seguinte relação 𝑃 𝐹 𝑑 1 𝑡 14 mas 𝒅 𝒕 v logo P F v Legenda F Força aplicada N d Distância percorrida m θ Ângulo formado entre F e d º 𝑡 Variação do Tempo s v velocidade do corpo ms Após a dedução realizada acima da equação que relaciona trabalho e potência vemos que é possível calcular a potência como forma de energia que é transformada em um corpo Isso é possível se soubermos o módulo da força resultante que deverá ser multiplicado pela velocidade média percorrida pelo corpo ao longo de um percurso de distância de modulo com um valor d No entanto é necessário lembrar que a definição apresentada acima só é válida para valores constantes de Potência instantânea definida de forma equacionada Potência instantânea é a medida da quantidade de trabalho realizado em um processo durante um intervalo de tempo muito pequeno infinitesimal Podemos dizer portanto que a potência instantânea é a taxa de variação da quantidade de trabalho durante um intervalo de tempo que tende a zero Pinst τ t com t 0 Legenda Pinst Potência instantânea W Δτ Trabalho infinitesimal J Δt Intervalo de tempo infinitesimal s 15 Também temos a Potência instantânea de forma literal em associação direta com o experimento que James Watt realizou na Inglaterra A melhor definição da Potência Instantânea é quando se tem a necessidade de medir a energia de um trabalho em intervalo de tempo menor logo quanto menor o intervalo de tempo mais precisas serão as aferições da potência instantânea Assim para a aplicação de trabalho por um tempo tem a medida do Trabalho ou seja uma Energia Mecânica realizada Então 𝑃 𝑇𝑟𝑎𝑏𝑎𝑙ℎ𝑜 𝑇𝑒𝑚𝑝𝑜 𝜏 𝑡 como 𝜏 𝐹 𝑠 𝑃 𝐹𝑠 𝑡 sendo 𝜗 𝑠 𝑡 Equação da Velocidade logo podemos escrever 𝑃 𝐹𝑇 𝜗𝑝 A unidade da Potência no SI Sistema Internacional de Unidades é 𝑁 𝑚 𝑠 𝐽 𝑠 W Sendo 𝑃 Potência W 𝐹𝑇 Força Tangencial N 𝜗𝑝 Velocidade Periférica 𝑚 𝑠 Como forma de mensurar a Potência no início do século XVIII ao inventar a máquina a vapor James Watt apresenta sua descoberta ao povo inglês Ele faria a relação de quantos Cavalos referência naquele século seriam necessários para realizar o movimento de energia motriz como mostrado na Figura 19 Desta forma sua unidade de Watt W teria a correlação de Energia Mecânica realizada por meio de Cavalos até em sua unidade Cv 16 Figura 19 Representação do experimento de James Watt Fonte adaptado de MELCONIAN 2011 A forma utilizada para demonstrar a Potência é 𝐹 𝑄𝑚𝑎𝑥 76 kgf Carga máxima que o cavalo elevou com a velocidade de 1 𝑚 𝑠 assim resultando em 𝑃 𝐹 𝑣 𝑃 76𝑘𝑔𝑓 1 𝑚 𝑠 𝑃 76 𝑘𝑔𝑓 𝑚 𝑠 considerando 1 𝑘𝑔𝑓 980665𝑁 então 𝑃 76 980665 𝑁𝑚 𝑠 𝑃 7453 𝑁𝑚 𝑠 1𝑊 Da experiência de Watt surgiu o hp horse power vedado no SI Já na França a experiência foi repetida utilizando 𝑄𝑚𝑎𝑥 75 kgf que originou o cv cheval vapeur resultando em 𝑃 𝐹 𝑣 𝑃 75𝑘𝑔𝑓 1 𝑚 𝑠 𝑃 75 𝑘𝑔𝑓 𝑚𝑠 Como 1 𝑘𝑔𝑓 980665𝑁 então 𝑃 75 980665 𝑁𝑚 𝑠 𝑃 7355 𝑁𝑚 𝑠 1𝑊 Desta forma o cv é temporariamente permitido no SI 17 Agora que temos os conceitos de Torque e Potência definidos segue abaixo equações que podem ser aplicadas para determinar os valores de Torque Potência e até Velocidade Angular 𝝎 Considerando 𝑃 𝐹𝑇 𝑣𝑃 1 𝐹𝑇 𝑀𝑇 𝑟 2 𝑣𝑃 𝜔 𝑟 3 Substituindo 2 e 3 em 1 temos 𝑃 𝑀𝑇 𝑟 𝜔 𝑟 P 𝑀𝑇 𝜔 Ou ainda 𝑀𝑇 𝑃 𝜔 Considerando através da velocidade angular 𝜔 𝜋𝑛 30 Temos que 𝑀𝑇 30𝑃 𝜋𝑛 𝑁𝑚 Ou 𝑀𝑇 30000𝑃 𝜋𝑛 𝑁𝑚𝑚 Sendo 𝑃 𝑃𝑜𝑡ê𝑛𝑐𝑖𝑎 𝑊 𝑀𝑇 𝑀𝑜𝑚𝑒𝑛𝑡𝑜 𝑇𝑜𝑟ç𝑜𝑟 𝑁 𝑚 𝑛 𝑅𝑜𝑡𝑎çã𝑜 𝑟𝑝𝑚 𝜔 𝑉𝑒𝑙𝑜𝑐𝑖𝑑𝑎𝑑𝑒 𝑎𝑛𝑔𝑢𝑙𝑎𝑟 𝑟𝑎𝑑 𝑠 18 133 Força tangencial 𝐅𝐓 A força tangencial 𝐅𝐓 pode ser definida como o modulo de uma força que um objeto em movimento circular faz ao movimentarse em direção à tangente do círculo que ele percorre como no exemplo da trajetória circular realizada na Figura 110 A força centrípeta é a força que mantém o objeto na trajetória circular Assim sempre devese associar que o equilíbrio entre a força centrípeta e a força tangencial se obtém da trajetória circular Tendo o valor do módulo da Força Tangencial para se obter o esforço mecânico denominado de Torque devese realizar o produto da Força Tangencial e o raio da trajetória circular conforme representado na Figura 110 Figura 110 Representação da Força Tangencial Torque e Velocidade periférica Fonte adaptado de MELCONIAN 2011 A força tangencial é dada por 𝐹𝑇 𝑀𝑇 𝑟 𝑃 𝑉𝑃 𝑃 𝜔 𝑟 Sendo 𝐹𝑇 Força tangencial N 𝑀𝑇 Torque Nm r Raio do elemento m 19 P Potência W VP Velocidade periférica ms ω Velocidade angular rads Vamos Aplicar Exercício 3 O elevador da figura 111 foi projetado para transportar uma carga máxima Cmax 7000 N 10 pessoas O peso do elevador é Pe 1 kN e o contrapeso possui a mesma carga CP 1 kN Determine a potência do motor M para que o elevador se desloque com Velocidade constante de v 1 m s Figura 111 Representação do Sistema de elevação de carga Fonte MELCONIAN 2011 Solução Fazemos o diagrama de corpo livre deste sistema conforme Figura 112 20 Figura 112 Representação do diagrama de corpo livre do sistema em análise Fonte Adaptado de MELCONIAN 2011 O peso do elevador é compensado pelo do contrapeso logo a única carga a considerar á 𝐶𝑚𝑎𝑥 7000 𝑁 que é a força que atua no cabo Então 𝑃𝑚𝑜𝑡𝑜𝑟 𝐹𝑐𝑎𝑏𝑜 𝑣 𝑃𝑚𝑜𝑡𝑜𝑟 7000 𝑁 1𝑚𝑠 𝐹𝑐𝑎𝑏𝑜 𝐶𝑚á𝑥 Força do Cabo 7000 N 𝑣 𝑉𝑒𝑙𝑜𝑐𝑖𝑑𝑎𝑑𝑒 𝑝𝑒𝑟𝑖𝑓é𝑟𝑖𝑐𝑎 𝑚 𝑠 𝑃𝑚𝑜𝑡𝑜𝑟 7000 W Para obter na unidade em cv devemos dividir por 7355 𝑊𝑐𝑣 Então 𝑃𝑚𝑜𝑡𝑜𝑟 7000 𝑊 7355 𝑊 𝑐𝑣 𝑃𝑚𝑜𝑡𝑜𝑟 95 𝑐𝑣 Conclusão Neste Bloco foram apresentadas as grandezas fundamentais da mecânica e sua aplicação prática apresentando medidas Físicas e Mecânicas que serão fundamentais na descrição geometria e seu dimensionamento que sempre estará envolvido em um projeto de Sistema Mecânico 21 Além disso também foi estudada a correlação existente entre um movimento que realiza uma energia mecânica com um módulo de velocidade linear e se altera para um movimento circular ou seja realiza trajetórias lineares para circunferenciais mas como há mudança direcional de movimento linear para circular será utilizado para determinação da avaliação das velocidades lineares ms e incluemse as velocidades angulares 𝜔 e periféricas 𝜗 ex rads Também foi apresentada a grandeza mecânica do Torque que é o produto entre uma Força e um módulo de distância assim T F d NM resulta no Momento Torçor Dessa forma a trajetória conceitual que foi apresentada servirá como base para aplicar as novas grandezas físicas e mecânicas em projetos que deverão ser realizados em um sistema mecânico REFERÊNCIAS ANDRADE A S Elementos Orgânicos de Máquinas II UFP SD HELERBROCK R Potência e Rendimento Brasil Escola SDa Disponível em httpsbitly32doKeB Acesso em 13 abr 2021 HELERBROCK R Torque Brasil Escola SDb Disponível em httpsbitly3uS3w2p Acesso em 13 abr 2020 MELCONIAN S Elementos de Máquinas 9ª ed São Paulo Erica 2011 MOTT R L Elementos de máquinas em projetos mecânicos São Paulo 2015 NORTON R L Projetos de Máquinas Uma Abordagem Integrada 4ºed Porto Alegre Bookman 2013 SHIGLEY J E BUDYNAS R G NISBETT J K Elementos de máquinas de Shigley 8º ed São Paulo AMGH Editora Ltda 2011 22 2 CONCEITOS NO DIMENSIONAMENTO DE SISTEMAS MECÂNICOS Neste Bloco serão apresentadas as análises e cálculos dos esforços combinados Esforço Longitudinal e o Transversal em projetos de peças tendo como objetivo atender os limites de integridade sendo examinados os valores de propriedades mecânicas em principal e considerar também a influência da geometria da peça Ao longo do estudo deste bloco você verá a aplicação de conceitos apresentados em outras disciplinas já estudadas Resistência dos Materiais e Elementos de Máquina Afinal elas são de grande aplicação teórica para o entendimento na disciplina de Sistemas Mecânicos 21 ESFORÇOS COMBINADOS EM UM SISTEMA MECÂNICO Peças e equipamentos de maneira geral devem suportar os esforços a que estão sujeitos sem se romper São exceções a esta regra certos pinos de segurança que devem ser rompidos quando houver uma sobrecarga na máquina Assim não se deve permitir entretanto que um eixo quando solicitado tenha deformações permanentes Por isso a tensão máxima em qualquer ponto do eixo deve ser menor que a tensão de escoamento do material adotado Um elemento de máquina trabalhando com tensões abaixo da tensão de escoamento pode se romper quando os esforços forem realizados de forma cíclica Assim esse rompimento se dá devido ao material ter atingido seu limite de fadiga e por consequência acontece a ruptura Considerando a Força Axial e Radial a Figura 21 representa seus vetores momentos no plano que contribuem para a distribuição de Tensões Normais na seção Para o cálculo da Tensão Longitudinal sempre será considerada a relação dos esforços na direção normal assim será a razão entre a Força e a área aplicada sendo que esta tensão gerada no corpo pelos esforços normais dependendo da direção é definida e denominada como esforços de tração ou compressão 23 Figura 21 A representação dos Esforços Combinados como Longitudinais e Transversais Fonte BEER 2011 Cálculo da Tensão Normal ou Longitudinal 𝝈 aplicada 𝜎 𝑃 𝐴 N à Equação da carga Normal Longitudinal Onde 𝜎 Tensão Normal ou Longitudinal Nm2 ou Pa P Força aplicada na área transversal a Tensão Longitudinal Normal aplicadaN A Área da região que recebe o esforço ou tensão m2 que aplicada a um Eixo de seção cilíndrica A π r2 Sempre que é realizada a análise de esforços aplicados em um elemento mecânico qualquer durante a etapa de um Projeto Mecânico deve ser considerada a ocorrência de Tensões ou Esforços Tranversais e também Tensões ou Esforços Cortantes Tensão de Cisalhamento Desta forma para o cálculo do Limite admissível da Tensão Transversal que podem ocorrer como um Esforço de Momento Torçor ou um Esforço Cisalhante considerandose a área da seção longitudinal em análise sempre será necessário considerar a existência de aplicações no elemento de máquina ou sistema em análise na ocorrência de esforços Transversais e Longitudinais conforme Figura 22 e como revistos acima com o objetivo de que na sua solicitação de esforços máximos não seja gerada uma ruptura 24 Figura 22 A representação dos Esforços Combinados como Longitudinais e Transversais que podem variar dependendo do ponto em que está em relação aos esforços Fonte BEER 2011 Cálculo da Tensão Cisalhante Torçor ou Transversal 𝜏 aplicada 𝜏 𝑇 𝑐 𝐽 𝑁 𝑚2 𝑃𝑎 Onde T Torque Aplicado no Corpo C Raio do Corpo J Momento Polar de Inércia Detalhamento para Estudo Tabela 1 Para eixos cilíndricos à 𝐽 𝜋 2 𝑐4 Para relembrar os conceitos de Centro de Gravidade ou Momento Polar de Inércia ou seja onde ficam concentrados os Esforços ou Tensões que também já foram apresentados na disciplina de Resistência dos Materiais veja abaixo a tabela 21 que apresenta de maneira resumida os Momentos Polares de Inércia de Figuras com Geometrias Notáveis 25 Tabela 21 Equações de Momentos de Inércia Polares de Figuras Geométricas Notáveis Fonte BEER 2011 22 ANÁLISE DA PROPRIEDADE DA RIGIDEZ EM ESFORÇOS COMBINADOS Há peças que devem ser dimensionadas limitando suas deformações Um eixo por exemplo de uma caixa de mudança de velocidades não pode ter flexas excessivas para um bom funcionamento do conjunto O feixe de molas desse mesmo veículo será dimensionado para se conseguir uma certa flexa em cada condição de carga Analogamente temos limitações na deformação angular devido a torção imposta ao eixo 221 Custo de Fabricação É um dos critérios que oferece maior dificuldade ao projetista e está ligado a Tipo e Bitola da matéria à disposição Processo de Fabricação da Peça Número de Peças a serem produzidas 26 Além disso existem outros fatores que influenciam diretamente na vida útil do Elemento Mecânico ou peça como o desgaste pois onde há contato há atrito e ocorre o desgaste que se torna maior com o aumento da Temperatura e é influenciado pelo meio em que está devido à Corrosão Oxidação 23 ANÁLISE DA PROPRIEDADE DA RESISTÊNCIA Na disciplina Sistemas Mecânicos serão apresentados os esforços que a peça ou elemento de máquina a ser projetado sofrerá e que deverão atender diversas propriedades de resistência mecânica como o limite de escoamento e a resistência à fadiga quando o elemento ou peça for submetido a esforços Cíclicos Assim serão definidas quais características deverão compor o material a ser utilizado para a confecção da peça Então este material deverá resistir a Esforços Longitudinais eou Transversais Momento Torçor ou Esforço Cisalhante e que quando ocorrem juntos damos o nome de esforços mecânicos combinados 231 Pré Cálculo da Peça Neste subtema será estudada a forma de calcular os esforços atuantes para que as propriedades de resistência sejam atendidas no Projeto Vale lembrar que ao ser realizado um projeto e para que as propriedades de resistência sejam atendidas o projetista sempre irá analisar o Sistema Mecânico em equilíbrio Vale neste caso recordar uma forma mais simples de analisar esforços ou momento torçor e aplicar a Regra do Paralelograma para que seja possível determinar o valor do Vetor Resultante que conforme o exemplo a seguir na Figura 23 apresenta os vetores combinados e sua resultante Mz ou seja o momento resultante entre os vetores M1 e M2 Lembrando que temos a mesma regra para determinar o valor do Vetor de Momentos torçores e tensões e então determinar o valor da resultante em esforços longitudinais ou transversais Determinase os esforços ativos forças eou momentos provenientes de outros elementos de máquinas ou peças quando compõe um Sistema Mecânico aplicando a Regra do Paralelogramo conforme apresentado a seguir 27 Figura 23 Módulo do vetor resultante que segue sua geometria como paralelogramo e assim facilita o cálculo de seu valor Fonte Elaborado pelo autor Determinase os esforços reativos Impondose o equilíbrio da peça e em seguida traçamse os diagramas de momento Fletor e Torçor que atuam na peça por meio da aplicação da Regra do Paralelograma Veja que o exemplo a seguir segue a aplicação da Regra que considera a Figura 23 como referência na análise de equilíbrio de esforços 𝑀𝐸 𝑀1 𝑀2 ou 𝑀𝐸 𝑀12 𝑀2 2 Se 𝑀1 𝑀2 Constróise o Diagrama do Momento Torçor 𝑀𝑡 71620 𝑃 𝑛 Kgfcm Ou 𝑀𝑡 30 𝑃 𝜋 𝑛 Nm 28 Assim a próxima etapa será o cálculo do Momento Ideal 𝑀𝑖 Após obter o valor do Momento ou esforço resultante será obtido o Momento ou esforço resultante ideal e seu cálculo deverá ser realizado conforme as equações a seguir Será fundamental a análise do valor de 𝛼 𝐶𝑜𝑟𝑟𝑖𝑔𝑒 𝑜 𝑀𝑜𝑚𝑒𝑛𝑡𝑜 𝑇𝑜𝑟ç𝑜𝑟 e também será analisado o comportamento deste elemento de máquinas ou peça em condição de esforços ciclicos com uma frequência e formato de suas curvas de acordo com a figura 24 𝑀𝑖 𝑀𝐸 2 𝛼 𝑀𝑇2 𝛼 𝐶𝑜𝑟𝑟𝑖𝑔𝑒 𝑜 𝑀𝑜𝑚𝑒𝑛𝑡𝑜 𝑇𝑜𝑟ç𝑜𝑟 Figura 24 Curva S N em um Momento Ideal Caso Flexão e Torção Fonte SHIGLEY 2011 Sempre ao idealizar o projeto de uma peça ou elemento de máquina recebendo em sua aplicação esforços cíclicos devese ter em mente que independentemente da frequência do esforço cíclico deve ser analisado no projeto o tempo que as fibras externas e internas sofrerão diferentes tipos de esforços Sendo assim quando ocorre esforço de Flexão em uma fibra ou região da peça o outro extremo estará recebendo esforço Torçor e vice e versa conforme apresentado na figura 24 E com extrema importância temos o cálculo da resistência a Fadiga que é determinar o valor de 𝜶 e este sempre deve atender a condição de que seu valor seja menor ou igual a 1 29 𝛼 𝜎𝑐𝑎𝑠𝑜 𝑓𝑙𝑒𝑥ã𝑜 𝜏𝑐𝑎𝑠𝑜 𝑡𝑜𝑟çã𝑜 1 Assim determinando o Diâmetro do eixo 𝜎 𝑀𝑖 𝜋 𝑑3 32 232 Limite de Fadiga O conceito de Limite de Fadiga é a capacidade que o elemento de máquina ou eixo árvore terá em suportar um possível dano estrutural que é provocado por esforços cíclicos ou seja fenômeno este que quando ocorre reduz da propriedade de resistência do material e desta formaleva a ruptura A tabela 22 apresenta os Tipos de Solicitações de Esforços e correlaciona aos Tipos de Ciclos que pode ser simétrico ou pulsante Tabela 22 Correlação entre Esforços modos de Ciclos e suas equações Fonte Adaptado de SHIGLEY 2011 Tipo de Solicitação Ciclo Simétrico III Ciclo Pulsante II Flexão 𝜎𝑓 045 𝜎𝑟𝑢𝑝 𝜎𝑡𝑜 060 𝜎𝑟𝑢𝑝 𝜎𝑒 Tração Compresssão 𝜎𝑓 036 𝜎𝑟𝑢𝑝 𝜎𝑡𝑜 050 𝜎𝑟𝑢𝑝 𝜎𝑒 Torção 𝜏𝑓 022 𝜎𝑟𝑢𝑝 𝜏𝑜 030 𝜎𝑟𝑢𝑝 𝜏𝑒 30 Para aços de baixa liga à 𝜎𝑓 047 𝜎𝑟𝑢𝑝 Para aços de alta liga à 𝜎𝑓 053 𝜎𝑟𝑢𝑝 Para FoFo à 𝜎𝑓 042 𝜎𝑟𝑢𝑝 Além dos fatores do material os esforços e suas direções geram formas sendo que existem três formas fundamentais segundo as quais a carga pode operar sobre a ocorrência de uma trinca e cada um irá afetar um deslocamento diferente da superfície da trinca Figura 25 Modo I ocorre a abertura devido à concentração de tensões ou modo trativo as superfícies da trinca são tracionadas a parte Fonte adaptado de SHIGLEY 2011 Figura 26 Modo II ocorre a abertura devido ao deslizamento ou cisalhamento no plano as superfícies da trinca deslizam uma sobre a outra Fonte adaptado de SHIGLEY 2011 31 Figura 27 Modo III ocorre o rasgamento ou cisalhamento fora do plano as superfícies da trinca se movem paralelamente frente da trinca e uma a outra Fonte Adaptado de SHIGLEY2011 Conforme mencionado um eixo pode sofrer ruptura mesmo quando sujeito a tensões menores que a tensão de escoamento No ensaio de ruptura por flexão de um corpo de prova solicitado por tensões do caso III Tensão simétrica apresentada na tabela 22 seu comportamento seguirá a curva SN geral Abaixo são apresentados o comportamento e a forma da referida curva para cada tipo de material Figura 28 Curva S N de acordo com tensões cíclicas simétricas Tipo Ciclo Simétrico III Tabela 22 Fonte adaptado de SHIGLEY SD 32 O significado da curva SN vem das palavras em inglês Stress e Number of Cicles Estresse e Número de Ciclos também denominada de a Curva de Wohler Assim vemos que na Figura 28 é apresentada a Curva padrão do Stress aplicado a um determinado material e ao lado alguns exemplos de como cada material metálico tem comportamento diferente quando submetido a esforços cíclicos O que deve ser fixado conceitualmente é que a ocorrência de um estresse no material quando a tensão é elevada faz o corpo romperse antes de iniciar a rotação ou seja a ruptura será estática Para C 0 tem se 𝜎 𝜎𝑟𝑢𝑝𝑡𝑢𝑟𝑎 Sendo 𝜎1as solicitações a que está sujeito o corpo de prova para que a ruptura ocorra a 𝐶1 ciclos Aumentando a Vida Útil do Material para não ocorrer a fadiga conforme figura 28 Diminuindose a solicitação para 𝜎2 𝜎1 o rompimento se dará com um número de ciclos 𝐶2 𝐶1 Há uma tensão 𝜎𝑓 para qual o corpo pode ser solicitado durante infinitos ciclos 𝐶 sem ocorrer a ruptura 233 Cálculo de Concentrações de Tensões Outro cálculo prévio que deve ser realizado é o da tensão ou esforço aplicado na direção longitudinal de uma peça Esse cálculo pode não ser correto pois a presença de geometria Cantos vivos ou locais que geram uma maior concentração de tensões ou esforços conforme figura 28 podem acarretar em uma ruptura precoce também conhecida como fadiga Entretanto sua ocorrência se difere pois no ponto de concentração de Tensões ou Esforços há o aumento do valor da tensão aplicada e que não mais irá se distribuir mas sim concentrarse em uma região a ponto de gerar um rasgo conforme as figuras 25 26 27 e 29 33 Figura 29 Região sobre Tensão Aplicada com início da nucleação da Trinca Fonte adaptado de SHIGLEY 2011 𝜎 𝐹 𝐴 sendo F Força aplicada e A a área que é calculada entre a área base Para o exemplo a área é uma seção quadrangular e portanto é o produto das dimensões de suas laterais Se houver uma variação de seção como indicada na figura 29 temos que calcular a nova tensão 𝜎 𝜎 𝐹 𝐴0 𝐴2𝑏 assim a principal alteração será o valor no denominador ou seja calcular o valor da Área inicial 𝐴0 subtraindo o valor da nova Área 𝐴2𝑏 devido à nucleação que ocorreu Entretanto o grande objetivo da seleção do material e dimensionamento é para que esta última Tensão Normal não seja aplicada e seu valor nunca atingido desta forma mantemse a integridade da peça Dependendo então do tipo de singularidade teremos diferentes valores de 𝜎𝑚á𝑥 O quociente entre a máxima tensão 𝜎𝑚á𝑥 e a tensão calculada 𝜎 chamase concentração de tensões K 𝐾 𝜎𝑚á𝑥 𝜎 1 Lembrando 𝜎 𝐹 𝐴0 𝐴2𝑏 34 𝜎 à Tensão Cálculada 𝐴0 𝐴2𝑏 à Área útil O valor de K depende a Da geometria da singularidade forma de analisar e determinar valores de tensões aplicadas por meio do conceito que utiliza como exemplo um eixo circular Barra de metal modelo este ideal para auxílio dessa análise conforme já apresentado na disciplina de Resistência dos Materiais b Do Material da peça Conclusão Neste bloco foi apresentada a forma de análise e cálculo para evitar fraturas que acontecem devido a uma sobrecarga de tensões normais ou transversais podendo até serem de esforços com cargas combinadas Vimos também como caracterizar uma falha por fadiga e assim identificar e prevenir para que essa falha não ocorra mais tendo como fundamentos que devem ser analisados duas condições de projeto na engenharia Primeiramente o fator de uma Falha Mecânica em que as tensões eou tipo de esforços ocasionaram a falha e assim devemse analisar as forças atuantes na peça ou equipamento o tipo de esforço que está sendo submetido a ocorrência de forças excessivas ou qualquer carregamento que não seja da condição nominal do projeto ou Sistema Mecânico em análise Além disso cálculos dos esforços e carregamentos no sistema que podem e devem ser simulados por meio de ensaios experimentais de vibração e extensometria para a determinação do limite K da região da peça em estudo e que serão apresentados nas disciplinas de seleção de material de projetos na engenharia para que seja vista a segunda condição da causa a Falha metalúrgica que é ocasionada devido a defeitos metalúrgicos e que podem ser gerados ao longo do processo de fabricação Podendo ocorrer a descontinuidade na superfície fraturada a ocorrência de defeitos pontuais em ligações cristalinas entre outros Sendo que para identificar falha metalúrgica a matéria prima a ser utilizada na peça ou equipamento necessita de ensaios químicos metalográficos e caracterização das propriedades mecânicas do material 35 REFERÊNCIAS ANDRADE A S Elementos Orgânicos de Máquinas II UFP SD BEER F P et al Mecânica dos Materiais 5ª ed Porto Alegre AMGH 2011 MELCONIAN S Elementos de Máquinas 9ª ed São Paulo Erica 2011 MOTT R L Elementos de máquinas em projetos mecânicos São Paulo 2015 NORTON R L Projetos de Máquinas Uma Abordagem Integrada 4ºed Porto Alegre Bookman 2013 SHIGLEY J E BUDYNAS R G NISBETT J K Elementos de máquinas de Shigley 8 ed São Paulo AMGH Editora 2011 36 3 CONCEITOS NO DIMENSIONAMENTO DE EIXOS ÁRVORES Neste Bloco serão apresentadas as principais análises e seus cálculos para a seleção do material considerando a geometria e quais esforços combinados Esforço Longitudinal e o Transversal irão atuar para fundamentar os conceitos e realizar o projeto para o dimensionamento de eixos com o objetivo de atender os limites de integridade Para isto são analisados os valores de propriedades mecânica e a influência nas concentrações de tensões geradas na geometria ao longo do eixo em estudo para suportar suas condições de trabalho sem que haja um desgaste precoce com a ocorrência de uma fratura no eixo de forma que seja bemsucedido o projeto a ser realizado 31 MATERIAIS PARA APLICAÇÃO EM EIXOS Para se escolher um material para a fabricação de eixos devese considerar os seguintes fatores a Preço do material b Facilidade de obtenção no mercado da bitola a ser aplicada c Possibilidade de tratamento térmico e conhecer suas eventuais deformações d Ductilidade e Coeficiente de sensibilidade f Usinabilidade g Resistência à flexão e a torção h Resistência ao desgaste 37 São selecionados materiais metálicos de aço carbono e também os de aços ligas Eles devem ter em sua constituição valores de Carbono entre 03 até 07 C em média para Aumento da resistência Maior temperabilidade Menores deformações durante um tratamento térmico Agora ao ser aplicado o ferro fundido sua maior vantagem é o bom amortecimento de vibrações Podemos chegar a conclusão que os constituintes de elementos químicos metal ou ametal podem se combinar com o aço ou seja liga de ferro e carbono e ainda em sua composição com outros elementos sendo que estes podem melhorar as propriedades do material com a matéria prima que irá compor o projeto Segue a seguir na Tabela 31 a relação de nomenclatura em aços de baixa e média liga e sua percentagem de carbono correlacionando as Normas SAE DIN e os aços vilares bem como os níveis de níquel cromo molibdênio e outros Elementos estes que de acordo com a quantidade na composição química total dos aços melhoram os resultados das propriedades mecânicas como rigidez tenacidade resiliência elasticidade condutividade térmica ou elétrica e ponto de fusão 38 Tabela 31 Principais Aços para aplicação em produção de eixos e engrenagens SAEDIN para Villares Fonte MELCONIAN 2011 32 TEORIA DA TORÇÃO APLICADA EM EIXOS ÁRVORES Para o projeto de um eixo árvore a ser realizado a seleção do material deve ser tratada com fundamental importância bem como considerar sua geometria suas dimensões as condições em que os materiais serão utilizados e também as variáveis de esforços de carregamento Como exemplo temos as cargas que ocorrem em eixos de transmissão de rotação e que neste caso tem predominantemente esforços aplicados de dois tipos Eles são o de torção devido ao torque transmitido e o de Flexão devido às cargas transversais em engrenagens polias e catracas Assim na combinação dos dois tipos pode ocorrer carga axial também se a linha de centro do eixo for vertical O grande diferencial no projeto será em como avaliar e quais equações devem ser calculadas Então será apresentada uma sequência que será a melhor forma de avaliar conforme a Figura 31 O plano de ação do conjugado é igual ao plano da seção transversal Os conjugados são chamados de momentos de torção momentos torcionais ou torque T T e que têm a mesma intensidade T e sentidos opostos Nash1982 Ao ser analisado o Centro de Torção o ponto em torno do qual a seção transversal gira e que para seções simétricas coincide com o centro de gravidade vemos que o Eixo de Torção é o próprio lugar geométrico dos centros de torção 39 Um eixo circular está fixado a um suporte por uma de suas extremidades e aplicando à extremidade livre um momento de torção T o eixo gira e a seção transversal da extremidade apresenta uma rotação representada pelo ângulo φ chamado ângulo de torção BEER 2011 Figura 31 O eixo e o centro de torção gerado quando aplicado um Esforço Torçor Fonte adaptado de BEER 2011 Assim vemos na Figura 32 que a barra cilíndrica está fixada na Vertical ou na Horizontal Na Figura 33 temos que ao ser inserido um Momento de Torção Torque ou Momento Torçor ao longo de um comprimento L da barra esta será rotacionada e será gerada uma deformação ao longo de toda a barra por consequência do Momento Torçor aplicado Nestas condições descritas surgirá uma inclinação que será denominada de Ângulo de Torção φ variável fundamental para a análise do limite de resistência das propriedades mecânicas do material e do elemento mecânico em análise que em nosso estudo serão os eixos árvores Figura 32 Formação do ângulo de torção φ visto de formato em prisma circulares Fonte Adaptado de BEER 2011 40 Figura 33 O ângulo φ chamado ângulo de torção quando aplicado Torque no comprimento L Fonte Adaptado de BEER 2011 Quanto a análise dos esforços aplicados a um eixo árvore temos as fibras representadas como um prisma de seção circular conforme a Figura 32 ou Figura 34 e as condições que podem ser consideradas são a As geratrizes se transformam em hélices b O quadrado se transforma em um losango com os lados sofrendo a mesma deformação angular ângulo de torção φ c as seções normais permanecem planas e normais ao eixo de rotação e conservam sua forma Neste caso é preciso assegurar que os momentos sejam aplicados de tal forma que as extremidades também permaneçam planas e sem deformação 41 Figura 34 Linha central ou imaginária e as deformações ocorridas pelo esforço Torçor Fonte adaptado de BEER 2011 Por fim os critérios que são observados na Figura 34 acima nos apresenta que o Torque Momento Torçor aplicado ao eixo produzirá tensões de cisalhamento nas faces perpendiculares ao eixo As condições de equilíbrio requerem a existência de tensões iguais nas faces dos dois planos que contêm a linha central do eixo Também há existência dos componentes de cisalhamento axiais e que são demonstradas quando considerado um eixo composto de varetas axiais Sendo assim as varetas deslizam umas em relação às outras quando torques iguais e opostos são aplicados às extremidades do eixo Para atender as condições de equilíbrio as fibras nas faces externas e internas devem se equilibrar e por fim o eixo árvore atenderá sua condição de aplicação tanto no limite de resistência mecânica solicitada como também no aumento da vida útil 33 Cálculo da torção aplicada em eixos árvores Uma forma de realizar a determinação da distribuição de tensões de cisalhamento na seção transversal de deformação de cisalhamento γ é que ela deve ser igual ao ângulo formado por AB e AB 42 Figura 35 Eixo Circular de comprimento L com raio c e aplicado uma Torção Fonte adaptado de BEER 2011 Para melhorar o entendimento e a aplicação dos cálculos a seguir a barra cilíndrica conforme a Figura 36 deverá atender as seguintes condições a O eixo circular de comprimento L e raio c que foi torcido em um ângulo de torção φ b Retirando do interior do eixo um cilindro de raio ρ marcandose um quadrado sobre a superfície dele sem atuação de momento de torção c Aplicase a torção o quadrado se transforma em losango as deformações de cisalhamento são medidas pela variação de dois lados Figura 36 Eixo Circular de comprimento L em análise na seção AA Fonte adaptado de BEER2011 43 Por meio da Figura 36 você pode observar que quando γ é pequeno o comprimento de arco AA é dado por AALγ e na seção transversal AA ρ Φ A equação a ser utilizada para a determinação do ângulo de torção 𝛾 será 𝛾 𝜌 Φ 𝐿 sendo 𝛾 𝑒 𝜌 𝑒𝑚 𝑟𝑎𝑑𝑖𝑎𝑛𝑜 Onde 𝛾 𝐴𝑛𝑔𝑢𝑙𝑜 𝑑𝑒 𝑇𝑜𝑟çã𝑜 𝑛𝑜 𝑒𝑖𝑥𝑜 𝑐𝑖𝑟𝑐𝑢𝑙𝑎𝑟 𝜌 𝐴𝑛𝑔𝑢𝑙𝑜 𝑐𝑒𝑛𝑡𝑟𝑎𝑙 𝑑𝑒 𝑟𝑒𝑓𝑒𝑟ê𝑛𝑐𝑖𝑎 𝑞𝑢𝑎𝑛𝑑𝑜 𝑎𝑝𝑙𝑖𝑐𝑎𝑑𝑎 𝑎 𝑇𝑜𝑟çã𝑜 φ um ângulo de torção aplicado no eixo circular L Comprimento do eixo circular c raio do eixo circular Podese concluir que a deformação de cisalhamento em uma barra circular varia linearmente com a distância ao eixo da barra sendo o 𝛾𝑀á𝑥 na superfície da barra circular onde 𝜌 𝑐 𝛾𝑀á𝑥 𝑐 Φ 𝐿 e 𝛾 𝜌 𝑐 𝛾𝑀á𝑥 331 Tensões no Regime Elástico Quando considerada a torção T tem um valor tal que as tensões no material se mantêm abaixo da tensão de cisalhamento de escoamento 𝜏𝑒 Nesse caso as tensões no material permanecem abaixo dos limites de proporcionalidade e elasticidade Lei de Hooke conforme a Figura 37 que apresenta a Curva de um Material Dúctil no ensaio de Tensão por uma Deformação 44 Figura 37 Curva de um Ensaio de Tensão e Deformação de um material Dúctil Fonte Adaptado de SHIGLEY 2011 A tensão de cisalhamento na barra irá variar linearmente com a distância 𝜌 do eixo da barra 𝜏 𝐺 𝛾 𝐺 𝛾 𝜌 𝑐 𝐺 𝛾𝑀á𝑥 Então temse 𝜏 𝜌 𝑐 𝜏𝑀á𝑥 Da mesma forma a Tensão Máxima de Torção 𝜏𝑀á𝑥 𝑇 𝑐 𝐽 Considerando a Tensão de Cisalhamento a uma distância 𝜌 do eixo da barra 𝜏 𝑇 𝜌 𝐽 sendo J O momento de Inércia Polar de um círculo com raio c 𝐽 1 2 𝜋 𝑐4 45 A tensão de torção em uma barra de seção circular maciça ocorrerá como demonstrado na Figura 38 Desta forma irá variar linearmente com a distância ρ que inicia a ação deste esforço cisalhante no centro do eixo até a superfície externa da barra Figura 38 Distribuição das Tensões de Cisalhamento para um eixo circular maciço Fonte adaptado de BEER 2011 Caso seja aplicada a Tensão de Torção em uma barra vazada de raio externo 𝑪𝟐 Conforme a Figura 39 que apresenta a distribuição das tensões de cisalhamento para um eixo vazado o cálculo do Momento de Inércia Polar considerando o raio interno c1 e raio externo c2 Figura 39 Distribuição das Tensões de Cisalhamento para um eixo circular vazado Fonte adaptado de BEER 2011 Sendo o caso de avaliar o valor da Tensão Mínima de Cisalhamento com relação a Tensão Máxima de Cisalhamento em um eixo circular vazado temse 46 𝜏𝑀𝑖𝑛 𝑐1 𝑐2 𝜏𝑀á𝑥 O Momento de Inércia Polar será 𝐽 1 2 𝜋 𝑐24 𝑐14 Lembrando das variáveis e suas unidades por meio do Sistema Internacional SI T Nm c 𝜌 m J 𝑚4 𝜏 𝑁 𝑚4 Φ 𝛾 radianos 332 Ângulo de Torção no Regime Elástico Para este item vamos visualizar de acordo com a Figura 310 um eixo circular de comprimento L seção transversal uniforme de raio c Figura 310 Eixo Árvore maciço recebendo diferentes valores de Torção Fonte BEER 2011 O eixo está sujeito à ação de um momento de torção T O ângulo de torção φ e a deformação de cisalhamento máxima 𝛾𝑀á𝑥 estão relacionados por 𝛾𝑀á𝑥 𝑐 Φ 𝐿 47 No regime elástico 𝛾𝑀á𝑥 𝜏𝑀á𝑥 𝐺 Sendo γMáx τMáx G T c J G Para obter o valor do Ângulo de Torção portanto Φ 𝑇 𝐿 𝐽 𝐺 φ é expresso em radianos No regime elástico o ângulo de torção φ é proporcional ao momento de torção T aplicado no eixo circular A equação só pode ser usada no caso de material homogêneo para eixos de seção transversal constante e momentos aplicados nas extremidades da barra Eixos submetidos a momentos de torção aplicados em outros pontos com seções transversais compostas e o ângulo de torção φ do eixo circular é igual ao ângulo de rotação da extremidade livre De forma análoga e com a correta análise dos esforços Torçor aplicados ao longo do eixo AB representado na Figura 310 devese considerar quatro partes diferentes AC CD DE e EB O ângulo de torção total do eixo isto é o ângulo segundo o qual a seção A gira em relação a seção B será obtido somando algebricamente os ângulos de torção de dada parte do componente Então o ângulo de torção total será dado por ϕ Σ𝑖 𝑇𝑖 𝐿𝑖 𝐽𝑖 𝐺𝑖 Onde Ti Li Ji e Gi correspondem à parte i do eixo Podese escrever a potência mecânica transmitida H em W como 𝐻 𝑇 𝜔 48 Onde 𝜔 é a velocidade angular do eixo rads e o T o torque mensurado em Nm 𝜔 2 𝜋 𝑛 60 Vamos aplicar Exercício 1 Considere um sistema mecânico manivela que é utilizada em uma determinada etapa de processo de peneiramento em uma mineradora As condições de trabalho ou seja os esforços atuantes geometria e as dimensões estão representadas na Figura 311 assim pedese Figura 311 Representação da Manivela que será analisada Fonte BEER 2011 Considerando os valores de F 13 kN Eixo engastado com diâmetro de 20 mm Determinar a DCL Diagrama de Corpo Livre do eixo e do braço bem como todas as forças e momentos atuantes b Localizar um elemento de tensão em A e calcular as tensões atuantes c Determinar as tensões normais e cisalhamento máximas em A 49 Solução Item a Para obter os valores das tensões aplicadas ao sistema será analisado separadamente ou seja ponto a ponto da manivela figura 312 assim são obtidos os esforços atuantes e seus valores separados assim facilita para obter dados deste e outros itens deste exemplo Na extremidade C do braço BC F 13j kN Tc 005k kN m Na extremidade B do braço BC F 13j kN M1 013i kN m T1 005k kN m Na extremidade B do eixo AB F 13j kN T2 013i kN m M2 005k kN m Na extremidade A do eixo AB F 13j kN MA 066k kN m TA 013i kN M Figura 312 Representação do Diagrama de Corpo Livre DCL da manivela separada em nós Fonte BEER 2011 Continuação da Solução Item b Utilizandose as equações do círculo de Mohr no ponto A 50 𝜎𝑥 𝑀 𝐼 𝑐 32 660 𝜋 0023 8403 𝑀𝑃𝑎 𝜏𝑥𝑧 𝑇 𝐽 𝑐 16 130 𝜋 0023 828 𝑀𝑃𝑎 Item c 𝜎1 8484 𝑀𝑃𝑎 τ1 4282 MPa Vamos Aplicar Exercício 2 Considere também no processo de peneiramento de uma mineradora onde há um Sistema Mecânico um módulo redutor de velocidades com polias para a movimentação de minério Assim temos o sistema mecânico Eixo com polias Dados Eixo maciço de d 40 mm Diâmetro da Polia A à DB 100 mm e Diâmetro da Polia C à DC 200 mm Obter Determine a localização e magnitude das maiores tensões de cisalhamento tração e compressão no eixo Figura 313 Representação do Eixo com Polias Fonte BEER 2011 51 Solução DCL e Diagramas de momento fletor Figura 314 Diagrama Corpo livre e Cálculo do Momento Fletor em Eixo com Polias Fonte BEER 2011 Solução Tensões Solução 52 Figura 315 Representação dos esforços de Momento Fletor e os ângulos gerados na seção transversal da Manivela Fonte BEER 2011 Conclusão O fundamento principal deste Bloco é apresentar os conceitos em projetos de sistemas mecânicos e aplicar as variáveis elementares no projeto de um eixo árvore desde a seleção de material e geometria até as dimensões Por fim analisamos os esforços combinados que são aplicados durante o trabalho de um eixo árvore tendo aprendido uma aplicação em uma linha de produção considerando dois Sistemas Mecânicos Manivela e Eixo com Polias REFERÊNCIAS ANDRADE A S Elementos Orgânicos de Máquinas II UFP SD BEER F P et al Mecânica dos Materiais 5ª ed Porto Alegre AMGH 2011 MELCONIAN S Elementos de Máquinas 9ª ed São Paulo Erica 2011 MOTT R L Elementos de máquinas em projetos mecânicos São Paulo 2015 NORTON R L Projetos de Máquinas Uma Abordagem Integrada 4º ed Porto Alegre Bookman 2013 SHIGLEY J E BUDYNAS R G NISBETT J K Elementos de máquinas de Shigley 8ª ed São Paulo AMGH Editora Ltda 2011 53 4 CONCEITOS EM ENGRENAGENS CILÍNDRICAS DE DENTES RETOS ECDR Neste Bloco serão apresentados os principais conceitos de uma engrenagem item selecionado dentre uma extensa gama de elementos de máquinas que é utilizada no conjunto de um sistema mecânico Ao considerar o objetivo de aprendizagem foi selecionado o elemento de uma Engrenagem Cilíndrica de Dentes Retos ECDR assim serão apresentados os conceitos de suas aplicações a seleção de materiais que irá compor a engrenagem o processo de fabricação selecionado e suas especificações desde a geometria até todas as dimensões que por meio do memorial de cálculo que será definido comporá o projeto mecânico que ao final terá a resistência da engrenagem com os diversos esforços das cargas mecânicas e suportará sem fadigar e sofrer redução de vida útil 41 CARACTERÍSTICAS FUNDAMENTAIS DAS ENGRENAGENS DO MODELO ECDR As engrenagens são elementos de transmissão largamente utilizados em projeto de máquinas pois tem vantagens em sua utilização em sistemas mecânicos razão de transmissão constante relação potênciapeso elevados custo baixo em grandes produções rendimento elevado e sua variedade de formas de transmissão Veja a seguir os critérios fundamentais das Engrenagens Fabricação de engrenagens Qualidade das engrenagens Características gerais Tipos de engrenagens Engrenagens cilíndricas de dentes retos Características geométricas Dimensionamento 54 411 Processos de Fabricação de Engrenagens Os processos de fabricação de engrenagens podem ser realizados por a Usinagem b Fundição c Sem retirada de cavaco Veja a seguir como funciona cada processo A usinagem de engrenagens pode ser A usinagem por geração que utiliza fresas caracol conforme a Figura 41 Engrenagem de corte conforme a Figura 42 ou de Cremalheira de corte conforme a Figura 43 Sendo que entre os 3 processos pelo método de usinagem o mais utilizado na indústria é o de Engrenagem de corte Figura 42 a Usinagem de engrenagens Figura 41 Usinagem por fresa caracol Fonte ANDRADE SD 55 Figura 42 Usinagem por engrenagem de corte Fonte ANDRADE SD Figura 43 Usinagem por cremalheira de corte Fonte SHIGLEY 2011 Figura 44 Usinagem por fresa módulo Fonte ANDRADE SD 56 b Fundição de engrenagens A fabricação de engrenagens por fundição utiliza processos por gravidade demonstrado na Figura 5a sob pressão na Figura 5b ou em casca na Figura 5c que são apresentados a seguir A Figura 45 a a seguir nos apresenta de forma detalhada as etapas do processo de fabricação de engrenagens pelo método de Fundição por gravidade em que se inicia a etapa de fabricação nos seus moldes fixomóvel Começando pelos moldes fixo e móvel passando pelo cadinho com metal fundente que por gravidade energia potencial preenche os moldes para que ao final tenhamos nossa engrenagem Após este processo há apenas uma etapa de lixamento para que atenda aos dimensionais geométricos Figura 45 a Processo de fabricação das engrenagens pelo método de Fundição Ciclo do Processo de Fundição por gravidade Fonte Adaptado de KIMINAME CASTRO OLIVEIRA SD 57 A Figura 45 b a seguir nos apresenta o processo de fabricação de engrenagens pelo método sob pressão em que se inicia a etapa de fabricação nos seus moldes fixomóvel Começando pelos moldes fixo e móvel passando pelo sistema de pistão para a injeção de material fundente que por pressão finaliza o preenchimento dos moldes e ao final teremos a nossa engrenagem Após este processo há uma etapa de lixamento para que atenda aos dimensionais geométricos Figura 45 b Processo de fabricação das engrenagens pelo método de Fundição Ciclo do Processo sob pressão Fonte Adaptado de KIMINAME CASTRO OLIVEIRA SD A Figura 45 c a seguir nos apresenta o processo de fabricação de engrenagens pelo método em casca em que se inicia a etapa de fabricação nos seus moldes fixomóvel Começando pelo molde fixo e molde móvel em casca passando metal fundente na caixa basculada antes de ser inserida no forno térmico para que ao final tenhamos nossa engrenagem 58 Figura 45 c Processo de fabricação das engrenagens pelo método de Fundição Ciclo do Processo de Fundição em casca Fonte Adaptado de KIMINAME CASTRO OLIVEIRA SD c Sem retirada de cavaco Esse processo é dividido em dois subgrupos estampagem e forjamento O processo de estampagem ocorre por meio da pressão aplicada entre a matéria prima e o seu molde matriz para assim ser obtida a engrenagem Já o forjamento é classificado entre os processos de extrusão e trefilação laminação forjamento em matriz conforme Figura 46 59 Figura 46 Processo de fabricação de engrenagens pelo método sem retirada de cavaco Processo Forjamento Fonte Adaptado de KIMINAME CASTRO OLIVEIRA SD 412 Qualidade das Engrenagens O conceito de qualidade das engrenagens ocorre por meio das Normas DIN 862 e 867 que especifica as 12 principais características de qualidade Qualidade 1 Atualmente não utilizada pode ser usada quando não há uma referência da aplicação desta Engrenagem Qualidade 2 São utilizadas em indústria de precisão Relojoaria e aparelhos de precisão Qualidade 3 São utilizadas como padrão em laboratórios de controle Assim são consideradas engrenagens de precisão Qualidade 4 Utilizase na fabricação de engrenagens padrão engrenagens para aviação e engrenagens de alta precisão para torres de radar Qualidade 5 São utilizadas em aviões máquina operatrizes instrumentos de medida turbinas etc Qualidade 6 Utilizase em automóveis ônibus caminhões navios e mecanismo de alta rotação Qualidade 7 Engrenagens Sheivadas são empregadas em veículos máquinas operatrizes máquinas de levantamento e transporte etc Qualidade 8 e 9 São as mais empregadas pois não precisam ser retificadas Utilizamse em máquinas gerais 60 Qualidade 10 a 12 São engrenagens mais rústicas normalmente utilizadas em máquinas agrícolas Desta forma podese concluir que das 12 principais características de qualidade a Qualidade 1 é utilizada para aplicações com elevada precisão e segue até a Qualidade 12 cuja aplicação será mais rústica por exemplo em máquinas agrícolas moinhos de moagem de cana de açúcar etc 413 Aplicação Tipos e a Geometria de Engrenagens Cilíndricas de Dentes Retos ECDR Algo fundamental a saber é que os principais critérios e condições de aplicação de engrenagens estão descritas na norma DIN 862 e 867 que referencia os critérios de Geometria Conforme a engrenagem Figura 47 e também especificam o grau de qualidade materiais de fabricação quais processos de fabricação podem ser utilizados e por fim as dimensões que terá a engrenagem que será projetada para atender aos requisitos de resistência em condições de diversos esforços mecânicos e assim aumentar a sua vida útil Figura 47 Características geométricas conforme DIN 862 e 867 Neste acoplamento entre as engrenagens vemos a engrenagem de diâmetro maior Coroa e a de diâmetro menor Pinhão Fonte SHIGLEY 2011 61 Para facilitar a sequência de projeto iremos apresentar três tipos de nomenclaturas para as formas de acoplamento durante a transmissão de energia de uma ECDR 1 Engrenagens externas Em que a energia mecânica de transmissão gerada e seu acoplamento ocorrem de forma Externa conforme Figura 48 a Figura 48 a Exemplo do tipo de Engrenagem Cilíndrica de Dente Reto ECDR com engrenamento externo Fonte MELCONIAN 2011 2 Engrenagens internas em que a energia mecânica de transmissão gerada e seu acoplamento ocorrem de forma Interna conforme Figura 48 b Figura 48 b Exemplo do tipo de Engrenagem Cilíndrica de Dente Reto ECDR com engrenamento interno Fonte MELCONIAN 2011 3 Pinhão e cremalheira que geram a energia mecânica de transmissão e seu acoplamento também ocorre de forma Externa conforme Figura 48 c 62 Figura 48 c Exemplo do tipo de Engrenagem Cilíndrica de Dente Reto ECDR Pinhão e cremalheira Fonte MELCONIAN 2011 Os elementos mecânicos em análise neste Bloco são as Engrenagens Cilíndricas de Dentes Retos ECDR que serão dimensionadas conforme DIN 862 e 867 normas que ditam a geometria de cada elemento mecânico como as engrenagens Estas podem ter a geometria variada e por consequência diferentes referencias de nomenclatura e pontos de dimensões obtidos através do cálculo de projeto Esse cálculo tem como objetivo definir a propriedade mecânica de sua ruptura e tempo de duração da vida útil que dependem do tipo e horas diárias de funcionamento como você poderá ver mais à frente na Tabela AGMA 𝝋 Abaixo na Figura 49 serão apresentadas as cotas dos diâmetros principais de acordo com as normas DIN 862 e 867 63 Figura 4 9 Diâmetros principais de uma ECDR Fonte SHIGLEY 2011 Diâmetros principais Diâmetro primitivo 𝑑0 𝑚 𝑍 Diâmetro de base 𝑑𝑔 𝑑0 𝑐𝑜𝑠 𝛼 Diâmetro interno pé dente 𝑑𝑓 𝑑0 2 ℎ𝑓 Diâmetro externo cabeça do dente 𝑑𝑘 𝑑0 2 ℎ𝑘 Para determinar os diâmetros principais suas características geométricas e seus valores dimensionais de acordo com a Norma DIN 862 e 867 você verá na Tabela 41 as principais equações que deverão ser consideradas pelo projetista no Memorial de Cálculo do Projeto de um Sistema Mecânico que neste caso será a Engrenagem Cilíndricas de Dentes Retos ECDR 64 Tabela 41 Equações que determinam os valores que compõe a geometria de uma Engrenagem Cilíndrica de Dentes Retos ECRD Fonte MELCONIAN 2011 De acordo com as Normas DIN 862 e 867 a Figura 410 apresenta as terminologias utilizadas nas características geométricas de uma ECDR Número de dentes Z 𝑍 𝑑0 𝑚 Módulo m m t0 𝜋 Diâmetro primitivo 𝑑0 𝑑0 𝑚 𝑍 Diâmetro de base 𝑑𝑔 𝑑𝑔 𝑑0 𝑐𝑜𝑠𝛼0 Passo 𝑡0 𝑡0 𝑚 𝜋 Espessura do dente no primitivo 𝑆0 𝑡0 2 folga nula no flanco Altura comum do dente ℎ 2 𝑚 Altura da cabeça do dente ℎ𝑘 𝑚 Altura total do dente ℎ𝑧 22 𝑚 Altura do pé do dente ℎ𝑓 12 m Vão entre os dentes no primitivo 𝑙0 𝑡0 2 folga nula no flanco Ângulo de pressão 𝛼0 20 145 𝑜𝑢 25 Folga da cabeça 𝑆𝐾 02 𝑚 Relação da transmissão 𝑖 𝑍2 𝑍1 𝑑02 𝑑01 𝑛1 𝑛2 Largura do dente b 9m 𝑏 14m Distância entre centros 𝐶𝑐 𝑑01 𝑑02 2 65 Figura 410 Terminologias utilizadas nas Engrenagens Cilíndricas de Dentes Retos ECDR Fonte SHIGLEY 2011 42 DIMENSIONAMENTO DE ENGRENAGENS CILÍNDRICAS DE DENTES RETOS ECDR Neste item serão apresentadas as principais equações que serão utilizadas no dimensionamento de uma ECDR para atender ao limite e à aplicação deste elemento mecânico ao ser solicitada em um projeto Etapa 1 Dimensionamento com o Critério de desgaste As etapas de um projeto de um elemento mecânico engrenagens de dentes retos seguem dessa maneira Veja a seguinte expressão que deve ser utilizada no dimensionamento de pinhões com ângulo de pressão 20 e número de dentes de 18 a 40 Material utilizado na fabricação Material aço 𝑏1𝑑01 2 572 105 𝑀𝑡 𝑝2 𝑎𝑑𝑚 𝑖 1 𝑖 014 𝜑 Sendo que há 2 condições nesta expressão de Volume da base do dente 66 í𝑛𝑑𝑖𝑐𝑒 𝑒𝑛𝑔𝑟𝑒𝑛𝑎𝑔𝑒𝑛𝑠 𝑒𝑥𝑡𝑒𝑟𝑛𝑎𝑠 í𝑛𝑑𝑖𝑐𝑒 𝑒𝑛𝑔𝑟𝑒𝑛𝑎𝑔𝑒𝑛𝑠 𝑖𝑛𝑡𝑒𝑟𝑛𝑎𝑠 𝑜𝑢 𝑝𝑙𝑎𝑛𝑒𝑡á𝑟𝑖𝑎𝑠 Ambos os exemplos de Engrenamento Externo ou Interno foram apresentados na Figura 47 Seguem outras variáveis consideradas no cálculo acima b1 Largura do dente do pinhão mm d01 Diâmetro primitivo do pinhão mm MT Momento torçor do pinhão Nmm Padm Pressão admissível de contato Nmm2 𝒊 Relação de transmissão Z2Z1 adimensional 𝝋 Fator de serviço consultar tabela adimensional Etapa 2 Para o Dimensionamento de ECDR Pressão admissível 𝑝𝑎𝑑𝑚𝑖𝑠𝑠í𝑣𝑒𝑙 𝑝𝑎𝑑𝑚 0487 𝐻𝐵 𝑊1 6 𝑁 𝑚𝑚2 No exemplo que vamos aplicar mais à frente no enunciado do Estudo de Caso para Dimensionar uma ECDR serão fornecidos os valores de Dureza Horas de atividade do elemento mecânico e seu Valor de utilização Agma 𝜑 Assim falta o valor do Fator de Durabilidade W Seu cálculo é feito por meio da equação a seguir Fator de durabilidade W 𝑊 60 𝑛𝑝 ℎ 106 67 Em que Np Rotação do pinhão rpm h Duração do par horas HB Dureza Brinell Nmm2 A tabela 42 a seguir apresenta a correlação entre os tipos de material que podem ser utilizados na confecção de uma ECDR e os valores determinados por meio do método de ensaio de dureza Brinell Vale lembrar que não há uma equação de conversão entre os métodos dos Ensaios de Dureza mas existe uma tabela que correlaciona o valor obtido em diferentes métodos utilizados no ensaio A tabela 42 apresenta apenas como referência os Valores de HBrinell Mas para os tipos de aços descritos abaixo deverá ser utilizada a tabela Rockwell C HRc mesmo sendo só como referência Os aços são SAE 4320 SAE 4340 SAE 8620 SAE 8640 e temperados Tabela 42 Tabela de Dureza pelo Método Brinell Material HBRINELL 𝑵 𝒎𝒎𝟐 Aço fundido tipo 2 1700 2500 Aço fundido tipo 𝑩𝟐 1250 1500 Aço SAE 1020 1400 1750 Aço SAE 1040 1800 2300 Aço SAE 1050 2200 2600 Aço SAE 31453150 1900 2300 Aço SAE 4320 2000 4200 Aço SAE 4340 2600 6000 Aço SAE 8620 1700 2700 Aço SAE 8640 2000 6000 Aço fundido cinzento 1200 2400 Aço fundido nodular 1100 1400 Fonte MELCONIAN 2011 68 Já a Tabela 43 apresenta o conceito de determinação dos valores de dureza obtidos nos Ensaios de Dureza Uma importante informação não há uma equação ou uma tabela que ajude a realizar a conversão nos valores do Ensaio de Dureza pois cada valor é associado ao seu ensaio e tem particularidades de carga aplicada O elemento penetrador da superfície e a forma da impressão que será analisada de acordo com o método de ensaio e também com o valor de Dureza Brinnell HB solicitada na equação pode ser encontrada em catálogos ou em certificados de fabricação do lote produzido de Aço ou Ferro Fundido Estes terão as informações de Composição Química e as Propriedades Mecânicas com Tenacidade e sua Dureza conforme exemplo da Tabela 43 Tabela 43 Valores de correlação entre os valores obtidos nos Ensaios de dureza Brinell Resistência 𝑵 𝒎𝒎𝟐 Rockwell Impr mm Carga 30 kN Esfera Dureza HB 𝑵 𝒎𝒎𝟐 Aço carbono HB x 036 C Rc B Rb A Ra Shore Vickers 365 2270 997 29 104 646 39 279 370 2690 969 28 104 641 38 270 375 2620 943 26 103 636 37 263 380 2550 918 25 102 630 37 256 400 2290 824 21 98 608 33 229 Fonte adaptado de MELCONIAN 2011 No cálculo da expressão a seguir temos a relação entre a Largura da engrenagem b e o Diâmetro primitivo d0 e é determinado o valor de b d0 Então para ECDR e para o bom dimensionamento da engrenagem haverá duas condições 1 Engrenagem Biapoiada o valor é b d0 12 Característica as duas extremidades do eixo são apoiadas 2 Engrenagem em Balanço o valor é b d0 075 Característica uma das extremidades do eixo é apoiada 69 Confira como é a representação dessas expressões na figura 411 Figura 411 Representação das duas formas de uma ECDR se apoiar em um eixo Fonte MELCONIAN 2011 Na tabela 44 apresentada a seguir é definido o incremento no módulo após sua obtenção no cálculo do módulo de engrenamento de uma ECDR Este cálculo é usado para a fabricação de engrenagens no processo de fresamento e o módulo da ferramenta será o Módulo da engrenagem somado ao incremento Tabela 44 Correlação entre os valores dos Módulos normalizados DIN 780 e o incremento para a ferramenta de fabricação da engrenagem Módulo mm Incremento mm 03 a 10 010 10 a 40 025 40 a 70 050 70 a 160 100 160 a 240 200 240 a 450 300 450 a 750 500 Fonte adaptado de MELCONIAN 2011 Etapa 3 Esforços de flexão no pé do dente e os Tipos de Esforços gerados Normalmente para projetar escolhemos um critério para o dimensionamento e outro para a verificação No caso de engrenagens dimensionamos pelo desgaste e verificamos pelo critério de tensão no pé do dente Essa deve ser menor que a tensão admissível do material indicado 70 Durante a atividade desta engrenagem em um sistema mecânico de Transmissão de Movimentos Rotativos acontecerão Esforços de Flexão nos Pés dos Dentes da engrenagem ECDR Nas engrenagens cilíndricas de dentes retos ECDR são gerados dois esforços que geram uma Força de Flexão nos Pés dos Dentes da ECDR conforme apresentado na Figura 412 Os esforços são 1 Força tangencial 2 Força radial Figura 412 Representação da interação das forças Tangenciais e Radiais que gera Flexão no Pé dos Dentes de uma ECDR Fonte SHIGLEY 2011 Então as seguintes equações são aplicadas para obter o valor dos Esforços Para o caso de uma Força Tangencial 𝑭𝒕 veja a Figura 413 1 Força tangencial 𝑭𝒕 A carga tangencial Ft é responsável pelo movimento das engrenagens sendo também a carga que origina o momento fletor tendendo por flexão o pé do dente 71 A fórmula tangencial é determinada da seguinte maneira 𝐹𝑡 𝑀𝑡 𝑟0 2𝑀𝑡 𝑑0 raio primitivo 𝑟0 𝑑0 2 Em que Ft força tangencial N MT torque Nmm ro raio primitivo da engrenagem mm do diâmetro da engrenagem mm Figura 413 Força Tangencial aplicada e que gera esforço de Flexão no pé do dente Fonte SHIGLEY 2011 Então para obter o valor da Força Radial 𝑭𝒓 aplicada temos 2 Força radial 𝑭𝒓 A Força Radial atua na direção radial no Pé do Dente de uma engrenagem ECDR É determinada por meio da tangente do ângulo α ângulo de pressão tag 𝛼 𝐹𝑟 𝐹𝑡 Temos Fr Ft tag α 72 Em que Fr carga radial N Ft carga tangencial N α ângulo de pressão graus 3 Força resultante 𝐹r É a resultante Ft e Fr sendo determinada por meio de Pitágoras como segue Em que Fn carga resultante N Fr carga radial N Ft carga tangencial N Ou ainda pelas reações 𝑐𝑜𝑠 𝛼 𝐹𝑡 𝐹𝑛 𝐹𝑛 𝐹𝑡 𝑐𝑜𝑠 𝛼 As cargas radial e resultante serão importantes no dimensionamento de eixos e mancais sendo necessário o seu dimensionamento das engrenagens Etapa 4 Tensão máxima aplicada e a correlação entre a Tensão Material usada na fabricação da ECDR e o valor do esforço de Tensão de flexão no pé do dente A tensão atuante no pé do dente deve ser menor ou igual à tensão admissível do material indicado Veja a seguir fórmula que determina a intensidade da tensão máxima que a engrenagem sofrerá e que seu material de fabricação deverá resistir além de indicar os limites da Propriedades Mecânicas e a sua Vida Útil 𝜎𝑚á𝑥 𝐹𝑡 𝑞 𝜑 𝑏 𝑚𝑛 𝜎𝑚𝑎𝑡𝑒𝑟𝑖𝑎𝑙 73 Em que σ máx Tensão máxima atuante na base do dente Nmm2 𝝈 material Tensão admissível do material Nmm2 Ft Força tangencial N mn Módulo normalizado mm b Largura do dente do pinhão mm ϕ Fator de serviço tabela AGMA adimensional q Fator de forma adimensional Etapa 5 Cálculo do Fator de forma 𝑞 que deverá ser de acordo com o número de dentes entre as engrenagens como por exemplo Coroa e Pinhão com geometria de uma ECDR O fator de forma de engrenagem é obtido em função do número de dentes da engrenagem conforme apresentado na Tabela 45 Tabela 45 Correlação entre os valores do número de dentes e o fator de forma Fonte SHIGLEY 2011 Obs Se o número e dentes for intermediário aos apresentados na Tabela 45 será necessário realizar a operação matemática de interpolação tanto no número de dentes Z quanto no Fator de Forma q 74 Etapa 6 Obtémse nas tabelas a seguir o Valor dos Fatores de Serviço AGMA 𝝋 Este valor será considerado entre 2 condições ou seja 10 ou 24 horas de serviço para então obter o valor dos fatores de serviço AGMA conforme os exemplos apresentados a seguir nas Tabelas 46 e 47 Vale lembra que os valores do Fator de Serviço AGMA ϕ de uma engrenagem ECDR como exemplificados nas Tabelas 46 e 47 ficam sempre à disposição em catálogos de fabricantes de engrenagens ou elementos de máquinas aplicado a um sistema mecânico Tabela 46 Tabelas de fatores de serviço AGMA ϕ Fonte adaptado de MELCONIAN 2011 A Tabela 47 apresenta características fundamentais para o dimensionamento e a correta seleção do valor de acordo com as horas de serviço Esta condição altera a vida útil do projeto de um sistema mecânico Tabela 47 Continuação do exemplo de Tabelas de fatores de serviço AGMA ϕ para o acionamento de motores a explosão e serviços intermitentes Motor Elétrico Motor Elétrico Motores a Explosão Multicilíndricos 10 h 3 h 3 h 10 h 24 h 100 050 100 125 150 125 100 125 150 175 175 150 175 200 225 Fonte adaptado de MELCONIAN 2011 Aplicações Serviço Horas de Atividade 10 h 24 h AGITADORES Líquidos 100 125 Misturadores de polpa 125 150 Semilíquidos de densidade variável 125 150 ALIMENTADORES Alimentadores helicoidais 125 150 Alimentadores recíprocos 175 200 Transportadores esteira e correia 125 150 75 43 TENSÕES ADMISSÍVEIS Neste subtema serão avaliados e determinados os valores máximos de tensão do material para assim poder determinar qual material poderá ser utilizado na fabricação de uma ECDR Veja a seguir a tabela 48 com especificações das tensões admissíveis para os materiais Tabela 48 Tensões ideais para os materiais no dimensionamento de engrenagens MATERIAL Mpa 𝑵 𝒎𝒎𝟐 FoFo cinzento 40 FoFo nodular 80 Aço fundido 90 SAE 10101020 90 SAE 10401050 120 SAE 43204340 170 SAE 86208640 200 Mat Sintético Resinas 35 Fonte adaptado de MELCONIAN 2011 Algumas recomendações são indicadas Recomendação 1 O projeto ideal é aquele em que a tensão atuante no pé do dente está bem próxima da tensão admissível no seu limite inferior Se a tensão atuante estiver acima da tensão admissível 𝝈 a engrenagem pode não suportar a transmissão vindo a romper na base do dente prematuramente Se por outro lado a tensão atuante estiver bem aquém da tensão admissível a engrenagem estará superdimensionada tornandose antieconômica Recomendação 2 Ângulo de pressão 𝛼 Observe o par de dentes apresentado na Figura 414 a seguir 76 Iniciam o contato no ponto A A cinemática do mecanismo faz com que o ponto A descreva a trajetória AB No ponto B termina o contato entre os dentes O segmento de reta AB descrito pela trajetória do ponto de contato e a tangente comum aos diâmetros primitivos das engrenagens define o ângulo da pressão Pela norma DIN 867 recomendase a utilização do ângulo de pressão α 20 Figura 414 Trajetória demonstrada desde seu o início até o fim do contato entre dentes Fonte SHIGLEY 2011 Recomendação 3 A seguir serão apresentadas as Engrenagens com perfil cicloidal e as teorias relacionadas a elas Suas representações podem ser vistas nas figuras 415 416 417 e 418 Aplicações Esse tipo de engrenagem é limitada às construções mecânicas podendo ser encontrada em bombas ventiladores volumétricos relógios e aparelhos de precisão 77 Processos de Fabricação A engrenagem cicloidal é obtida por meio de estampagem trefilação brochamento ou injeção mecânica fina por fresamento ou aplainamento As ferramentas são mais caras pois possuem flancos retos O processo de fabricação por ser mais preciso tornase mais caro Curva Cicloidal Posição inicial Figura 415 Ambas as Figuras representam um contato entre engrenagens com curva cicloidal A curva cicloidal é obtida fazendo rolar o círculo 1 sobre o círculo 2 sem que ocorra escorregamento A trajetória do ponto A no movimento descreve a curva cicloidal Círculo 1 em movimento e Círculo 2 fixo Observe que à medida que o círculo 1 rola sem escorregamento sobre a periferia do círculo 2 o ponto A se desloca para a posição A1 formando o arco A A1 que representa parte da curva cicloidal A parte pontilhada da trajetória do ponto A é a trajetória a ser descrita pelo ponto na sequência do movimento Fonte SHIGLEY 2011 78 Engrenagem curva de envolvente A maioria absoluta das engrenagens utilizadas nas construções mecânicas é constituída de dentadura com perfil envolvente Isso ocorre em virtude de o processo de fabricação ser mais simples resultando em um menor custo Figura 416 Representação de um dente da engrenagem curva de envolvente Fonte SHIGLEY 2011 Para entender a representação da Figura 416 apresentada acima os seguintes pontos têm sua nomenclatura e sua teoria das características geométricas Ponto 1 Corda def é enrolada ao redor do cilindro e mantida esticada Ponto 2 Ponto b na corda é o ponto traçador ou seja a medida que a corda é enrolada e desenrolada ao redor do cilindro esse ponto irá traçar a curva evolvente ac Ponto 3 No ponto b o raio é exatamente a distância be Ponto 4 Raio de curvatura da evolvente é zero em a e um máximo em c 79 Ponto 5 de é normal em relação à evolvente em todos os pontos da intersecção e ao mesmo tempo sempre tangente ao cilindro A Seguindo a sequência de detalhamento das características geométricas para aplicação seguimos com o exemplo da Curva Envolvente e o quanto o início desta curva será considerado sendo apresentado a seguir na Figura 417 Figura 417 Engrenamento com dentadura de perfil evolvente Fonte SHIGLEY 2011 A seguir na Figura 418 temos o exemplo da utilização de uma engrenagem cicloidal com o perfil envolvente comumente utilizado em relógios 80 Figura 418 Perfil do engrenamento cicloidal normalmente utilizado em relógios Fonte SHIGLEY 2011 Vamos Aplicar Exercício Estudo de Caso Dimensionamento de engrenagens ECDR Roteiro para o dimensionamento de um par de engrenagens O pinhão engrenagem menor Item 1 da Figura 419 é o dimensionado pois se ele resistir ao esforço aplicado a coroa engrenagem maior Item 2 da Figura 419 suportará com folga a mesma carga por ser uma engrenagem maior Figura 419 Sistema Mecânico de transmissão de movimento entre pinhão e coroa Ambas são ECDR Fonte MELCONIAN 2011 Dimensionamento do pinhão Procedimento 81 1 Critério de pressão desgaste Para que não haja a ocorrência de uma Fadiga Superficial Crateração conforme Figura 420 deverão ser consideradas no cálculo durante o dimensionamento da engrenagem as seguintes etapas para realizar um bom e seguro projeto de engrenagens É importante lembrar que estamos aprendendo sobre engrenagens cilíndricas de Dentes Retos Figura 420 Ocorrência da Fadiga Superficial denominada de Crateração nos dentes de uma ECDR Fonte ANDRADE SD 11 Torque no pinhão 𝑀𝑇 30 𝜋 𝑃 𝑛 𝑁 𝑚 12 Relação de transmissão i 𝑖 𝑍2 𝑍1 13 Pressão admissível Padm deverá ser calculada conforme apresentado na equação a seguir e como foi visto na Etapa 2 Para o Dimensionamento de ECDR Pressão admissível 𝑝𝑎𝑑𝑚𝑖𝑠𝑠í𝑣𝑒𝑙 Para determinar seu valor deverão ser determinadas as seguintes variáveis Dureza pelo método Brinell e o fator de durabilidade padm 0487 HB W1 6 N mm2 82 131 Determinar a dureza Para a equação da tensão admissível será utilizado o valor de dureza pelo método Brinell que é obtido conforme exemplificado nas Tabelas 42 e 43 132 Fator de durabilidade W 𝑊 60 𝑛𝑝ℎ 106 Isolando o Fator de Durabilidade W 𝑊 1 6 𝑊 6 𝑊0168 133 Cálculo da pressão admissível Como foi calculado no item 13 deste exercício 𝑝𝑎𝑑𝑚 0487 𝐻𝐵 𝑊 1 6 Poderá ser calculado o valor da Máxima Tensão admissível para o projeto da engrenagem ECDR 134 Fator de serviço ϕ Obtémse na tabela AGMA Representados nas Tabelas 46 e 47 Ex O fator de serviço ϕ para eixo de transmissão e carga uniforme para funcionamento de 10 h diárias é Ao consultar o valor de AGMA à disposição em catálogos de fabricantes de engrenagens ou elementos aplicado a um sistema mecânico ϕ 1 eixo de transmissão carga uniforme 10hdia ϕ 1 tabela AGMA 14 Volume mínimo do pinhão Para determina o volume do Pé dos Dentes em engrenagens s ECDR utilizase a seguinte equação 83 b1 d0 2 572 105 MT padm2 i 1 i 014 φ Unidades no Sistema Internacional SI Índice Denominase x o 2 membro da equação Temse então Volume mínimo do pinhão 𝑏1 𝑑0 2 𝑥 15 Módulo do engrenamento O módulo do engrenamento é determinado por meio de 𝑏1 𝑑0 2 𝑥 Eq I Volume mínimo do pinhão 𝑏1 𝑑01 𝑦 𝑏1 𝑦 𝑑01 Eq II Substituindo II em I tem se 𝑦 𝑑0 𝑑01 2 𝑥 𝑑01 3 𝑥 𝑦 𝑑01 𝑥 𝑦 3 O módulo do engrenamento é determinado pela expressão do diâmetro primitivo 𝑑01 𝑚 𝑍1 Assim 𝑚 𝑑01 𝑍1 O módulo a ser utilizado será o normalizado mais próximo ao módulo calculado que será obtido por meio da tabela de módulos normalizados DIN780 84 𝑚𝑛 Módulo normalizado módulo da ferramenta que vai usinar a engrenagem 16 Diâmetro primitivo recalculado Definido o módulo da ferramenta é recalculado o diâmetro primitivo por intermédio de 𝑑01 𝑅 𝑚𝑛 𝑍1 17 Largura do pinhão 𝑏1 𝑥 𝑑01 𝑅 2 2 Critério de resistência à flexão no pé do dente A tensão máxima no pé do dente é expressa por meio de Figura 421 Apresenta a força tangencial aplicada e o esforço gerado no pé do dente Fonte SHIGLEY 2011 Considerando a equação que define a máxima tensão no pé do dente da engrenagem onde também é possível selecionar a melhor matéria prima para produção de uma engrenagem σmáx Ft q φ b mn σmaterial 85 21 Força tangencial FT 𝐹𝑇 2 𝑀𝑇1 𝑑01 2 𝑀𝑇2 𝑑02 𝑁 22 Fator de forma q Obtémse por meio da tabela 45 apresentada anteriormente neste Bloco 23 Módulo normalizado mn Obtémse por meio da tabela 44 24 Largura do pinhão b Mesmo do 18 Largura do pinhão b1 X d01 R 2 25 Por meio da equação da Tensão máxima atuante no pé do dente 𝝈𝒎á𝒙 e o valor da Tensão do Material 𝝈𝒎𝒂𝒕𝒆𝒓𝒊𝒂𝒍 é obtido o valor da largura do Pinhão b Ft q φ σmáx mn σmaterial Vamos Aplicar Para condição de aprendizagem no exercício proposto a seguir estará as informações dos valores das variáveis que serão aplicadas no dimensionamento que nesse bloco será realizado para uma Engrenagem de Dentes Retos ECDR Exercício 1 Dimensionar o par de engrenagens cilíndricas de dentes retos ECDR para que possa atuar com segurança na transmissão especificada em seguida A transmissão será acionada por um motor de P 15 CV 11 kW que atua com uma rotação de 1140 rpm ω 38 πrads O material a ser utilizado é o SAE 4340 A dureza específica é 58 HRC e a duração prevista para 10000h 86 As engrenagens atuarão em eixos de transmissão com carga uniforme com o tempo de serviço máximo de 10h diárias Figura 422 Sistema Mecânico de transmissão de movimento entre pinhão e coroa ambas são ECDR Fonte MELCONIAN 2011 Considere 𝑏1 𝑑01 025 Relação entre a largura e o diâmetro primitivo da engrenagem 𝛼 20 Ângulo de pressão 𝑍1 29 dentes pinhão 𝑍2 110 dentes coroa 11 Torque no pinhão 𝑀𝑇 30 𝜋 𝑃 𝑛 𝑁 𝑚 𝑀𝑇 30 𝜋 11000 1140 𝑁 𝑚 𝑀𝑇 9214 𝑁 𝑚 𝑀𝑇 92141 𝑁 𝑚𝑚 12 Relação de transmissão i 𝑖 𝑍2 𝑍1 𝑖 110 29 3793 𝑖 379 87 13 Pressão admissível 131 Fator de durabilidade W 𝑊 60 𝑛𝑝 ℎ 106 𝑊 60 1140 1 104 106 𝑊 60 1140 1 102 𝑊 684 como 𝑊 1 6 297 132 Cálculo da pressão padm 0487 HB W 1 6 𝑝𝑎𝑑𝑚 0487 6000 297 𝑝𝑎𝑑𝑚 0487 6000 297 𝑝𝑎𝑑𝑚 983838 984 102 𝑁 𝑚𝑚2 A dureza de 58 HRC corresponde a 6000 HB ou seja 6000 Nmm2 14 Fator de serviço ϕ Obtémse na tabela AGMA O fator de serviço ϕ para eixo de transmissão carga uniforme para funcionamento de 10 h diárias é ϕ 1 tabela AGMA 88 15 Volume mínimo do pinhão 𝑏1 𝑑0 2 572 105 𝑀𝑇 𝑝𝑎𝑑𝑚2 𝑖 1 𝑖 014 𝜑 𝑏1 𝑑0 2 572 105 92140 984 1022 379 1 379 014 1 𝑏1 𝑑0 2 572 105 92140 9842 1022 479 393 1 𝐿𝑒𝑚𝑏𝑟𝑎𝑛𝑑𝑜 𝑎 𝑐𝑜𝑛𝑑𝑖çã𝑜 𝑒𝑥𝑝𝑜𝑛𝑒𝑛𝑐𝑖𝑎𝑙 1022 104 𝑏1 𝑑0 2 66343 𝑚𝑚3 𝑏1 𝑑0 2 66343 104 𝑚𝑚3 16 Módulo de engrenamento b1 d0 2 66343 mm3 I b1 d01 025 b1 025 d01 II Substituindo II em I 025 d01 d0 2 66343 mm3 d01 3 66343 025 d01 66343 025 265372 mm3 d01 265372 mm3 3 d01 6426 mm Portanto 𝑚 𝑑01 𝑍1 643 29 𝑚 221 𝑚𝑚 89 Por meio da DIN 780 conforme tabela 47 incremento de 025 fixase o módulo da ferramenta em 𝑚𝑛 225 𝑚𝑚 Módulo normalizado DIN 780 17 Recálculo do diâmetro primitivo do pinhão 𝑑01𝑅 𝑚𝑛 𝑍1 𝑑01𝑅 225 29 𝑑01𝑅 6525 𝑚𝑚 18 Largura do pinhão 𝑏1 𝑑01𝑅 2 66343 𝑏1 66343 𝑑01𝑅 2 66343 65252 𝑏1 16 mm 2 Resistência à flexão no pé do dente 21 Força tangencial FT 𝐹𝑇 2 𝑀𝑇1 𝑑01𝑅 𝑁 𝐹𝑇 2 92140 𝑁𝑚𝑚 6525 𝑚𝑚 𝐹𝑇 285 𝑁 22 Fator de forma q Como Z1 29 dentes encontramos na tabela fator q 30835 23 Fator de serviço ϕ Obtémse na tabela AGMA 90 O fator de serviço ϕ para eixo de transmissão carga uniforme para funcionamento de 10 h diárias é Ao consultar o valor de AGMA à disposição em catálogos de fabricantes de engrenagens ou elementos aplicado a um sistema mecânico ϕ 1 eixo de transmissão carga uniforme 10hdia ϕ 1 tabela AGMA 24 Módulo normalizado O mesmo do item 16 de acordo com tabela 46 𝑚𝑛 225 mm DIN 780 25 Largura do pinhão b O mesmo do item 18 𝑏1 16 𝑚𝑚 26 Tensão máxima atuante no pé do dente 𝜎𝑚á𝑥 𝐹𝑡 𝑞 𝜑 𝑏 𝑚𝑛 𝜎𝑚𝑎𝑡𝑒𝑟𝑖𝑎𝑙 𝜎𝑚á𝑥 2825 30835 1 16 225 𝜎𝑚𝑎𝑡𝑒𝑟𝑖𝑎𝑙 𝜎𝑚á𝑥 242 𝑁 𝑚𝑚2 27 Análise do dimensionamento Como a tensão máxima atuante é superior à tensão admissível do material concluise que o pinhão será redimensionado 𝜎4340 170 𝑁 𝑚𝑚2 de acordo com a tabela 48 𝜎𝑚á𝑥 242 𝑁 𝑚𝑚2 𝜎4340 170 𝑁 𝑚𝑚2 91 Com a condição não atendida da Tensão máxima aplicada no pé do dente da engrenagem ECDR o valor da tensão do material inicialmente selecionado não atenderá aos esforços deste elemento mecânico a ECDR Assim o recálculo terá de ser feito com os seguintes itens a serem alterados como sugestão Selecionar outro material exemplo Aço 1020 𝜎1020 300 𝑁 𝑚𝑚2 𝜎4340 170 𝑁 𝑚𝑚2 assim atenderá a solicitação de flexão no pé do dente Alterar Largura do pé do dente b Número de dentes Z ou Diâmetro primitivo da engrenagem 𝑑0 Assim deverá realizar todo o roteiro de cálculo sugerido 28 Redimensionamento do pinhão 281 1ª Hipótese mantémse o módulo e fazse o redimensionamento da largura b utilizando a tensão admissível do material SAE 4340 Como σ4340 170 N mm2 vem que b Ft q φ σ4340 mn b 2285 30835 1 170 225 b 23 mm Para esse dimensionamento temos um pinhão com as seguintes características Número de dentes Z1 29 dentes Módulo mn 225 mm Diâmetro primitivo 𝑑01𝑅 6525 𝑚𝑚 Largura 𝑏 23 𝑚𝑚 282 Relação largura b diâmetro primitivo do b1 d01 23 6525 035 92 Portanto b1 d01 035 12 a engrenagem está dentro das especificações 283 2ª hipótese mantémse a largura alterando o módulo da 𝒃𝟏 16 mm engrenagem e consequentemente o diâmetro primitivo e a força tangencial 284 Alterase também o valor do módulo normalizado 𝒎𝒏 275 mm pois a tensão admissível está bem aquém da tensão máxima obtida 285 Diâmetro primitivo d01R Z1 mn d01R 29 275 d01R 7975 mm 286 Força tangencial FT FT 2 MT1 d01R N FT 2 92140 7975 N FT 2310 N 287 Tensão máxima atuante σmáx Ft q φ b1 mn σmáx 2310 30835 1 16 275 σmáx 162 N mm2 288 Análise do dimensionamento Como a 𝜎𝑚á𝑥 162 𝑁 𝑚𝑚2 𝜎4340 170 𝑁 𝑚𝑚2 concluise que a engrenagem está em perfeitas condições de utilização 93 289 Relação entre largura e diâmetro primitivo 𝑏1 𝑑01 16 7975 02 Portanto 𝑏1 𝑑01 02 12 a relação encontrase dentro da especificação indicada Para esse dimensionamento temos um pinhão com as seguintes características Número de dentes 𝑍1 29 dentes Módulo 𝑚𝑛 275 mm Diâmetro primitivo 𝑑01𝑅 7975 𝑚𝑚 Largura 𝑏 16 𝑚𝑚 Conforme apresentado na Tabela 41 temos as equações para determinar os valores das dimensões requerida nas Normas DIN 862 e 867 Já a Tabela 49 a seguir se refere as características geométricas de uma ECDR de acordo com as Normas DIN 862 e 867 94 Tabela 49 Formulário das variáveis fundamentais do projeto de uma ECDR Fonte adaptado de MELCONIAN 2011 A Tabela 410 a seguir é uma continuação da Tabela 49 Tabela 410 continuação Formulário das variáveis fundamentais do projeto de uma ECDR Formulário Pinhão mm Coroa mm Espessura do dente no primitivo folga nula no flanco 𝑆0 𝑡0 2 𝑆0 𝑡0 2 864 2 432 𝑆0 𝑡0 2 864 2 432 Formulário Pinhão mm Coroa mm Módulo normalizado DIN 780 𝑚𝑛 275 𝑚𝑛 275 Passo 𝑡0 𝑡0 𝑚𝑛 𝜋 𝑡0 275 𝜋 864 𝑡0 275 𝜋 864 Vão entre os dentes no primitivo folga nula no flanco 𝑙0 𝑡0 2 𝑙0 864 2 432 𝑙0 864 2 432 Altura da cabeça do dente ℎ𝑘 𝑚𝑛 ℎ𝑘 275 ℎ𝑘 275 Altura comum do dente ℎ𝑓 12 𝑚𝑛 ℎ𝑓 12 275 33 ℎ𝑓 12 275 33 Altura comum do dente ℎ 2 𝑚𝑛 ℎ 2 275 55 ℎ 2 275 55 Altura total do dente ℎ𝑧 22 𝑚𝑛 ℎ𝑧 22 275 605 ℎ𝑧 22 275 605 95 Folga da cabeça 𝑆𝐾 02 𝑚𝑛 𝑆𝐾 02 275 055 𝑆𝐾 02 275 055 Diâmetro primitivo 𝑑0 𝑑0 𝑚𝑛 𝑍 𝑑0 𝑚𝑛 𝑍1 𝑑0 275 29 𝑑0 7975 𝑑0 𝑚𝑛 𝑍2 𝑑0 275 110 𝑑0 3025 Fonte adaptado de MELCONIAN 2011 A Tabela 411 a seguir é uma continuação da Tabela 410 e se refere as características geométricas de uma ECDR de acordo com as Normas DIN 862 e 867 Tabela 411 continuação Formulário das variáveis fundamentais do projeto de uma ECDR Fonte adaptado de MELCONIAN 2011 Formulário Pinhão mm Coroa mm Diâmetro de base 𝑑𝑔 𝑑𝑔 𝑑0 𝑐𝑜𝑠𝛼0 𝑑𝑔1 𝑑01 𝑐𝑜𝑠𝛼0 𝑑𝑔1 7975 𝑐𝑜𝑠 20 𝑑𝑔1 7494 𝑑𝑔2 𝑑02 𝑐𝑜𝑠𝛼0 𝑑𝑔2 3025 𝑐𝑜𝑠 20 𝑑𝑔2 28425 Diâmetro interno 𝑑𝑓 𝑑0 24𝑚𝑛 𝑑𝑓1 𝑑01 24𝑚𝑛 𝑑𝑓1 7975 24 275 𝑑𝑓1 7315 𝑑𝑓2 𝑑02 24𝑚𝑛 𝑑𝑓2 3025 24 275 𝑑𝑓1 2959 Diâmetro externo 𝑑𝑘 𝑑0 2𝑚𝑛 𝑑𝑘1 𝑑01 2𝑚𝑛 𝑑𝑘1 7975 2 275 𝑑𝑘1 8525 𝑑𝑘2 𝑑02 2𝑚𝑛 𝑑𝑘2 3025 2 275 𝑑𝑘2 308 Distância entre centros 𝐶𝑐 𝑑01 𝑑02 2 7975 3025 2 𝐶𝑐 19112 Largura das engrenagens 𝑏1 𝑏2 16 96 Conclusão Neste bloco nós estudamos o vasto universo dos elementos de máquinas Além disso revisamos a disciplina de resistência dos materiais Foi apresentado o elemento engrenagens como referência na aplicação de um Projeto Mecânico frente as etapas que devem ser seguidas abordando a seleção do material o tipo de processo de fabricação utilizado as geometrias e como dimensionar para obter uma Engrenagem Cilíndrica de Dentes Retos ECDR para assim termos o completo Memorial de Cálculo do elemento mecânico em questão e que neste exemplo compõe um Sistema Mecânico Referências Bibliográficas ANDRADE A S Elementos Orgânicos de Máquinas II UFP SD KIMINAMI C S CASTRO W B OLIVEIRA M F Introdução aos processos de fabricação de produtos metálicos São Paulo Blucher 2013 MELCONIAN S Elementos de Máquinas 9ª ed São Paulo Erica 2011 MOTT R L Elementos de máquinas em projetos mecânicos São Paulo 2015 NORTON R L Projetos de Máquinas Uma Abordagem Integrada 4º ed Porto Alegre Bookman 2013 SHIGLEY J E BUDYNAS R G NISBETT J K Elementos de máquinas de Shigley 8ª ed São Paulo AMGH Editora Ltda 2011 97 5 CONCEITOS EM ENGRENAGENS CILÍNDRICAS DE DENTES HELICOIDAIS ECDH Este Bloco em sua grande parte será uma extensão dos conceitos apresentados no Bloco 4 Engrenagens Cilíndricas de Dentes Retos ECDR Porém ao analisar já para a condição de projeto de uma Engrenagem Cilíndricas de Dentes Helicoidais ECDH sua aplicação e geometria possuem particularidades que devem ser seguidas no seu dimensionamento e também onde quer que seja aplicado no conjunto de um sistema mecânico em que a engrenagem será utilizada Ainda haverá a condição de mais um ângulo denominado como 𝜷 devido à inclinação apresentada nos dentes desta engrenagem e que altera a sua geometria além de manter ângulo de pressão 𝜶 assim a mudança na geometria nos dentes e a condição de mais um ângulo serão apresentados e também como deverá ser o dimensionamento para realizar um correto projeto mecânico 51 CARACTERÍSTICAS FUNDAMENTAIS DAS ENGRENAGENS DO MODELO ECDH As engrenagens ECDH são caracterizadas pela inclinação dos dentes em relação ao eixo geométrico da roda e suas vantagens são a alta resistência e trabalho silencioso São aplicadas quando se faz necessário resistir a grandes esforços como em caixa de redução de câmbio etc Também permitem transmitir potências maiores com rotação variada Dentre os tipos de engrenagens helicoidais ECDH as engrenagens para rosca sem fim se destacam quando a redução de velocidade na transmissão do movimento se faz necessária Podemos concluir que as Engrenagens Cilíndricas de Dentes Helicoidais ECDH possuem de forma geral como característica a transmissão de rotação entre eixos diversos não paralelos além de apresentarem um ruído menor do que as Engrenagens Cilíndricas de Dentes Retos ECDR 98 Veja a seguir os critérios fundamentais das Engrenagens Fabricação Qualidade Características gerais Tipos de engrenagens Engrenagens cilíndricas de dentes retos Características geométricas Dimensionamento 511 Processos de Fabricação de Engrenagens Os processos de fabricação de engrenagens podem ser realizados por a Usinagem b Fundição c Sem retirada de cavaco 512 Qualidade das Engrenagens O conceito de qualidade das engrenagens ocorre por meio das Normas DIN 862 e 867 que especificam as 12 principais características de qualidade Qualidade 1 Atualmente não utilizada pode ser usada quando não há uma referência da aplicação desta Engrenagem Qualidade 2 São utilizadas em indústria de precisão Relojoaria e aparelhos de precisão Qualidade 3 São utilizadas como padrão em laboratórios de controle Assim são consideradas engrenagens de precisão Qualidade 4 Utilizase na fabricação de engrenagens padrão engrenagens para aviação e engrenagens de alta precisão para torres de radar 99 Qualidade 5 São utilizadas em aviões máquina operatrizes instrumentos de medida turbinas etc Qualidade 6 Utilizase em automóveis ônibus caminhões navios e mecanismo de alta rotação Qualidade 7 Engrenagens Sheivadas são empregadas em veículos máquinas operatrizes máquinas de levantamento e transporte etc Qualidade 8 e 9 São as mais empregadas pois não precisam ser retificadas Utilizamse em máquinas gerais Qualidade 10 a 12 São engrenagens mais rústicas normalmente utilizadas em máquinas agrícolas Podese concluir que das 12 principais características de qualidade a Qualidade 1 é utilizada para aplicações com elevada precisão e segue até a Qualidade 12 cuja aplicação será mais rústica por exemplo em máquinas agrícolas moinhos de moagem de cana de açúcar etc 513 Aplicação Tipos e a Geometria de Engrenagens Cilíndricas de Dentes Helicoidais ECDH Os principais critérios e condições de aplicação de engrenagens estão descritos na norma DIN 862 e 867 Estas normas referenciam os critérios de Geometria De acordo com a engrenagem das figuras 52 e 53 e também especificam o grau de qualidade materiais de fabricação quais processos de fabricação podem ser utilizados e por fim as dimensões que terá a engrenagem a ser projetada para que atenda aos requisitos de resistência em condições de diversos esforços mecânicos e para que possa aumentar a sua vida útil As Engrenagens Cilíndricas de Dentes Helicoidais se apresentam em três tipos de nomenclaturas para as formas de acoplamento durante a transmissão de energia 100 Figura 51 a Exemplo de Engrenagem Cilíndrica de Dentes Helicoidais ECDH Engrenagens Externas Fonte MELCONIAN 2011 Figura 51 b Exemplo de Engrenagem Cilíndrica de Dentes Helicoidais ECDH Engrenagens Internas Fonte MELCONIAN 2011 Figura 51 c Exemplo de Engrenagem Cilíndrica de Dentes Helicoidais ECDH Engrenagens Cônicas Fonte MELCONIAN 2011 101 O elemento mecânico em análise são as Engrenagens Cilíndricas de Dentes Helicoidais ECDH que serão dimensionadas conforme DIN 862 e 867 As características geométricas de um elemento mecânico como as engrenagens podem variar Dessa forma ocorrerá a variação das referências de nomenclatura e dos pontos de dimensões obtidas por meio do cálculo de projeto Este cálculo define a propriedade mecânica até sua ruptura e tempo de duração da vida útil e isso depende do tipo de aplicação e horas diárias de funcionamento Você poderá ver esses dados mais à frente nas Tabelas 511 e 512 AGMA 𝝋 Figura 52 Representação da geometria e em detalhe a inclinação 𝜷 de uma ECDH Fonte SHIGLEY 2011 102 Figura 53 Apresenta todas as dimensões com geometria e as nomenclaturas de uma ECDH Fonte SHIGLEY 2011 Diâmetros principais Diâmetro primitivo 𝑑0 𝑍 𝑚𝑠 Diâmetro de base 𝑑𝑔 𝑑0 𝑐𝑜𝑠 𝛼𝑠0 Diâmetro interno pé dente 𝑑𝑓 𝑑0 2 ℎ𝑓 Diâmetro externo cabeça do dente 𝑑𝐾 𝑑0 2 ℎ𝑘 Para determinar os diâmetros principais suas características geométricas e seus valores dimensionais de acordo com a Norma DIN 862 e 867 você verá na Tabela 51 as principais equações que deverão ser consideradas pelo projetista no Memorial de Cálculo do Projeto de um Sistema Mecânico que neste caso será da Engrenagem Cilíndricas de Dentes Helicoidais ECDH 103 Tabela 51 Equações de elementos que compõe a ECDH Denominação Formulário Número Imaginário de Dentes 𝑍1 𝑍 𝑐𝑜𝑠 𝛽03 Avanço de Dente 𝑆 𝑏 𝑡𝑎𝑔 𝛽0 Diâmetro Primitivo 𝑑0 𝑍 𝑚𝑠 Diâmetro Externo 𝑑𝐾 𝑑0 2 ℎ𝑘 Diâmetro do Pé do Dente 𝑑𝑓 𝑑0 2 ℎ𝑓 Diâmetro de Base 𝑑𝑔 𝑑0 𝑐𝑜𝑠 𝛼𝑠0 Fonte Adaptado de Melconian 2011 Tabela 52 continuação Equações de elementos que compõe a ECDH Denominação Formulário Altura da Cabeça do Dente ℎ𝑘 𝑚𝑛0 Altura do Pé do Dente ℎ𝑓 12 𝑚𝑛0 Altura Total do Dente ℎ𝑍 22 𝑚𝑛0 Folga da Cabeça 𝑆𝑘 02 𝑚𝑛0 Ângulo de Hélice 𝛽0 𝑆𝑒𝑐𝛽0 𝑑0 𝑚𝑛0 2 𝐴 𝑍1 𝑚𝑛0 𝑖 1 104 Ângulo de Pressão Normal 𝛼𝑛0 𝛼𝑛0 20 DIN 867 Ângulo de Pressão Frontal 𝛼𝑠0 𝑡𝑎𝑔 𝛼𝑠0 𝑡𝑎𝑔 𝛼𝑛0 𝑐𝑜𝑠 𝛽0 Distância Centro a Centro 𝐶𝐶 𝑍1 𝑍2 2 𝑚𝑠 Raio Imaginário Medido no Plano Normal 𝑟𝑛 𝑟0 𝑐𝑜𝑠 𝛽0 2 Fonte adaptado de MELCONIAN 2011 Tabela 53 continuação Equações de elementos que compõe a ECDH Denominação Formulário Módulo Normal normalizado 𝑚𝑛0 𝑇0 𝜋 Módulo Frontal 𝑚𝑠0 𝑚𝑛0 𝑐𝑜𝑠 𝛽0 𝑚𝑛0 𝑠𝑒𝑐 𝛽0 Passo Frontal 𝑡𝑠0 𝑚𝑠 𝜋 Passo Normal 𝑡𝑛0 𝑚𝑛0 𝜋 Espessura do Dente Frontal 𝑆𝑆0 𝑡𝑠0 2 Folga nula no flanco Vão entre Dentes no Frontal 𝑙𝑆0 𝑡𝑠0 2 Folga nula no flanco 105 Espessura do Dente Normal 𝑆𝑛0 𝑡𝑛0 2 Folga nula no flanco Vão entre Dentes Normais 𝑙𝑛0 𝑡𝑛0 2 Folga nula no flanco Fonte adaptado de MELCONIAN 2011 52 DIMENSIONAMENTO DE UMA ENGRENAGEM CILÍDRICA DE DENTES HELICOIDAIS ECDH Neste item serão apresentadas as principais equações que serão utilizadas no dimensionamento de uma ECDH e que servem para atender a aplicação deste elemento mecânico que irá compor uma caixa redutora de dupla redução conforme Figura 54 Veja a seguir as etapas de um projeto de elemento mecânico de Engrenagens Cilíndricas de Dentes Helicoidais ECDH Etapa 1 Dimensionamento com o Critério de desgaste Figura 54 Redutor de Dupla Redução com Engrenagens Cilíndricas de Dentes Helicoidais Fonte ANDRADE SD Critério de desgaste A seguinte expressão deve ser utilizada no dimensionamento de pinhões com ângulo de pressão 𝛼20 e número de dentes de 18 a 40 Material aço 106 b d0 2 02 f 2 Mt p2 adm φ p i 1 i í𝑛𝑑𝑖𝑐𝑒𝑒𝑛𝑔𝑟𝑒𝑛𝑎𝑔𝑒𝑛𝑠 𝑒𝑥𝑡𝑒𝑟𝑛𝑎𝑠 í𝑛𝑑𝑖𝑐𝑒𝑒𝑛𝑔𝑟𝑒𝑛𝑎𝑔𝑒𝑛𝑠 𝑖𝑛𝑡𝑒𝑟𝑛𝑎𝑠 𝑜𝑢 𝑝𝑙𝑎𝑛𝑒𝑡a𝑟𝑖𝑎𝑠 Em que b Largura do pinhão mm d0 Diâmetro primitivo do pinhão mm f Fator de características elásticas do par adimensional 𝒊 Relação de transmissão adimensional Padm Pressão admissível de contato Nmm2 𝝋 p Fator de correlação de hélice pressão adimensional O fator de correção 𝝋𝒑 utilizado para o critério de pressão obtémse por meio do ângulo de correção de hélice 𝜷𝟎 na tabela a seguir Tabela 54 Tabela de correlação entre o ângulo de hélice 𝜷𝟎 e o fator de correção 𝝋𝒓 𝜑𝑝 100 111 122 131 140 147 154 160 166 171 𝛽0 0 5 10 15 20 25 30 35 40 45 Fonte adaptado de MELCONIAN 2011 Etapa 2 Para o Dimensionamento de ECDH Pressão admissível padmissível padm 0487 HB W1 6 N mm2 107 No exemplo que vamos aplicar neste Bloco serão fornecidos os valores de Dureza Horas de atividade do elemento mecânico e seu Valor de utilização Agma 𝝋 no enunciado do Estudo de Caso para Dimensionar uma ECDH Assim falta o valor do Fator de Durabilidade W e seu cálculo se dá por meio da equação abaixo Fator de durabilidade W W 60 np h 106 Em que np Rotação do pinhão rpm h Duração do par horas HB Dureza Brinell Nmm2 Etapa 3 Fator de características elásticas 𝑓 Para ângulo de pressão 𝜶 20 Quando é necessário obter o valor do Fator de Características Elásticas f deve ser considerado o modelo da engrenagem ECDH e a relação de engrenamento para a determinação do f apresentados na Tabela 55 Tabela 55 Tabela de correlação entre a engrenagem seu material e seu fator de característica elástica Material E GPa Fator f Pinhão de aço Coroa de aço E 210 E 210 1512 Pinhão de aço Coroa de FoFo E 210 E 105 1234 108 Pinhão de FoFo Coroa de FoFo E 105 E 105 1069 Fonte adaptado de MELCONIAN 2011 A tabela 56 apresenta a correlação entre os tipos de material que podem ser utilizados na confecção de uma ECDH e os valores determinados por meio do método de ensaio de dureza Brinell Vale lembrar que não há uma equação de conversão entre os métodos dos Ensaios de Dureza mas existe uma tabela que correlaciona o valor obtido em diferentes métodos utilizados no ensaio Na tabela 56 são apresentados como referência os Valores de Dureza HBrinell mas para os tipos de aços descritos a seguir deverá ser utilizado a tabela Rockwell C HRc mesmo sendo só como referência Aços SAE 4320 SAE 4340 SAE 8620 e SAE 8640 temperados Tabela 56 Correlação entre os valores obtidos no Ensaio de Dureza do tipo Brinell Material HBRINELL 𝑵 𝒎𝒎𝟐 Aço fundido tipo 2 1700 2500 Aço fundido tipo 𝑩𝟐 1250 1500 Aço SAE 1020 1400 1750 Aço SAE 1040 1800 2300 Aço SAE 1050 2200 2600 Aço SAE 31453150 1900 2300 Aço SAE 4320 2000 4200 Aço SAE 4340 2600 6000 Aço SAE 8620 1700 2700 Aço SAE 8640 2000 6000 Aço fundido cinzento 1200 2400 Aço fundido nodular 1100 1400 Fonte adaptado de MELCONIAN 2011 109 Já a Tabela 57 apresenta o conceito de determinação dos valores obtidos nos Ensaios de Dureza Uma importante informação não há uma equação ou uma tabela para que se realize a conversão nos valores do Ensaio de Dureza pois cada valor é associado ao seu ensaio e tem particularidades de carga aplicada O elemento penetrador da superfície e a forma da impressão que será analisada de acordo com um método de ensaio junto com o valor de Dureza Brinnell HB solicitada na equação pode ser encontrado em catálogos ou até em certificados de fabricação do lote produzido de Aço ou Ferro Fundido Estes certificados ainda terão as informações de Composição Química e as Propriedades Mecânicas como Tenacidade e Dureza conforme exemplo da Tabela 57 Tabela 57 Valores de correlação entre os valores obtidos nos Ensaios de dureza Brinell Resistência 𝑁 𝑚𝑚2 Rockwell Impr mm Carga 30 kN Esfera Dureza HB 𝑁 𝑚𝑚2 Aço Carbono HB x 036 C Rc B Rb A Ra Shore Vickers 365 2270 997 29 104 646 39 279 370 2690 969 28 104 641 38 270 375 2620 943 26 103 636 37 263 380 2550 918 25 102 630 37 256 400 2290 824 21 98 608 33 229 Fonte adaptado de MELCONIAN 2011 Para o cálculo da expressão a seguir temos a Relação entre a Largura da engrenagem b e o Diâmetro primitivo 𝑑0 e é determinado o valor de 𝑏 𝑑0 Então para ECDH e para o bom dimensionamento da engrenagem haverá duas condições 1 Engrenagem Biapoiada o valor de 𝑏 𝑑0 12 Característica as duas extremidades do eixo são apoiadas 110 2 Engrenagem em Balanço o valor de 𝑏 𝑑0 075 Característica uma das extremidades do eixo é apoiada Confira como é a representação dessas expressões na figura 55 Figura 55 Representação das diferentes formas de fixar uma ECDH Fonte adaptado de MELCONIAN 2011 Na tabela 58 apresentada a seguir é definido o incremento no módulo após sua obtenção no cálculo do módulo de engrenamento de uma ECDH Este cálculo é usado para a fabricação da engrenagem no processo de fresamento e o módulo da ferramenta será o módulo da engrenagem somado ao incremento Tabela 58 Correlação entre os valores dos Módulos normalizados DIN 780 e o incremento Módulo mm Incremento mm 03 a 10 010 10 a 40 025 40 a 70 050 70 a 160 100 160 a 240 200 240 a 450 300 450 a 750 500 Fonte adaptado de MELCONIAN 2011 111 Etapa 4 Esforços de flexão no pé do dente e seus Tipos de Esforços gerados Normalmente para projetar escolhemos um critério para o dimensionamento e outro para a verificação No caso de engrenagens dimensionamos pelo desgaste e verificamos pelo critério de tensão no pé do dente Essa deve ser menor que a tensão admissível do material indicado Durante a atividade desta engrenagem em um sistema mecânico de transmissão de movimentos rotativos acontecerão esforços de flexão nos pés dos dentes da engrenagem ECDH Nas engrenagens cilíndricas de dentes helicoidais ECDH são gerados três esforços que geram uma Força de Flexão nos Pés dos Dentes da ECDH conforme apresentado na Figura 56 1 Força tangencial 2 Força radial 3 Força axial Figura 56 Representação da interação das forças distribuídas entre os dentes na ECDH Fonte SHIGLEY 2011 112 Então as seguintes equações serão aplicadas para obter o valor dos Esforços para o caso de uma Força Tangencial 𝐹𝑡 conforme a Figura 57 Segue 1 Força tangencial 𝐹𝑡 A carga tangencial Ft é responsável pelo movimento das engrenagens sendo também a carga que origina momento fletor tendendo por flexão o pé do dente A fórmula tangencial é determinada por 𝐹𝑡 𝑀𝑡 𝑟0 2𝑀𝑡 𝑑0 raio primitivo 𝑟0 𝑑0 2 Em que Ft força tangencial N MT torque N mm ro raio primitivo da engrenagem mm do diâmetro da engrenagem mm Figura 57 Apresenta a Força Tangencial aplicada e o esforço gerado no pé do dente Fonte SHIGLEY 2011 Força radial Fr Atua na direção radial da engrenagem É determinada por meio da tangente do ângulo c ângulo de pressão 113 tan 𝛼 𝐹𝑟 𝐹𝑡 Sendo Fr FT tag αS0 𝑁 Em que Fr carga radial N Ft carga tangencial N α ângulo de pressão graus Força axial 𝐹𝑎 Quando se utilizam engrenagens helicoidais cônicas ou parafuso sem fim surge outro esforço na transmissão que é a carga axial originada pela inclinação do ângulo da hélice sendo 𝛽0 representado na Figura 58 𝐹𝑎 𝐹𝑇 tag 𝛽0 ou 𝐹𝑎 𝐹𝑇𝑡𝑎g 𝛽0 N Figura 58 Apresenta as Forças aplicadas e o esforço gerado no pé do dente considerando a inclinação de 𝜷 Fonte SHIGLEY 2011 Força resultante 𝐹𝑛 114 É a resultante das cargas Ft e Fr sendo determinada por meio de Pitágoras como segue 𝐹𝑛 𝐹𝑡 2 𝐹𝑟 2 Em que Fn carga resultante N Fr carga radial N Ft carga tangencial N Ou ainda pelas reações cos α Ft Fn Fn Ft cos α sen α Fr Fn Fn Fr sen α As cargas radial e resultante serão importantes no dimensionamento de eixos e mancais sendo necessário o dimensionamento das engrenagens Etapa 5 Tensão máxima aplicada e a correlação entre Tensão Material usada na fabricação da ECDH e o valor do esforço de Tensão de flexão no pé do dente A tensão atuante no pé do dente deve ser menor ou igual à tensão admissível do material indicado Veja a seguir a fórmula que determina a intensidade da tensão máxima que a engrenagem sofrerá e que seu material de fabricação deverá resistir além de indicar os limites da Propriedades Mecânicas e a sua Vida Útil 𝜎𝑚á𝑥 𝐹𝑡 𝑞 𝑏 𝑚𝑛 𝑒 𝜑𝑟 𝜎𝑚𝑎𝑡𝑒𝑟𝑖𝑎𝑙 115 Em que Ft Força tangencial N q Fator de forma adimensional b Largura do pinhão mm Mn Módulo normal mm ϕ r Fator de correção de hélice adimensional e Fator de carga 080 e 150 adimensional Etapa 6 Fator de serviço 𝑒 e fator de correção de hélice 𝛗𝐫 Pelo fator de serviço 𝜑 da tabela AGMA determinase 𝑒 por intermédio de Sendo ϕ r fator de correção de hélice resistência Após ser obtido o fator de correção de hélice 𝜑𝑟 conforme apresentado anteriormente na Tabela 54 podemos determinar o valor do ângulo de hélice 𝛽0 por meio da tabela 59 Tabela 59 Tabela de correlação entre o ângulo de hélice 𝜷𝟎e o fator de correção 𝝋𝒓 Fonte Adaptado de Melconian 2011 𝝋𝒓 10 12 128 135 136 𝜷𝟎 0 5 10 15 a 25 25 a 45 𝑒 1 𝜑 116 Etapa 7 Para obtermos o valor do Fator de forma 𝑞 que está apresentado na tabela 59 o Cálculo do Número de Dentes Equivalentes 𝒛𝒆 da engrenagem ECDH deverá ser considerado antes conforme a equação a seguir Cálculo do número de dentes equivalente 𝒛𝒆 Assim o cálculo do número de dentes será pela expressão descrita a seguir 𝑧𝑒 𝑧1 cos𝛽03 Desta forma será obtido pela Tabela 510 o valor do fator de forma q e sua relação depende do número de dentes da engrenagem ECDH Tabela 510 Tabela de correlação entre o número de dentes e o fator de forma q Fonte SHIGLEY 2011 Uma observação Se o número de dentes for intermediário aos apresentados na Tabela 510 será necessário realizar a operação matemática de interpolação tanto no número de dentes Z quanto no Fator de Forma q Etapa 8 Obtémse nas tabelas a seguir o Valor dos Fatores de Serviço AGMA 𝜑 Este valor será considerado entre 2 condições ou seja 10 ou 24 horas de serviço para então obter o valor dos fatores de serviço AGMA conforme os exemplos apresentados abaixo nas Tabelas 511 e 512 117 Vale lembrar que os valores do Fator de Serviço AGMA ϕ de uma engrenagem ECDH como exemplificados nas Tabelas 511 e 512 ficam sempre à disposição em catálogos de fabricantes de engrenagens ou elementos de máquinas aplicado a um sistema mecânico Tabela 511 Tabelas de fatores de serviço AGMA ϕ Aplicações Serviço Horas de Atividade 10 h 24 h AGITADORES Líquidos 100 125 Misturadores de polpa 125 150 Semilíquidos de densidade variável 125 150 ALIMENTADORES Alimentadores helicoidais 125 150 Alimentadores recíprocos 175 200 Transportadores esteira e correia 125 150 Fonte adaptado de MELCONIAN 2011 Conforme apresentado na Tabela 512 as principais características se tornam variáveis fundamentais no dimensionamento bem como na correta seleção de valor de acordo com as horas de serviço Esta condição altera a vida útil do projeto de um sistema mecânico Tabela 512 Continuação do exemplo de Tabelas de fatores de serviço AGMA ϕ para o acionamento de motores a explosão e serviços intermitentes Motor Elétrico Motor Elétrico Motores a Explosão Multicilíndricos 10 h 3 h 3 h 10 h 24 h 100 050 100 125 150 125 100 125 150 175 175 150 175 200 225 Fonte adaptado de MELCONIAN 2011 Para finalizar este item veja a Tabela 513 que apresenta os valores das Tensões admissíveis para os materiais que serão utilizados na fabricação de uma engrenagem ECDH 118 Tabela 513 Tensões ideais para os materiais no dimensionamento de engrenagens MATERIAL Mpa 𝑵 𝒎𝒎𝟐 FoFo cinzento 40 FoFo nodular 80 Aço fundido 90 SAE 10101020 90 SAE 10401050 120 SAE 43204340 170 SAE 86208640 200 Mat Sintético Resinas 35 Fonte adaptado de MELCONIAN 2011 53 TENSÕES ADMISSÍVEIS Neste subtema serão avaliados e determinados os valores máximos de tensão do material para assim podermos determinar qual material poderá ser utilizado na fabricação de uma ECDH Algumas recomendações são indicadas Recomendação 1 O projeto ideal é aquele em que a tensão atuante no pé do dente está bem próxima da tensão admissível no seu limite inferior Se a tensão atuante estiver acima da tensão admissível 𝜎 a engrenagem pode não suportar a transmissão vindo a romper na base do dente prematuramente Se por outro lado a tensão atuante estiver bem aquém da tensão admissível a engrenagem estará superdimensionada tornandose antieconômica Recomendação 2 Ângulo de pressão 𝛼 Observe o par de dentes apresentado na Figura 59 119 Iniciam o contato no ponto A A cinemática do mecanismo faz com que o ponto A descreva a trajetória AB No ponto B termina o contato entre os dentes O segmento de reta AB descrito pela trajetória do ponto de contato e a tangente comum aos diâmetros primitivos das engrenagens define o ângulo da pressão Pela norma DIN 867 recomendase a utilização do ângulo de pressão α 20 Figura 59 Trajetória demonstrada desde seu o início até o fim do contato entre dentes Fonte SHIGLEY 2011 Recomendação 3 Para a Engrenagem com perfil cicloidal serão apresentadas sua teoria e sua representação em condições de curvas nas Figuras 513 514 515 e 516 Aplicações Esse tipo de engrenagem limitado às construções mecânicas pode ser encontrada em bombas e ventiladores volumétricos em relógios e aparelhos de precisão Processos de Fabricação A engrenagem cicloidal é obtida por meio de estampagem trefilação brochamento ou injeção mecânica fina por fresamento ou aplainamento 120 As ferramentas são mais caras pois possuem flancos retos O processo de fabricação por ser mais preciso tornase mais caro Vamos Aplicar Nas etapas a seguir você verá o passoapasso para o projetista realizar o procedimento para dimensionar a engrenagem cilíndrica de dentes helicoidais ECDH Exercício Estudo de Caso Dimensionamento de engrenagens ECDH Roteiro para o dimensionamento de um par de engrenagens ECDH O pinhão engrenagem menor Item 1 da Figura 510 é o dimensionado pois se ele resistir ao esforço aplicado a coroa engrenagem maior Item 1 da Figura 510 suportará com folga a mesma carga por ser uma engrenagem maior Figura 510 Sistema Mecânico de transmissão de movimento entre pinhão e coroa ambas são engrenagens ECDH Fonte MELCONIAN 2011 Dimensionamento do pinhão Procedimento 1 Critério de pressão desgaste Para que não haja a ocorrência de uma Fadiga Superficial Crateração conforme Figura 511 deverão ser consideradas no cálculo durante o dimensionamento da engrenagem as seguintes etapas para realizar um bom e seguro projeto de engrenagens 121 Figura 511 Ocorrência da Fadiga Superficial denominada de Crateração nos dentes de uma ECDH Fonte ANDRADE SD 11 Torque no pinhão 𝑴𝑻 MT 30 π P n N m 12 Relação de transmissão i i Z2 Z1 13 Pressão admissível Padm deverá ser calculada conforme apresentado na equação abaixo e como foi visto na Etapa 2 Dimensionamento de ECDH Pressão admissível padmissível Para determinar seu valor deverão ser determinadas as seguintes variáveis Dureza pelo método Brinell e o fator de durabilidade padm 0487 HB W1 6 N mm2 131 Determinar a dureza Para a equação da tensão admissível será utilizado o valor de dureza pelo método Brinell que é obtido conforme exemplificado na Tabela 56 e 57 132 Fator de durabilidade W 𝑊 60 𝑛𝑝ℎ 106 122 Isolando o Fator de Durabilidade W 𝑊 1 6 𝑊 6 𝑊0168 133 Cálculo da pressão admissível Como foi calculado no item 13 deste exercício padm 0487 HB W 1 6 Poderá ser calculado o valor da Máxima Tensão admissível para o projeto da engrenagem ECDH 14 Fator de correção de hélice ϕp pressão Obtémse por meio do ângulo de inclinação de hélice βo na tabela 54 15 Volume mínimo do pinhão 𝑏1 𝑑01 2 02 𝑓2 𝑀𝑡 𝑝2 𝑎𝑑𝑚𝜑 𝑝 𝑖1 𝑖 denominado como X 𝑏1 𝑑01 2 𝑋 16 Módulo do engrenamento 𝑏1 𝑑01 2 𝑋 I volume mínimo 𝑏1 𝑦 𝑑01 II proporcionalidade Substituindo II em I tem se 𝑦 𝑑01 𝑑01 2 𝑋 𝑑01 3 𝑋 𝑌 𝑑01 𝑋 𝑌 3 Como o diâmetro primitivo d01 é definido por meio do produto entre o módulo frontal ms e o número de dentes da engrenagem temse d01 ms 𝑍1 123 161 Módulo Frontal 𝐦𝐬 ms 𝑑01 𝑍1 162 Módulo normal ferramenta mn ms cos βo Normalizar o módulo obtido por meio da DIN 780 Mn módulo normalizado 163 Recálculo do módulo frontal 𝒎𝒔𝟎 𝑚𝑠0 𝑚𝑛0 𝑐𝑜𝑠 𝛽0 17 Recálculo do diâmetro primitivo 𝒅𝟎𝒓 d0r Z1 ms0 18 Largura da engrenagem b1 X d0r 2 As equações dos itens 17 e 18 serão fundamentais no dimensionamento Critério de resistência à flexão no pé do dente A tensão máxima no pé do dente é expressa por meio de 124 Figura 512 Apresenta a Força Tangencial aplicada e o esforço gerado no pé do dente Fonte SHIGLEY 2011 2 Resistência à flexão no pé do dente σmáx Ft q b mn0 e φr φmaterial 21 Força tangencial FT FT 2 MT1 d01r MT1 r01 N 211 Raio primitivo 𝐫𝟎𝟏 𝑟01 𝑑01𝑟 2 22 Fator de forma q Para utilizar a tabela 510 onde determinase o valor do fator de forma de uma engrenagem ECDH tornase necessário determinar o número de dentes equivalentes Utilizase para tal a relação seguinte 𝑍𝑒 𝑍1 𝑐𝑜𝑠 𝛽0 3 Ze número de dentes equivalentes Por meio do 𝑍𝑒 obtémse o fator q na tabela 510 23 Fator de serviço e 125 Obtido na tabela AGMA por meio da relação e 1 φ 24 Largura da engrenagem b1 X d01 R 2 25 Módulo normalizado 𝑏1 𝑑01 2 𝑋 I volume mínimo 𝑏1 𝑦 𝑑01 II proporcionalidade Substituindo II em I tem se d01 ms 𝑍1 26 Módulo Frontal 𝐦𝐬 ms 𝑑01 𝑍1 27 Fator de correção de hélice 𝝋𝒓 Obtido em 𝑓 𝛽0 valor tabelado obtido em catálogo de fabricantes 28 Tensão máxima atuante no pé do dente σmáx Ft q b mn0 e φr Sempre merecendo um destaque nas equações dos itens 27 e 28 29 Análise do dimensionamento A engrenagem estará apta para suportar a transmissão se atender todas as características geométricas de acordo com as Normas DIN 862 e 867 para então atender aos Limites de Propriedades Mecânicas que em nosso estudo será a tensão Máxima de projeto e a tensão Máxima do material de fabricação para ECDH como apresentada na Figura 513 a seguir σmáx σmaterial 126 Figura 513 Acoplamento entre os dentes de uma ECDH e os 3 tipos esforços gerados Fonte SHIGLEY 2011 Os três tipos de esforços são Tangencial Axial e Radial Seus Cálculos podem ser vistos a seguir 1 Força tangencial FT FT 2 MT1 d01r 2 MT2 d02 N 2 Força radial Fr Fr FT tag αS0 𝑁 3 Força axial 𝑭𝒂 𝐹𝑎 𝐹𝑇 𝑡𝑎g 𝛽0 N Vamos Aplicar Exercício 1 1 Dimensionar o par de engrenagens ECDH para que possa atuar com segurança na transmissão representada conforme segue 127 O acionamento será por meio de motor elétrico com potência P 147kW 20CV e rotação n 1140rpm ω 38πrads O material a ser utilizado é o SAE 8640 A dureza especificada é de 58 HRC A duração prevista para 10000h de funcionamento com atuação em eixos de transmissão e acionamento máximo de 10hdia Figura 514 Sistema Mecânico de transmissão de movimento entre pinhão e coroa ambas são ECDH Fonte MELCONIAN 2011 Fator de serviço e 1 ϕ Sendo o fator de serviço AGMA ϕ 140 Considere 𝑏1 𝑑01 025 relação entre largura e diâmetro primitivo 𝛼𝑛0 20 ângulo de pressão 𝑍1 29 𝑑𝑒𝑛𝑡𝑒𝑠 𝑝𝑖𝑛ℎã𝑜 𝑍2 89 𝑑𝑒𝑛𝑡𝑒𝑠 𝑐𝑜𝑟𝑜𝑎 𝛽0 20 â𝑛𝑔𝑢𝑙𝑜 𝑑𝑒 ℎé𝑙𝑖𝑐𝑒 𝛼𝑛0 20â𝑛𝑔𝑢𝑙𝑜 𝑑𝑒 𝑝𝑟𝑒𝑠𝑠ã𝑜 𝑛𝑜𝑟𝑚𝑎𝑙 Desprezar as perdas na transmissão 128 Dimensionamento 1 Critério de pressão desgaste 11 Fator de características elásticas do material f Como o material utilizado é o aço concluise que F 1512 12 Torque no pinhão 𝑀𝑇1 30000 𝜋 𝑃 𝑛 𝑁 𝑚𝑚 𝑀𝑇1 30000 𝜋 14700 1140 𝑁 𝑚𝑚 𝑀𝑇1 123136 𝑁 𝑚𝑚 13 Relação de transmissão i 𝑖 𝑍2 𝑍1 89 29 𝑖 307 14 Pressão admissível Padm 141 Fator de durabilidade W W 60 np h 106 60 1140 104 106 np nmotor 1140 rpm motor acoplado ao eixo do pinhão W 684 142 Intensidade da pressão admissível Pressão admissível 𝒑𝒂𝒅𝒎 𝑝𝑎𝑑𝑚 0487𝐻𝐵 𝑊1 6 𝑁 𝑚𝑚2 Por meio da tabela de correlação de dureza obtémse que 58HRC equivale aproximadamente a 6000 Nmm2 6000HB 129 padm 0487 6000 6841 6 0487 6000 297 N mm2 𝑝𝑎𝑑𝑚 984 𝑁 𝑚𝑚2 984 102 𝑁 𝑚𝑚2 15 Fator de correção de hélice ϕp pressão Como o ângulo de hélice é βo 20 obtémse na tabela 54 ϕp 140 16 Volume mínimo do pinhão 𝑏1 𝑑01 2 02 𝑓2 𝑀𝑡 𝑝2 𝑎𝑑𝑚 𝜑 𝑝 𝑖 1 𝑖 𝑏1 𝑑01 2 02 15122 123136 984 102 2 14 307 1 307 𝑏1 𝑑01 2 45723 104 123136 984 2 104 14 407 307 𝑏1 𝑑01 2 55063 𝑚𝑚3 17 Módulo do engrenamento 𝑏1 𝑑01 2 55063 𝑚𝑚3 I 𝑏1 025 𝑑01 II Substituindo II em I tem se 025 𝑑01 2 𝑑01 55063 d01 3 55063 025 d01 55063 025 3 𝑑01 604 𝑚𝑚 18 Módulo frontal 𝐦𝐬 ms 𝑑01 𝑍1 604 29 ms 208 𝑚𝑚 130 19 Módulo normal ferramenta mn ms cos β0 𝑚𝑛 208 cos 20 𝑚𝑛 195 mm Por meio da DIN 780 escolhese o módulo normalizado 𝑚𝑛0 2 mm 110 Recálculo do módulo frontal 𝒎𝒔𝟎 𝑚𝑠0 𝑚𝑛0 cos 𝛽0 2 cos 20 𝑚𝑠0 213 𝑚𝑚 111 Recálculo do diâmetro primitivo 𝒅𝟎𝟏 𝑹 d01 R Z1 ms0 d01 R 29 213 d01 R 6177 mm 112 Largura da engrenagem b1 X d01 R2 b1 55063 61772 b1 15 mm 131 2 Resistência à flexão no pé do dente 𝜎 𝐹𝑡 𝑞 𝑏 𝑚𝑛0 𝑒 𝜑𝑟 𝜎𝑚𝑎𝑡𝑒𝑟𝑖𝑎𝑙 21 Força tangencial 𝐹𝑇 2 𝑀𝑇1 d01 R 2 123136 6177 𝐹𝑇 398 N 22 Fator de forma q 221 Número de dentes equivalentes Ze 𝑍𝑒1 𝑍1 𝑐𝑜𝑠 𝛽1 3 29 𝑐𝑜𝑠 20 3 𝑍𝑒1 35 dentes Por meio da tabela do fator q encontrase que Z fator q 34 30 40 29 Interpolando os valores da tabela obtémse que Incremento da interpolação l 30 29 6 00167 Por meio do incremento encontrado são determinados os seguintes valores 132 Tabela 514 Tabela da correlação entre o número de dentes da engrenagem e seu incremento q Número de Dentes Fator q 34 3000 35 2983 36 2967 37 2950 38 2933 39 2917 40 2900 Fonte MELCONIAN 2011 Portanto para Ze 35 dentes o fator q 2983 23 Fator de serviço e Para trabalhar em eixo de transmissão com duração de serviço diário prevista para 10 horas a tabela da AGMA recomenda ϕ 1 Como e 𝟏 𝝋 concluise que para este projeto e 1 24 Largura da engrenagem 𝑏1 15 𝑚𝑚 25 Normalizado 𝐦𝐧𝟎 mn0 2 mm 26 Fator de correção de hélice ϕr Como βo 20 encontrase na tabela ϕr 135 27 Tensão máxima atuante no pé do dente 𝜎𝑚á𝑥 𝐹𝑡 𝑞 𝑏 𝑚𝑛0 𝑒 𝜑𝑟 𝜎𝑚á𝑥 3987 2983 15 2 1 135 𝜎𝑚á𝑥 294 𝑁 𝑚𝑚2 133 28 Análise do dimensionamento Como a tensão máxima atuante é maior que a tensão admissível do material 𝜎𝑚á𝑥 294 𝑁 𝑚𝑚2 𝜎8640 200 𝑁 𝑚𝑚2 Concluise que o pinhão está mal dimensionado devendo ser reforçado 29 Redimensionamento do pinhão 1ª hipótese mantémse o módulo do engrenamento e alterase a largura Fixase a tensão atuante máxima com o mesmo valor da tensão admissível do material SAE 8640 portanto 𝜎𝑚á𝑥 𝜎8640 200 𝑁 𝑚𝑚2 291 Largura do pinhão 𝑏1 𝐹𝑡 𝑞 𝜎8640 𝑚𝑛0 𝑒 𝜑𝑟 3987 2983 200 2 1 135 𝑏1 22 𝑚𝑚 3 Cálculo para obter os valores das características geométricas segundo as Normas DIN 862 e 867 As tabelas a seguir de 515 a 518 apresentam as equações para realização dos cálculos Tabela 515 Formulário das variáveis fundamentais do projeto de uma ECDH Formulário Pinhão mm Coroa mm Módulo normalizado DIN 780 mn0 2 mn0 2 Passo t0 t0 mn0 π t0 628 t0 628 134 Fonte adaptado de MELCONIAN 2011 Vão entre os dentes no primitivo folga nula no flanco l0 t0 2 l0 628 2 314 l0 628 2 314 Espessura do dente no primitivo folga nula no flanco S0 t0 2 S0 t0 2 628 2 314 S0 t0 2 628 2 314 Altura da cabeça do dente hk mn0 hk 2 hk 2 135 Tabela 516 continuação Formulário das variáveis fundamentais do projeto de uma ECDH Fonte adaptado de MELCONIAN 2011 Tabela 517 continuação Formulário das variáveis fundamentais do projeto de uma ECDH Formulário Pinhão mm Coroa mm Ângulo de pressão frontal 𝛼𝑆0 tag 𝛼𝑆0 𝑡𝑎𝑔 𝛼𝑛0 𝑐𝑜𝑠 𝛽0 tag 𝛼𝑆0 𝑡𝑎𝑔 20 𝑐𝑜𝑠 20 tag 𝛼𝑆0 036 093 𝛼𝑆0 21 10 tag 𝛼𝑆0 𝑡𝑎𝑔 20 𝑐𝑜𝑠 20 tag 𝛼𝑆0 036 093 𝛼𝑆0 21 10 Avanço do dente s 𝑠 𝑏 tag 𝛽0 𝑠 22 tag 20 𝑠 8 𝑠 22 tag 20 𝑠 8 Formulário Pinhão mm Coroa mm Altura do pé do dente ℎ𝑓 12 𝑚𝑛0 ℎ𝑓 12 2 24 ℎ𝑓 12 2 24 Altura total do dente ℎ𝑧 22 𝑚𝑛0 ℎ𝑧 22 2 44 ℎ𝑧 22 2 44 Altura comum do dente ℎ 2 𝑚𝑛0 ℎ 2 2 4 ℎ 2 2 4 Folga da cabeça do dente 𝑆𝐾 02 𝑚𝑛0 𝑆𝐾 02 2 04 𝑆𝐾 02 2 04 Módulo frontal 𝑚𝑠 𝑚𝑛0 𝑐𝑜𝑠 𝛽0 𝑚𝑠 2 𝑐𝑜𝑠 20 𝑚𝑠 213 𝑚𝑠 2 𝑐𝑜𝑠 20 𝑚𝑠 213 136 Diâmetro primitivo 𝑑0 𝑑0 𝑚𝑠 𝑍 𝑑0 𝑚𝑠 𝑍1 𝑑0 213 29 𝑑0 6177 𝑑0 𝑚𝑠 𝑍2 𝑑0 213 89 𝑑0 18957 Fonte adaptado de MELCONIAN 2011 Tabela 518 continuação Formulário das variáveis fundamentais do projeto de uma ECDH Fonte adaptado de MELCONIAN 2011 Formulário Pinhão mm Coroa mm Diâmetro de base 𝑑𝑔 𝑑𝑔 𝑑0 𝑐𝑜𝑠 𝛼𝑠0 dg1 d01 cos 21 10 dg1 6177 093 dg1 5760 dg2 d02 cos 21 10 dg2 18957 093 dg2 17677 Diâmetro interno 𝑑𝑓 𝑑0 2 ℎ𝑓 df1 d01 2 hf df1 6177 2 24 df1 5697 df2 d02 2 hf df2 18957 2 24 df2 18477 Diâmetro externo 𝑑𝑘 𝑑0 2 ℎ𝑘 dk1 d01 2 hk dk1 6177 2 2 dk1 6577 dk2 d02 2 hk dk2 18957 2 2 dk2 19357 Distância entre centros mm Cc Z1 Z2 ms 2 29 89 213 2 Cc 123785 Largura das engrenagens mm b1 b2 22 137 4 Engrenagens cônicas de dentes retos e Espirais Tem as seguintes características 1 São utilizadas em eixos reversos 2 A relação de transmissão máxima é 16 3 Para relações de transmissão acima de 112 são mais caras que as engrenagens cilíndricas 41 Engrenagens cônicas Em uma engrenagem cônica o diâmetro externo De pode ser medido por meio do número de dentes Z e do ângulo primitivo δ para então ser calculado Na Figura 515 podemos ver os diferentes tipos de engrenamento considerando engrenagens cônicas São 4 Tipos de geometrias nas engrenagens cônicas como apresentado na figura 515 a seguir Figura 515 Exemplos de Engrenagens Cônicas 138 Fonte SHIGLEY 2011 Por meio da Figura 516 podem ser vistos os seguintes pontos o acoplamento entre engrenagens cônicas seus detalhes construtivos e suas Nomenclaturas de acordo com as Normas DIN 682 e 687 Figura 516 Geometria de uma Engrenagem Cônica com suas dimensões e ângulos 139 Fonte SHIGLEY 2011 Para determinar os diâmetros principais suas características geométricas e seus valores dimensionais de acordo com a Norma DIN 862 e 867 você verá nas Tabela 519 a 523 as principais equações que deverão ser consideradas pelo projetista no Memorial de Cálculo do Projeto de um Sistema Mecânico que neste caso será a Engrenagem Cônica ECDH Tabela 519 Formulário das variáveis fundamentais do projeto de uma Engrenagem Cônicas de Dentes Helicoidais Denominação Símbolo Fórmula Número de dentes 𝑍1 𝑍1 𝑑01 𝑚 Módulo m 𝑚 𝑡0 𝜋 140 Fonte adaptado de MELCONIAN 2011 Tabela 520 continuação Formulário das variáveis fundamentais do projeto de uma Engrenagem Cônicas de Dentes Helicoidais Denominação Símbolo Fórmula Altura da cabeça do dente ℎ𝑘 ℎ𝑘 𝑚 Altura do pé do dente ℎ𝑓 ℎ𝑓 11 𝑎 13 𝑚 Altura total do dente ℎ𝑍 ℎ𝑍 21 𝑎 23 𝑚 Folga na cabeça 𝑆𝑘 𝑆𝑘 01 𝑎 03 𝑚 Módulo médio 𝑚𝑚 𝑚𝑚 𝑑𝑚 𝑍 𝑅𝑎 𝑏 2 𝑅𝑎 𝑚 ou 𝑚𝑚 08 𝑚 Passo 𝑡0 𝑡0 𝑚 𝜋 Espessura no primitivo 𝑆0 𝑆0 𝑡0 2 com folga de flanco nula Vão entre os dentes no primitivo 𝑙0 𝑙0 𝑡0 2 com folga de flanco nula Diâmetro primitivo 𝑑01 𝑑01 𝑚 𝑍1 Diâmetro primitivo médio 𝑑𝑚1 𝑑𝑚1 𝑑01 𝑏 𝑠𝑒𝑛 𝛿1 e 𝑑𝑚2 𝑑𝑚1 l Altura comum do dente h ℎ 2 𝑚 141 Diâmetro externo ou de cabeça 𝑑𝑘1 2 𝑑𝑘1 𝑑01 2 𝑚 𝑐𝑜𝑠 𝛿1 𝑑𝑘1 𝑚 𝑍1 2 𝑐𝑜𝑠 𝛿1 𝑑𝑘2 𝑑02 2 𝑚 𝑐𝑜𝑠 𝛿2 𝑑𝑘2 𝑚 𝑍2 2 𝑐𝑜𝑠 𝛿2 para 𝛿 90 𝑐𝑜𝑠 𝛿2 𝑠𝑒𝑛 𝛿 Ângulo de pressão 𝛼0 𝛼0 20 norma DIN 867 Abertura angular entre eixos 𝛿 𝛿 𝛿1 𝛿2 Fonte adaptado de MELCONIAN 2011 Tabela 521 continuação Formulário das variáveis fundamentais do projeto de uma Engrenagem Cônicas de Dentes Helicoidai Denominação Símbolo Fórmula Conicidade de engrenagem relativa no primitivo 𝛿1 2 𝑡𝑎𝑔 𝛿2 𝑠𝑒𝑛 𝛿 𝑐𝑜𝑠 𝛿 𝑍1 𝑍2 𝑝𝑎𝑟𝑎 𝛿 90 𝛿1 𝛿 𝛿2 𝑡𝑎𝑔 𝛿2 𝑍2 𝑍1 i Conicidade de engrenagem relativa no diâmetro externo 𝛿 𝐾1 2 𝛿𝐾1 𝛿1 𝑘 em que tag k ℎ𝑘 𝑅𝑎 𝑚 𝑅𝑎 para 𝛿 90 tag 𝑘 4 𝑍12 𝑍22 Fonte adaptado de MELCONIAN 2011 142 Tabela 522 continuação Formulário das variáveis fundamentais do projeto de uma Engrenagem Cônicas de Dentes Helicoidais Denominação Símbolo Fórmula Geratriz relativa no diâmetro primitivo 𝑅𝑎 𝑅𝑎 𝑑01 2 𝑠𝑒𝑛 𝛿1 Para 𝛿 90 𝑅𝑎 𝑚 𝑍1 2 𝑍2 2 4 𝑅𝑎 𝑑01 1 𝑖 2 4 Geratriz relativa no diâmetro primitivo médio 𝑅𝑚 𝑅𝑚 𝑑𝑚1 1 𝑖 2 4 para 𝛼 90 Largura do dente b 𝑏 1 3 𝑅𝑎 8 𝑚 Fonte adaptado de MELCONIAN 2011 Tabela 523 continuação Formulário das variáveis fundamentais do projeto de uma Engrenagem Cônicas de Dentes Reto Denominação Símbolo Fórmula Número de dentes equivalente 𝑍01 2 𝑍𝑒1 𝑍1 𝑐𝑜𝑠 𝛿1 e 𝑍𝑒2 𝑍2 𝑐𝑜𝑠 𝛿2 Para 𝛿 90 𝑍𝑒2 𝑍01 𝑙2 143 Raio primitivo da engrenagem equivalente 𝑟𝑒1 2 𝑟𝑒1 𝑑01 2 𝑐𝑜𝑠 𝛿1 Relação de multiplicação L I 𝑍2 𝑍1 𝑑02 𝑑01 𝑛1 𝑛2 𝑠𝑒𝑛 𝛿2 𝑠𝑒𝑛 𝛿1 Para 𝛿 90 I tag 𝛿2 Fonte adaptado de MELCONIAN 2011 42 Dimensionamento de Engrenagens Cônicas ECDH Neste item serão apresentadas as principais equações que serão utilizadas no dimensionamento de uma ECDH para atender ao limite e à aplicação deste elemento mecânico ao ser solicitada em um projeto As equações deverão atender as condições descritas a seguir que estão no Memorial de Cálculo de Projeto de Elemento Mecânico e atender também ao dimensionamento com o Critério de desgaste Veja a seguir as etapas de um projeto de um elemento mecânico Engrenagens Cônicas Vamos entender a seguinte expressão que deve ser utilizada no dimensionamento de pinhões com ângulo de pressão 𝛼 20 e número de dentes de 18 a 40 Material utilizado na fabricação com material aço Condição 1 Atender o Volume da Base do Dente 𝑏1𝑑01 2 572 105 𝑀𝑡 𝑝2 𝑎𝑑𝑚 𝑖 1 𝑖 014 𝜑 Sendo que há 2 condições nesta expressão de Volume da base do dente índice engrenagens externas índice engrenagens internas ou planetárias 144 Ambos os exemplos de Engrenamento Externo ou Interno foram apresentados na Figura 51 itens a b e c Condição 2 Atender o Critério de Pressão Desgaste 𝑏𝑑𝑚1 2 02 𝑓2 𝑀𝑇 cos 𝛿1 𝑝𝑎𝑑𝑚2 𝑖2 1 𝑖2 Condição 3 Atender o Critério de Resistência à Flexão 𝜎𝑚á𝑥 𝐹𝑡 𝑞 𝑏 𝑚𝑚 𝑒 𝜎𝑎𝑑𝑚 Condição 4 Para obter o fator q definido na Tabela 54 devemos calcular o número de dentes equivalente da engrenagem cônica cônica cilíndrica 𝑍𝑒 𝑍1 cos 𝛿1 Em que b Largura do pinhão mm dm Diâmetro médio mm f Fator das características elásticas do par adimensional MT Momento Torçor N mm Padm Pressão admissível Nmm2 t Relação de transmissão adimensional máx Tensão máxima atuante Nmm2 Ft Fator tangencial N q Fator de forma adimensional mm Módulo médio mm Condição 5 Por meio das condições de atividade da engrenagem cônica será determinado a faixa de valores para o Fator de Serviço e como por exemplo Engrenagem Cônica ECDH 145 O fator de forma de engrenagem é obtido em função do número de dentes da engrenagem conforme é apresentado na Tabela 55 e fator de serviço serviços leves e 175 Serviços normais e 15 Serviços pesados e 125 Por meio dos cálculos realizados dos itens 10 a 42 concluise que ele atenderá todos os valores das Características Geométricas conforme Normas DIN 682 e 687 e as Propriedades Mecânicas devidos aos esforços aplicados nas Engrenagens Cônicas ECDH Conclusão Neste Bloco apresentamos a Engrenagem Cilíndrica de Dentes Helicoidais ECDH que em sua maior parte segue o mesmo conceito nas etapas de cálculo da ECDR vista no Bloco 4 Além disso suas características geométricas também seguem as Normas DIN 682 e 687 sendo então importante realizar um comparativo entre ECDR e ECDH Como vimos algumas vantagens da ECDR são possuir manufaturabilidade ou seja são mais fáceis de projetar e fabricar e ser de fácil montagem e maior eficiência quando comparada a ECDH pois esta possui em sua geometria uma inclinação β na região dos dentes que gera um esforço na axial além do esforço radial e com esses dois esforços ocorrerá um aumento de temperatura média de trabalho durante o engrenamento reduzindo a sua eficiência quando comparada a ECDR Já ao analisar as vantagens da ECDH temos no processo de engate os dentes que se engatam um pouco de cada vez ao invés de toda face ao mesmo tempo como visto na ECDR sendo assim gera uma operação mais silenciosa ao considerar que para o mesmo tamanho do dente módulo e largura equivalente as engrenagens helicoidais podem lidar com mais carga do que as engrenagens retas já que o dente da engrenagem helicoidal é efetivamente maior por estar posicionada diagonalmente 146 Desta forma fica a critério do engenheiro projetista selecionar qual engrenagem trará mais vantagens ao Sistema Mecânico a ser projetado REFERÊNCIAS ANDRADE A S Elementos Orgânicos de Máquinas II UFP SD KIMINAMI C S CASTRO W B OLIVEIRA M F Introdução aos processos de fabricação de produtos metálicos São Paulo Blucher 2013 MELCONIAN S Elementos de Máquinas 9ª ed São Paulo Erica 2011 MOTT R L Elementos de máquinas em projetos mecânicos São Paulo 2015 NORTON R L Projetos de Máquinas Uma Abordagem Integrada 4º ed Porto Alegre Bookman 2013 SHIGLEY J E BUDYNAS R G NISBETT J K Elementos de máquinas de Shigley 8ª ed São Paulo AMGH Editora Ltda 2011 147 6 CONCEITOS NOS ELEMENTOS DE ACOPLAMENTO Neste Bloco serão apresentados os principais elementos de acoplamento Assim como os tipos e as diversas aplicações dos acomplamentos nos Sistemas Mecânicos Também serão definidos os critérios que deverão ser considerados para que ocorra uma correta seleção de qual acoplamento deve ser utilizado Por fim serão demonstradas as formas de desalinhamento dos acoplamentos pois mesmo ocorrendo o desalinhamento este deve suportar suas condições de trabalho sem que hajam falhas ou rompimento do acoplamento em análise 61 APLICAÇÕES DO ACOPLAMENTO Acoplamento é um conjunto mecânico constituído de elementos de máquinas empregado na transmissão de movimento de rotação entre duas árvores ou eixo árvores conforme Figura 61 Empregase o acoplamento quando se deseja transmitir um momento de rotação de um eixo motor a outro elemento de máquina situado coaxialmente eixo comum a ele Também podem ser definidos como elementos de transmissão de máquinas cujo objetivo é unir duas extremidades eixos de equipamentos distintos na transmissão de força Figura 61 Acoplamento entre eixos àrvores de um sistema de motor e bomba Fonte FRANCESCHI ANTONELLO SD 148 Também devem ser informadas as funções em geral dos acoplamentos tais como Absorver desalinhamento entre os eixos Absorver parcialmente choques em um dos eixos Amortecer vibrações torcionais Proteger máquinas e equipamentos de sobrecarga funcionando como fusível Um acoplamento que faz parte da rotina de quem dirige e que opera por atrito é a embreagem fricção Na Figura 62 você pode ver um disco de embreagem e na figura 63 o local do acoplamento de um disco de embreagem Figura 62 Acoplamento que opera por atrito imagem de Disco de Embreagem Então chegase à conclusão de que o elemento mecânico que compõe o sistema da transmissão é o disco de embreagem como observado a seguir na Figura 63 instalado entre o motor e a caixa de mudanças de modo a conectar e desconectar estes dois componentes por ação do motorista 149 Figura 63 Acoplamento que opera por atrito sistema mecânico completo em que o disco de embreagem acoplamento realiza a ligação e a transmissão na caixa de mudança de um veículo 62 CLASSIFICAÇÃO E TIPOS DE ACOPLAMENTOS Para facilitar há uma classificação dos acoplamentos que se dividem em permanentes e comutáveis sendo que os permanentes atuam continuamente e são separados em acoplamentos rígidos e flexíveis Já os comutáveis ao atuar obedecem a um comando Assim veja os itens a seguir que apresentarão alguns tipos de acoplamento sua definição aplicação e imagem 621 ACOPLAMENTOS PERMANENTES Algumas vezes há a necessidade de desconexão durante o funcionamento da máquina ou equipamento e os acoplamentos permanentes são usados para conectar eixos em que não existe a necessidade de desconexão estas que ocorrem somente em caso de manutenção Acoplamentos destes tipos são utilizados em situações em que os eixos das árvores estão em uma forma de aplicação que se faz necessário algumas especificidades por exemplo a São colineares temse o acoplamento de flange conforme Figura 65 b Se cruzam temse a Junta universal conforme Figura 69 c São paralelos temse a Junta oldham conforme Figura 64 150 Figura 64 Modelo de uma Junta de oldham Fonte FRANCESCHI ANTONELLO SD 6211 ACOPLAMENTOS PERMANENTES RÍGIDOS FLANGES O método mais clássico de acoplamento para se conectar árvores utiliza o tipo de acoplamento rígido também denominado Flange conforme Figura 65 Ele é adequado na transmissão de potência elevada em baixa velocidade tendo também como garantir um alinhamento conciso sendo que estes acoplamentos frequentemente são usados por terem uma protuberância com a sua finalidade de ser encaixada em um rebaixo Figura 65 Modelo de um Acoplamento Permanente Rígido Flange Fonte FRANCESCHI ANTONELLO SD 151 Por meio de chaveta é realizada a união das Luvas ou Flanges nas Árvores com a condição de encaixe com interferência ou cones São utilizados acoplamentos de disco ou de pratos quando é desejado transmissões de grande potência 6212 ACOPLAMENTO COM LUVA DE COMPRESSÃO OU DE APERTO Para a seleção de um acoplamento que facilita no momento de uma manutenção de máquinas e de equipamentos são utilizados os do modelo Tipo Luva conforme figura 66 pelo fato de não interferir no posicionamento das árvores e não apresentarem problemas de alinhamento na montagem ou remoção Figura 66 Modelo de uma Luva de Compressão ou Aperto Fonte FRANCESCHI ANTONELLO SD 6213 ACOPLAMENTOS PERMANENTES FLEXIVEIS Utilizado quando na ocorrência de movimentos bruscos for necessário que a realização da transmissão de movimentos aconteça de forma mais suave durante seu movimento Será mantido o alinhamento entre as árvores e eixos árvores sendo que para o atendimento dessas condições citadas existem três modelos 152 Figura 67 Modelo de um Acoplamento Elástico de Garras Fonte FRANCESCHI ANTONELLO SD a Acoplamento elástico de garras Ao analisar as garras neste caso são constituídas por tocos de borracha Entre as aberturas do contra disco figura 67 ocorre o encaixe e será transmitido desta maneira o movimento de rotação b Acoplamento de dentes arqueados A característica principal ao classificar este modelo de acoplamento é que ele apresenta dentes de forma ligeiramente curvada no sentido axial sendo permitido até 3 graus de desalinhamento angular Através de um anel dentado que é a transmissora do movimento com suas duas carreiras separadas por uma saliência central c Acoplamentos elásticos São todos os elementos que são utilizados com a função de tornar a transmissão do movimento em árvores mais suave nos casos em que estes movimentos são bruscos Permitindo por meio destes acoplamentos o funcionamento do conjunto com desalinhamento angular paralelo e axial entre as árvores Tendo estes acoplamentos como principal função transmitir à máquina a energia de acionamento produzida pela unidade geradora porém com o mínimo de vibrações 153 6214 FLEXIBILIDADE ELÁSTICA Um elemento elástico tem a capacidade de absorver desalinhamento axial radial e angular conforme apresentado na Figura 68 quando um sistema mecânico é aplicado em transmitir rotação movimento de torção e também em condições que solicite o amortecimento de Picos de Carga e ruídos das máquinas acopladas Assim para o atendimento das condições de trabalho é indicado a utilização de Acoplamento Elástico Podese observar que pelas características mencionadas acima haverá uma grande aplicação quando o sistema é acionado por um Motor Elétrico Figura 68 Representação de um Sistema de Acoplamento com Flexibilidade Elástica Fonte FRANCESCHI ANTONELLO SD 63 ACOPLAMENTOS ARTICULADOS Dentro da gama de aplicações em diversas peças e equipamentos existem os acoplamentos por juntas universais e conforme indicado na Figura 69 o Eixo de transmissão cardan Na Figura 610 vemos as juntas homocinéticas e os Acoplamentos articulados como a embreagem que são muito aplicados no cotidiano e requerem um bom projeto para que tais sistemas mecânicos atendam as propriedades mecânicas necessárias e consigam o aumento de sua vida útil Vamos detalhar cada sistema a seguir a Juntas universais exemplo o eixo cardan 154 Aplicado na ligação da árvore que formam um ângulo constante entre si Seu sistema mecânico é constituído basicamente de dois cubos que possuem em suas extremidades um garfo ligado a uma cruzeta conforme Figura 69 Figura 69 Representação de um Sistema de Acoplamento Eixo de Transmissão Cardan Fonte KAPP SD b Junta Universal exemplo a Homocinética Aplicado quando é solicitado a uma junta transmitir o movimento entre árvores que permitam a ocorrência de uma variação angular conforme Figura 68 durante seu funcionamento Sendo a constituição desta junta formada de esferas de aço que são acomodadas em específicos alojamentos que são denominados de calhas c Acoplamentos Móveis exemplo Sistema Mecânico de um veículo que possui a Embreagem Junta Homocinética Eixo de Transmissão e outros itens com outras classificações Aplicado quando se faz necessário durante seu regime de trabalho que um acoplamento deva suportar a conexão e desconexão das árvores sem a necessidade de o acoplamento ser desmontado e assim permitir que a árvore tenha um jogo longitudinal como por exemplo no controle no acionamento da embreagem que ocorre no pedal do automóvel conforme Figura 610 Controle este que comanda a transmissão da Força e o Movimento apenas em seu acionamento ou seja com o pedal de embreagem 155 Figura 610 Representação de um Sistema com as Juntas Homocinéticas caixa de transmissão onde está a Embreagem e o eixo de transmissão cardan Fonte Euroautomotive 2017 631 Critérios na Montagem de Acoplamentos Alguns cuidados durante a montagem dos acoplamentos devem ser adotados com grande importância tais como a Sempre que possível que a colocação do Flange seja a quente b Não utilizar golpes para a colocação de Flanges utilizar prensas ou os dispositivos adequados c O alinhamento das árvores devem ser prioridade pois mesmo que Acoplamentos Elásticos não sejam utilizados por ocorrerem desalinhamentos ao longo do tempo de serviço sempre deverão ser realizados novos alinhamentos d Sempre deverá ser realizada uma averiguação da folga entre flanges do alinhamento e por consequência da concentricidade do flange com a árvore 156 e Somente aplicar a carga após certificarse de que estejam bem instalados todos os elementos de ligação 632 Desalinhamento em Acoplamentos Desalinhamento é quando ocorre a não coincidência entre o eixo de simetria de dois veios colineares Porém existem casos específicos em que se faz necessária a existência de um pequeno desalinhamento para que ocorra a lubrificação de dentes de um acoplamento de engrenagem Assim existe uma classificação do desalinhamento sendo angular ou paralelo O desalinhamento angular conforme a figura 611 ocorre quando há uma formação de um ângulo durante a rotação do eixo e se forma entre os dois veios Já o desalinhamento paralelo ocorre quando o eixo de rotação entre os dois veios é paralelo Desta forma pode se considerar que há ocorrência da combinação angular e paralelo no desalinhamento Figura 611 Representação da ocorrência dos Tipos de Desalinhamento nos Acoplamentos Fonte FRANCESCHI ANTONELLO SD 157 Mesmo com severos desalinhamentos o Sistema Mecânico ao seguir seu projeto deverá suportar por longos períodos de funcionamento Mas existem alguns componentes mecânicos que não suportam esse mesmo desalinhamento Devemos sempre considerar que em um Sistema Mecânico será necessária a utilização de um modelo de acoplamento pois é comum ocorrer desalinhamentos conforme a Figura 612 Figura 612 Representação da ocorrência de Desalinhamento em um Sistema Mecânico motor elétrico e um eixo arvoré terá acoplamentos nesta união Fonte Piotrowsky SD Desta maneira a principal função de um acoplamento é transmitir potência entre uma máquina e outra E também este deverá suportar e compensar pequenos desalinhamentos Além da deflexão do veio ocorrem variações de temperatura Tendo muitas vezes a ocorrência de Falhas Prematuras devido aos desalinhamentos que são passados para os componentes mecânicos 158 Conclusão Neste Bloco aprendemos a definir os principais elementos de acoplamento e realizar a identificação de seus tipos Também compreendemos a diversidade de aplicação em Sistemas Mecânicos e entendemos como ocorre o desalinhamento dos acoplamentos e por fim verificamos as condições de trabalho e os limites existentes da inevitável ocorrência do desalinhamento Sendo também ilustradas e detalhadas as condições corretas que devem ser seguidas na montagem dos acoplamentos REFERÊNCIAS ANDRADE A S Elementos Orgânicos de Máquinas II UFP SD EUROAUTOMOTIVE How Automatic Transmission Works In Vehicle Slideshare 2017 Disponível em httpsbitly2QUhx0x Acesso em 6 jan 2021 FRANCESCHI A ANTONELLO M G Elementos de Máquinas Colégio Técnico de Santa Maria SD KAPP W Eixos e árvores Curitiba Editora UFPR SD Disponível em httpsbitly3tRGGba Acesso em 6 jan 2021 MELCONIAN S Elementos de Máquinas 9 ed São Paulo Erica 2011 MOTT R L Elementos de máquinas em projetos mecânicos São Paulo 2015 NORTON R L Projetos de Máquinas Uma Abordagem Integrada 4ºed Porto Alegre Bookman 2013 PIOTROWSKY J A importância do alinhamento entre eixos Pdfslide Disponível em httpsbitly3tPzdJm Acesso em 6 jan 2021 SHIGLEY J E BUDYNAS R G NISBETT J K Elementos de máquinas de Shigley 8ª ed São Paulo AMGH Editora Ltda 2011
Envie sua pergunta para a IA e receba a resposta na hora
Recomendado para você
20
Introdução aos Sistemas Mecânicos e Projetos de Transmissão
Modelagem de Sistemas Mecânicos
UNISA
18
Dimensionamento de Eixos: Análise de Materiais e Esforços Mecânicos
Modelagem de Sistemas Mecânicos
UNISA
45
Conceitos em Engrenagens Cilíndricas de Dentes Retos
Modelagem de Sistemas Mecânicos
UNISA
15
Conceitos no Dimensionamento de Sistemas Mecânicos
Modelagem de Sistemas Mecânicos
UNISA
2
Avaliação Contínua - Folha de Resposta
Modelagem de Sistemas Mecânicos
UNISA
1
Estudo do Controle de Velocidade em Motores de Corrente Continua
Modelagem de Sistemas Mecânicos
UNISA
3
Avaliação Integrada AVI - Detalhes e Questões
Modelagem de Sistemas Mecânicos
UNISA
7
Modelagem e Simulação Dinâmica de Manipulador Robótico Planar
Modelagem de Sistemas Mecânicos
UFRB
1
Modificações no Script para Trajetória Curva no Mecanismo Robótico
Modelagem de Sistemas Mecânicos
UCS
17
Modelagem Matemática de Motor CC em Mesa de Coordenadas
Modelagem de Sistemas Mecânicos
ENIAC
Texto de pré-visualização
SISTEMAS MECÂNICOS José Francisco de Barros Júnior 2 SUMÁRIO 1 INTRODUÇÃO AOS SISTEMAS MECÂNICOS 3 2 CONCEITOS NO DIMENSIONAMENTO DE SISTEMAS MECÂNICOS 22 3 CONCEITOS NO DIMENSIONAMENTO DE EIXOS ÁRVORES 36 4 CONCEITOS EM ENGRENAGENS CILÍNDRICAS DE DENTES RETOS ECDR 53 5 CONCEITOS EM ENGRENAGENS CILÍNDRICAS DE DENTES HELICOIDAIS ECDH 97 6 CONCEITOS NOS ELEMENTOS DE ACOPLAMENTO 147 3 1 INTRODUÇÃO AOS SISTEMAS MECÂNICOS Neste Bloco serão apresentadas as grandezas fundamentais da física e da mecânica e sua aplicação prática Esses conhecimentos são necessários para realizar um Projeto Mecânico ou seja a aplicação do elemento ou peça e sua geometria para assim poder dimensionar A disciplina de Sistemas Mecânicos utilizará conceitos apresentados em Resistência dos Materiais e Elementos de Máquinas além de apresentar conceitos novos como a correlação das grandezas fundamentais da Mecânica o Torque o Momento Torçor e a mudança em velocidade e também as transmissões de movimento linear para a circunferencial Com isto serão apresentadas equações para determinar o valor obtido nas velocidades angulares 𝜔 e nas velocidades periféricas 𝜗𝑝 bem como a determinação da unidade da Potência para mensurar o Trabalho mecânico realizado em um sistema 11 Introdução a projetos mecânicos Na disciplina de Sistemas Mecânicos estudaremos a transmissão mecânica por meios rígidos e flexíveis redutores e elementos de união Também conheceremos e aprenderemos a dimensionar a transmissão por engrenagens e correias com a utilização de redutores e elementos de união entre motor e máquina O objetivo principal deste estudo é apresentar a teoria já em suas aplicações reais como por exemplo Transmissão de potência entre motor e máquina Caixas de engrenagens de máquinas operatrizes Veículos aviões embarcações Transporte de materiais correia transportadora 4 Equipamentos de elevação e transporte Entre outros Buscamos também facilitar o entendimento e a elaboração de projetos mecânicos por meio do estudo de Especificações e definições dos meios de transmissão de força Classificação dos elementos de máquinas Transmissão de força por meios rígidos e flexíveis Classificação e aplicação de redutores e elementos de união Dimensionamento e aplicações 12 Torque nas transmissões 121 Torque ou Momento Torçor definido pela Física Por meio de conceitos fundamentais da física definese o Torque ou Momento Torçor como a tendência que uma força tem de rotacionar um corpo sobre o qual ela é aplicada O torque é um vetor perpendicular ao plano formado pelos vetores força e raio de rotação conforme representada na Figura 11 5 Figura 11 Direção dos vetores de Força e distância para realizar um Torque ou Momento Fletor Fonte HELERBROCK SDb Sempre que uma força for aplicada a alguma distância do eixo de rotação de um corpo esse corpo estará sujeito à rotação assim o torque pode ser entendido como o agente dinâmico das rotações Dessa forma ele está para os movimentos de rotação como a força está para os movimentos de translação Se quisermos fazer que um corpo gire em torno de algum ponto devemos exercer um torque sobre ele Veja a seguir alguns exemplos de Torque aplicado em nossa rotina Quando abrimos uma porta aplicamos força em um ponto distante do seu eixo de rotação Desta forma imprimimos sobre ela um torque maior conforme Figura 12 6 Figura 12 A maçaneta de uma porta é aberta pela aplicação de um torque Fonte HELERBROCK SDb Ao usarmos uma chave de boca como na Figura 13 podemos ver o aperto dos parafusos de uma roda de um veículo e utilizando um Torquimetro maior precisão do Torque aplicado é possível perceber que quanto maior for o tamanho da alavanca menor será o esforço necessário para parafusar a roda 7 Figura 13 Aplicação do Torque com um Torquimetro produto da Força aplicada e a dimensão da Ferramenta O torque conforme apresentado nas figuras 11 e 12 e quando há transmissões mecânicas forma de energia é produto de duas grandezas entre a força tangencial FT aplicada com ângulo de atuação de 𝑠𝑒𝑛 𝜃 definido e o raio r da peça O vetor torque pode ser calculado por meio do produto vetorial entre força e distância conforme a figura 14 e a equação a seguir 𝑀𝑇 𝐹𝑇 𝑑 𝑠𝑒𝑛 𝜃 8 Figura 14 Torque aplicado os esforços e a transmissão de movimento Fonte MELCONIAN 2011 Segundo Helerbroock na fórmula apresentada anteriormente θ é o ângulo formado entre o raio de rotação r e a força F No caso em que a força é aplicada com um ângulo de 90º em relação ao raio r o seno do ângulo é igual a 1 O raio r é determinado pela distância do ponto de aplicação até o eixo de rotação do corpo e também é conhecido como braço de alavanca Quanto maior for o braço de alavanca de um corpo mais fácil será rotacionálo E para determinar o módulo do torque pode ser calculado pelo produto da força vezes distância vezes 𝑠𝑒𝑛 do ângulo de 𝜃 Na nossa aplicação em Sistemas Mecânicos θ 90 e a inclinação da Força aplicada em sen θ 1 Considerando uma distância d r raio usualmente para os cálculos de Torque utilizase a equação abaixo 𝑀𝑇 𝐹𝑇 𝑟 Sendo A unidade do torque de acordo com o Sistema Internacional é Newton vezes metro Nm 9 MT Momento Torçor ou Torque Nm FT Força Tangencial N r raio m θ ângulo entre r e F graus Vamos aplicar Exercício 1 O velejador ao identificar a direção do vento gira uma manivela no sentido antihorário Com essa direção o vento tem uma maior eficiência no contato com a superfície da vela e isso gera uma Força F 50 N que é aplicada com ângulo θ de 45º em relação a um braço de alavanca de 025 m Desta forma o velejador poderá aproveitar a maior força aplicada e por um maior tempo Calcule o torque realizado sobre a manivela Dados sen θ ângulo 45º 22 Resolução 𝜏 𝑟 𝐹 𝑠𝑒𝑛𝜃 𝜏 025 50 𝑠𝑒𝑛 45 𝜏 025 50 2 2 𝜏 883 𝑁 𝑚 Exercício 2 A transmissão por correias representada na Figura 15 é composta pela polia motora 1 que possui diâmetro d1 100 mm e a polia movida 2 que possui diâmetro d2240 mm A transmissão é acionada por uma força tangencial Ft 600 N adaptado de MELCONIAN S Determine 1 Torque na polia 1 2 Torque na polia 2 10 Figura 15 Relação entre polias Fonte adaptado de MELCONIAN 2011 Solução Parte 1 Torque na polia 1 Figura 16 Relação da Força Tangencial aplicada em relação a polia 1 Fonte Adaptado de MELCONIAN 2011 𝑀𝑇1 𝐹𝑇 𝑟1 𝑟1 𝑑1 2 100 2 50 mm 50 103 m 𝑀𝑇1 600 𝑁 50 103 m 𝑀𝑇1 30 𝑁 𝑚 11 Parte 2 Torque na polia 2 Figura 17 Relação da Força Tangencial aplicada em relação a polia 2 Fonte Adaptado de MELCONIAN 2011 𝑀𝑇2 𝐹𝑇 𝑟2 𝑟2 𝑑2 2 240 2 120 mm 120 103 m 𝑀𝑇2 600 𝑁 012 𝑚 m 𝑀𝑇2 72 𝑁 𝑚 13 potência 131 A Potência definida pela Física Potência é uma grandeza física usada para calcular a quantidade de energia concedida ou consumida por unidade de tempo Em outras palavras é a taxa de variação da energia em função do tempo Assim a potência é útil para medir a rapidez com a qual uma forma de energia é transformada em outra Em nosso estudo será avaliado o quanto que uma energia mecânica é utilizada para a realização de um trabalho Dizemos que uma máquina é mais potente que as outras quando ela é capaz de realizar a mesma tarefa em um tempo menor ou ainda realizar uma quantidade maior de tarefas no mesmo intervalo de tempo 12 A definição de potência média é dada pelo trabalho realizado em função da variação de tempo P τ t Sendo P Potência média W τ Trabalho J Δt Intervalo de tempo s A unidade de medida da potência adotada pelo SI é o watt W unidade equivalente a joule por segundo Js A unidade watt foi adotada a partir de 1882 como forma de homenagear os trabalhos desenvolvidos por James Watt que foram de extrema relevância para o desenvolvimento das máquinas a vapor Segundo Helerbrock trabalho é a medida da transformação de uma forma de energia em outras formas de energia mediante a aplicação de uma força Sendo assim a definição de potência pode estar relacionada com qualquer forma de energia tais como energia mecânica energia potencial elétrica e energia térmica 132 Cálculo da potência Podemos determinar a potência realizada pela aplicação de uma força F que desloca um corpo de massa m em uma distância d Observe Figura 18 Representação de uma força F que desloca um corpo m em uma distância d Fonte HELERBROCK SDa 13 Na situação descrita acima podemos calcular a potência do movimento por meio da definição de potência média 𝑃 𝜏 𝑡 Para tanto é necessário recordar os Conceitos Fundamentais da Física e que trabalho realizado por um vetor força F conforme Figura 18 pode ser calculado por meio da seguinte fórmula 𝜏 𝐹 𝑑 𝑐𝑜𝑠 𝜃 Legenda F Força aplicada N d Distância percorrida m θ Ângulo formado entre F e d º 𝑡 Variação do Tempo s Reunindo as duas equações anteriores em uma só teremos a seguinte equação para o cálculo da potência relacionada a uma forma de energia qualquer 𝑃 𝐹 𝑑 𝑐𝑜𝑠 𝜃 𝑡 Legenda F Força aplicada N d Distância percorrida m θ Ângulo formado entre F e d º 𝑡 Variação do Tempo s Para os casos em que a força aplicada é paralela à distância percorrida pelo corpo o cosseno do ângulo θ terá seu valor máximo cos 0º 1 Portanto a potência média poderá ser calculada a partir da seguinte relação 𝑃 𝐹 𝑑 1 𝑡 14 mas 𝒅 𝒕 v logo P F v Legenda F Força aplicada N d Distância percorrida m θ Ângulo formado entre F e d º 𝑡 Variação do Tempo s v velocidade do corpo ms Após a dedução realizada acima da equação que relaciona trabalho e potência vemos que é possível calcular a potência como forma de energia que é transformada em um corpo Isso é possível se soubermos o módulo da força resultante que deverá ser multiplicado pela velocidade média percorrida pelo corpo ao longo de um percurso de distância de modulo com um valor d No entanto é necessário lembrar que a definição apresentada acima só é válida para valores constantes de Potência instantânea definida de forma equacionada Potência instantânea é a medida da quantidade de trabalho realizado em um processo durante um intervalo de tempo muito pequeno infinitesimal Podemos dizer portanto que a potência instantânea é a taxa de variação da quantidade de trabalho durante um intervalo de tempo que tende a zero Pinst τ t com t 0 Legenda Pinst Potência instantânea W Δτ Trabalho infinitesimal J Δt Intervalo de tempo infinitesimal s 15 Também temos a Potência instantânea de forma literal em associação direta com o experimento que James Watt realizou na Inglaterra A melhor definição da Potência Instantânea é quando se tem a necessidade de medir a energia de um trabalho em intervalo de tempo menor logo quanto menor o intervalo de tempo mais precisas serão as aferições da potência instantânea Assim para a aplicação de trabalho por um tempo tem a medida do Trabalho ou seja uma Energia Mecânica realizada Então 𝑃 𝑇𝑟𝑎𝑏𝑎𝑙ℎ𝑜 𝑇𝑒𝑚𝑝𝑜 𝜏 𝑡 como 𝜏 𝐹 𝑠 𝑃 𝐹𝑠 𝑡 sendo 𝜗 𝑠 𝑡 Equação da Velocidade logo podemos escrever 𝑃 𝐹𝑇 𝜗𝑝 A unidade da Potência no SI Sistema Internacional de Unidades é 𝑁 𝑚 𝑠 𝐽 𝑠 W Sendo 𝑃 Potência W 𝐹𝑇 Força Tangencial N 𝜗𝑝 Velocidade Periférica 𝑚 𝑠 Como forma de mensurar a Potência no início do século XVIII ao inventar a máquina a vapor James Watt apresenta sua descoberta ao povo inglês Ele faria a relação de quantos Cavalos referência naquele século seriam necessários para realizar o movimento de energia motriz como mostrado na Figura 19 Desta forma sua unidade de Watt W teria a correlação de Energia Mecânica realizada por meio de Cavalos até em sua unidade Cv 16 Figura 19 Representação do experimento de James Watt Fonte adaptado de MELCONIAN 2011 A forma utilizada para demonstrar a Potência é 𝐹 𝑄𝑚𝑎𝑥 76 kgf Carga máxima que o cavalo elevou com a velocidade de 1 𝑚 𝑠 assim resultando em 𝑃 𝐹 𝑣 𝑃 76𝑘𝑔𝑓 1 𝑚 𝑠 𝑃 76 𝑘𝑔𝑓 𝑚 𝑠 considerando 1 𝑘𝑔𝑓 980665𝑁 então 𝑃 76 980665 𝑁𝑚 𝑠 𝑃 7453 𝑁𝑚 𝑠 1𝑊 Da experiência de Watt surgiu o hp horse power vedado no SI Já na França a experiência foi repetida utilizando 𝑄𝑚𝑎𝑥 75 kgf que originou o cv cheval vapeur resultando em 𝑃 𝐹 𝑣 𝑃 75𝑘𝑔𝑓 1 𝑚 𝑠 𝑃 75 𝑘𝑔𝑓 𝑚𝑠 Como 1 𝑘𝑔𝑓 980665𝑁 então 𝑃 75 980665 𝑁𝑚 𝑠 𝑃 7355 𝑁𝑚 𝑠 1𝑊 Desta forma o cv é temporariamente permitido no SI 17 Agora que temos os conceitos de Torque e Potência definidos segue abaixo equações que podem ser aplicadas para determinar os valores de Torque Potência e até Velocidade Angular 𝝎 Considerando 𝑃 𝐹𝑇 𝑣𝑃 1 𝐹𝑇 𝑀𝑇 𝑟 2 𝑣𝑃 𝜔 𝑟 3 Substituindo 2 e 3 em 1 temos 𝑃 𝑀𝑇 𝑟 𝜔 𝑟 P 𝑀𝑇 𝜔 Ou ainda 𝑀𝑇 𝑃 𝜔 Considerando através da velocidade angular 𝜔 𝜋𝑛 30 Temos que 𝑀𝑇 30𝑃 𝜋𝑛 𝑁𝑚 Ou 𝑀𝑇 30000𝑃 𝜋𝑛 𝑁𝑚𝑚 Sendo 𝑃 𝑃𝑜𝑡ê𝑛𝑐𝑖𝑎 𝑊 𝑀𝑇 𝑀𝑜𝑚𝑒𝑛𝑡𝑜 𝑇𝑜𝑟ç𝑜𝑟 𝑁 𝑚 𝑛 𝑅𝑜𝑡𝑎çã𝑜 𝑟𝑝𝑚 𝜔 𝑉𝑒𝑙𝑜𝑐𝑖𝑑𝑎𝑑𝑒 𝑎𝑛𝑔𝑢𝑙𝑎𝑟 𝑟𝑎𝑑 𝑠 18 133 Força tangencial 𝐅𝐓 A força tangencial 𝐅𝐓 pode ser definida como o modulo de uma força que um objeto em movimento circular faz ao movimentarse em direção à tangente do círculo que ele percorre como no exemplo da trajetória circular realizada na Figura 110 A força centrípeta é a força que mantém o objeto na trajetória circular Assim sempre devese associar que o equilíbrio entre a força centrípeta e a força tangencial se obtém da trajetória circular Tendo o valor do módulo da Força Tangencial para se obter o esforço mecânico denominado de Torque devese realizar o produto da Força Tangencial e o raio da trajetória circular conforme representado na Figura 110 Figura 110 Representação da Força Tangencial Torque e Velocidade periférica Fonte adaptado de MELCONIAN 2011 A força tangencial é dada por 𝐹𝑇 𝑀𝑇 𝑟 𝑃 𝑉𝑃 𝑃 𝜔 𝑟 Sendo 𝐹𝑇 Força tangencial N 𝑀𝑇 Torque Nm r Raio do elemento m 19 P Potência W VP Velocidade periférica ms ω Velocidade angular rads Vamos Aplicar Exercício 3 O elevador da figura 111 foi projetado para transportar uma carga máxima Cmax 7000 N 10 pessoas O peso do elevador é Pe 1 kN e o contrapeso possui a mesma carga CP 1 kN Determine a potência do motor M para que o elevador se desloque com Velocidade constante de v 1 m s Figura 111 Representação do Sistema de elevação de carga Fonte MELCONIAN 2011 Solução Fazemos o diagrama de corpo livre deste sistema conforme Figura 112 20 Figura 112 Representação do diagrama de corpo livre do sistema em análise Fonte Adaptado de MELCONIAN 2011 O peso do elevador é compensado pelo do contrapeso logo a única carga a considerar á 𝐶𝑚𝑎𝑥 7000 𝑁 que é a força que atua no cabo Então 𝑃𝑚𝑜𝑡𝑜𝑟 𝐹𝑐𝑎𝑏𝑜 𝑣 𝑃𝑚𝑜𝑡𝑜𝑟 7000 𝑁 1𝑚𝑠 𝐹𝑐𝑎𝑏𝑜 𝐶𝑚á𝑥 Força do Cabo 7000 N 𝑣 𝑉𝑒𝑙𝑜𝑐𝑖𝑑𝑎𝑑𝑒 𝑝𝑒𝑟𝑖𝑓é𝑟𝑖𝑐𝑎 𝑚 𝑠 𝑃𝑚𝑜𝑡𝑜𝑟 7000 W Para obter na unidade em cv devemos dividir por 7355 𝑊𝑐𝑣 Então 𝑃𝑚𝑜𝑡𝑜𝑟 7000 𝑊 7355 𝑊 𝑐𝑣 𝑃𝑚𝑜𝑡𝑜𝑟 95 𝑐𝑣 Conclusão Neste Bloco foram apresentadas as grandezas fundamentais da mecânica e sua aplicação prática apresentando medidas Físicas e Mecânicas que serão fundamentais na descrição geometria e seu dimensionamento que sempre estará envolvido em um projeto de Sistema Mecânico 21 Além disso também foi estudada a correlação existente entre um movimento que realiza uma energia mecânica com um módulo de velocidade linear e se altera para um movimento circular ou seja realiza trajetórias lineares para circunferenciais mas como há mudança direcional de movimento linear para circular será utilizado para determinação da avaliação das velocidades lineares ms e incluemse as velocidades angulares 𝜔 e periféricas 𝜗 ex rads Também foi apresentada a grandeza mecânica do Torque que é o produto entre uma Força e um módulo de distância assim T F d NM resulta no Momento Torçor Dessa forma a trajetória conceitual que foi apresentada servirá como base para aplicar as novas grandezas físicas e mecânicas em projetos que deverão ser realizados em um sistema mecânico REFERÊNCIAS ANDRADE A S Elementos Orgânicos de Máquinas II UFP SD HELERBROCK R Potência e Rendimento Brasil Escola SDa Disponível em httpsbitly32doKeB Acesso em 13 abr 2021 HELERBROCK R Torque Brasil Escola SDb Disponível em httpsbitly3uS3w2p Acesso em 13 abr 2020 MELCONIAN S Elementos de Máquinas 9ª ed São Paulo Erica 2011 MOTT R L Elementos de máquinas em projetos mecânicos São Paulo 2015 NORTON R L Projetos de Máquinas Uma Abordagem Integrada 4ºed Porto Alegre Bookman 2013 SHIGLEY J E BUDYNAS R G NISBETT J K Elementos de máquinas de Shigley 8º ed São Paulo AMGH Editora Ltda 2011 22 2 CONCEITOS NO DIMENSIONAMENTO DE SISTEMAS MECÂNICOS Neste Bloco serão apresentadas as análises e cálculos dos esforços combinados Esforço Longitudinal e o Transversal em projetos de peças tendo como objetivo atender os limites de integridade sendo examinados os valores de propriedades mecânicas em principal e considerar também a influência da geometria da peça Ao longo do estudo deste bloco você verá a aplicação de conceitos apresentados em outras disciplinas já estudadas Resistência dos Materiais e Elementos de Máquina Afinal elas são de grande aplicação teórica para o entendimento na disciplina de Sistemas Mecânicos 21 ESFORÇOS COMBINADOS EM UM SISTEMA MECÂNICO Peças e equipamentos de maneira geral devem suportar os esforços a que estão sujeitos sem se romper São exceções a esta regra certos pinos de segurança que devem ser rompidos quando houver uma sobrecarga na máquina Assim não se deve permitir entretanto que um eixo quando solicitado tenha deformações permanentes Por isso a tensão máxima em qualquer ponto do eixo deve ser menor que a tensão de escoamento do material adotado Um elemento de máquina trabalhando com tensões abaixo da tensão de escoamento pode se romper quando os esforços forem realizados de forma cíclica Assim esse rompimento se dá devido ao material ter atingido seu limite de fadiga e por consequência acontece a ruptura Considerando a Força Axial e Radial a Figura 21 representa seus vetores momentos no plano que contribuem para a distribuição de Tensões Normais na seção Para o cálculo da Tensão Longitudinal sempre será considerada a relação dos esforços na direção normal assim será a razão entre a Força e a área aplicada sendo que esta tensão gerada no corpo pelos esforços normais dependendo da direção é definida e denominada como esforços de tração ou compressão 23 Figura 21 A representação dos Esforços Combinados como Longitudinais e Transversais Fonte BEER 2011 Cálculo da Tensão Normal ou Longitudinal 𝝈 aplicada 𝜎 𝑃 𝐴 N à Equação da carga Normal Longitudinal Onde 𝜎 Tensão Normal ou Longitudinal Nm2 ou Pa P Força aplicada na área transversal a Tensão Longitudinal Normal aplicadaN A Área da região que recebe o esforço ou tensão m2 que aplicada a um Eixo de seção cilíndrica A π r2 Sempre que é realizada a análise de esforços aplicados em um elemento mecânico qualquer durante a etapa de um Projeto Mecânico deve ser considerada a ocorrência de Tensões ou Esforços Tranversais e também Tensões ou Esforços Cortantes Tensão de Cisalhamento Desta forma para o cálculo do Limite admissível da Tensão Transversal que podem ocorrer como um Esforço de Momento Torçor ou um Esforço Cisalhante considerandose a área da seção longitudinal em análise sempre será necessário considerar a existência de aplicações no elemento de máquina ou sistema em análise na ocorrência de esforços Transversais e Longitudinais conforme Figura 22 e como revistos acima com o objetivo de que na sua solicitação de esforços máximos não seja gerada uma ruptura 24 Figura 22 A representação dos Esforços Combinados como Longitudinais e Transversais que podem variar dependendo do ponto em que está em relação aos esforços Fonte BEER 2011 Cálculo da Tensão Cisalhante Torçor ou Transversal 𝜏 aplicada 𝜏 𝑇 𝑐 𝐽 𝑁 𝑚2 𝑃𝑎 Onde T Torque Aplicado no Corpo C Raio do Corpo J Momento Polar de Inércia Detalhamento para Estudo Tabela 1 Para eixos cilíndricos à 𝐽 𝜋 2 𝑐4 Para relembrar os conceitos de Centro de Gravidade ou Momento Polar de Inércia ou seja onde ficam concentrados os Esforços ou Tensões que também já foram apresentados na disciplina de Resistência dos Materiais veja abaixo a tabela 21 que apresenta de maneira resumida os Momentos Polares de Inércia de Figuras com Geometrias Notáveis 25 Tabela 21 Equações de Momentos de Inércia Polares de Figuras Geométricas Notáveis Fonte BEER 2011 22 ANÁLISE DA PROPRIEDADE DA RIGIDEZ EM ESFORÇOS COMBINADOS Há peças que devem ser dimensionadas limitando suas deformações Um eixo por exemplo de uma caixa de mudança de velocidades não pode ter flexas excessivas para um bom funcionamento do conjunto O feixe de molas desse mesmo veículo será dimensionado para se conseguir uma certa flexa em cada condição de carga Analogamente temos limitações na deformação angular devido a torção imposta ao eixo 221 Custo de Fabricação É um dos critérios que oferece maior dificuldade ao projetista e está ligado a Tipo e Bitola da matéria à disposição Processo de Fabricação da Peça Número de Peças a serem produzidas 26 Além disso existem outros fatores que influenciam diretamente na vida útil do Elemento Mecânico ou peça como o desgaste pois onde há contato há atrito e ocorre o desgaste que se torna maior com o aumento da Temperatura e é influenciado pelo meio em que está devido à Corrosão Oxidação 23 ANÁLISE DA PROPRIEDADE DA RESISTÊNCIA Na disciplina Sistemas Mecânicos serão apresentados os esforços que a peça ou elemento de máquina a ser projetado sofrerá e que deverão atender diversas propriedades de resistência mecânica como o limite de escoamento e a resistência à fadiga quando o elemento ou peça for submetido a esforços Cíclicos Assim serão definidas quais características deverão compor o material a ser utilizado para a confecção da peça Então este material deverá resistir a Esforços Longitudinais eou Transversais Momento Torçor ou Esforço Cisalhante e que quando ocorrem juntos damos o nome de esforços mecânicos combinados 231 Pré Cálculo da Peça Neste subtema será estudada a forma de calcular os esforços atuantes para que as propriedades de resistência sejam atendidas no Projeto Vale lembrar que ao ser realizado um projeto e para que as propriedades de resistência sejam atendidas o projetista sempre irá analisar o Sistema Mecânico em equilíbrio Vale neste caso recordar uma forma mais simples de analisar esforços ou momento torçor e aplicar a Regra do Paralelograma para que seja possível determinar o valor do Vetor Resultante que conforme o exemplo a seguir na Figura 23 apresenta os vetores combinados e sua resultante Mz ou seja o momento resultante entre os vetores M1 e M2 Lembrando que temos a mesma regra para determinar o valor do Vetor de Momentos torçores e tensões e então determinar o valor da resultante em esforços longitudinais ou transversais Determinase os esforços ativos forças eou momentos provenientes de outros elementos de máquinas ou peças quando compõe um Sistema Mecânico aplicando a Regra do Paralelogramo conforme apresentado a seguir 27 Figura 23 Módulo do vetor resultante que segue sua geometria como paralelogramo e assim facilita o cálculo de seu valor Fonte Elaborado pelo autor Determinase os esforços reativos Impondose o equilíbrio da peça e em seguida traçamse os diagramas de momento Fletor e Torçor que atuam na peça por meio da aplicação da Regra do Paralelograma Veja que o exemplo a seguir segue a aplicação da Regra que considera a Figura 23 como referência na análise de equilíbrio de esforços 𝑀𝐸 𝑀1 𝑀2 ou 𝑀𝐸 𝑀12 𝑀2 2 Se 𝑀1 𝑀2 Constróise o Diagrama do Momento Torçor 𝑀𝑡 71620 𝑃 𝑛 Kgfcm Ou 𝑀𝑡 30 𝑃 𝜋 𝑛 Nm 28 Assim a próxima etapa será o cálculo do Momento Ideal 𝑀𝑖 Após obter o valor do Momento ou esforço resultante será obtido o Momento ou esforço resultante ideal e seu cálculo deverá ser realizado conforme as equações a seguir Será fundamental a análise do valor de 𝛼 𝐶𝑜𝑟𝑟𝑖𝑔𝑒 𝑜 𝑀𝑜𝑚𝑒𝑛𝑡𝑜 𝑇𝑜𝑟ç𝑜𝑟 e também será analisado o comportamento deste elemento de máquinas ou peça em condição de esforços ciclicos com uma frequência e formato de suas curvas de acordo com a figura 24 𝑀𝑖 𝑀𝐸 2 𝛼 𝑀𝑇2 𝛼 𝐶𝑜𝑟𝑟𝑖𝑔𝑒 𝑜 𝑀𝑜𝑚𝑒𝑛𝑡𝑜 𝑇𝑜𝑟ç𝑜𝑟 Figura 24 Curva S N em um Momento Ideal Caso Flexão e Torção Fonte SHIGLEY 2011 Sempre ao idealizar o projeto de uma peça ou elemento de máquina recebendo em sua aplicação esforços cíclicos devese ter em mente que independentemente da frequência do esforço cíclico deve ser analisado no projeto o tempo que as fibras externas e internas sofrerão diferentes tipos de esforços Sendo assim quando ocorre esforço de Flexão em uma fibra ou região da peça o outro extremo estará recebendo esforço Torçor e vice e versa conforme apresentado na figura 24 E com extrema importância temos o cálculo da resistência a Fadiga que é determinar o valor de 𝜶 e este sempre deve atender a condição de que seu valor seja menor ou igual a 1 29 𝛼 𝜎𝑐𝑎𝑠𝑜 𝑓𝑙𝑒𝑥ã𝑜 𝜏𝑐𝑎𝑠𝑜 𝑡𝑜𝑟çã𝑜 1 Assim determinando o Diâmetro do eixo 𝜎 𝑀𝑖 𝜋 𝑑3 32 232 Limite de Fadiga O conceito de Limite de Fadiga é a capacidade que o elemento de máquina ou eixo árvore terá em suportar um possível dano estrutural que é provocado por esforços cíclicos ou seja fenômeno este que quando ocorre reduz da propriedade de resistência do material e desta formaleva a ruptura A tabela 22 apresenta os Tipos de Solicitações de Esforços e correlaciona aos Tipos de Ciclos que pode ser simétrico ou pulsante Tabela 22 Correlação entre Esforços modos de Ciclos e suas equações Fonte Adaptado de SHIGLEY 2011 Tipo de Solicitação Ciclo Simétrico III Ciclo Pulsante II Flexão 𝜎𝑓 045 𝜎𝑟𝑢𝑝 𝜎𝑡𝑜 060 𝜎𝑟𝑢𝑝 𝜎𝑒 Tração Compresssão 𝜎𝑓 036 𝜎𝑟𝑢𝑝 𝜎𝑡𝑜 050 𝜎𝑟𝑢𝑝 𝜎𝑒 Torção 𝜏𝑓 022 𝜎𝑟𝑢𝑝 𝜏𝑜 030 𝜎𝑟𝑢𝑝 𝜏𝑒 30 Para aços de baixa liga à 𝜎𝑓 047 𝜎𝑟𝑢𝑝 Para aços de alta liga à 𝜎𝑓 053 𝜎𝑟𝑢𝑝 Para FoFo à 𝜎𝑓 042 𝜎𝑟𝑢𝑝 Além dos fatores do material os esforços e suas direções geram formas sendo que existem três formas fundamentais segundo as quais a carga pode operar sobre a ocorrência de uma trinca e cada um irá afetar um deslocamento diferente da superfície da trinca Figura 25 Modo I ocorre a abertura devido à concentração de tensões ou modo trativo as superfícies da trinca são tracionadas a parte Fonte adaptado de SHIGLEY 2011 Figura 26 Modo II ocorre a abertura devido ao deslizamento ou cisalhamento no plano as superfícies da trinca deslizam uma sobre a outra Fonte adaptado de SHIGLEY 2011 31 Figura 27 Modo III ocorre o rasgamento ou cisalhamento fora do plano as superfícies da trinca se movem paralelamente frente da trinca e uma a outra Fonte Adaptado de SHIGLEY2011 Conforme mencionado um eixo pode sofrer ruptura mesmo quando sujeito a tensões menores que a tensão de escoamento No ensaio de ruptura por flexão de um corpo de prova solicitado por tensões do caso III Tensão simétrica apresentada na tabela 22 seu comportamento seguirá a curva SN geral Abaixo são apresentados o comportamento e a forma da referida curva para cada tipo de material Figura 28 Curva S N de acordo com tensões cíclicas simétricas Tipo Ciclo Simétrico III Tabela 22 Fonte adaptado de SHIGLEY SD 32 O significado da curva SN vem das palavras em inglês Stress e Number of Cicles Estresse e Número de Ciclos também denominada de a Curva de Wohler Assim vemos que na Figura 28 é apresentada a Curva padrão do Stress aplicado a um determinado material e ao lado alguns exemplos de como cada material metálico tem comportamento diferente quando submetido a esforços cíclicos O que deve ser fixado conceitualmente é que a ocorrência de um estresse no material quando a tensão é elevada faz o corpo romperse antes de iniciar a rotação ou seja a ruptura será estática Para C 0 tem se 𝜎 𝜎𝑟𝑢𝑝𝑡𝑢𝑟𝑎 Sendo 𝜎1as solicitações a que está sujeito o corpo de prova para que a ruptura ocorra a 𝐶1 ciclos Aumentando a Vida Útil do Material para não ocorrer a fadiga conforme figura 28 Diminuindose a solicitação para 𝜎2 𝜎1 o rompimento se dará com um número de ciclos 𝐶2 𝐶1 Há uma tensão 𝜎𝑓 para qual o corpo pode ser solicitado durante infinitos ciclos 𝐶 sem ocorrer a ruptura 233 Cálculo de Concentrações de Tensões Outro cálculo prévio que deve ser realizado é o da tensão ou esforço aplicado na direção longitudinal de uma peça Esse cálculo pode não ser correto pois a presença de geometria Cantos vivos ou locais que geram uma maior concentração de tensões ou esforços conforme figura 28 podem acarretar em uma ruptura precoce também conhecida como fadiga Entretanto sua ocorrência se difere pois no ponto de concentração de Tensões ou Esforços há o aumento do valor da tensão aplicada e que não mais irá se distribuir mas sim concentrarse em uma região a ponto de gerar um rasgo conforme as figuras 25 26 27 e 29 33 Figura 29 Região sobre Tensão Aplicada com início da nucleação da Trinca Fonte adaptado de SHIGLEY 2011 𝜎 𝐹 𝐴 sendo F Força aplicada e A a área que é calculada entre a área base Para o exemplo a área é uma seção quadrangular e portanto é o produto das dimensões de suas laterais Se houver uma variação de seção como indicada na figura 29 temos que calcular a nova tensão 𝜎 𝜎 𝐹 𝐴0 𝐴2𝑏 assim a principal alteração será o valor no denominador ou seja calcular o valor da Área inicial 𝐴0 subtraindo o valor da nova Área 𝐴2𝑏 devido à nucleação que ocorreu Entretanto o grande objetivo da seleção do material e dimensionamento é para que esta última Tensão Normal não seja aplicada e seu valor nunca atingido desta forma mantemse a integridade da peça Dependendo então do tipo de singularidade teremos diferentes valores de 𝜎𝑚á𝑥 O quociente entre a máxima tensão 𝜎𝑚á𝑥 e a tensão calculada 𝜎 chamase concentração de tensões K 𝐾 𝜎𝑚á𝑥 𝜎 1 Lembrando 𝜎 𝐹 𝐴0 𝐴2𝑏 34 𝜎 à Tensão Cálculada 𝐴0 𝐴2𝑏 à Área útil O valor de K depende a Da geometria da singularidade forma de analisar e determinar valores de tensões aplicadas por meio do conceito que utiliza como exemplo um eixo circular Barra de metal modelo este ideal para auxílio dessa análise conforme já apresentado na disciplina de Resistência dos Materiais b Do Material da peça Conclusão Neste bloco foi apresentada a forma de análise e cálculo para evitar fraturas que acontecem devido a uma sobrecarga de tensões normais ou transversais podendo até serem de esforços com cargas combinadas Vimos também como caracterizar uma falha por fadiga e assim identificar e prevenir para que essa falha não ocorra mais tendo como fundamentos que devem ser analisados duas condições de projeto na engenharia Primeiramente o fator de uma Falha Mecânica em que as tensões eou tipo de esforços ocasionaram a falha e assim devemse analisar as forças atuantes na peça ou equipamento o tipo de esforço que está sendo submetido a ocorrência de forças excessivas ou qualquer carregamento que não seja da condição nominal do projeto ou Sistema Mecânico em análise Além disso cálculos dos esforços e carregamentos no sistema que podem e devem ser simulados por meio de ensaios experimentais de vibração e extensometria para a determinação do limite K da região da peça em estudo e que serão apresentados nas disciplinas de seleção de material de projetos na engenharia para que seja vista a segunda condição da causa a Falha metalúrgica que é ocasionada devido a defeitos metalúrgicos e que podem ser gerados ao longo do processo de fabricação Podendo ocorrer a descontinuidade na superfície fraturada a ocorrência de defeitos pontuais em ligações cristalinas entre outros Sendo que para identificar falha metalúrgica a matéria prima a ser utilizada na peça ou equipamento necessita de ensaios químicos metalográficos e caracterização das propriedades mecânicas do material 35 REFERÊNCIAS ANDRADE A S Elementos Orgânicos de Máquinas II UFP SD BEER F P et al Mecânica dos Materiais 5ª ed Porto Alegre AMGH 2011 MELCONIAN S Elementos de Máquinas 9ª ed São Paulo Erica 2011 MOTT R L Elementos de máquinas em projetos mecânicos São Paulo 2015 NORTON R L Projetos de Máquinas Uma Abordagem Integrada 4ºed Porto Alegre Bookman 2013 SHIGLEY J E BUDYNAS R G NISBETT J K Elementos de máquinas de Shigley 8 ed São Paulo AMGH Editora 2011 36 3 CONCEITOS NO DIMENSIONAMENTO DE EIXOS ÁRVORES Neste Bloco serão apresentadas as principais análises e seus cálculos para a seleção do material considerando a geometria e quais esforços combinados Esforço Longitudinal e o Transversal irão atuar para fundamentar os conceitos e realizar o projeto para o dimensionamento de eixos com o objetivo de atender os limites de integridade Para isto são analisados os valores de propriedades mecânica e a influência nas concentrações de tensões geradas na geometria ao longo do eixo em estudo para suportar suas condições de trabalho sem que haja um desgaste precoce com a ocorrência de uma fratura no eixo de forma que seja bemsucedido o projeto a ser realizado 31 MATERIAIS PARA APLICAÇÃO EM EIXOS Para se escolher um material para a fabricação de eixos devese considerar os seguintes fatores a Preço do material b Facilidade de obtenção no mercado da bitola a ser aplicada c Possibilidade de tratamento térmico e conhecer suas eventuais deformações d Ductilidade e Coeficiente de sensibilidade f Usinabilidade g Resistência à flexão e a torção h Resistência ao desgaste 37 São selecionados materiais metálicos de aço carbono e também os de aços ligas Eles devem ter em sua constituição valores de Carbono entre 03 até 07 C em média para Aumento da resistência Maior temperabilidade Menores deformações durante um tratamento térmico Agora ao ser aplicado o ferro fundido sua maior vantagem é o bom amortecimento de vibrações Podemos chegar a conclusão que os constituintes de elementos químicos metal ou ametal podem se combinar com o aço ou seja liga de ferro e carbono e ainda em sua composição com outros elementos sendo que estes podem melhorar as propriedades do material com a matéria prima que irá compor o projeto Segue a seguir na Tabela 31 a relação de nomenclatura em aços de baixa e média liga e sua percentagem de carbono correlacionando as Normas SAE DIN e os aços vilares bem como os níveis de níquel cromo molibdênio e outros Elementos estes que de acordo com a quantidade na composição química total dos aços melhoram os resultados das propriedades mecânicas como rigidez tenacidade resiliência elasticidade condutividade térmica ou elétrica e ponto de fusão 38 Tabela 31 Principais Aços para aplicação em produção de eixos e engrenagens SAEDIN para Villares Fonte MELCONIAN 2011 32 TEORIA DA TORÇÃO APLICADA EM EIXOS ÁRVORES Para o projeto de um eixo árvore a ser realizado a seleção do material deve ser tratada com fundamental importância bem como considerar sua geometria suas dimensões as condições em que os materiais serão utilizados e também as variáveis de esforços de carregamento Como exemplo temos as cargas que ocorrem em eixos de transmissão de rotação e que neste caso tem predominantemente esforços aplicados de dois tipos Eles são o de torção devido ao torque transmitido e o de Flexão devido às cargas transversais em engrenagens polias e catracas Assim na combinação dos dois tipos pode ocorrer carga axial também se a linha de centro do eixo for vertical O grande diferencial no projeto será em como avaliar e quais equações devem ser calculadas Então será apresentada uma sequência que será a melhor forma de avaliar conforme a Figura 31 O plano de ação do conjugado é igual ao plano da seção transversal Os conjugados são chamados de momentos de torção momentos torcionais ou torque T T e que têm a mesma intensidade T e sentidos opostos Nash1982 Ao ser analisado o Centro de Torção o ponto em torno do qual a seção transversal gira e que para seções simétricas coincide com o centro de gravidade vemos que o Eixo de Torção é o próprio lugar geométrico dos centros de torção 39 Um eixo circular está fixado a um suporte por uma de suas extremidades e aplicando à extremidade livre um momento de torção T o eixo gira e a seção transversal da extremidade apresenta uma rotação representada pelo ângulo φ chamado ângulo de torção BEER 2011 Figura 31 O eixo e o centro de torção gerado quando aplicado um Esforço Torçor Fonte adaptado de BEER 2011 Assim vemos na Figura 32 que a barra cilíndrica está fixada na Vertical ou na Horizontal Na Figura 33 temos que ao ser inserido um Momento de Torção Torque ou Momento Torçor ao longo de um comprimento L da barra esta será rotacionada e será gerada uma deformação ao longo de toda a barra por consequência do Momento Torçor aplicado Nestas condições descritas surgirá uma inclinação que será denominada de Ângulo de Torção φ variável fundamental para a análise do limite de resistência das propriedades mecânicas do material e do elemento mecânico em análise que em nosso estudo serão os eixos árvores Figura 32 Formação do ângulo de torção φ visto de formato em prisma circulares Fonte Adaptado de BEER 2011 40 Figura 33 O ângulo φ chamado ângulo de torção quando aplicado Torque no comprimento L Fonte Adaptado de BEER 2011 Quanto a análise dos esforços aplicados a um eixo árvore temos as fibras representadas como um prisma de seção circular conforme a Figura 32 ou Figura 34 e as condições que podem ser consideradas são a As geratrizes se transformam em hélices b O quadrado se transforma em um losango com os lados sofrendo a mesma deformação angular ângulo de torção φ c as seções normais permanecem planas e normais ao eixo de rotação e conservam sua forma Neste caso é preciso assegurar que os momentos sejam aplicados de tal forma que as extremidades também permaneçam planas e sem deformação 41 Figura 34 Linha central ou imaginária e as deformações ocorridas pelo esforço Torçor Fonte adaptado de BEER 2011 Por fim os critérios que são observados na Figura 34 acima nos apresenta que o Torque Momento Torçor aplicado ao eixo produzirá tensões de cisalhamento nas faces perpendiculares ao eixo As condições de equilíbrio requerem a existência de tensões iguais nas faces dos dois planos que contêm a linha central do eixo Também há existência dos componentes de cisalhamento axiais e que são demonstradas quando considerado um eixo composto de varetas axiais Sendo assim as varetas deslizam umas em relação às outras quando torques iguais e opostos são aplicados às extremidades do eixo Para atender as condições de equilíbrio as fibras nas faces externas e internas devem se equilibrar e por fim o eixo árvore atenderá sua condição de aplicação tanto no limite de resistência mecânica solicitada como também no aumento da vida útil 33 Cálculo da torção aplicada em eixos árvores Uma forma de realizar a determinação da distribuição de tensões de cisalhamento na seção transversal de deformação de cisalhamento γ é que ela deve ser igual ao ângulo formado por AB e AB 42 Figura 35 Eixo Circular de comprimento L com raio c e aplicado uma Torção Fonte adaptado de BEER 2011 Para melhorar o entendimento e a aplicação dos cálculos a seguir a barra cilíndrica conforme a Figura 36 deverá atender as seguintes condições a O eixo circular de comprimento L e raio c que foi torcido em um ângulo de torção φ b Retirando do interior do eixo um cilindro de raio ρ marcandose um quadrado sobre a superfície dele sem atuação de momento de torção c Aplicase a torção o quadrado se transforma em losango as deformações de cisalhamento são medidas pela variação de dois lados Figura 36 Eixo Circular de comprimento L em análise na seção AA Fonte adaptado de BEER2011 43 Por meio da Figura 36 você pode observar que quando γ é pequeno o comprimento de arco AA é dado por AALγ e na seção transversal AA ρ Φ A equação a ser utilizada para a determinação do ângulo de torção 𝛾 será 𝛾 𝜌 Φ 𝐿 sendo 𝛾 𝑒 𝜌 𝑒𝑚 𝑟𝑎𝑑𝑖𝑎𝑛𝑜 Onde 𝛾 𝐴𝑛𝑔𝑢𝑙𝑜 𝑑𝑒 𝑇𝑜𝑟çã𝑜 𝑛𝑜 𝑒𝑖𝑥𝑜 𝑐𝑖𝑟𝑐𝑢𝑙𝑎𝑟 𝜌 𝐴𝑛𝑔𝑢𝑙𝑜 𝑐𝑒𝑛𝑡𝑟𝑎𝑙 𝑑𝑒 𝑟𝑒𝑓𝑒𝑟ê𝑛𝑐𝑖𝑎 𝑞𝑢𝑎𝑛𝑑𝑜 𝑎𝑝𝑙𝑖𝑐𝑎𝑑𝑎 𝑎 𝑇𝑜𝑟çã𝑜 φ um ângulo de torção aplicado no eixo circular L Comprimento do eixo circular c raio do eixo circular Podese concluir que a deformação de cisalhamento em uma barra circular varia linearmente com a distância ao eixo da barra sendo o 𝛾𝑀á𝑥 na superfície da barra circular onde 𝜌 𝑐 𝛾𝑀á𝑥 𝑐 Φ 𝐿 e 𝛾 𝜌 𝑐 𝛾𝑀á𝑥 331 Tensões no Regime Elástico Quando considerada a torção T tem um valor tal que as tensões no material se mantêm abaixo da tensão de cisalhamento de escoamento 𝜏𝑒 Nesse caso as tensões no material permanecem abaixo dos limites de proporcionalidade e elasticidade Lei de Hooke conforme a Figura 37 que apresenta a Curva de um Material Dúctil no ensaio de Tensão por uma Deformação 44 Figura 37 Curva de um Ensaio de Tensão e Deformação de um material Dúctil Fonte Adaptado de SHIGLEY 2011 A tensão de cisalhamento na barra irá variar linearmente com a distância 𝜌 do eixo da barra 𝜏 𝐺 𝛾 𝐺 𝛾 𝜌 𝑐 𝐺 𝛾𝑀á𝑥 Então temse 𝜏 𝜌 𝑐 𝜏𝑀á𝑥 Da mesma forma a Tensão Máxima de Torção 𝜏𝑀á𝑥 𝑇 𝑐 𝐽 Considerando a Tensão de Cisalhamento a uma distância 𝜌 do eixo da barra 𝜏 𝑇 𝜌 𝐽 sendo J O momento de Inércia Polar de um círculo com raio c 𝐽 1 2 𝜋 𝑐4 45 A tensão de torção em uma barra de seção circular maciça ocorrerá como demonstrado na Figura 38 Desta forma irá variar linearmente com a distância ρ que inicia a ação deste esforço cisalhante no centro do eixo até a superfície externa da barra Figura 38 Distribuição das Tensões de Cisalhamento para um eixo circular maciço Fonte adaptado de BEER 2011 Caso seja aplicada a Tensão de Torção em uma barra vazada de raio externo 𝑪𝟐 Conforme a Figura 39 que apresenta a distribuição das tensões de cisalhamento para um eixo vazado o cálculo do Momento de Inércia Polar considerando o raio interno c1 e raio externo c2 Figura 39 Distribuição das Tensões de Cisalhamento para um eixo circular vazado Fonte adaptado de BEER 2011 Sendo o caso de avaliar o valor da Tensão Mínima de Cisalhamento com relação a Tensão Máxima de Cisalhamento em um eixo circular vazado temse 46 𝜏𝑀𝑖𝑛 𝑐1 𝑐2 𝜏𝑀á𝑥 O Momento de Inércia Polar será 𝐽 1 2 𝜋 𝑐24 𝑐14 Lembrando das variáveis e suas unidades por meio do Sistema Internacional SI T Nm c 𝜌 m J 𝑚4 𝜏 𝑁 𝑚4 Φ 𝛾 radianos 332 Ângulo de Torção no Regime Elástico Para este item vamos visualizar de acordo com a Figura 310 um eixo circular de comprimento L seção transversal uniforme de raio c Figura 310 Eixo Árvore maciço recebendo diferentes valores de Torção Fonte BEER 2011 O eixo está sujeito à ação de um momento de torção T O ângulo de torção φ e a deformação de cisalhamento máxima 𝛾𝑀á𝑥 estão relacionados por 𝛾𝑀á𝑥 𝑐 Φ 𝐿 47 No regime elástico 𝛾𝑀á𝑥 𝜏𝑀á𝑥 𝐺 Sendo γMáx τMáx G T c J G Para obter o valor do Ângulo de Torção portanto Φ 𝑇 𝐿 𝐽 𝐺 φ é expresso em radianos No regime elástico o ângulo de torção φ é proporcional ao momento de torção T aplicado no eixo circular A equação só pode ser usada no caso de material homogêneo para eixos de seção transversal constante e momentos aplicados nas extremidades da barra Eixos submetidos a momentos de torção aplicados em outros pontos com seções transversais compostas e o ângulo de torção φ do eixo circular é igual ao ângulo de rotação da extremidade livre De forma análoga e com a correta análise dos esforços Torçor aplicados ao longo do eixo AB representado na Figura 310 devese considerar quatro partes diferentes AC CD DE e EB O ângulo de torção total do eixo isto é o ângulo segundo o qual a seção A gira em relação a seção B será obtido somando algebricamente os ângulos de torção de dada parte do componente Então o ângulo de torção total será dado por ϕ Σ𝑖 𝑇𝑖 𝐿𝑖 𝐽𝑖 𝐺𝑖 Onde Ti Li Ji e Gi correspondem à parte i do eixo Podese escrever a potência mecânica transmitida H em W como 𝐻 𝑇 𝜔 48 Onde 𝜔 é a velocidade angular do eixo rads e o T o torque mensurado em Nm 𝜔 2 𝜋 𝑛 60 Vamos aplicar Exercício 1 Considere um sistema mecânico manivela que é utilizada em uma determinada etapa de processo de peneiramento em uma mineradora As condições de trabalho ou seja os esforços atuantes geometria e as dimensões estão representadas na Figura 311 assim pedese Figura 311 Representação da Manivela que será analisada Fonte BEER 2011 Considerando os valores de F 13 kN Eixo engastado com diâmetro de 20 mm Determinar a DCL Diagrama de Corpo Livre do eixo e do braço bem como todas as forças e momentos atuantes b Localizar um elemento de tensão em A e calcular as tensões atuantes c Determinar as tensões normais e cisalhamento máximas em A 49 Solução Item a Para obter os valores das tensões aplicadas ao sistema será analisado separadamente ou seja ponto a ponto da manivela figura 312 assim são obtidos os esforços atuantes e seus valores separados assim facilita para obter dados deste e outros itens deste exemplo Na extremidade C do braço BC F 13j kN Tc 005k kN m Na extremidade B do braço BC F 13j kN M1 013i kN m T1 005k kN m Na extremidade B do eixo AB F 13j kN T2 013i kN m M2 005k kN m Na extremidade A do eixo AB F 13j kN MA 066k kN m TA 013i kN M Figura 312 Representação do Diagrama de Corpo Livre DCL da manivela separada em nós Fonte BEER 2011 Continuação da Solução Item b Utilizandose as equações do círculo de Mohr no ponto A 50 𝜎𝑥 𝑀 𝐼 𝑐 32 660 𝜋 0023 8403 𝑀𝑃𝑎 𝜏𝑥𝑧 𝑇 𝐽 𝑐 16 130 𝜋 0023 828 𝑀𝑃𝑎 Item c 𝜎1 8484 𝑀𝑃𝑎 τ1 4282 MPa Vamos Aplicar Exercício 2 Considere também no processo de peneiramento de uma mineradora onde há um Sistema Mecânico um módulo redutor de velocidades com polias para a movimentação de minério Assim temos o sistema mecânico Eixo com polias Dados Eixo maciço de d 40 mm Diâmetro da Polia A à DB 100 mm e Diâmetro da Polia C à DC 200 mm Obter Determine a localização e magnitude das maiores tensões de cisalhamento tração e compressão no eixo Figura 313 Representação do Eixo com Polias Fonte BEER 2011 51 Solução DCL e Diagramas de momento fletor Figura 314 Diagrama Corpo livre e Cálculo do Momento Fletor em Eixo com Polias Fonte BEER 2011 Solução Tensões Solução 52 Figura 315 Representação dos esforços de Momento Fletor e os ângulos gerados na seção transversal da Manivela Fonte BEER 2011 Conclusão O fundamento principal deste Bloco é apresentar os conceitos em projetos de sistemas mecânicos e aplicar as variáveis elementares no projeto de um eixo árvore desde a seleção de material e geometria até as dimensões Por fim analisamos os esforços combinados que são aplicados durante o trabalho de um eixo árvore tendo aprendido uma aplicação em uma linha de produção considerando dois Sistemas Mecânicos Manivela e Eixo com Polias REFERÊNCIAS ANDRADE A S Elementos Orgânicos de Máquinas II UFP SD BEER F P et al Mecânica dos Materiais 5ª ed Porto Alegre AMGH 2011 MELCONIAN S Elementos de Máquinas 9ª ed São Paulo Erica 2011 MOTT R L Elementos de máquinas em projetos mecânicos São Paulo 2015 NORTON R L Projetos de Máquinas Uma Abordagem Integrada 4º ed Porto Alegre Bookman 2013 SHIGLEY J E BUDYNAS R G NISBETT J K Elementos de máquinas de Shigley 8ª ed São Paulo AMGH Editora Ltda 2011 53 4 CONCEITOS EM ENGRENAGENS CILÍNDRICAS DE DENTES RETOS ECDR Neste Bloco serão apresentados os principais conceitos de uma engrenagem item selecionado dentre uma extensa gama de elementos de máquinas que é utilizada no conjunto de um sistema mecânico Ao considerar o objetivo de aprendizagem foi selecionado o elemento de uma Engrenagem Cilíndrica de Dentes Retos ECDR assim serão apresentados os conceitos de suas aplicações a seleção de materiais que irá compor a engrenagem o processo de fabricação selecionado e suas especificações desde a geometria até todas as dimensões que por meio do memorial de cálculo que será definido comporá o projeto mecânico que ao final terá a resistência da engrenagem com os diversos esforços das cargas mecânicas e suportará sem fadigar e sofrer redução de vida útil 41 CARACTERÍSTICAS FUNDAMENTAIS DAS ENGRENAGENS DO MODELO ECDR As engrenagens são elementos de transmissão largamente utilizados em projeto de máquinas pois tem vantagens em sua utilização em sistemas mecânicos razão de transmissão constante relação potênciapeso elevados custo baixo em grandes produções rendimento elevado e sua variedade de formas de transmissão Veja a seguir os critérios fundamentais das Engrenagens Fabricação de engrenagens Qualidade das engrenagens Características gerais Tipos de engrenagens Engrenagens cilíndricas de dentes retos Características geométricas Dimensionamento 54 411 Processos de Fabricação de Engrenagens Os processos de fabricação de engrenagens podem ser realizados por a Usinagem b Fundição c Sem retirada de cavaco Veja a seguir como funciona cada processo A usinagem de engrenagens pode ser A usinagem por geração que utiliza fresas caracol conforme a Figura 41 Engrenagem de corte conforme a Figura 42 ou de Cremalheira de corte conforme a Figura 43 Sendo que entre os 3 processos pelo método de usinagem o mais utilizado na indústria é o de Engrenagem de corte Figura 42 a Usinagem de engrenagens Figura 41 Usinagem por fresa caracol Fonte ANDRADE SD 55 Figura 42 Usinagem por engrenagem de corte Fonte ANDRADE SD Figura 43 Usinagem por cremalheira de corte Fonte SHIGLEY 2011 Figura 44 Usinagem por fresa módulo Fonte ANDRADE SD 56 b Fundição de engrenagens A fabricação de engrenagens por fundição utiliza processos por gravidade demonstrado na Figura 5a sob pressão na Figura 5b ou em casca na Figura 5c que são apresentados a seguir A Figura 45 a a seguir nos apresenta de forma detalhada as etapas do processo de fabricação de engrenagens pelo método de Fundição por gravidade em que se inicia a etapa de fabricação nos seus moldes fixomóvel Começando pelos moldes fixo e móvel passando pelo cadinho com metal fundente que por gravidade energia potencial preenche os moldes para que ao final tenhamos nossa engrenagem Após este processo há apenas uma etapa de lixamento para que atenda aos dimensionais geométricos Figura 45 a Processo de fabricação das engrenagens pelo método de Fundição Ciclo do Processo de Fundição por gravidade Fonte Adaptado de KIMINAME CASTRO OLIVEIRA SD 57 A Figura 45 b a seguir nos apresenta o processo de fabricação de engrenagens pelo método sob pressão em que se inicia a etapa de fabricação nos seus moldes fixomóvel Começando pelos moldes fixo e móvel passando pelo sistema de pistão para a injeção de material fundente que por pressão finaliza o preenchimento dos moldes e ao final teremos a nossa engrenagem Após este processo há uma etapa de lixamento para que atenda aos dimensionais geométricos Figura 45 b Processo de fabricação das engrenagens pelo método de Fundição Ciclo do Processo sob pressão Fonte Adaptado de KIMINAME CASTRO OLIVEIRA SD A Figura 45 c a seguir nos apresenta o processo de fabricação de engrenagens pelo método em casca em que se inicia a etapa de fabricação nos seus moldes fixomóvel Começando pelo molde fixo e molde móvel em casca passando metal fundente na caixa basculada antes de ser inserida no forno térmico para que ao final tenhamos nossa engrenagem 58 Figura 45 c Processo de fabricação das engrenagens pelo método de Fundição Ciclo do Processo de Fundição em casca Fonte Adaptado de KIMINAME CASTRO OLIVEIRA SD c Sem retirada de cavaco Esse processo é dividido em dois subgrupos estampagem e forjamento O processo de estampagem ocorre por meio da pressão aplicada entre a matéria prima e o seu molde matriz para assim ser obtida a engrenagem Já o forjamento é classificado entre os processos de extrusão e trefilação laminação forjamento em matriz conforme Figura 46 59 Figura 46 Processo de fabricação de engrenagens pelo método sem retirada de cavaco Processo Forjamento Fonte Adaptado de KIMINAME CASTRO OLIVEIRA SD 412 Qualidade das Engrenagens O conceito de qualidade das engrenagens ocorre por meio das Normas DIN 862 e 867 que especifica as 12 principais características de qualidade Qualidade 1 Atualmente não utilizada pode ser usada quando não há uma referência da aplicação desta Engrenagem Qualidade 2 São utilizadas em indústria de precisão Relojoaria e aparelhos de precisão Qualidade 3 São utilizadas como padrão em laboratórios de controle Assim são consideradas engrenagens de precisão Qualidade 4 Utilizase na fabricação de engrenagens padrão engrenagens para aviação e engrenagens de alta precisão para torres de radar Qualidade 5 São utilizadas em aviões máquina operatrizes instrumentos de medida turbinas etc Qualidade 6 Utilizase em automóveis ônibus caminhões navios e mecanismo de alta rotação Qualidade 7 Engrenagens Sheivadas são empregadas em veículos máquinas operatrizes máquinas de levantamento e transporte etc Qualidade 8 e 9 São as mais empregadas pois não precisam ser retificadas Utilizamse em máquinas gerais 60 Qualidade 10 a 12 São engrenagens mais rústicas normalmente utilizadas em máquinas agrícolas Desta forma podese concluir que das 12 principais características de qualidade a Qualidade 1 é utilizada para aplicações com elevada precisão e segue até a Qualidade 12 cuja aplicação será mais rústica por exemplo em máquinas agrícolas moinhos de moagem de cana de açúcar etc 413 Aplicação Tipos e a Geometria de Engrenagens Cilíndricas de Dentes Retos ECDR Algo fundamental a saber é que os principais critérios e condições de aplicação de engrenagens estão descritas na norma DIN 862 e 867 que referencia os critérios de Geometria Conforme a engrenagem Figura 47 e também especificam o grau de qualidade materiais de fabricação quais processos de fabricação podem ser utilizados e por fim as dimensões que terá a engrenagem que será projetada para atender aos requisitos de resistência em condições de diversos esforços mecânicos e assim aumentar a sua vida útil Figura 47 Características geométricas conforme DIN 862 e 867 Neste acoplamento entre as engrenagens vemos a engrenagem de diâmetro maior Coroa e a de diâmetro menor Pinhão Fonte SHIGLEY 2011 61 Para facilitar a sequência de projeto iremos apresentar três tipos de nomenclaturas para as formas de acoplamento durante a transmissão de energia de uma ECDR 1 Engrenagens externas Em que a energia mecânica de transmissão gerada e seu acoplamento ocorrem de forma Externa conforme Figura 48 a Figura 48 a Exemplo do tipo de Engrenagem Cilíndrica de Dente Reto ECDR com engrenamento externo Fonte MELCONIAN 2011 2 Engrenagens internas em que a energia mecânica de transmissão gerada e seu acoplamento ocorrem de forma Interna conforme Figura 48 b Figura 48 b Exemplo do tipo de Engrenagem Cilíndrica de Dente Reto ECDR com engrenamento interno Fonte MELCONIAN 2011 3 Pinhão e cremalheira que geram a energia mecânica de transmissão e seu acoplamento também ocorre de forma Externa conforme Figura 48 c 62 Figura 48 c Exemplo do tipo de Engrenagem Cilíndrica de Dente Reto ECDR Pinhão e cremalheira Fonte MELCONIAN 2011 Os elementos mecânicos em análise neste Bloco são as Engrenagens Cilíndricas de Dentes Retos ECDR que serão dimensionadas conforme DIN 862 e 867 normas que ditam a geometria de cada elemento mecânico como as engrenagens Estas podem ter a geometria variada e por consequência diferentes referencias de nomenclatura e pontos de dimensões obtidos através do cálculo de projeto Esse cálculo tem como objetivo definir a propriedade mecânica de sua ruptura e tempo de duração da vida útil que dependem do tipo e horas diárias de funcionamento como você poderá ver mais à frente na Tabela AGMA 𝝋 Abaixo na Figura 49 serão apresentadas as cotas dos diâmetros principais de acordo com as normas DIN 862 e 867 63 Figura 4 9 Diâmetros principais de uma ECDR Fonte SHIGLEY 2011 Diâmetros principais Diâmetro primitivo 𝑑0 𝑚 𝑍 Diâmetro de base 𝑑𝑔 𝑑0 𝑐𝑜𝑠 𝛼 Diâmetro interno pé dente 𝑑𝑓 𝑑0 2 ℎ𝑓 Diâmetro externo cabeça do dente 𝑑𝑘 𝑑0 2 ℎ𝑘 Para determinar os diâmetros principais suas características geométricas e seus valores dimensionais de acordo com a Norma DIN 862 e 867 você verá na Tabela 41 as principais equações que deverão ser consideradas pelo projetista no Memorial de Cálculo do Projeto de um Sistema Mecânico que neste caso será a Engrenagem Cilíndricas de Dentes Retos ECDR 64 Tabela 41 Equações que determinam os valores que compõe a geometria de uma Engrenagem Cilíndrica de Dentes Retos ECRD Fonte MELCONIAN 2011 De acordo com as Normas DIN 862 e 867 a Figura 410 apresenta as terminologias utilizadas nas características geométricas de uma ECDR Número de dentes Z 𝑍 𝑑0 𝑚 Módulo m m t0 𝜋 Diâmetro primitivo 𝑑0 𝑑0 𝑚 𝑍 Diâmetro de base 𝑑𝑔 𝑑𝑔 𝑑0 𝑐𝑜𝑠𝛼0 Passo 𝑡0 𝑡0 𝑚 𝜋 Espessura do dente no primitivo 𝑆0 𝑡0 2 folga nula no flanco Altura comum do dente ℎ 2 𝑚 Altura da cabeça do dente ℎ𝑘 𝑚 Altura total do dente ℎ𝑧 22 𝑚 Altura do pé do dente ℎ𝑓 12 m Vão entre os dentes no primitivo 𝑙0 𝑡0 2 folga nula no flanco Ângulo de pressão 𝛼0 20 145 𝑜𝑢 25 Folga da cabeça 𝑆𝐾 02 𝑚 Relação da transmissão 𝑖 𝑍2 𝑍1 𝑑02 𝑑01 𝑛1 𝑛2 Largura do dente b 9m 𝑏 14m Distância entre centros 𝐶𝑐 𝑑01 𝑑02 2 65 Figura 410 Terminologias utilizadas nas Engrenagens Cilíndricas de Dentes Retos ECDR Fonte SHIGLEY 2011 42 DIMENSIONAMENTO DE ENGRENAGENS CILÍNDRICAS DE DENTES RETOS ECDR Neste item serão apresentadas as principais equações que serão utilizadas no dimensionamento de uma ECDR para atender ao limite e à aplicação deste elemento mecânico ao ser solicitada em um projeto Etapa 1 Dimensionamento com o Critério de desgaste As etapas de um projeto de um elemento mecânico engrenagens de dentes retos seguem dessa maneira Veja a seguinte expressão que deve ser utilizada no dimensionamento de pinhões com ângulo de pressão 20 e número de dentes de 18 a 40 Material utilizado na fabricação Material aço 𝑏1𝑑01 2 572 105 𝑀𝑡 𝑝2 𝑎𝑑𝑚 𝑖 1 𝑖 014 𝜑 Sendo que há 2 condições nesta expressão de Volume da base do dente 66 í𝑛𝑑𝑖𝑐𝑒 𝑒𝑛𝑔𝑟𝑒𝑛𝑎𝑔𝑒𝑛𝑠 𝑒𝑥𝑡𝑒𝑟𝑛𝑎𝑠 í𝑛𝑑𝑖𝑐𝑒 𝑒𝑛𝑔𝑟𝑒𝑛𝑎𝑔𝑒𝑛𝑠 𝑖𝑛𝑡𝑒𝑟𝑛𝑎𝑠 𝑜𝑢 𝑝𝑙𝑎𝑛𝑒𝑡á𝑟𝑖𝑎𝑠 Ambos os exemplos de Engrenamento Externo ou Interno foram apresentados na Figura 47 Seguem outras variáveis consideradas no cálculo acima b1 Largura do dente do pinhão mm d01 Diâmetro primitivo do pinhão mm MT Momento torçor do pinhão Nmm Padm Pressão admissível de contato Nmm2 𝒊 Relação de transmissão Z2Z1 adimensional 𝝋 Fator de serviço consultar tabela adimensional Etapa 2 Para o Dimensionamento de ECDR Pressão admissível 𝑝𝑎𝑑𝑚𝑖𝑠𝑠í𝑣𝑒𝑙 𝑝𝑎𝑑𝑚 0487 𝐻𝐵 𝑊1 6 𝑁 𝑚𝑚2 No exemplo que vamos aplicar mais à frente no enunciado do Estudo de Caso para Dimensionar uma ECDR serão fornecidos os valores de Dureza Horas de atividade do elemento mecânico e seu Valor de utilização Agma 𝜑 Assim falta o valor do Fator de Durabilidade W Seu cálculo é feito por meio da equação a seguir Fator de durabilidade W 𝑊 60 𝑛𝑝 ℎ 106 67 Em que Np Rotação do pinhão rpm h Duração do par horas HB Dureza Brinell Nmm2 A tabela 42 a seguir apresenta a correlação entre os tipos de material que podem ser utilizados na confecção de uma ECDR e os valores determinados por meio do método de ensaio de dureza Brinell Vale lembrar que não há uma equação de conversão entre os métodos dos Ensaios de Dureza mas existe uma tabela que correlaciona o valor obtido em diferentes métodos utilizados no ensaio A tabela 42 apresenta apenas como referência os Valores de HBrinell Mas para os tipos de aços descritos abaixo deverá ser utilizada a tabela Rockwell C HRc mesmo sendo só como referência Os aços são SAE 4320 SAE 4340 SAE 8620 SAE 8640 e temperados Tabela 42 Tabela de Dureza pelo Método Brinell Material HBRINELL 𝑵 𝒎𝒎𝟐 Aço fundido tipo 2 1700 2500 Aço fundido tipo 𝑩𝟐 1250 1500 Aço SAE 1020 1400 1750 Aço SAE 1040 1800 2300 Aço SAE 1050 2200 2600 Aço SAE 31453150 1900 2300 Aço SAE 4320 2000 4200 Aço SAE 4340 2600 6000 Aço SAE 8620 1700 2700 Aço SAE 8640 2000 6000 Aço fundido cinzento 1200 2400 Aço fundido nodular 1100 1400 Fonte MELCONIAN 2011 68 Já a Tabela 43 apresenta o conceito de determinação dos valores de dureza obtidos nos Ensaios de Dureza Uma importante informação não há uma equação ou uma tabela que ajude a realizar a conversão nos valores do Ensaio de Dureza pois cada valor é associado ao seu ensaio e tem particularidades de carga aplicada O elemento penetrador da superfície e a forma da impressão que será analisada de acordo com o método de ensaio e também com o valor de Dureza Brinnell HB solicitada na equação pode ser encontrada em catálogos ou em certificados de fabricação do lote produzido de Aço ou Ferro Fundido Estes terão as informações de Composição Química e as Propriedades Mecânicas com Tenacidade e sua Dureza conforme exemplo da Tabela 43 Tabela 43 Valores de correlação entre os valores obtidos nos Ensaios de dureza Brinell Resistência 𝑵 𝒎𝒎𝟐 Rockwell Impr mm Carga 30 kN Esfera Dureza HB 𝑵 𝒎𝒎𝟐 Aço carbono HB x 036 C Rc B Rb A Ra Shore Vickers 365 2270 997 29 104 646 39 279 370 2690 969 28 104 641 38 270 375 2620 943 26 103 636 37 263 380 2550 918 25 102 630 37 256 400 2290 824 21 98 608 33 229 Fonte adaptado de MELCONIAN 2011 No cálculo da expressão a seguir temos a relação entre a Largura da engrenagem b e o Diâmetro primitivo d0 e é determinado o valor de b d0 Então para ECDR e para o bom dimensionamento da engrenagem haverá duas condições 1 Engrenagem Biapoiada o valor é b d0 12 Característica as duas extremidades do eixo são apoiadas 2 Engrenagem em Balanço o valor é b d0 075 Característica uma das extremidades do eixo é apoiada 69 Confira como é a representação dessas expressões na figura 411 Figura 411 Representação das duas formas de uma ECDR se apoiar em um eixo Fonte MELCONIAN 2011 Na tabela 44 apresentada a seguir é definido o incremento no módulo após sua obtenção no cálculo do módulo de engrenamento de uma ECDR Este cálculo é usado para a fabricação de engrenagens no processo de fresamento e o módulo da ferramenta será o Módulo da engrenagem somado ao incremento Tabela 44 Correlação entre os valores dos Módulos normalizados DIN 780 e o incremento para a ferramenta de fabricação da engrenagem Módulo mm Incremento mm 03 a 10 010 10 a 40 025 40 a 70 050 70 a 160 100 160 a 240 200 240 a 450 300 450 a 750 500 Fonte adaptado de MELCONIAN 2011 Etapa 3 Esforços de flexão no pé do dente e os Tipos de Esforços gerados Normalmente para projetar escolhemos um critério para o dimensionamento e outro para a verificação No caso de engrenagens dimensionamos pelo desgaste e verificamos pelo critério de tensão no pé do dente Essa deve ser menor que a tensão admissível do material indicado 70 Durante a atividade desta engrenagem em um sistema mecânico de Transmissão de Movimentos Rotativos acontecerão Esforços de Flexão nos Pés dos Dentes da engrenagem ECDR Nas engrenagens cilíndricas de dentes retos ECDR são gerados dois esforços que geram uma Força de Flexão nos Pés dos Dentes da ECDR conforme apresentado na Figura 412 Os esforços são 1 Força tangencial 2 Força radial Figura 412 Representação da interação das forças Tangenciais e Radiais que gera Flexão no Pé dos Dentes de uma ECDR Fonte SHIGLEY 2011 Então as seguintes equações são aplicadas para obter o valor dos Esforços Para o caso de uma Força Tangencial 𝑭𝒕 veja a Figura 413 1 Força tangencial 𝑭𝒕 A carga tangencial Ft é responsável pelo movimento das engrenagens sendo também a carga que origina o momento fletor tendendo por flexão o pé do dente 71 A fórmula tangencial é determinada da seguinte maneira 𝐹𝑡 𝑀𝑡 𝑟0 2𝑀𝑡 𝑑0 raio primitivo 𝑟0 𝑑0 2 Em que Ft força tangencial N MT torque Nmm ro raio primitivo da engrenagem mm do diâmetro da engrenagem mm Figura 413 Força Tangencial aplicada e que gera esforço de Flexão no pé do dente Fonte SHIGLEY 2011 Então para obter o valor da Força Radial 𝑭𝒓 aplicada temos 2 Força radial 𝑭𝒓 A Força Radial atua na direção radial no Pé do Dente de uma engrenagem ECDR É determinada por meio da tangente do ângulo α ângulo de pressão tag 𝛼 𝐹𝑟 𝐹𝑡 Temos Fr Ft tag α 72 Em que Fr carga radial N Ft carga tangencial N α ângulo de pressão graus 3 Força resultante 𝐹r É a resultante Ft e Fr sendo determinada por meio de Pitágoras como segue Em que Fn carga resultante N Fr carga radial N Ft carga tangencial N Ou ainda pelas reações 𝑐𝑜𝑠 𝛼 𝐹𝑡 𝐹𝑛 𝐹𝑛 𝐹𝑡 𝑐𝑜𝑠 𝛼 As cargas radial e resultante serão importantes no dimensionamento de eixos e mancais sendo necessário o seu dimensionamento das engrenagens Etapa 4 Tensão máxima aplicada e a correlação entre a Tensão Material usada na fabricação da ECDR e o valor do esforço de Tensão de flexão no pé do dente A tensão atuante no pé do dente deve ser menor ou igual à tensão admissível do material indicado Veja a seguir fórmula que determina a intensidade da tensão máxima que a engrenagem sofrerá e que seu material de fabricação deverá resistir além de indicar os limites da Propriedades Mecânicas e a sua Vida Útil 𝜎𝑚á𝑥 𝐹𝑡 𝑞 𝜑 𝑏 𝑚𝑛 𝜎𝑚𝑎𝑡𝑒𝑟𝑖𝑎𝑙 73 Em que σ máx Tensão máxima atuante na base do dente Nmm2 𝝈 material Tensão admissível do material Nmm2 Ft Força tangencial N mn Módulo normalizado mm b Largura do dente do pinhão mm ϕ Fator de serviço tabela AGMA adimensional q Fator de forma adimensional Etapa 5 Cálculo do Fator de forma 𝑞 que deverá ser de acordo com o número de dentes entre as engrenagens como por exemplo Coroa e Pinhão com geometria de uma ECDR O fator de forma de engrenagem é obtido em função do número de dentes da engrenagem conforme apresentado na Tabela 45 Tabela 45 Correlação entre os valores do número de dentes e o fator de forma Fonte SHIGLEY 2011 Obs Se o número e dentes for intermediário aos apresentados na Tabela 45 será necessário realizar a operação matemática de interpolação tanto no número de dentes Z quanto no Fator de Forma q 74 Etapa 6 Obtémse nas tabelas a seguir o Valor dos Fatores de Serviço AGMA 𝝋 Este valor será considerado entre 2 condições ou seja 10 ou 24 horas de serviço para então obter o valor dos fatores de serviço AGMA conforme os exemplos apresentados a seguir nas Tabelas 46 e 47 Vale lembra que os valores do Fator de Serviço AGMA ϕ de uma engrenagem ECDR como exemplificados nas Tabelas 46 e 47 ficam sempre à disposição em catálogos de fabricantes de engrenagens ou elementos de máquinas aplicado a um sistema mecânico Tabela 46 Tabelas de fatores de serviço AGMA ϕ Fonte adaptado de MELCONIAN 2011 A Tabela 47 apresenta características fundamentais para o dimensionamento e a correta seleção do valor de acordo com as horas de serviço Esta condição altera a vida útil do projeto de um sistema mecânico Tabela 47 Continuação do exemplo de Tabelas de fatores de serviço AGMA ϕ para o acionamento de motores a explosão e serviços intermitentes Motor Elétrico Motor Elétrico Motores a Explosão Multicilíndricos 10 h 3 h 3 h 10 h 24 h 100 050 100 125 150 125 100 125 150 175 175 150 175 200 225 Fonte adaptado de MELCONIAN 2011 Aplicações Serviço Horas de Atividade 10 h 24 h AGITADORES Líquidos 100 125 Misturadores de polpa 125 150 Semilíquidos de densidade variável 125 150 ALIMENTADORES Alimentadores helicoidais 125 150 Alimentadores recíprocos 175 200 Transportadores esteira e correia 125 150 75 43 TENSÕES ADMISSÍVEIS Neste subtema serão avaliados e determinados os valores máximos de tensão do material para assim poder determinar qual material poderá ser utilizado na fabricação de uma ECDR Veja a seguir a tabela 48 com especificações das tensões admissíveis para os materiais Tabela 48 Tensões ideais para os materiais no dimensionamento de engrenagens MATERIAL Mpa 𝑵 𝒎𝒎𝟐 FoFo cinzento 40 FoFo nodular 80 Aço fundido 90 SAE 10101020 90 SAE 10401050 120 SAE 43204340 170 SAE 86208640 200 Mat Sintético Resinas 35 Fonte adaptado de MELCONIAN 2011 Algumas recomendações são indicadas Recomendação 1 O projeto ideal é aquele em que a tensão atuante no pé do dente está bem próxima da tensão admissível no seu limite inferior Se a tensão atuante estiver acima da tensão admissível 𝝈 a engrenagem pode não suportar a transmissão vindo a romper na base do dente prematuramente Se por outro lado a tensão atuante estiver bem aquém da tensão admissível a engrenagem estará superdimensionada tornandose antieconômica Recomendação 2 Ângulo de pressão 𝛼 Observe o par de dentes apresentado na Figura 414 a seguir 76 Iniciam o contato no ponto A A cinemática do mecanismo faz com que o ponto A descreva a trajetória AB No ponto B termina o contato entre os dentes O segmento de reta AB descrito pela trajetória do ponto de contato e a tangente comum aos diâmetros primitivos das engrenagens define o ângulo da pressão Pela norma DIN 867 recomendase a utilização do ângulo de pressão α 20 Figura 414 Trajetória demonstrada desde seu o início até o fim do contato entre dentes Fonte SHIGLEY 2011 Recomendação 3 A seguir serão apresentadas as Engrenagens com perfil cicloidal e as teorias relacionadas a elas Suas representações podem ser vistas nas figuras 415 416 417 e 418 Aplicações Esse tipo de engrenagem é limitada às construções mecânicas podendo ser encontrada em bombas ventiladores volumétricos relógios e aparelhos de precisão 77 Processos de Fabricação A engrenagem cicloidal é obtida por meio de estampagem trefilação brochamento ou injeção mecânica fina por fresamento ou aplainamento As ferramentas são mais caras pois possuem flancos retos O processo de fabricação por ser mais preciso tornase mais caro Curva Cicloidal Posição inicial Figura 415 Ambas as Figuras representam um contato entre engrenagens com curva cicloidal A curva cicloidal é obtida fazendo rolar o círculo 1 sobre o círculo 2 sem que ocorra escorregamento A trajetória do ponto A no movimento descreve a curva cicloidal Círculo 1 em movimento e Círculo 2 fixo Observe que à medida que o círculo 1 rola sem escorregamento sobre a periferia do círculo 2 o ponto A se desloca para a posição A1 formando o arco A A1 que representa parte da curva cicloidal A parte pontilhada da trajetória do ponto A é a trajetória a ser descrita pelo ponto na sequência do movimento Fonte SHIGLEY 2011 78 Engrenagem curva de envolvente A maioria absoluta das engrenagens utilizadas nas construções mecânicas é constituída de dentadura com perfil envolvente Isso ocorre em virtude de o processo de fabricação ser mais simples resultando em um menor custo Figura 416 Representação de um dente da engrenagem curva de envolvente Fonte SHIGLEY 2011 Para entender a representação da Figura 416 apresentada acima os seguintes pontos têm sua nomenclatura e sua teoria das características geométricas Ponto 1 Corda def é enrolada ao redor do cilindro e mantida esticada Ponto 2 Ponto b na corda é o ponto traçador ou seja a medida que a corda é enrolada e desenrolada ao redor do cilindro esse ponto irá traçar a curva evolvente ac Ponto 3 No ponto b o raio é exatamente a distância be Ponto 4 Raio de curvatura da evolvente é zero em a e um máximo em c 79 Ponto 5 de é normal em relação à evolvente em todos os pontos da intersecção e ao mesmo tempo sempre tangente ao cilindro A Seguindo a sequência de detalhamento das características geométricas para aplicação seguimos com o exemplo da Curva Envolvente e o quanto o início desta curva será considerado sendo apresentado a seguir na Figura 417 Figura 417 Engrenamento com dentadura de perfil evolvente Fonte SHIGLEY 2011 A seguir na Figura 418 temos o exemplo da utilização de uma engrenagem cicloidal com o perfil envolvente comumente utilizado em relógios 80 Figura 418 Perfil do engrenamento cicloidal normalmente utilizado em relógios Fonte SHIGLEY 2011 Vamos Aplicar Exercício Estudo de Caso Dimensionamento de engrenagens ECDR Roteiro para o dimensionamento de um par de engrenagens O pinhão engrenagem menor Item 1 da Figura 419 é o dimensionado pois se ele resistir ao esforço aplicado a coroa engrenagem maior Item 2 da Figura 419 suportará com folga a mesma carga por ser uma engrenagem maior Figura 419 Sistema Mecânico de transmissão de movimento entre pinhão e coroa Ambas são ECDR Fonte MELCONIAN 2011 Dimensionamento do pinhão Procedimento 81 1 Critério de pressão desgaste Para que não haja a ocorrência de uma Fadiga Superficial Crateração conforme Figura 420 deverão ser consideradas no cálculo durante o dimensionamento da engrenagem as seguintes etapas para realizar um bom e seguro projeto de engrenagens É importante lembrar que estamos aprendendo sobre engrenagens cilíndricas de Dentes Retos Figura 420 Ocorrência da Fadiga Superficial denominada de Crateração nos dentes de uma ECDR Fonte ANDRADE SD 11 Torque no pinhão 𝑀𝑇 30 𝜋 𝑃 𝑛 𝑁 𝑚 12 Relação de transmissão i 𝑖 𝑍2 𝑍1 13 Pressão admissível Padm deverá ser calculada conforme apresentado na equação a seguir e como foi visto na Etapa 2 Para o Dimensionamento de ECDR Pressão admissível 𝑝𝑎𝑑𝑚𝑖𝑠𝑠í𝑣𝑒𝑙 Para determinar seu valor deverão ser determinadas as seguintes variáveis Dureza pelo método Brinell e o fator de durabilidade padm 0487 HB W1 6 N mm2 82 131 Determinar a dureza Para a equação da tensão admissível será utilizado o valor de dureza pelo método Brinell que é obtido conforme exemplificado nas Tabelas 42 e 43 132 Fator de durabilidade W 𝑊 60 𝑛𝑝ℎ 106 Isolando o Fator de Durabilidade W 𝑊 1 6 𝑊 6 𝑊0168 133 Cálculo da pressão admissível Como foi calculado no item 13 deste exercício 𝑝𝑎𝑑𝑚 0487 𝐻𝐵 𝑊 1 6 Poderá ser calculado o valor da Máxima Tensão admissível para o projeto da engrenagem ECDR 134 Fator de serviço ϕ Obtémse na tabela AGMA Representados nas Tabelas 46 e 47 Ex O fator de serviço ϕ para eixo de transmissão e carga uniforme para funcionamento de 10 h diárias é Ao consultar o valor de AGMA à disposição em catálogos de fabricantes de engrenagens ou elementos aplicado a um sistema mecânico ϕ 1 eixo de transmissão carga uniforme 10hdia ϕ 1 tabela AGMA 14 Volume mínimo do pinhão Para determina o volume do Pé dos Dentes em engrenagens s ECDR utilizase a seguinte equação 83 b1 d0 2 572 105 MT padm2 i 1 i 014 φ Unidades no Sistema Internacional SI Índice Denominase x o 2 membro da equação Temse então Volume mínimo do pinhão 𝑏1 𝑑0 2 𝑥 15 Módulo do engrenamento O módulo do engrenamento é determinado por meio de 𝑏1 𝑑0 2 𝑥 Eq I Volume mínimo do pinhão 𝑏1 𝑑01 𝑦 𝑏1 𝑦 𝑑01 Eq II Substituindo II em I tem se 𝑦 𝑑0 𝑑01 2 𝑥 𝑑01 3 𝑥 𝑦 𝑑01 𝑥 𝑦 3 O módulo do engrenamento é determinado pela expressão do diâmetro primitivo 𝑑01 𝑚 𝑍1 Assim 𝑚 𝑑01 𝑍1 O módulo a ser utilizado será o normalizado mais próximo ao módulo calculado que será obtido por meio da tabela de módulos normalizados DIN780 84 𝑚𝑛 Módulo normalizado módulo da ferramenta que vai usinar a engrenagem 16 Diâmetro primitivo recalculado Definido o módulo da ferramenta é recalculado o diâmetro primitivo por intermédio de 𝑑01 𝑅 𝑚𝑛 𝑍1 17 Largura do pinhão 𝑏1 𝑥 𝑑01 𝑅 2 2 Critério de resistência à flexão no pé do dente A tensão máxima no pé do dente é expressa por meio de Figura 421 Apresenta a força tangencial aplicada e o esforço gerado no pé do dente Fonte SHIGLEY 2011 Considerando a equação que define a máxima tensão no pé do dente da engrenagem onde também é possível selecionar a melhor matéria prima para produção de uma engrenagem σmáx Ft q φ b mn σmaterial 85 21 Força tangencial FT 𝐹𝑇 2 𝑀𝑇1 𝑑01 2 𝑀𝑇2 𝑑02 𝑁 22 Fator de forma q Obtémse por meio da tabela 45 apresentada anteriormente neste Bloco 23 Módulo normalizado mn Obtémse por meio da tabela 44 24 Largura do pinhão b Mesmo do 18 Largura do pinhão b1 X d01 R 2 25 Por meio da equação da Tensão máxima atuante no pé do dente 𝝈𝒎á𝒙 e o valor da Tensão do Material 𝝈𝒎𝒂𝒕𝒆𝒓𝒊𝒂𝒍 é obtido o valor da largura do Pinhão b Ft q φ σmáx mn σmaterial Vamos Aplicar Para condição de aprendizagem no exercício proposto a seguir estará as informações dos valores das variáveis que serão aplicadas no dimensionamento que nesse bloco será realizado para uma Engrenagem de Dentes Retos ECDR Exercício 1 Dimensionar o par de engrenagens cilíndricas de dentes retos ECDR para que possa atuar com segurança na transmissão especificada em seguida A transmissão será acionada por um motor de P 15 CV 11 kW que atua com uma rotação de 1140 rpm ω 38 πrads O material a ser utilizado é o SAE 4340 A dureza específica é 58 HRC e a duração prevista para 10000h 86 As engrenagens atuarão em eixos de transmissão com carga uniforme com o tempo de serviço máximo de 10h diárias Figura 422 Sistema Mecânico de transmissão de movimento entre pinhão e coroa ambas são ECDR Fonte MELCONIAN 2011 Considere 𝑏1 𝑑01 025 Relação entre a largura e o diâmetro primitivo da engrenagem 𝛼 20 Ângulo de pressão 𝑍1 29 dentes pinhão 𝑍2 110 dentes coroa 11 Torque no pinhão 𝑀𝑇 30 𝜋 𝑃 𝑛 𝑁 𝑚 𝑀𝑇 30 𝜋 11000 1140 𝑁 𝑚 𝑀𝑇 9214 𝑁 𝑚 𝑀𝑇 92141 𝑁 𝑚𝑚 12 Relação de transmissão i 𝑖 𝑍2 𝑍1 𝑖 110 29 3793 𝑖 379 87 13 Pressão admissível 131 Fator de durabilidade W 𝑊 60 𝑛𝑝 ℎ 106 𝑊 60 1140 1 104 106 𝑊 60 1140 1 102 𝑊 684 como 𝑊 1 6 297 132 Cálculo da pressão padm 0487 HB W 1 6 𝑝𝑎𝑑𝑚 0487 6000 297 𝑝𝑎𝑑𝑚 0487 6000 297 𝑝𝑎𝑑𝑚 983838 984 102 𝑁 𝑚𝑚2 A dureza de 58 HRC corresponde a 6000 HB ou seja 6000 Nmm2 14 Fator de serviço ϕ Obtémse na tabela AGMA O fator de serviço ϕ para eixo de transmissão carga uniforme para funcionamento de 10 h diárias é ϕ 1 tabela AGMA 88 15 Volume mínimo do pinhão 𝑏1 𝑑0 2 572 105 𝑀𝑇 𝑝𝑎𝑑𝑚2 𝑖 1 𝑖 014 𝜑 𝑏1 𝑑0 2 572 105 92140 984 1022 379 1 379 014 1 𝑏1 𝑑0 2 572 105 92140 9842 1022 479 393 1 𝐿𝑒𝑚𝑏𝑟𝑎𝑛𝑑𝑜 𝑎 𝑐𝑜𝑛𝑑𝑖çã𝑜 𝑒𝑥𝑝𝑜𝑛𝑒𝑛𝑐𝑖𝑎𝑙 1022 104 𝑏1 𝑑0 2 66343 𝑚𝑚3 𝑏1 𝑑0 2 66343 104 𝑚𝑚3 16 Módulo de engrenamento b1 d0 2 66343 mm3 I b1 d01 025 b1 025 d01 II Substituindo II em I 025 d01 d0 2 66343 mm3 d01 3 66343 025 d01 66343 025 265372 mm3 d01 265372 mm3 3 d01 6426 mm Portanto 𝑚 𝑑01 𝑍1 643 29 𝑚 221 𝑚𝑚 89 Por meio da DIN 780 conforme tabela 47 incremento de 025 fixase o módulo da ferramenta em 𝑚𝑛 225 𝑚𝑚 Módulo normalizado DIN 780 17 Recálculo do diâmetro primitivo do pinhão 𝑑01𝑅 𝑚𝑛 𝑍1 𝑑01𝑅 225 29 𝑑01𝑅 6525 𝑚𝑚 18 Largura do pinhão 𝑏1 𝑑01𝑅 2 66343 𝑏1 66343 𝑑01𝑅 2 66343 65252 𝑏1 16 mm 2 Resistência à flexão no pé do dente 21 Força tangencial FT 𝐹𝑇 2 𝑀𝑇1 𝑑01𝑅 𝑁 𝐹𝑇 2 92140 𝑁𝑚𝑚 6525 𝑚𝑚 𝐹𝑇 285 𝑁 22 Fator de forma q Como Z1 29 dentes encontramos na tabela fator q 30835 23 Fator de serviço ϕ Obtémse na tabela AGMA 90 O fator de serviço ϕ para eixo de transmissão carga uniforme para funcionamento de 10 h diárias é Ao consultar o valor de AGMA à disposição em catálogos de fabricantes de engrenagens ou elementos aplicado a um sistema mecânico ϕ 1 eixo de transmissão carga uniforme 10hdia ϕ 1 tabela AGMA 24 Módulo normalizado O mesmo do item 16 de acordo com tabela 46 𝑚𝑛 225 mm DIN 780 25 Largura do pinhão b O mesmo do item 18 𝑏1 16 𝑚𝑚 26 Tensão máxima atuante no pé do dente 𝜎𝑚á𝑥 𝐹𝑡 𝑞 𝜑 𝑏 𝑚𝑛 𝜎𝑚𝑎𝑡𝑒𝑟𝑖𝑎𝑙 𝜎𝑚á𝑥 2825 30835 1 16 225 𝜎𝑚𝑎𝑡𝑒𝑟𝑖𝑎𝑙 𝜎𝑚á𝑥 242 𝑁 𝑚𝑚2 27 Análise do dimensionamento Como a tensão máxima atuante é superior à tensão admissível do material concluise que o pinhão será redimensionado 𝜎4340 170 𝑁 𝑚𝑚2 de acordo com a tabela 48 𝜎𝑚á𝑥 242 𝑁 𝑚𝑚2 𝜎4340 170 𝑁 𝑚𝑚2 91 Com a condição não atendida da Tensão máxima aplicada no pé do dente da engrenagem ECDR o valor da tensão do material inicialmente selecionado não atenderá aos esforços deste elemento mecânico a ECDR Assim o recálculo terá de ser feito com os seguintes itens a serem alterados como sugestão Selecionar outro material exemplo Aço 1020 𝜎1020 300 𝑁 𝑚𝑚2 𝜎4340 170 𝑁 𝑚𝑚2 assim atenderá a solicitação de flexão no pé do dente Alterar Largura do pé do dente b Número de dentes Z ou Diâmetro primitivo da engrenagem 𝑑0 Assim deverá realizar todo o roteiro de cálculo sugerido 28 Redimensionamento do pinhão 281 1ª Hipótese mantémse o módulo e fazse o redimensionamento da largura b utilizando a tensão admissível do material SAE 4340 Como σ4340 170 N mm2 vem que b Ft q φ σ4340 mn b 2285 30835 1 170 225 b 23 mm Para esse dimensionamento temos um pinhão com as seguintes características Número de dentes Z1 29 dentes Módulo mn 225 mm Diâmetro primitivo 𝑑01𝑅 6525 𝑚𝑚 Largura 𝑏 23 𝑚𝑚 282 Relação largura b diâmetro primitivo do b1 d01 23 6525 035 92 Portanto b1 d01 035 12 a engrenagem está dentro das especificações 283 2ª hipótese mantémse a largura alterando o módulo da 𝒃𝟏 16 mm engrenagem e consequentemente o diâmetro primitivo e a força tangencial 284 Alterase também o valor do módulo normalizado 𝒎𝒏 275 mm pois a tensão admissível está bem aquém da tensão máxima obtida 285 Diâmetro primitivo d01R Z1 mn d01R 29 275 d01R 7975 mm 286 Força tangencial FT FT 2 MT1 d01R N FT 2 92140 7975 N FT 2310 N 287 Tensão máxima atuante σmáx Ft q φ b1 mn σmáx 2310 30835 1 16 275 σmáx 162 N mm2 288 Análise do dimensionamento Como a 𝜎𝑚á𝑥 162 𝑁 𝑚𝑚2 𝜎4340 170 𝑁 𝑚𝑚2 concluise que a engrenagem está em perfeitas condições de utilização 93 289 Relação entre largura e diâmetro primitivo 𝑏1 𝑑01 16 7975 02 Portanto 𝑏1 𝑑01 02 12 a relação encontrase dentro da especificação indicada Para esse dimensionamento temos um pinhão com as seguintes características Número de dentes 𝑍1 29 dentes Módulo 𝑚𝑛 275 mm Diâmetro primitivo 𝑑01𝑅 7975 𝑚𝑚 Largura 𝑏 16 𝑚𝑚 Conforme apresentado na Tabela 41 temos as equações para determinar os valores das dimensões requerida nas Normas DIN 862 e 867 Já a Tabela 49 a seguir se refere as características geométricas de uma ECDR de acordo com as Normas DIN 862 e 867 94 Tabela 49 Formulário das variáveis fundamentais do projeto de uma ECDR Fonte adaptado de MELCONIAN 2011 A Tabela 410 a seguir é uma continuação da Tabela 49 Tabela 410 continuação Formulário das variáveis fundamentais do projeto de uma ECDR Formulário Pinhão mm Coroa mm Espessura do dente no primitivo folga nula no flanco 𝑆0 𝑡0 2 𝑆0 𝑡0 2 864 2 432 𝑆0 𝑡0 2 864 2 432 Formulário Pinhão mm Coroa mm Módulo normalizado DIN 780 𝑚𝑛 275 𝑚𝑛 275 Passo 𝑡0 𝑡0 𝑚𝑛 𝜋 𝑡0 275 𝜋 864 𝑡0 275 𝜋 864 Vão entre os dentes no primitivo folga nula no flanco 𝑙0 𝑡0 2 𝑙0 864 2 432 𝑙0 864 2 432 Altura da cabeça do dente ℎ𝑘 𝑚𝑛 ℎ𝑘 275 ℎ𝑘 275 Altura comum do dente ℎ𝑓 12 𝑚𝑛 ℎ𝑓 12 275 33 ℎ𝑓 12 275 33 Altura comum do dente ℎ 2 𝑚𝑛 ℎ 2 275 55 ℎ 2 275 55 Altura total do dente ℎ𝑧 22 𝑚𝑛 ℎ𝑧 22 275 605 ℎ𝑧 22 275 605 95 Folga da cabeça 𝑆𝐾 02 𝑚𝑛 𝑆𝐾 02 275 055 𝑆𝐾 02 275 055 Diâmetro primitivo 𝑑0 𝑑0 𝑚𝑛 𝑍 𝑑0 𝑚𝑛 𝑍1 𝑑0 275 29 𝑑0 7975 𝑑0 𝑚𝑛 𝑍2 𝑑0 275 110 𝑑0 3025 Fonte adaptado de MELCONIAN 2011 A Tabela 411 a seguir é uma continuação da Tabela 410 e se refere as características geométricas de uma ECDR de acordo com as Normas DIN 862 e 867 Tabela 411 continuação Formulário das variáveis fundamentais do projeto de uma ECDR Fonte adaptado de MELCONIAN 2011 Formulário Pinhão mm Coroa mm Diâmetro de base 𝑑𝑔 𝑑𝑔 𝑑0 𝑐𝑜𝑠𝛼0 𝑑𝑔1 𝑑01 𝑐𝑜𝑠𝛼0 𝑑𝑔1 7975 𝑐𝑜𝑠 20 𝑑𝑔1 7494 𝑑𝑔2 𝑑02 𝑐𝑜𝑠𝛼0 𝑑𝑔2 3025 𝑐𝑜𝑠 20 𝑑𝑔2 28425 Diâmetro interno 𝑑𝑓 𝑑0 24𝑚𝑛 𝑑𝑓1 𝑑01 24𝑚𝑛 𝑑𝑓1 7975 24 275 𝑑𝑓1 7315 𝑑𝑓2 𝑑02 24𝑚𝑛 𝑑𝑓2 3025 24 275 𝑑𝑓1 2959 Diâmetro externo 𝑑𝑘 𝑑0 2𝑚𝑛 𝑑𝑘1 𝑑01 2𝑚𝑛 𝑑𝑘1 7975 2 275 𝑑𝑘1 8525 𝑑𝑘2 𝑑02 2𝑚𝑛 𝑑𝑘2 3025 2 275 𝑑𝑘2 308 Distância entre centros 𝐶𝑐 𝑑01 𝑑02 2 7975 3025 2 𝐶𝑐 19112 Largura das engrenagens 𝑏1 𝑏2 16 96 Conclusão Neste bloco nós estudamos o vasto universo dos elementos de máquinas Além disso revisamos a disciplina de resistência dos materiais Foi apresentado o elemento engrenagens como referência na aplicação de um Projeto Mecânico frente as etapas que devem ser seguidas abordando a seleção do material o tipo de processo de fabricação utilizado as geometrias e como dimensionar para obter uma Engrenagem Cilíndrica de Dentes Retos ECDR para assim termos o completo Memorial de Cálculo do elemento mecânico em questão e que neste exemplo compõe um Sistema Mecânico Referências Bibliográficas ANDRADE A S Elementos Orgânicos de Máquinas II UFP SD KIMINAMI C S CASTRO W B OLIVEIRA M F Introdução aos processos de fabricação de produtos metálicos São Paulo Blucher 2013 MELCONIAN S Elementos de Máquinas 9ª ed São Paulo Erica 2011 MOTT R L Elementos de máquinas em projetos mecânicos São Paulo 2015 NORTON R L Projetos de Máquinas Uma Abordagem Integrada 4º ed Porto Alegre Bookman 2013 SHIGLEY J E BUDYNAS R G NISBETT J K Elementos de máquinas de Shigley 8ª ed São Paulo AMGH Editora Ltda 2011 97 5 CONCEITOS EM ENGRENAGENS CILÍNDRICAS DE DENTES HELICOIDAIS ECDH Este Bloco em sua grande parte será uma extensão dos conceitos apresentados no Bloco 4 Engrenagens Cilíndricas de Dentes Retos ECDR Porém ao analisar já para a condição de projeto de uma Engrenagem Cilíndricas de Dentes Helicoidais ECDH sua aplicação e geometria possuem particularidades que devem ser seguidas no seu dimensionamento e também onde quer que seja aplicado no conjunto de um sistema mecânico em que a engrenagem será utilizada Ainda haverá a condição de mais um ângulo denominado como 𝜷 devido à inclinação apresentada nos dentes desta engrenagem e que altera a sua geometria além de manter ângulo de pressão 𝜶 assim a mudança na geometria nos dentes e a condição de mais um ângulo serão apresentados e também como deverá ser o dimensionamento para realizar um correto projeto mecânico 51 CARACTERÍSTICAS FUNDAMENTAIS DAS ENGRENAGENS DO MODELO ECDH As engrenagens ECDH são caracterizadas pela inclinação dos dentes em relação ao eixo geométrico da roda e suas vantagens são a alta resistência e trabalho silencioso São aplicadas quando se faz necessário resistir a grandes esforços como em caixa de redução de câmbio etc Também permitem transmitir potências maiores com rotação variada Dentre os tipos de engrenagens helicoidais ECDH as engrenagens para rosca sem fim se destacam quando a redução de velocidade na transmissão do movimento se faz necessária Podemos concluir que as Engrenagens Cilíndricas de Dentes Helicoidais ECDH possuem de forma geral como característica a transmissão de rotação entre eixos diversos não paralelos além de apresentarem um ruído menor do que as Engrenagens Cilíndricas de Dentes Retos ECDR 98 Veja a seguir os critérios fundamentais das Engrenagens Fabricação Qualidade Características gerais Tipos de engrenagens Engrenagens cilíndricas de dentes retos Características geométricas Dimensionamento 511 Processos de Fabricação de Engrenagens Os processos de fabricação de engrenagens podem ser realizados por a Usinagem b Fundição c Sem retirada de cavaco 512 Qualidade das Engrenagens O conceito de qualidade das engrenagens ocorre por meio das Normas DIN 862 e 867 que especificam as 12 principais características de qualidade Qualidade 1 Atualmente não utilizada pode ser usada quando não há uma referência da aplicação desta Engrenagem Qualidade 2 São utilizadas em indústria de precisão Relojoaria e aparelhos de precisão Qualidade 3 São utilizadas como padrão em laboratórios de controle Assim são consideradas engrenagens de precisão Qualidade 4 Utilizase na fabricação de engrenagens padrão engrenagens para aviação e engrenagens de alta precisão para torres de radar 99 Qualidade 5 São utilizadas em aviões máquina operatrizes instrumentos de medida turbinas etc Qualidade 6 Utilizase em automóveis ônibus caminhões navios e mecanismo de alta rotação Qualidade 7 Engrenagens Sheivadas são empregadas em veículos máquinas operatrizes máquinas de levantamento e transporte etc Qualidade 8 e 9 São as mais empregadas pois não precisam ser retificadas Utilizamse em máquinas gerais Qualidade 10 a 12 São engrenagens mais rústicas normalmente utilizadas em máquinas agrícolas Podese concluir que das 12 principais características de qualidade a Qualidade 1 é utilizada para aplicações com elevada precisão e segue até a Qualidade 12 cuja aplicação será mais rústica por exemplo em máquinas agrícolas moinhos de moagem de cana de açúcar etc 513 Aplicação Tipos e a Geometria de Engrenagens Cilíndricas de Dentes Helicoidais ECDH Os principais critérios e condições de aplicação de engrenagens estão descritos na norma DIN 862 e 867 Estas normas referenciam os critérios de Geometria De acordo com a engrenagem das figuras 52 e 53 e também especificam o grau de qualidade materiais de fabricação quais processos de fabricação podem ser utilizados e por fim as dimensões que terá a engrenagem a ser projetada para que atenda aos requisitos de resistência em condições de diversos esforços mecânicos e para que possa aumentar a sua vida útil As Engrenagens Cilíndricas de Dentes Helicoidais se apresentam em três tipos de nomenclaturas para as formas de acoplamento durante a transmissão de energia 100 Figura 51 a Exemplo de Engrenagem Cilíndrica de Dentes Helicoidais ECDH Engrenagens Externas Fonte MELCONIAN 2011 Figura 51 b Exemplo de Engrenagem Cilíndrica de Dentes Helicoidais ECDH Engrenagens Internas Fonte MELCONIAN 2011 Figura 51 c Exemplo de Engrenagem Cilíndrica de Dentes Helicoidais ECDH Engrenagens Cônicas Fonte MELCONIAN 2011 101 O elemento mecânico em análise são as Engrenagens Cilíndricas de Dentes Helicoidais ECDH que serão dimensionadas conforme DIN 862 e 867 As características geométricas de um elemento mecânico como as engrenagens podem variar Dessa forma ocorrerá a variação das referências de nomenclatura e dos pontos de dimensões obtidas por meio do cálculo de projeto Este cálculo define a propriedade mecânica até sua ruptura e tempo de duração da vida útil e isso depende do tipo de aplicação e horas diárias de funcionamento Você poderá ver esses dados mais à frente nas Tabelas 511 e 512 AGMA 𝝋 Figura 52 Representação da geometria e em detalhe a inclinação 𝜷 de uma ECDH Fonte SHIGLEY 2011 102 Figura 53 Apresenta todas as dimensões com geometria e as nomenclaturas de uma ECDH Fonte SHIGLEY 2011 Diâmetros principais Diâmetro primitivo 𝑑0 𝑍 𝑚𝑠 Diâmetro de base 𝑑𝑔 𝑑0 𝑐𝑜𝑠 𝛼𝑠0 Diâmetro interno pé dente 𝑑𝑓 𝑑0 2 ℎ𝑓 Diâmetro externo cabeça do dente 𝑑𝐾 𝑑0 2 ℎ𝑘 Para determinar os diâmetros principais suas características geométricas e seus valores dimensionais de acordo com a Norma DIN 862 e 867 você verá na Tabela 51 as principais equações que deverão ser consideradas pelo projetista no Memorial de Cálculo do Projeto de um Sistema Mecânico que neste caso será da Engrenagem Cilíndricas de Dentes Helicoidais ECDH 103 Tabela 51 Equações de elementos que compõe a ECDH Denominação Formulário Número Imaginário de Dentes 𝑍1 𝑍 𝑐𝑜𝑠 𝛽03 Avanço de Dente 𝑆 𝑏 𝑡𝑎𝑔 𝛽0 Diâmetro Primitivo 𝑑0 𝑍 𝑚𝑠 Diâmetro Externo 𝑑𝐾 𝑑0 2 ℎ𝑘 Diâmetro do Pé do Dente 𝑑𝑓 𝑑0 2 ℎ𝑓 Diâmetro de Base 𝑑𝑔 𝑑0 𝑐𝑜𝑠 𝛼𝑠0 Fonte Adaptado de Melconian 2011 Tabela 52 continuação Equações de elementos que compõe a ECDH Denominação Formulário Altura da Cabeça do Dente ℎ𝑘 𝑚𝑛0 Altura do Pé do Dente ℎ𝑓 12 𝑚𝑛0 Altura Total do Dente ℎ𝑍 22 𝑚𝑛0 Folga da Cabeça 𝑆𝑘 02 𝑚𝑛0 Ângulo de Hélice 𝛽0 𝑆𝑒𝑐𝛽0 𝑑0 𝑚𝑛0 2 𝐴 𝑍1 𝑚𝑛0 𝑖 1 104 Ângulo de Pressão Normal 𝛼𝑛0 𝛼𝑛0 20 DIN 867 Ângulo de Pressão Frontal 𝛼𝑠0 𝑡𝑎𝑔 𝛼𝑠0 𝑡𝑎𝑔 𝛼𝑛0 𝑐𝑜𝑠 𝛽0 Distância Centro a Centro 𝐶𝐶 𝑍1 𝑍2 2 𝑚𝑠 Raio Imaginário Medido no Plano Normal 𝑟𝑛 𝑟0 𝑐𝑜𝑠 𝛽0 2 Fonte adaptado de MELCONIAN 2011 Tabela 53 continuação Equações de elementos que compõe a ECDH Denominação Formulário Módulo Normal normalizado 𝑚𝑛0 𝑇0 𝜋 Módulo Frontal 𝑚𝑠0 𝑚𝑛0 𝑐𝑜𝑠 𝛽0 𝑚𝑛0 𝑠𝑒𝑐 𝛽0 Passo Frontal 𝑡𝑠0 𝑚𝑠 𝜋 Passo Normal 𝑡𝑛0 𝑚𝑛0 𝜋 Espessura do Dente Frontal 𝑆𝑆0 𝑡𝑠0 2 Folga nula no flanco Vão entre Dentes no Frontal 𝑙𝑆0 𝑡𝑠0 2 Folga nula no flanco 105 Espessura do Dente Normal 𝑆𝑛0 𝑡𝑛0 2 Folga nula no flanco Vão entre Dentes Normais 𝑙𝑛0 𝑡𝑛0 2 Folga nula no flanco Fonte adaptado de MELCONIAN 2011 52 DIMENSIONAMENTO DE UMA ENGRENAGEM CILÍDRICA DE DENTES HELICOIDAIS ECDH Neste item serão apresentadas as principais equações que serão utilizadas no dimensionamento de uma ECDH e que servem para atender a aplicação deste elemento mecânico que irá compor uma caixa redutora de dupla redução conforme Figura 54 Veja a seguir as etapas de um projeto de elemento mecânico de Engrenagens Cilíndricas de Dentes Helicoidais ECDH Etapa 1 Dimensionamento com o Critério de desgaste Figura 54 Redutor de Dupla Redução com Engrenagens Cilíndricas de Dentes Helicoidais Fonte ANDRADE SD Critério de desgaste A seguinte expressão deve ser utilizada no dimensionamento de pinhões com ângulo de pressão 𝛼20 e número de dentes de 18 a 40 Material aço 106 b d0 2 02 f 2 Mt p2 adm φ p i 1 i í𝑛𝑑𝑖𝑐𝑒𝑒𝑛𝑔𝑟𝑒𝑛𝑎𝑔𝑒𝑛𝑠 𝑒𝑥𝑡𝑒𝑟𝑛𝑎𝑠 í𝑛𝑑𝑖𝑐𝑒𝑒𝑛𝑔𝑟𝑒𝑛𝑎𝑔𝑒𝑛𝑠 𝑖𝑛𝑡𝑒𝑟𝑛𝑎𝑠 𝑜𝑢 𝑝𝑙𝑎𝑛𝑒𝑡a𝑟𝑖𝑎𝑠 Em que b Largura do pinhão mm d0 Diâmetro primitivo do pinhão mm f Fator de características elásticas do par adimensional 𝒊 Relação de transmissão adimensional Padm Pressão admissível de contato Nmm2 𝝋 p Fator de correlação de hélice pressão adimensional O fator de correção 𝝋𝒑 utilizado para o critério de pressão obtémse por meio do ângulo de correção de hélice 𝜷𝟎 na tabela a seguir Tabela 54 Tabela de correlação entre o ângulo de hélice 𝜷𝟎 e o fator de correção 𝝋𝒓 𝜑𝑝 100 111 122 131 140 147 154 160 166 171 𝛽0 0 5 10 15 20 25 30 35 40 45 Fonte adaptado de MELCONIAN 2011 Etapa 2 Para o Dimensionamento de ECDH Pressão admissível padmissível padm 0487 HB W1 6 N mm2 107 No exemplo que vamos aplicar neste Bloco serão fornecidos os valores de Dureza Horas de atividade do elemento mecânico e seu Valor de utilização Agma 𝝋 no enunciado do Estudo de Caso para Dimensionar uma ECDH Assim falta o valor do Fator de Durabilidade W e seu cálculo se dá por meio da equação abaixo Fator de durabilidade W W 60 np h 106 Em que np Rotação do pinhão rpm h Duração do par horas HB Dureza Brinell Nmm2 Etapa 3 Fator de características elásticas 𝑓 Para ângulo de pressão 𝜶 20 Quando é necessário obter o valor do Fator de Características Elásticas f deve ser considerado o modelo da engrenagem ECDH e a relação de engrenamento para a determinação do f apresentados na Tabela 55 Tabela 55 Tabela de correlação entre a engrenagem seu material e seu fator de característica elástica Material E GPa Fator f Pinhão de aço Coroa de aço E 210 E 210 1512 Pinhão de aço Coroa de FoFo E 210 E 105 1234 108 Pinhão de FoFo Coroa de FoFo E 105 E 105 1069 Fonte adaptado de MELCONIAN 2011 A tabela 56 apresenta a correlação entre os tipos de material que podem ser utilizados na confecção de uma ECDH e os valores determinados por meio do método de ensaio de dureza Brinell Vale lembrar que não há uma equação de conversão entre os métodos dos Ensaios de Dureza mas existe uma tabela que correlaciona o valor obtido em diferentes métodos utilizados no ensaio Na tabela 56 são apresentados como referência os Valores de Dureza HBrinell mas para os tipos de aços descritos a seguir deverá ser utilizado a tabela Rockwell C HRc mesmo sendo só como referência Aços SAE 4320 SAE 4340 SAE 8620 e SAE 8640 temperados Tabela 56 Correlação entre os valores obtidos no Ensaio de Dureza do tipo Brinell Material HBRINELL 𝑵 𝒎𝒎𝟐 Aço fundido tipo 2 1700 2500 Aço fundido tipo 𝑩𝟐 1250 1500 Aço SAE 1020 1400 1750 Aço SAE 1040 1800 2300 Aço SAE 1050 2200 2600 Aço SAE 31453150 1900 2300 Aço SAE 4320 2000 4200 Aço SAE 4340 2600 6000 Aço SAE 8620 1700 2700 Aço SAE 8640 2000 6000 Aço fundido cinzento 1200 2400 Aço fundido nodular 1100 1400 Fonte adaptado de MELCONIAN 2011 109 Já a Tabela 57 apresenta o conceito de determinação dos valores obtidos nos Ensaios de Dureza Uma importante informação não há uma equação ou uma tabela para que se realize a conversão nos valores do Ensaio de Dureza pois cada valor é associado ao seu ensaio e tem particularidades de carga aplicada O elemento penetrador da superfície e a forma da impressão que será analisada de acordo com um método de ensaio junto com o valor de Dureza Brinnell HB solicitada na equação pode ser encontrado em catálogos ou até em certificados de fabricação do lote produzido de Aço ou Ferro Fundido Estes certificados ainda terão as informações de Composição Química e as Propriedades Mecânicas como Tenacidade e Dureza conforme exemplo da Tabela 57 Tabela 57 Valores de correlação entre os valores obtidos nos Ensaios de dureza Brinell Resistência 𝑁 𝑚𝑚2 Rockwell Impr mm Carga 30 kN Esfera Dureza HB 𝑁 𝑚𝑚2 Aço Carbono HB x 036 C Rc B Rb A Ra Shore Vickers 365 2270 997 29 104 646 39 279 370 2690 969 28 104 641 38 270 375 2620 943 26 103 636 37 263 380 2550 918 25 102 630 37 256 400 2290 824 21 98 608 33 229 Fonte adaptado de MELCONIAN 2011 Para o cálculo da expressão a seguir temos a Relação entre a Largura da engrenagem b e o Diâmetro primitivo 𝑑0 e é determinado o valor de 𝑏 𝑑0 Então para ECDH e para o bom dimensionamento da engrenagem haverá duas condições 1 Engrenagem Biapoiada o valor de 𝑏 𝑑0 12 Característica as duas extremidades do eixo são apoiadas 110 2 Engrenagem em Balanço o valor de 𝑏 𝑑0 075 Característica uma das extremidades do eixo é apoiada Confira como é a representação dessas expressões na figura 55 Figura 55 Representação das diferentes formas de fixar uma ECDH Fonte adaptado de MELCONIAN 2011 Na tabela 58 apresentada a seguir é definido o incremento no módulo após sua obtenção no cálculo do módulo de engrenamento de uma ECDH Este cálculo é usado para a fabricação da engrenagem no processo de fresamento e o módulo da ferramenta será o módulo da engrenagem somado ao incremento Tabela 58 Correlação entre os valores dos Módulos normalizados DIN 780 e o incremento Módulo mm Incremento mm 03 a 10 010 10 a 40 025 40 a 70 050 70 a 160 100 160 a 240 200 240 a 450 300 450 a 750 500 Fonte adaptado de MELCONIAN 2011 111 Etapa 4 Esforços de flexão no pé do dente e seus Tipos de Esforços gerados Normalmente para projetar escolhemos um critério para o dimensionamento e outro para a verificação No caso de engrenagens dimensionamos pelo desgaste e verificamos pelo critério de tensão no pé do dente Essa deve ser menor que a tensão admissível do material indicado Durante a atividade desta engrenagem em um sistema mecânico de transmissão de movimentos rotativos acontecerão esforços de flexão nos pés dos dentes da engrenagem ECDH Nas engrenagens cilíndricas de dentes helicoidais ECDH são gerados três esforços que geram uma Força de Flexão nos Pés dos Dentes da ECDH conforme apresentado na Figura 56 1 Força tangencial 2 Força radial 3 Força axial Figura 56 Representação da interação das forças distribuídas entre os dentes na ECDH Fonte SHIGLEY 2011 112 Então as seguintes equações serão aplicadas para obter o valor dos Esforços para o caso de uma Força Tangencial 𝐹𝑡 conforme a Figura 57 Segue 1 Força tangencial 𝐹𝑡 A carga tangencial Ft é responsável pelo movimento das engrenagens sendo também a carga que origina momento fletor tendendo por flexão o pé do dente A fórmula tangencial é determinada por 𝐹𝑡 𝑀𝑡 𝑟0 2𝑀𝑡 𝑑0 raio primitivo 𝑟0 𝑑0 2 Em que Ft força tangencial N MT torque N mm ro raio primitivo da engrenagem mm do diâmetro da engrenagem mm Figura 57 Apresenta a Força Tangencial aplicada e o esforço gerado no pé do dente Fonte SHIGLEY 2011 Força radial Fr Atua na direção radial da engrenagem É determinada por meio da tangente do ângulo c ângulo de pressão 113 tan 𝛼 𝐹𝑟 𝐹𝑡 Sendo Fr FT tag αS0 𝑁 Em que Fr carga radial N Ft carga tangencial N α ângulo de pressão graus Força axial 𝐹𝑎 Quando se utilizam engrenagens helicoidais cônicas ou parafuso sem fim surge outro esforço na transmissão que é a carga axial originada pela inclinação do ângulo da hélice sendo 𝛽0 representado na Figura 58 𝐹𝑎 𝐹𝑇 tag 𝛽0 ou 𝐹𝑎 𝐹𝑇𝑡𝑎g 𝛽0 N Figura 58 Apresenta as Forças aplicadas e o esforço gerado no pé do dente considerando a inclinação de 𝜷 Fonte SHIGLEY 2011 Força resultante 𝐹𝑛 114 É a resultante das cargas Ft e Fr sendo determinada por meio de Pitágoras como segue 𝐹𝑛 𝐹𝑡 2 𝐹𝑟 2 Em que Fn carga resultante N Fr carga radial N Ft carga tangencial N Ou ainda pelas reações cos α Ft Fn Fn Ft cos α sen α Fr Fn Fn Fr sen α As cargas radial e resultante serão importantes no dimensionamento de eixos e mancais sendo necessário o dimensionamento das engrenagens Etapa 5 Tensão máxima aplicada e a correlação entre Tensão Material usada na fabricação da ECDH e o valor do esforço de Tensão de flexão no pé do dente A tensão atuante no pé do dente deve ser menor ou igual à tensão admissível do material indicado Veja a seguir a fórmula que determina a intensidade da tensão máxima que a engrenagem sofrerá e que seu material de fabricação deverá resistir além de indicar os limites da Propriedades Mecânicas e a sua Vida Útil 𝜎𝑚á𝑥 𝐹𝑡 𝑞 𝑏 𝑚𝑛 𝑒 𝜑𝑟 𝜎𝑚𝑎𝑡𝑒𝑟𝑖𝑎𝑙 115 Em que Ft Força tangencial N q Fator de forma adimensional b Largura do pinhão mm Mn Módulo normal mm ϕ r Fator de correção de hélice adimensional e Fator de carga 080 e 150 adimensional Etapa 6 Fator de serviço 𝑒 e fator de correção de hélice 𝛗𝐫 Pelo fator de serviço 𝜑 da tabela AGMA determinase 𝑒 por intermédio de Sendo ϕ r fator de correção de hélice resistência Após ser obtido o fator de correção de hélice 𝜑𝑟 conforme apresentado anteriormente na Tabela 54 podemos determinar o valor do ângulo de hélice 𝛽0 por meio da tabela 59 Tabela 59 Tabela de correlação entre o ângulo de hélice 𝜷𝟎e o fator de correção 𝝋𝒓 Fonte Adaptado de Melconian 2011 𝝋𝒓 10 12 128 135 136 𝜷𝟎 0 5 10 15 a 25 25 a 45 𝑒 1 𝜑 116 Etapa 7 Para obtermos o valor do Fator de forma 𝑞 que está apresentado na tabela 59 o Cálculo do Número de Dentes Equivalentes 𝒛𝒆 da engrenagem ECDH deverá ser considerado antes conforme a equação a seguir Cálculo do número de dentes equivalente 𝒛𝒆 Assim o cálculo do número de dentes será pela expressão descrita a seguir 𝑧𝑒 𝑧1 cos𝛽03 Desta forma será obtido pela Tabela 510 o valor do fator de forma q e sua relação depende do número de dentes da engrenagem ECDH Tabela 510 Tabela de correlação entre o número de dentes e o fator de forma q Fonte SHIGLEY 2011 Uma observação Se o número de dentes for intermediário aos apresentados na Tabela 510 será necessário realizar a operação matemática de interpolação tanto no número de dentes Z quanto no Fator de Forma q Etapa 8 Obtémse nas tabelas a seguir o Valor dos Fatores de Serviço AGMA 𝜑 Este valor será considerado entre 2 condições ou seja 10 ou 24 horas de serviço para então obter o valor dos fatores de serviço AGMA conforme os exemplos apresentados abaixo nas Tabelas 511 e 512 117 Vale lembrar que os valores do Fator de Serviço AGMA ϕ de uma engrenagem ECDH como exemplificados nas Tabelas 511 e 512 ficam sempre à disposição em catálogos de fabricantes de engrenagens ou elementos de máquinas aplicado a um sistema mecânico Tabela 511 Tabelas de fatores de serviço AGMA ϕ Aplicações Serviço Horas de Atividade 10 h 24 h AGITADORES Líquidos 100 125 Misturadores de polpa 125 150 Semilíquidos de densidade variável 125 150 ALIMENTADORES Alimentadores helicoidais 125 150 Alimentadores recíprocos 175 200 Transportadores esteira e correia 125 150 Fonte adaptado de MELCONIAN 2011 Conforme apresentado na Tabela 512 as principais características se tornam variáveis fundamentais no dimensionamento bem como na correta seleção de valor de acordo com as horas de serviço Esta condição altera a vida útil do projeto de um sistema mecânico Tabela 512 Continuação do exemplo de Tabelas de fatores de serviço AGMA ϕ para o acionamento de motores a explosão e serviços intermitentes Motor Elétrico Motor Elétrico Motores a Explosão Multicilíndricos 10 h 3 h 3 h 10 h 24 h 100 050 100 125 150 125 100 125 150 175 175 150 175 200 225 Fonte adaptado de MELCONIAN 2011 Para finalizar este item veja a Tabela 513 que apresenta os valores das Tensões admissíveis para os materiais que serão utilizados na fabricação de uma engrenagem ECDH 118 Tabela 513 Tensões ideais para os materiais no dimensionamento de engrenagens MATERIAL Mpa 𝑵 𝒎𝒎𝟐 FoFo cinzento 40 FoFo nodular 80 Aço fundido 90 SAE 10101020 90 SAE 10401050 120 SAE 43204340 170 SAE 86208640 200 Mat Sintético Resinas 35 Fonte adaptado de MELCONIAN 2011 53 TENSÕES ADMISSÍVEIS Neste subtema serão avaliados e determinados os valores máximos de tensão do material para assim podermos determinar qual material poderá ser utilizado na fabricação de uma ECDH Algumas recomendações são indicadas Recomendação 1 O projeto ideal é aquele em que a tensão atuante no pé do dente está bem próxima da tensão admissível no seu limite inferior Se a tensão atuante estiver acima da tensão admissível 𝜎 a engrenagem pode não suportar a transmissão vindo a romper na base do dente prematuramente Se por outro lado a tensão atuante estiver bem aquém da tensão admissível a engrenagem estará superdimensionada tornandose antieconômica Recomendação 2 Ângulo de pressão 𝛼 Observe o par de dentes apresentado na Figura 59 119 Iniciam o contato no ponto A A cinemática do mecanismo faz com que o ponto A descreva a trajetória AB No ponto B termina o contato entre os dentes O segmento de reta AB descrito pela trajetória do ponto de contato e a tangente comum aos diâmetros primitivos das engrenagens define o ângulo da pressão Pela norma DIN 867 recomendase a utilização do ângulo de pressão α 20 Figura 59 Trajetória demonstrada desde seu o início até o fim do contato entre dentes Fonte SHIGLEY 2011 Recomendação 3 Para a Engrenagem com perfil cicloidal serão apresentadas sua teoria e sua representação em condições de curvas nas Figuras 513 514 515 e 516 Aplicações Esse tipo de engrenagem limitado às construções mecânicas pode ser encontrada em bombas e ventiladores volumétricos em relógios e aparelhos de precisão Processos de Fabricação A engrenagem cicloidal é obtida por meio de estampagem trefilação brochamento ou injeção mecânica fina por fresamento ou aplainamento 120 As ferramentas são mais caras pois possuem flancos retos O processo de fabricação por ser mais preciso tornase mais caro Vamos Aplicar Nas etapas a seguir você verá o passoapasso para o projetista realizar o procedimento para dimensionar a engrenagem cilíndrica de dentes helicoidais ECDH Exercício Estudo de Caso Dimensionamento de engrenagens ECDH Roteiro para o dimensionamento de um par de engrenagens ECDH O pinhão engrenagem menor Item 1 da Figura 510 é o dimensionado pois se ele resistir ao esforço aplicado a coroa engrenagem maior Item 1 da Figura 510 suportará com folga a mesma carga por ser uma engrenagem maior Figura 510 Sistema Mecânico de transmissão de movimento entre pinhão e coroa ambas são engrenagens ECDH Fonte MELCONIAN 2011 Dimensionamento do pinhão Procedimento 1 Critério de pressão desgaste Para que não haja a ocorrência de uma Fadiga Superficial Crateração conforme Figura 511 deverão ser consideradas no cálculo durante o dimensionamento da engrenagem as seguintes etapas para realizar um bom e seguro projeto de engrenagens 121 Figura 511 Ocorrência da Fadiga Superficial denominada de Crateração nos dentes de uma ECDH Fonte ANDRADE SD 11 Torque no pinhão 𝑴𝑻 MT 30 π P n N m 12 Relação de transmissão i i Z2 Z1 13 Pressão admissível Padm deverá ser calculada conforme apresentado na equação abaixo e como foi visto na Etapa 2 Dimensionamento de ECDH Pressão admissível padmissível Para determinar seu valor deverão ser determinadas as seguintes variáveis Dureza pelo método Brinell e o fator de durabilidade padm 0487 HB W1 6 N mm2 131 Determinar a dureza Para a equação da tensão admissível será utilizado o valor de dureza pelo método Brinell que é obtido conforme exemplificado na Tabela 56 e 57 132 Fator de durabilidade W 𝑊 60 𝑛𝑝ℎ 106 122 Isolando o Fator de Durabilidade W 𝑊 1 6 𝑊 6 𝑊0168 133 Cálculo da pressão admissível Como foi calculado no item 13 deste exercício padm 0487 HB W 1 6 Poderá ser calculado o valor da Máxima Tensão admissível para o projeto da engrenagem ECDH 14 Fator de correção de hélice ϕp pressão Obtémse por meio do ângulo de inclinação de hélice βo na tabela 54 15 Volume mínimo do pinhão 𝑏1 𝑑01 2 02 𝑓2 𝑀𝑡 𝑝2 𝑎𝑑𝑚𝜑 𝑝 𝑖1 𝑖 denominado como X 𝑏1 𝑑01 2 𝑋 16 Módulo do engrenamento 𝑏1 𝑑01 2 𝑋 I volume mínimo 𝑏1 𝑦 𝑑01 II proporcionalidade Substituindo II em I tem se 𝑦 𝑑01 𝑑01 2 𝑋 𝑑01 3 𝑋 𝑌 𝑑01 𝑋 𝑌 3 Como o diâmetro primitivo d01 é definido por meio do produto entre o módulo frontal ms e o número de dentes da engrenagem temse d01 ms 𝑍1 123 161 Módulo Frontal 𝐦𝐬 ms 𝑑01 𝑍1 162 Módulo normal ferramenta mn ms cos βo Normalizar o módulo obtido por meio da DIN 780 Mn módulo normalizado 163 Recálculo do módulo frontal 𝒎𝒔𝟎 𝑚𝑠0 𝑚𝑛0 𝑐𝑜𝑠 𝛽0 17 Recálculo do diâmetro primitivo 𝒅𝟎𝒓 d0r Z1 ms0 18 Largura da engrenagem b1 X d0r 2 As equações dos itens 17 e 18 serão fundamentais no dimensionamento Critério de resistência à flexão no pé do dente A tensão máxima no pé do dente é expressa por meio de 124 Figura 512 Apresenta a Força Tangencial aplicada e o esforço gerado no pé do dente Fonte SHIGLEY 2011 2 Resistência à flexão no pé do dente σmáx Ft q b mn0 e φr φmaterial 21 Força tangencial FT FT 2 MT1 d01r MT1 r01 N 211 Raio primitivo 𝐫𝟎𝟏 𝑟01 𝑑01𝑟 2 22 Fator de forma q Para utilizar a tabela 510 onde determinase o valor do fator de forma de uma engrenagem ECDH tornase necessário determinar o número de dentes equivalentes Utilizase para tal a relação seguinte 𝑍𝑒 𝑍1 𝑐𝑜𝑠 𝛽0 3 Ze número de dentes equivalentes Por meio do 𝑍𝑒 obtémse o fator q na tabela 510 23 Fator de serviço e 125 Obtido na tabela AGMA por meio da relação e 1 φ 24 Largura da engrenagem b1 X d01 R 2 25 Módulo normalizado 𝑏1 𝑑01 2 𝑋 I volume mínimo 𝑏1 𝑦 𝑑01 II proporcionalidade Substituindo II em I tem se d01 ms 𝑍1 26 Módulo Frontal 𝐦𝐬 ms 𝑑01 𝑍1 27 Fator de correção de hélice 𝝋𝒓 Obtido em 𝑓 𝛽0 valor tabelado obtido em catálogo de fabricantes 28 Tensão máxima atuante no pé do dente σmáx Ft q b mn0 e φr Sempre merecendo um destaque nas equações dos itens 27 e 28 29 Análise do dimensionamento A engrenagem estará apta para suportar a transmissão se atender todas as características geométricas de acordo com as Normas DIN 862 e 867 para então atender aos Limites de Propriedades Mecânicas que em nosso estudo será a tensão Máxima de projeto e a tensão Máxima do material de fabricação para ECDH como apresentada na Figura 513 a seguir σmáx σmaterial 126 Figura 513 Acoplamento entre os dentes de uma ECDH e os 3 tipos esforços gerados Fonte SHIGLEY 2011 Os três tipos de esforços são Tangencial Axial e Radial Seus Cálculos podem ser vistos a seguir 1 Força tangencial FT FT 2 MT1 d01r 2 MT2 d02 N 2 Força radial Fr Fr FT tag αS0 𝑁 3 Força axial 𝑭𝒂 𝐹𝑎 𝐹𝑇 𝑡𝑎g 𝛽0 N Vamos Aplicar Exercício 1 1 Dimensionar o par de engrenagens ECDH para que possa atuar com segurança na transmissão representada conforme segue 127 O acionamento será por meio de motor elétrico com potência P 147kW 20CV e rotação n 1140rpm ω 38πrads O material a ser utilizado é o SAE 8640 A dureza especificada é de 58 HRC A duração prevista para 10000h de funcionamento com atuação em eixos de transmissão e acionamento máximo de 10hdia Figura 514 Sistema Mecânico de transmissão de movimento entre pinhão e coroa ambas são ECDH Fonte MELCONIAN 2011 Fator de serviço e 1 ϕ Sendo o fator de serviço AGMA ϕ 140 Considere 𝑏1 𝑑01 025 relação entre largura e diâmetro primitivo 𝛼𝑛0 20 ângulo de pressão 𝑍1 29 𝑑𝑒𝑛𝑡𝑒𝑠 𝑝𝑖𝑛ℎã𝑜 𝑍2 89 𝑑𝑒𝑛𝑡𝑒𝑠 𝑐𝑜𝑟𝑜𝑎 𝛽0 20 â𝑛𝑔𝑢𝑙𝑜 𝑑𝑒 ℎé𝑙𝑖𝑐𝑒 𝛼𝑛0 20â𝑛𝑔𝑢𝑙𝑜 𝑑𝑒 𝑝𝑟𝑒𝑠𝑠ã𝑜 𝑛𝑜𝑟𝑚𝑎𝑙 Desprezar as perdas na transmissão 128 Dimensionamento 1 Critério de pressão desgaste 11 Fator de características elásticas do material f Como o material utilizado é o aço concluise que F 1512 12 Torque no pinhão 𝑀𝑇1 30000 𝜋 𝑃 𝑛 𝑁 𝑚𝑚 𝑀𝑇1 30000 𝜋 14700 1140 𝑁 𝑚𝑚 𝑀𝑇1 123136 𝑁 𝑚𝑚 13 Relação de transmissão i 𝑖 𝑍2 𝑍1 89 29 𝑖 307 14 Pressão admissível Padm 141 Fator de durabilidade W W 60 np h 106 60 1140 104 106 np nmotor 1140 rpm motor acoplado ao eixo do pinhão W 684 142 Intensidade da pressão admissível Pressão admissível 𝒑𝒂𝒅𝒎 𝑝𝑎𝑑𝑚 0487𝐻𝐵 𝑊1 6 𝑁 𝑚𝑚2 Por meio da tabela de correlação de dureza obtémse que 58HRC equivale aproximadamente a 6000 Nmm2 6000HB 129 padm 0487 6000 6841 6 0487 6000 297 N mm2 𝑝𝑎𝑑𝑚 984 𝑁 𝑚𝑚2 984 102 𝑁 𝑚𝑚2 15 Fator de correção de hélice ϕp pressão Como o ângulo de hélice é βo 20 obtémse na tabela 54 ϕp 140 16 Volume mínimo do pinhão 𝑏1 𝑑01 2 02 𝑓2 𝑀𝑡 𝑝2 𝑎𝑑𝑚 𝜑 𝑝 𝑖 1 𝑖 𝑏1 𝑑01 2 02 15122 123136 984 102 2 14 307 1 307 𝑏1 𝑑01 2 45723 104 123136 984 2 104 14 407 307 𝑏1 𝑑01 2 55063 𝑚𝑚3 17 Módulo do engrenamento 𝑏1 𝑑01 2 55063 𝑚𝑚3 I 𝑏1 025 𝑑01 II Substituindo II em I tem se 025 𝑑01 2 𝑑01 55063 d01 3 55063 025 d01 55063 025 3 𝑑01 604 𝑚𝑚 18 Módulo frontal 𝐦𝐬 ms 𝑑01 𝑍1 604 29 ms 208 𝑚𝑚 130 19 Módulo normal ferramenta mn ms cos β0 𝑚𝑛 208 cos 20 𝑚𝑛 195 mm Por meio da DIN 780 escolhese o módulo normalizado 𝑚𝑛0 2 mm 110 Recálculo do módulo frontal 𝒎𝒔𝟎 𝑚𝑠0 𝑚𝑛0 cos 𝛽0 2 cos 20 𝑚𝑠0 213 𝑚𝑚 111 Recálculo do diâmetro primitivo 𝒅𝟎𝟏 𝑹 d01 R Z1 ms0 d01 R 29 213 d01 R 6177 mm 112 Largura da engrenagem b1 X d01 R2 b1 55063 61772 b1 15 mm 131 2 Resistência à flexão no pé do dente 𝜎 𝐹𝑡 𝑞 𝑏 𝑚𝑛0 𝑒 𝜑𝑟 𝜎𝑚𝑎𝑡𝑒𝑟𝑖𝑎𝑙 21 Força tangencial 𝐹𝑇 2 𝑀𝑇1 d01 R 2 123136 6177 𝐹𝑇 398 N 22 Fator de forma q 221 Número de dentes equivalentes Ze 𝑍𝑒1 𝑍1 𝑐𝑜𝑠 𝛽1 3 29 𝑐𝑜𝑠 20 3 𝑍𝑒1 35 dentes Por meio da tabela do fator q encontrase que Z fator q 34 30 40 29 Interpolando os valores da tabela obtémse que Incremento da interpolação l 30 29 6 00167 Por meio do incremento encontrado são determinados os seguintes valores 132 Tabela 514 Tabela da correlação entre o número de dentes da engrenagem e seu incremento q Número de Dentes Fator q 34 3000 35 2983 36 2967 37 2950 38 2933 39 2917 40 2900 Fonte MELCONIAN 2011 Portanto para Ze 35 dentes o fator q 2983 23 Fator de serviço e Para trabalhar em eixo de transmissão com duração de serviço diário prevista para 10 horas a tabela da AGMA recomenda ϕ 1 Como e 𝟏 𝝋 concluise que para este projeto e 1 24 Largura da engrenagem 𝑏1 15 𝑚𝑚 25 Normalizado 𝐦𝐧𝟎 mn0 2 mm 26 Fator de correção de hélice ϕr Como βo 20 encontrase na tabela ϕr 135 27 Tensão máxima atuante no pé do dente 𝜎𝑚á𝑥 𝐹𝑡 𝑞 𝑏 𝑚𝑛0 𝑒 𝜑𝑟 𝜎𝑚á𝑥 3987 2983 15 2 1 135 𝜎𝑚á𝑥 294 𝑁 𝑚𝑚2 133 28 Análise do dimensionamento Como a tensão máxima atuante é maior que a tensão admissível do material 𝜎𝑚á𝑥 294 𝑁 𝑚𝑚2 𝜎8640 200 𝑁 𝑚𝑚2 Concluise que o pinhão está mal dimensionado devendo ser reforçado 29 Redimensionamento do pinhão 1ª hipótese mantémse o módulo do engrenamento e alterase a largura Fixase a tensão atuante máxima com o mesmo valor da tensão admissível do material SAE 8640 portanto 𝜎𝑚á𝑥 𝜎8640 200 𝑁 𝑚𝑚2 291 Largura do pinhão 𝑏1 𝐹𝑡 𝑞 𝜎8640 𝑚𝑛0 𝑒 𝜑𝑟 3987 2983 200 2 1 135 𝑏1 22 𝑚𝑚 3 Cálculo para obter os valores das características geométricas segundo as Normas DIN 862 e 867 As tabelas a seguir de 515 a 518 apresentam as equações para realização dos cálculos Tabela 515 Formulário das variáveis fundamentais do projeto de uma ECDH Formulário Pinhão mm Coroa mm Módulo normalizado DIN 780 mn0 2 mn0 2 Passo t0 t0 mn0 π t0 628 t0 628 134 Fonte adaptado de MELCONIAN 2011 Vão entre os dentes no primitivo folga nula no flanco l0 t0 2 l0 628 2 314 l0 628 2 314 Espessura do dente no primitivo folga nula no flanco S0 t0 2 S0 t0 2 628 2 314 S0 t0 2 628 2 314 Altura da cabeça do dente hk mn0 hk 2 hk 2 135 Tabela 516 continuação Formulário das variáveis fundamentais do projeto de uma ECDH Fonte adaptado de MELCONIAN 2011 Tabela 517 continuação Formulário das variáveis fundamentais do projeto de uma ECDH Formulário Pinhão mm Coroa mm Ângulo de pressão frontal 𝛼𝑆0 tag 𝛼𝑆0 𝑡𝑎𝑔 𝛼𝑛0 𝑐𝑜𝑠 𝛽0 tag 𝛼𝑆0 𝑡𝑎𝑔 20 𝑐𝑜𝑠 20 tag 𝛼𝑆0 036 093 𝛼𝑆0 21 10 tag 𝛼𝑆0 𝑡𝑎𝑔 20 𝑐𝑜𝑠 20 tag 𝛼𝑆0 036 093 𝛼𝑆0 21 10 Avanço do dente s 𝑠 𝑏 tag 𝛽0 𝑠 22 tag 20 𝑠 8 𝑠 22 tag 20 𝑠 8 Formulário Pinhão mm Coroa mm Altura do pé do dente ℎ𝑓 12 𝑚𝑛0 ℎ𝑓 12 2 24 ℎ𝑓 12 2 24 Altura total do dente ℎ𝑧 22 𝑚𝑛0 ℎ𝑧 22 2 44 ℎ𝑧 22 2 44 Altura comum do dente ℎ 2 𝑚𝑛0 ℎ 2 2 4 ℎ 2 2 4 Folga da cabeça do dente 𝑆𝐾 02 𝑚𝑛0 𝑆𝐾 02 2 04 𝑆𝐾 02 2 04 Módulo frontal 𝑚𝑠 𝑚𝑛0 𝑐𝑜𝑠 𝛽0 𝑚𝑠 2 𝑐𝑜𝑠 20 𝑚𝑠 213 𝑚𝑠 2 𝑐𝑜𝑠 20 𝑚𝑠 213 136 Diâmetro primitivo 𝑑0 𝑑0 𝑚𝑠 𝑍 𝑑0 𝑚𝑠 𝑍1 𝑑0 213 29 𝑑0 6177 𝑑0 𝑚𝑠 𝑍2 𝑑0 213 89 𝑑0 18957 Fonte adaptado de MELCONIAN 2011 Tabela 518 continuação Formulário das variáveis fundamentais do projeto de uma ECDH Fonte adaptado de MELCONIAN 2011 Formulário Pinhão mm Coroa mm Diâmetro de base 𝑑𝑔 𝑑𝑔 𝑑0 𝑐𝑜𝑠 𝛼𝑠0 dg1 d01 cos 21 10 dg1 6177 093 dg1 5760 dg2 d02 cos 21 10 dg2 18957 093 dg2 17677 Diâmetro interno 𝑑𝑓 𝑑0 2 ℎ𝑓 df1 d01 2 hf df1 6177 2 24 df1 5697 df2 d02 2 hf df2 18957 2 24 df2 18477 Diâmetro externo 𝑑𝑘 𝑑0 2 ℎ𝑘 dk1 d01 2 hk dk1 6177 2 2 dk1 6577 dk2 d02 2 hk dk2 18957 2 2 dk2 19357 Distância entre centros mm Cc Z1 Z2 ms 2 29 89 213 2 Cc 123785 Largura das engrenagens mm b1 b2 22 137 4 Engrenagens cônicas de dentes retos e Espirais Tem as seguintes características 1 São utilizadas em eixos reversos 2 A relação de transmissão máxima é 16 3 Para relações de transmissão acima de 112 são mais caras que as engrenagens cilíndricas 41 Engrenagens cônicas Em uma engrenagem cônica o diâmetro externo De pode ser medido por meio do número de dentes Z e do ângulo primitivo δ para então ser calculado Na Figura 515 podemos ver os diferentes tipos de engrenamento considerando engrenagens cônicas São 4 Tipos de geometrias nas engrenagens cônicas como apresentado na figura 515 a seguir Figura 515 Exemplos de Engrenagens Cônicas 138 Fonte SHIGLEY 2011 Por meio da Figura 516 podem ser vistos os seguintes pontos o acoplamento entre engrenagens cônicas seus detalhes construtivos e suas Nomenclaturas de acordo com as Normas DIN 682 e 687 Figura 516 Geometria de uma Engrenagem Cônica com suas dimensões e ângulos 139 Fonte SHIGLEY 2011 Para determinar os diâmetros principais suas características geométricas e seus valores dimensionais de acordo com a Norma DIN 862 e 867 você verá nas Tabela 519 a 523 as principais equações que deverão ser consideradas pelo projetista no Memorial de Cálculo do Projeto de um Sistema Mecânico que neste caso será a Engrenagem Cônica ECDH Tabela 519 Formulário das variáveis fundamentais do projeto de uma Engrenagem Cônicas de Dentes Helicoidais Denominação Símbolo Fórmula Número de dentes 𝑍1 𝑍1 𝑑01 𝑚 Módulo m 𝑚 𝑡0 𝜋 140 Fonte adaptado de MELCONIAN 2011 Tabela 520 continuação Formulário das variáveis fundamentais do projeto de uma Engrenagem Cônicas de Dentes Helicoidais Denominação Símbolo Fórmula Altura da cabeça do dente ℎ𝑘 ℎ𝑘 𝑚 Altura do pé do dente ℎ𝑓 ℎ𝑓 11 𝑎 13 𝑚 Altura total do dente ℎ𝑍 ℎ𝑍 21 𝑎 23 𝑚 Folga na cabeça 𝑆𝑘 𝑆𝑘 01 𝑎 03 𝑚 Módulo médio 𝑚𝑚 𝑚𝑚 𝑑𝑚 𝑍 𝑅𝑎 𝑏 2 𝑅𝑎 𝑚 ou 𝑚𝑚 08 𝑚 Passo 𝑡0 𝑡0 𝑚 𝜋 Espessura no primitivo 𝑆0 𝑆0 𝑡0 2 com folga de flanco nula Vão entre os dentes no primitivo 𝑙0 𝑙0 𝑡0 2 com folga de flanco nula Diâmetro primitivo 𝑑01 𝑑01 𝑚 𝑍1 Diâmetro primitivo médio 𝑑𝑚1 𝑑𝑚1 𝑑01 𝑏 𝑠𝑒𝑛 𝛿1 e 𝑑𝑚2 𝑑𝑚1 l Altura comum do dente h ℎ 2 𝑚 141 Diâmetro externo ou de cabeça 𝑑𝑘1 2 𝑑𝑘1 𝑑01 2 𝑚 𝑐𝑜𝑠 𝛿1 𝑑𝑘1 𝑚 𝑍1 2 𝑐𝑜𝑠 𝛿1 𝑑𝑘2 𝑑02 2 𝑚 𝑐𝑜𝑠 𝛿2 𝑑𝑘2 𝑚 𝑍2 2 𝑐𝑜𝑠 𝛿2 para 𝛿 90 𝑐𝑜𝑠 𝛿2 𝑠𝑒𝑛 𝛿 Ângulo de pressão 𝛼0 𝛼0 20 norma DIN 867 Abertura angular entre eixos 𝛿 𝛿 𝛿1 𝛿2 Fonte adaptado de MELCONIAN 2011 Tabela 521 continuação Formulário das variáveis fundamentais do projeto de uma Engrenagem Cônicas de Dentes Helicoidai Denominação Símbolo Fórmula Conicidade de engrenagem relativa no primitivo 𝛿1 2 𝑡𝑎𝑔 𝛿2 𝑠𝑒𝑛 𝛿 𝑐𝑜𝑠 𝛿 𝑍1 𝑍2 𝑝𝑎𝑟𝑎 𝛿 90 𝛿1 𝛿 𝛿2 𝑡𝑎𝑔 𝛿2 𝑍2 𝑍1 i Conicidade de engrenagem relativa no diâmetro externo 𝛿 𝐾1 2 𝛿𝐾1 𝛿1 𝑘 em que tag k ℎ𝑘 𝑅𝑎 𝑚 𝑅𝑎 para 𝛿 90 tag 𝑘 4 𝑍12 𝑍22 Fonte adaptado de MELCONIAN 2011 142 Tabela 522 continuação Formulário das variáveis fundamentais do projeto de uma Engrenagem Cônicas de Dentes Helicoidais Denominação Símbolo Fórmula Geratriz relativa no diâmetro primitivo 𝑅𝑎 𝑅𝑎 𝑑01 2 𝑠𝑒𝑛 𝛿1 Para 𝛿 90 𝑅𝑎 𝑚 𝑍1 2 𝑍2 2 4 𝑅𝑎 𝑑01 1 𝑖 2 4 Geratriz relativa no diâmetro primitivo médio 𝑅𝑚 𝑅𝑚 𝑑𝑚1 1 𝑖 2 4 para 𝛼 90 Largura do dente b 𝑏 1 3 𝑅𝑎 8 𝑚 Fonte adaptado de MELCONIAN 2011 Tabela 523 continuação Formulário das variáveis fundamentais do projeto de uma Engrenagem Cônicas de Dentes Reto Denominação Símbolo Fórmula Número de dentes equivalente 𝑍01 2 𝑍𝑒1 𝑍1 𝑐𝑜𝑠 𝛿1 e 𝑍𝑒2 𝑍2 𝑐𝑜𝑠 𝛿2 Para 𝛿 90 𝑍𝑒2 𝑍01 𝑙2 143 Raio primitivo da engrenagem equivalente 𝑟𝑒1 2 𝑟𝑒1 𝑑01 2 𝑐𝑜𝑠 𝛿1 Relação de multiplicação L I 𝑍2 𝑍1 𝑑02 𝑑01 𝑛1 𝑛2 𝑠𝑒𝑛 𝛿2 𝑠𝑒𝑛 𝛿1 Para 𝛿 90 I tag 𝛿2 Fonte adaptado de MELCONIAN 2011 42 Dimensionamento de Engrenagens Cônicas ECDH Neste item serão apresentadas as principais equações que serão utilizadas no dimensionamento de uma ECDH para atender ao limite e à aplicação deste elemento mecânico ao ser solicitada em um projeto As equações deverão atender as condições descritas a seguir que estão no Memorial de Cálculo de Projeto de Elemento Mecânico e atender também ao dimensionamento com o Critério de desgaste Veja a seguir as etapas de um projeto de um elemento mecânico Engrenagens Cônicas Vamos entender a seguinte expressão que deve ser utilizada no dimensionamento de pinhões com ângulo de pressão 𝛼 20 e número de dentes de 18 a 40 Material utilizado na fabricação com material aço Condição 1 Atender o Volume da Base do Dente 𝑏1𝑑01 2 572 105 𝑀𝑡 𝑝2 𝑎𝑑𝑚 𝑖 1 𝑖 014 𝜑 Sendo que há 2 condições nesta expressão de Volume da base do dente índice engrenagens externas índice engrenagens internas ou planetárias 144 Ambos os exemplos de Engrenamento Externo ou Interno foram apresentados na Figura 51 itens a b e c Condição 2 Atender o Critério de Pressão Desgaste 𝑏𝑑𝑚1 2 02 𝑓2 𝑀𝑇 cos 𝛿1 𝑝𝑎𝑑𝑚2 𝑖2 1 𝑖2 Condição 3 Atender o Critério de Resistência à Flexão 𝜎𝑚á𝑥 𝐹𝑡 𝑞 𝑏 𝑚𝑚 𝑒 𝜎𝑎𝑑𝑚 Condição 4 Para obter o fator q definido na Tabela 54 devemos calcular o número de dentes equivalente da engrenagem cônica cônica cilíndrica 𝑍𝑒 𝑍1 cos 𝛿1 Em que b Largura do pinhão mm dm Diâmetro médio mm f Fator das características elásticas do par adimensional MT Momento Torçor N mm Padm Pressão admissível Nmm2 t Relação de transmissão adimensional máx Tensão máxima atuante Nmm2 Ft Fator tangencial N q Fator de forma adimensional mm Módulo médio mm Condição 5 Por meio das condições de atividade da engrenagem cônica será determinado a faixa de valores para o Fator de Serviço e como por exemplo Engrenagem Cônica ECDH 145 O fator de forma de engrenagem é obtido em função do número de dentes da engrenagem conforme é apresentado na Tabela 55 e fator de serviço serviços leves e 175 Serviços normais e 15 Serviços pesados e 125 Por meio dos cálculos realizados dos itens 10 a 42 concluise que ele atenderá todos os valores das Características Geométricas conforme Normas DIN 682 e 687 e as Propriedades Mecânicas devidos aos esforços aplicados nas Engrenagens Cônicas ECDH Conclusão Neste Bloco apresentamos a Engrenagem Cilíndrica de Dentes Helicoidais ECDH que em sua maior parte segue o mesmo conceito nas etapas de cálculo da ECDR vista no Bloco 4 Além disso suas características geométricas também seguem as Normas DIN 682 e 687 sendo então importante realizar um comparativo entre ECDR e ECDH Como vimos algumas vantagens da ECDR são possuir manufaturabilidade ou seja são mais fáceis de projetar e fabricar e ser de fácil montagem e maior eficiência quando comparada a ECDH pois esta possui em sua geometria uma inclinação β na região dos dentes que gera um esforço na axial além do esforço radial e com esses dois esforços ocorrerá um aumento de temperatura média de trabalho durante o engrenamento reduzindo a sua eficiência quando comparada a ECDR Já ao analisar as vantagens da ECDH temos no processo de engate os dentes que se engatam um pouco de cada vez ao invés de toda face ao mesmo tempo como visto na ECDR sendo assim gera uma operação mais silenciosa ao considerar que para o mesmo tamanho do dente módulo e largura equivalente as engrenagens helicoidais podem lidar com mais carga do que as engrenagens retas já que o dente da engrenagem helicoidal é efetivamente maior por estar posicionada diagonalmente 146 Desta forma fica a critério do engenheiro projetista selecionar qual engrenagem trará mais vantagens ao Sistema Mecânico a ser projetado REFERÊNCIAS ANDRADE A S Elementos Orgânicos de Máquinas II UFP SD KIMINAMI C S CASTRO W B OLIVEIRA M F Introdução aos processos de fabricação de produtos metálicos São Paulo Blucher 2013 MELCONIAN S Elementos de Máquinas 9ª ed São Paulo Erica 2011 MOTT R L Elementos de máquinas em projetos mecânicos São Paulo 2015 NORTON R L Projetos de Máquinas Uma Abordagem Integrada 4º ed Porto Alegre Bookman 2013 SHIGLEY J E BUDYNAS R G NISBETT J K Elementos de máquinas de Shigley 8ª ed São Paulo AMGH Editora Ltda 2011 147 6 CONCEITOS NOS ELEMENTOS DE ACOPLAMENTO Neste Bloco serão apresentados os principais elementos de acoplamento Assim como os tipos e as diversas aplicações dos acomplamentos nos Sistemas Mecânicos Também serão definidos os critérios que deverão ser considerados para que ocorra uma correta seleção de qual acoplamento deve ser utilizado Por fim serão demonstradas as formas de desalinhamento dos acoplamentos pois mesmo ocorrendo o desalinhamento este deve suportar suas condições de trabalho sem que hajam falhas ou rompimento do acoplamento em análise 61 APLICAÇÕES DO ACOPLAMENTO Acoplamento é um conjunto mecânico constituído de elementos de máquinas empregado na transmissão de movimento de rotação entre duas árvores ou eixo árvores conforme Figura 61 Empregase o acoplamento quando se deseja transmitir um momento de rotação de um eixo motor a outro elemento de máquina situado coaxialmente eixo comum a ele Também podem ser definidos como elementos de transmissão de máquinas cujo objetivo é unir duas extremidades eixos de equipamentos distintos na transmissão de força Figura 61 Acoplamento entre eixos àrvores de um sistema de motor e bomba Fonte FRANCESCHI ANTONELLO SD 148 Também devem ser informadas as funções em geral dos acoplamentos tais como Absorver desalinhamento entre os eixos Absorver parcialmente choques em um dos eixos Amortecer vibrações torcionais Proteger máquinas e equipamentos de sobrecarga funcionando como fusível Um acoplamento que faz parte da rotina de quem dirige e que opera por atrito é a embreagem fricção Na Figura 62 você pode ver um disco de embreagem e na figura 63 o local do acoplamento de um disco de embreagem Figura 62 Acoplamento que opera por atrito imagem de Disco de Embreagem Então chegase à conclusão de que o elemento mecânico que compõe o sistema da transmissão é o disco de embreagem como observado a seguir na Figura 63 instalado entre o motor e a caixa de mudanças de modo a conectar e desconectar estes dois componentes por ação do motorista 149 Figura 63 Acoplamento que opera por atrito sistema mecânico completo em que o disco de embreagem acoplamento realiza a ligação e a transmissão na caixa de mudança de um veículo 62 CLASSIFICAÇÃO E TIPOS DE ACOPLAMENTOS Para facilitar há uma classificação dos acoplamentos que se dividem em permanentes e comutáveis sendo que os permanentes atuam continuamente e são separados em acoplamentos rígidos e flexíveis Já os comutáveis ao atuar obedecem a um comando Assim veja os itens a seguir que apresentarão alguns tipos de acoplamento sua definição aplicação e imagem 621 ACOPLAMENTOS PERMANENTES Algumas vezes há a necessidade de desconexão durante o funcionamento da máquina ou equipamento e os acoplamentos permanentes são usados para conectar eixos em que não existe a necessidade de desconexão estas que ocorrem somente em caso de manutenção Acoplamentos destes tipos são utilizados em situações em que os eixos das árvores estão em uma forma de aplicação que se faz necessário algumas especificidades por exemplo a São colineares temse o acoplamento de flange conforme Figura 65 b Se cruzam temse a Junta universal conforme Figura 69 c São paralelos temse a Junta oldham conforme Figura 64 150 Figura 64 Modelo de uma Junta de oldham Fonte FRANCESCHI ANTONELLO SD 6211 ACOPLAMENTOS PERMANENTES RÍGIDOS FLANGES O método mais clássico de acoplamento para se conectar árvores utiliza o tipo de acoplamento rígido também denominado Flange conforme Figura 65 Ele é adequado na transmissão de potência elevada em baixa velocidade tendo também como garantir um alinhamento conciso sendo que estes acoplamentos frequentemente são usados por terem uma protuberância com a sua finalidade de ser encaixada em um rebaixo Figura 65 Modelo de um Acoplamento Permanente Rígido Flange Fonte FRANCESCHI ANTONELLO SD 151 Por meio de chaveta é realizada a união das Luvas ou Flanges nas Árvores com a condição de encaixe com interferência ou cones São utilizados acoplamentos de disco ou de pratos quando é desejado transmissões de grande potência 6212 ACOPLAMENTO COM LUVA DE COMPRESSÃO OU DE APERTO Para a seleção de um acoplamento que facilita no momento de uma manutenção de máquinas e de equipamentos são utilizados os do modelo Tipo Luva conforme figura 66 pelo fato de não interferir no posicionamento das árvores e não apresentarem problemas de alinhamento na montagem ou remoção Figura 66 Modelo de uma Luva de Compressão ou Aperto Fonte FRANCESCHI ANTONELLO SD 6213 ACOPLAMENTOS PERMANENTES FLEXIVEIS Utilizado quando na ocorrência de movimentos bruscos for necessário que a realização da transmissão de movimentos aconteça de forma mais suave durante seu movimento Será mantido o alinhamento entre as árvores e eixos árvores sendo que para o atendimento dessas condições citadas existem três modelos 152 Figura 67 Modelo de um Acoplamento Elástico de Garras Fonte FRANCESCHI ANTONELLO SD a Acoplamento elástico de garras Ao analisar as garras neste caso são constituídas por tocos de borracha Entre as aberturas do contra disco figura 67 ocorre o encaixe e será transmitido desta maneira o movimento de rotação b Acoplamento de dentes arqueados A característica principal ao classificar este modelo de acoplamento é que ele apresenta dentes de forma ligeiramente curvada no sentido axial sendo permitido até 3 graus de desalinhamento angular Através de um anel dentado que é a transmissora do movimento com suas duas carreiras separadas por uma saliência central c Acoplamentos elásticos São todos os elementos que são utilizados com a função de tornar a transmissão do movimento em árvores mais suave nos casos em que estes movimentos são bruscos Permitindo por meio destes acoplamentos o funcionamento do conjunto com desalinhamento angular paralelo e axial entre as árvores Tendo estes acoplamentos como principal função transmitir à máquina a energia de acionamento produzida pela unidade geradora porém com o mínimo de vibrações 153 6214 FLEXIBILIDADE ELÁSTICA Um elemento elástico tem a capacidade de absorver desalinhamento axial radial e angular conforme apresentado na Figura 68 quando um sistema mecânico é aplicado em transmitir rotação movimento de torção e também em condições que solicite o amortecimento de Picos de Carga e ruídos das máquinas acopladas Assim para o atendimento das condições de trabalho é indicado a utilização de Acoplamento Elástico Podese observar que pelas características mencionadas acima haverá uma grande aplicação quando o sistema é acionado por um Motor Elétrico Figura 68 Representação de um Sistema de Acoplamento com Flexibilidade Elástica Fonte FRANCESCHI ANTONELLO SD 63 ACOPLAMENTOS ARTICULADOS Dentro da gama de aplicações em diversas peças e equipamentos existem os acoplamentos por juntas universais e conforme indicado na Figura 69 o Eixo de transmissão cardan Na Figura 610 vemos as juntas homocinéticas e os Acoplamentos articulados como a embreagem que são muito aplicados no cotidiano e requerem um bom projeto para que tais sistemas mecânicos atendam as propriedades mecânicas necessárias e consigam o aumento de sua vida útil Vamos detalhar cada sistema a seguir a Juntas universais exemplo o eixo cardan 154 Aplicado na ligação da árvore que formam um ângulo constante entre si Seu sistema mecânico é constituído basicamente de dois cubos que possuem em suas extremidades um garfo ligado a uma cruzeta conforme Figura 69 Figura 69 Representação de um Sistema de Acoplamento Eixo de Transmissão Cardan Fonte KAPP SD b Junta Universal exemplo a Homocinética Aplicado quando é solicitado a uma junta transmitir o movimento entre árvores que permitam a ocorrência de uma variação angular conforme Figura 68 durante seu funcionamento Sendo a constituição desta junta formada de esferas de aço que são acomodadas em específicos alojamentos que são denominados de calhas c Acoplamentos Móveis exemplo Sistema Mecânico de um veículo que possui a Embreagem Junta Homocinética Eixo de Transmissão e outros itens com outras classificações Aplicado quando se faz necessário durante seu regime de trabalho que um acoplamento deva suportar a conexão e desconexão das árvores sem a necessidade de o acoplamento ser desmontado e assim permitir que a árvore tenha um jogo longitudinal como por exemplo no controle no acionamento da embreagem que ocorre no pedal do automóvel conforme Figura 610 Controle este que comanda a transmissão da Força e o Movimento apenas em seu acionamento ou seja com o pedal de embreagem 155 Figura 610 Representação de um Sistema com as Juntas Homocinéticas caixa de transmissão onde está a Embreagem e o eixo de transmissão cardan Fonte Euroautomotive 2017 631 Critérios na Montagem de Acoplamentos Alguns cuidados durante a montagem dos acoplamentos devem ser adotados com grande importância tais como a Sempre que possível que a colocação do Flange seja a quente b Não utilizar golpes para a colocação de Flanges utilizar prensas ou os dispositivos adequados c O alinhamento das árvores devem ser prioridade pois mesmo que Acoplamentos Elásticos não sejam utilizados por ocorrerem desalinhamentos ao longo do tempo de serviço sempre deverão ser realizados novos alinhamentos d Sempre deverá ser realizada uma averiguação da folga entre flanges do alinhamento e por consequência da concentricidade do flange com a árvore 156 e Somente aplicar a carga após certificarse de que estejam bem instalados todos os elementos de ligação 632 Desalinhamento em Acoplamentos Desalinhamento é quando ocorre a não coincidência entre o eixo de simetria de dois veios colineares Porém existem casos específicos em que se faz necessária a existência de um pequeno desalinhamento para que ocorra a lubrificação de dentes de um acoplamento de engrenagem Assim existe uma classificação do desalinhamento sendo angular ou paralelo O desalinhamento angular conforme a figura 611 ocorre quando há uma formação de um ângulo durante a rotação do eixo e se forma entre os dois veios Já o desalinhamento paralelo ocorre quando o eixo de rotação entre os dois veios é paralelo Desta forma pode se considerar que há ocorrência da combinação angular e paralelo no desalinhamento Figura 611 Representação da ocorrência dos Tipos de Desalinhamento nos Acoplamentos Fonte FRANCESCHI ANTONELLO SD 157 Mesmo com severos desalinhamentos o Sistema Mecânico ao seguir seu projeto deverá suportar por longos períodos de funcionamento Mas existem alguns componentes mecânicos que não suportam esse mesmo desalinhamento Devemos sempre considerar que em um Sistema Mecânico será necessária a utilização de um modelo de acoplamento pois é comum ocorrer desalinhamentos conforme a Figura 612 Figura 612 Representação da ocorrência de Desalinhamento em um Sistema Mecânico motor elétrico e um eixo arvoré terá acoplamentos nesta união Fonte Piotrowsky SD Desta maneira a principal função de um acoplamento é transmitir potência entre uma máquina e outra E também este deverá suportar e compensar pequenos desalinhamentos Além da deflexão do veio ocorrem variações de temperatura Tendo muitas vezes a ocorrência de Falhas Prematuras devido aos desalinhamentos que são passados para os componentes mecânicos 158 Conclusão Neste Bloco aprendemos a definir os principais elementos de acoplamento e realizar a identificação de seus tipos Também compreendemos a diversidade de aplicação em Sistemas Mecânicos e entendemos como ocorre o desalinhamento dos acoplamentos e por fim verificamos as condições de trabalho e os limites existentes da inevitável ocorrência do desalinhamento Sendo também ilustradas e detalhadas as condições corretas que devem ser seguidas na montagem dos acoplamentos REFERÊNCIAS ANDRADE A S Elementos Orgânicos de Máquinas II UFP SD EUROAUTOMOTIVE How Automatic Transmission Works In Vehicle Slideshare 2017 Disponível em httpsbitly2QUhx0x Acesso em 6 jan 2021 FRANCESCHI A ANTONELLO M G Elementos de Máquinas Colégio Técnico de Santa Maria SD KAPP W Eixos e árvores Curitiba Editora UFPR SD Disponível em httpsbitly3tRGGba Acesso em 6 jan 2021 MELCONIAN S Elementos de Máquinas 9 ed São Paulo Erica 2011 MOTT R L Elementos de máquinas em projetos mecânicos São Paulo 2015 NORTON R L Projetos de Máquinas Uma Abordagem Integrada 4ºed Porto Alegre Bookman 2013 PIOTROWSKY J A importância do alinhamento entre eixos Pdfslide Disponível em httpsbitly3tPzdJm Acesso em 6 jan 2021 SHIGLEY J E BUDYNAS R G NISBETT J K Elementos de máquinas de Shigley 8ª ed São Paulo AMGH Editora Ltda 2011